
Durabilité
Extrusion solutions for a wide variety of plastics recycling
| Andreas Weseler
Technologies for the plasticizing, compounding and degassing process steps, for pure regranulation and for recompounding
Converting clean industrial waste or contaminated mixed waste from the “Green Dot” system into pure polymers or even complex recompounds – plastics recycling is a highly diverse and extremely challenging task! As an experienced machine manufacturer and material expert, KraussMaffei's extrusion division brings a great deal of expertise to the table – perfect prerequisites for sustained success in this important growth market.
“The most important advantage KraussMaffei offers is the wide variety of line concepts, which are customized for each individual recycling application. Depending on the specific requirements, we can design these lines as stand-alone or cascade solutions with almost unlimited output rates,” says Carl-Philip Pöpel, Director of Global Application & Product Ownership – Extrusion Technology at KraussMaffei. “Another plus point is the option to use a system solution composed of a single-screw extruder and a twin-screw extruder, especially when it comes to solvent-based plastics recycling. We are the only machine manufacturer worldwide to offer this unique combination as a one-stop solution.”
Extrusion technology for thermomechanical recycling
During mechanical processing of plastics waste, the chemical structure remains unchanged. The used plastic parts are crushed, cleaned, sorted by material type and finally reprocessed.
“The KraussMaffei EdelweissCompounding technology is based on two extruders operating in cascade arrangement. In the first stage, a twin-screw extruder is fed with the plastics scrap and prepares the starting material so that the degassed melt can be filtered through a 100 to 300 µm filter – depending on the technical specifications of the future product,” explains Franz-Xaver Keilbach, Global Application Owner Recycling at KraussMaffei. “Depending on the planned use of the material to be produced, either a pelletizing system is arranged downstream from the ZE extruder or the cleaned melt is directly transferred to the second stage, i.e. a compounding extruder. This extruder is used for controlled material upcycling by incorporating fillers and reinforcing agents, additives, stabilizers and dye.”

KraussMaffei EdelweissCompounding technology:
perfect cascade solution for processing and compounding sorted plastics scrap in a single cycle
Cutter Compactor – made by KraussMaffei
For ground material with an apparent density of below 0.25 kilograms per liter, the EdelweissCompounding technology can be complemented by an upstream compacting stage. The “fluffier” the input material, the more important is the use of a compactor cutter in order to heat, dry and agglomerate the sheet and film scraps to facilitate their subsequent processing in the twin-screw extruder.
Optimum degassing solutions for solvent-based recycling
“The solvent-based process is an interesting alternative especