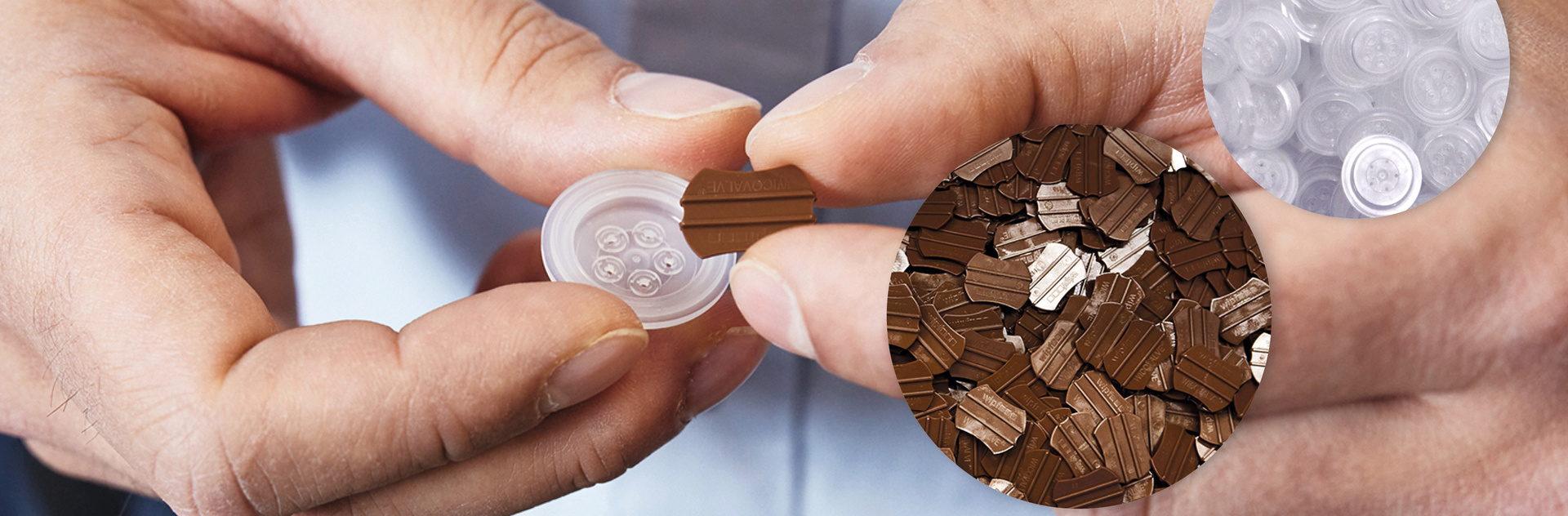
trendgineering
A family affair
| Petra Rehmet
Two Swiss companies together dominate the international market for aroma-seal valves
Two companies located just 600 m apart (as the crow flies) are connected closely in every way: Michel Werkzeugbau AG and Wipf AG. Together, they supply aroma-seal valves to the international market. For these and other projects, Michel has invested in 13 new KraussMaffei machines (12 all-electric PX machines and 1 hydraulic CX) since 2019.
Transporting coffee beans, leavened dough or other outgassing foodstuffs calls for aroma-seal valves, which allow gas to leave the packaging, but do not let any oxygen in. The latter would result in oxidation and spoilage of the product. Just two centimeters in diameter, the valves have an unassuming appearance that betrays little of the painstaking process required to produce them. However, this requires the famous Swiss precision and two closely connected companies.
Michel Werkzeugbau is part of the Wipf group and much more than "just" a moldmaking shop, given that 22 injection molding machines are now in operation there. When Reto Michel sold the business to Wipf – one of his good customers – in 2019, he did so to both ensure the company's future and enable further growth. Both companies have a familial culture and thus are a perfect fit.
Likewise, the relationship between Timo Brugger (CEO of Michel), Alexander Furrer (COO of Michel Werkzeugbau) and their contact at KraussMaffei, Michael Furlan (Switzerland Sales) is almost like family.
We are very, very satisfied with the machines and service from KraussMaffei. This has brought about a relationship of great trustTimo Brugger
CEO Michel Werkzeugbau AG
This makes it possible to get things done via direct, personal contact without major formalities – as evidenced in the thirteen machines that have been delivered in less than three years.
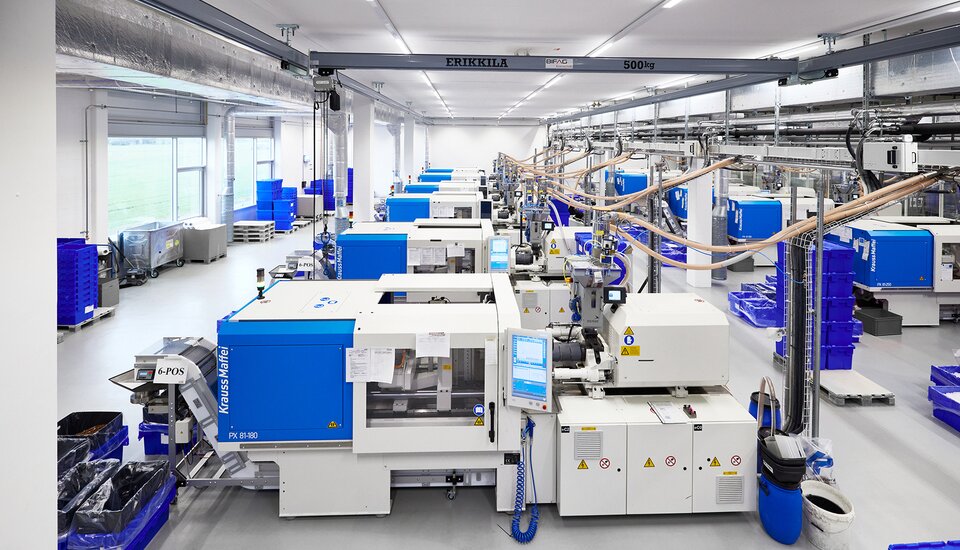
View into the production hall: Well-organized production with Swiss standard of quality
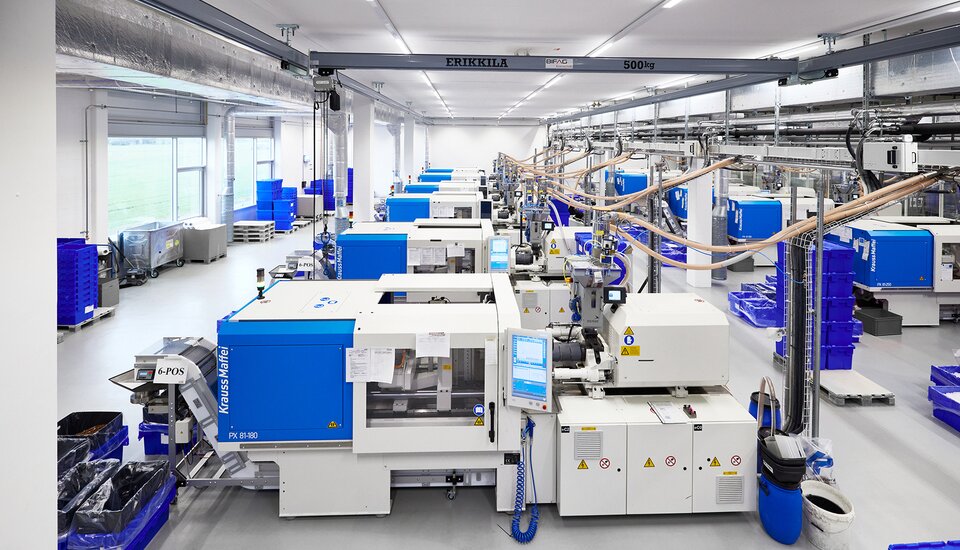
Millions of aroma-seal valves per year
For the aroma-seal valves, Michel makes the mold base body and the membrane holder from PE or PP with tolerances of 6/100 millimeters and Wipf takes over the assembly of the blanks. First, the sealing medium is introduced, then the membrane is inserted and finally fastened to the membrane holder. Wipf supplies several hundred million aroma-seal valves per year to international customers and thus is number two on the world market.
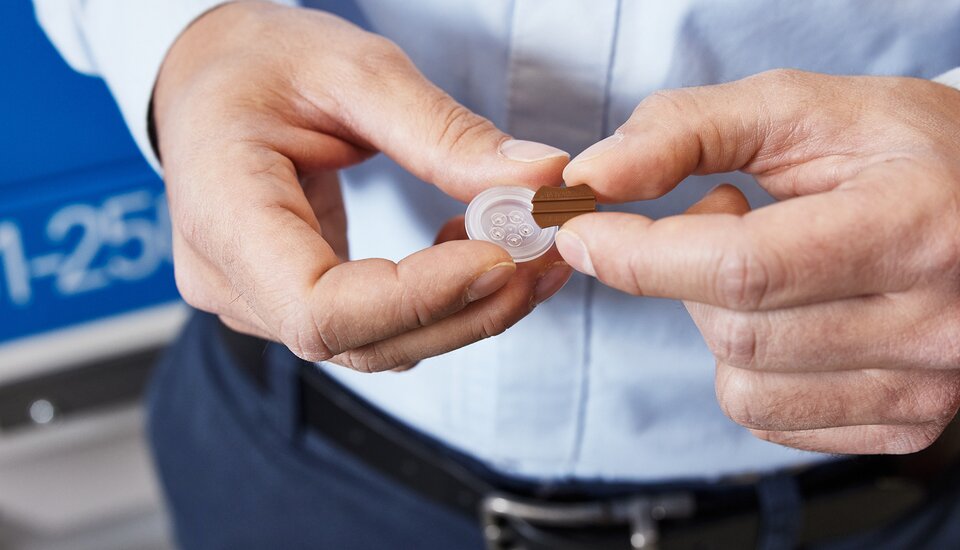
Base body and membrane holder: All that is needed to complete the aroma-seal valve is the sealing medium and the membrane
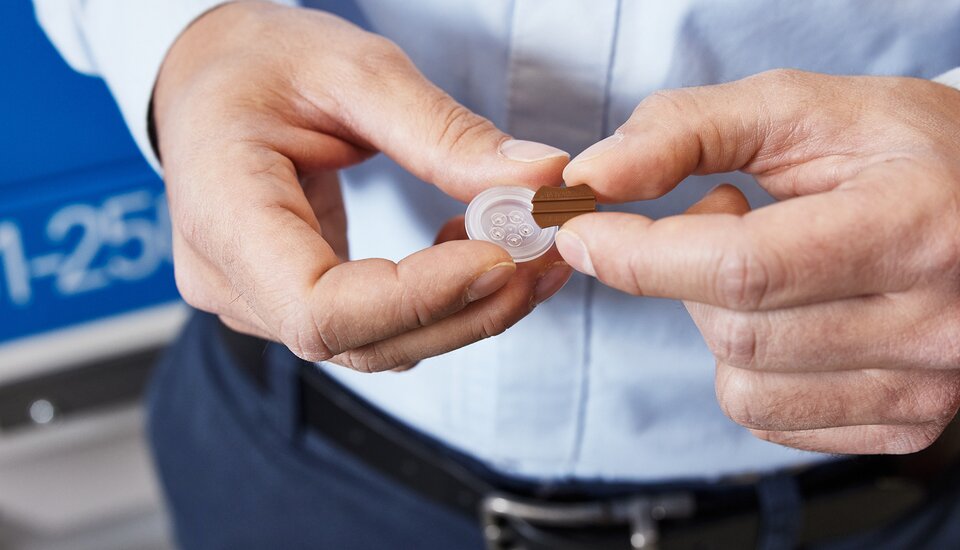
Proof of the particularly high quality is the three-year tightness guarantee that applies to the valves. They even work when the air pressure changes, by the way – in situations such as transporting goods in the cargo space of a plane. The pandemic had a thoroughly positive effect on sales, perhaps because people working from home tended to consume smaller packages of coffee than those commonly used in food service. Demand for premixed dough also grew considerably.
Strong growth and expansion
The strong growth in Michel's machine pool has taken place primarily since the move in 2020. The company had first looked for a new location that, unlike the old site, would offer space for expansion. With seven new KraussMaffei injection molding machines, production started in Nänikon (near Zurich).
The ten previous injection molding machines also moved into the new building, with the moldmaking shop following in 2021. The KraussMaffei (Schweiz) AG customer service team also provided active assistance for the move, enhancing the close and trusting collaboration. In addition, Wipf relocated the aroma-seal valve department to Nänikon, and thus a full-fledged expertise center is now located there. This is also how Timo Brugger switched from Wipf to Michel.
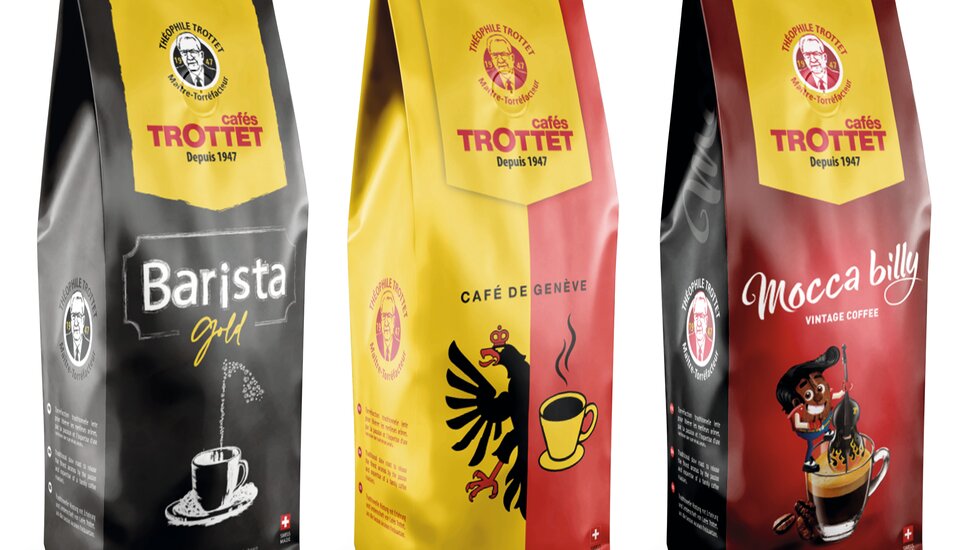
The aroma-seal valves are used in packaging from major coffee companies, for example
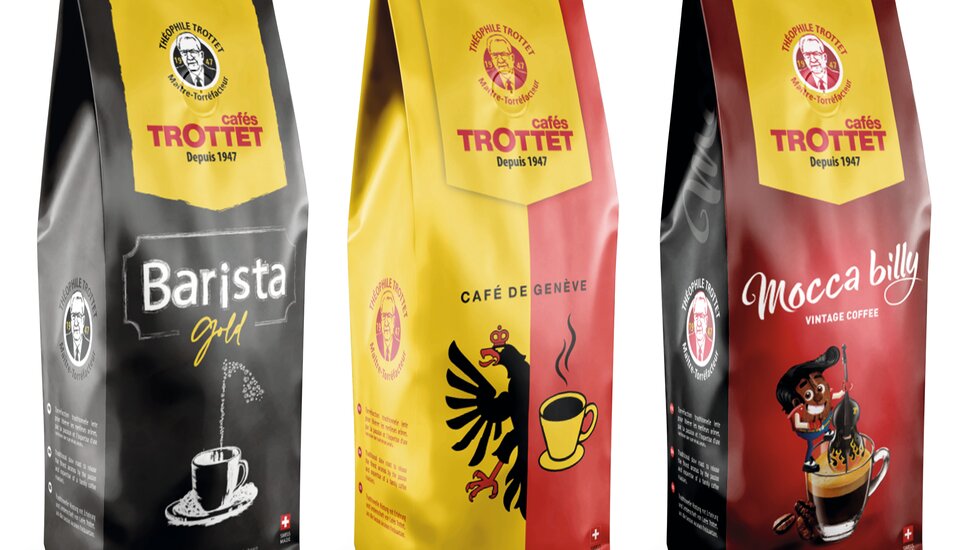
Together, the companies are responsible for the 20 or so different valve types, which consist of four basic body families subdivided into four or five versions each. Some 95 percent of the articles go to end customers, i.e. coffee roasters or food manufacturers, who then seal them in their foil packaging. Though the smallest order quantity is 10,000 units, for niche products, Wipf also offers shorter runs of the complete package consisting of a foil bag and an integrated valve.
Michel Werkzeugbau manufactures all injection molded parts needed by Wipf, thus covering approximately 60 percent of its own sales volume. This is supplemented by high-precision technical articles, for example for the building systems and plumbing industry. For small gears, tolerances of 3/100 millimeters must be complied with. For this and other purposes, four additional PX machines have gone online since the move, with two more following in 2023. The present clamping forces now range from 300 to 1,200 kN. All PX machines feature extended distances between tiebars and larger clamping platens that can hold molds with up to 36 cavities.
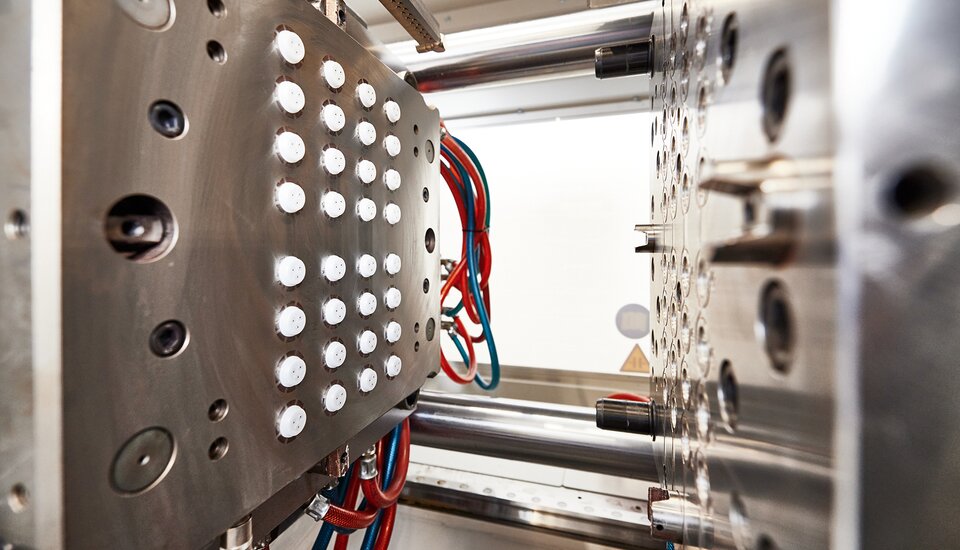
More space for larger molds: Multicavity molds make high yields possible
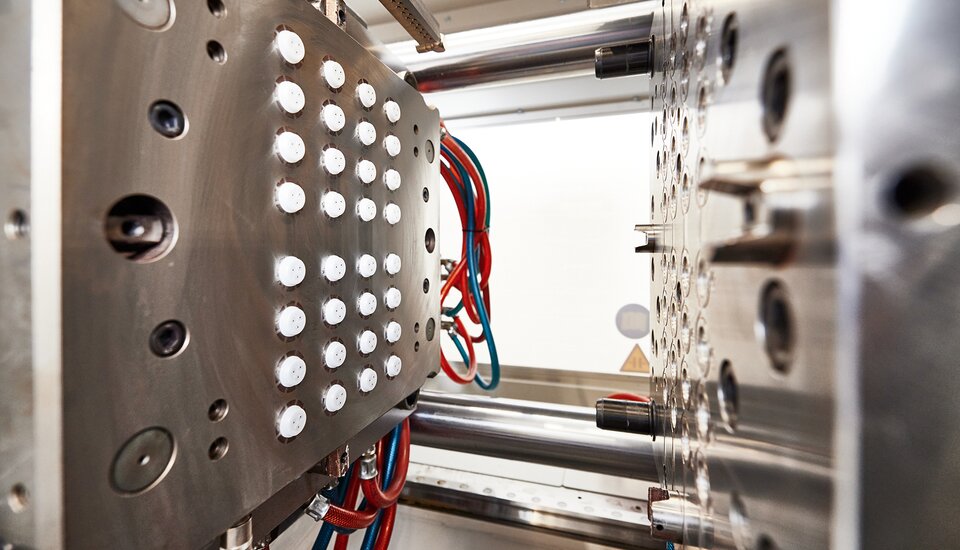
Short cycle times and 24/7 production
For a manufacturing operation in a high-wage country like Switzerland, it is indispensable for the machines to run 24 hours a day, 365 days a year. The day shift is present from 7 a.m. to 5 p.m., after which the "ghosts" take over and production is unsupervised. It is well known that the price-sensitive packaging industry needs fast cycle times – and efficient use of the staff on the shop floor. Michel employs a total of 20 employees and runs 21 (soon to be 23) injection molding machines.
We based our decision on the high repeatability, output and reliability of the PX because it makes us and our product competitive. Other suppliers have tried to manufacture more cheaply, but then the quality was never up to par.Alexander Furrer
COO Michel Werkzeugbau AG
The collaboration between Michel and KraussMaffei extends back to the turn of the millennium, and many of the hydraulic machines from that era are still working reliably.
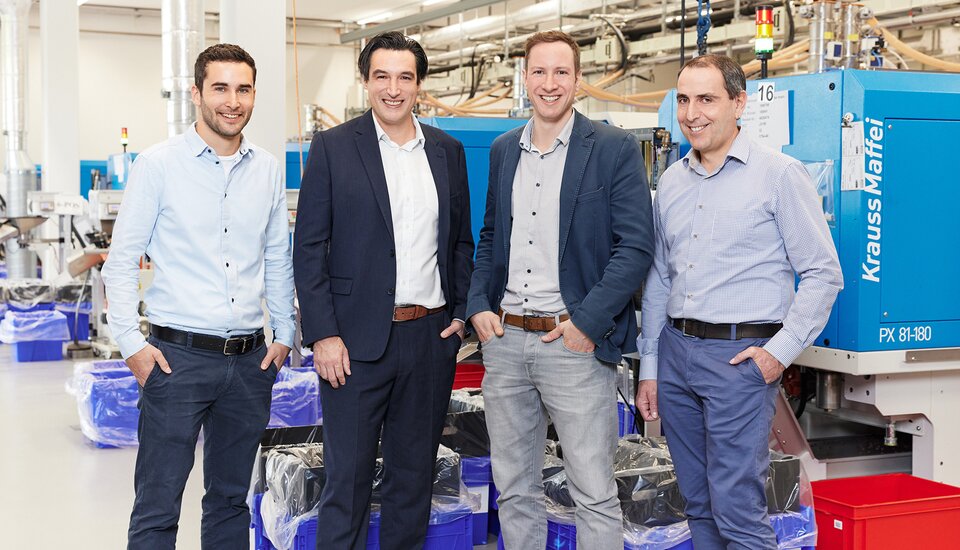
A strong team (from left to right): Timo Brugger, CEO, Michel Werkzeugbau AG - Michael Furlan, Sales, Krauss-Maffei (Schweiz) AG - Alexander Furrer, COO, Michel Werkzeugbau AG - Thomas Staffelbach, Head of Customer Service, Krauss-Maffei (Schweiz) AG
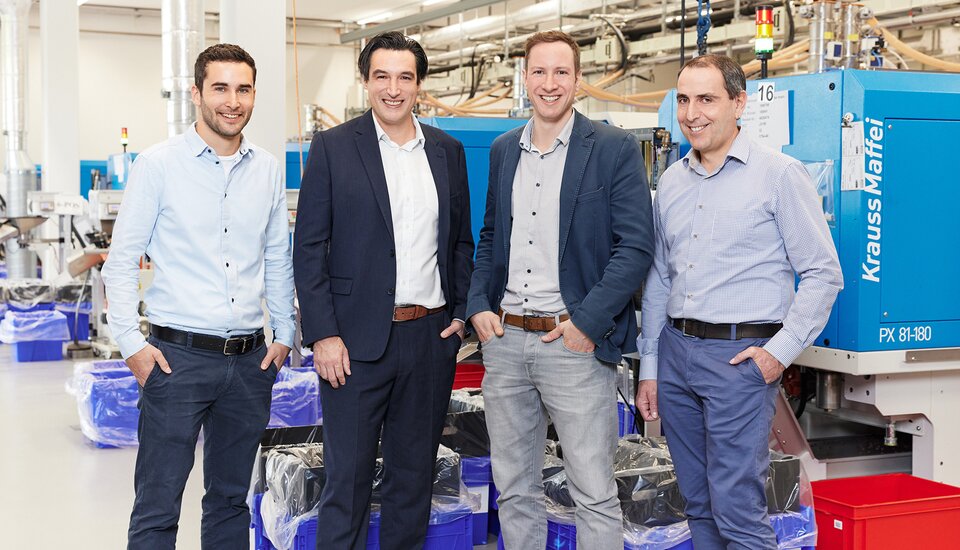
However, Michel is now making a consistent choice for all-electric, particularly while applications for the food industry are involved. Moreover, the PXs generate less noise and use less energy and oil. This is especially important given that Brugger is currently expecting surcharges of up to 40 percent for these.
Michel purchases its electricity on the free market and currently has a contract that is in effect, but at some point will have to negotiate for the next two-year-contract. It will then be good for the machines to run in as energy-saving a manner as possible.
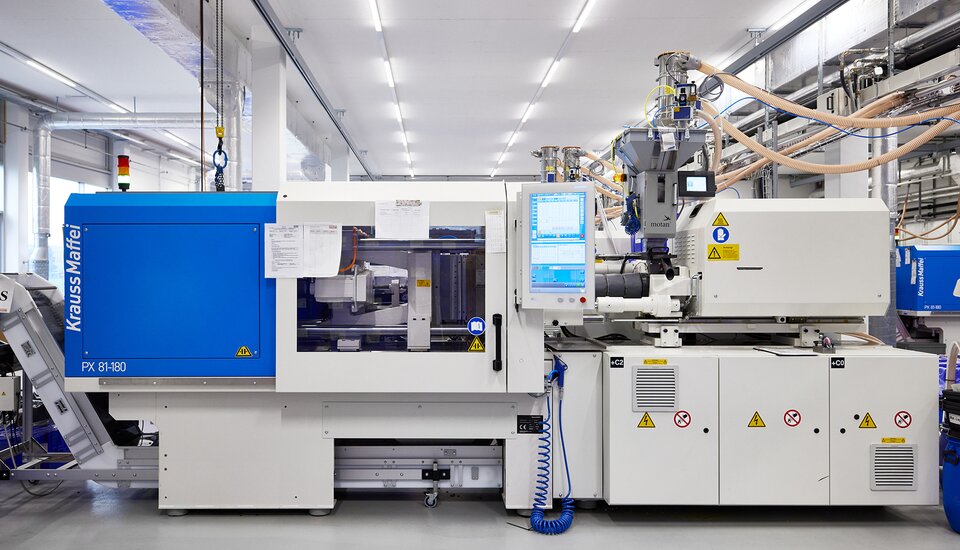
Repeatability, output and reliability – Michel cites these as the most important arguments in favor of the all-electric PX
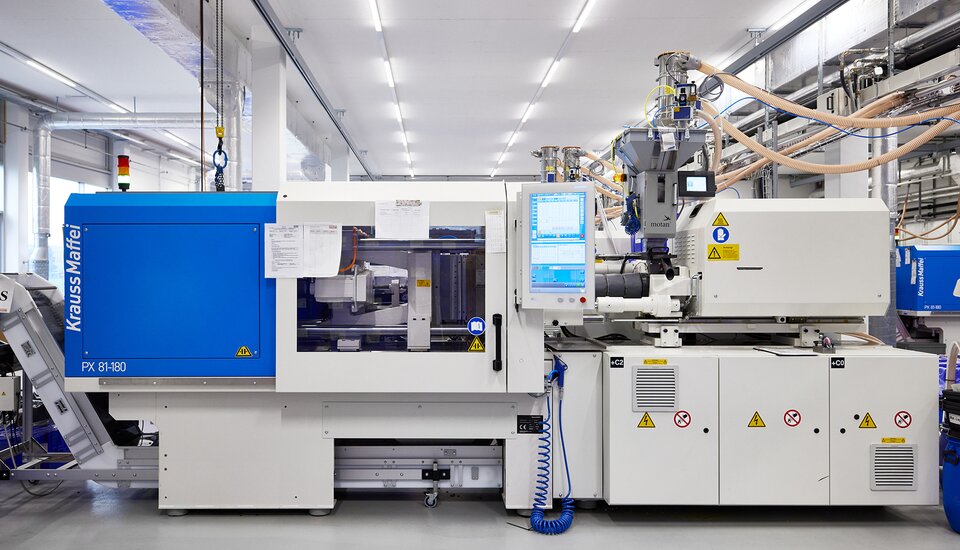
All parties are pulling together to ensure that the familial collaboration between Michel, Wipf and KraussMaffei remains successful. With this, they are proving that international competitiveness is possible with production in relatively expensive Europe.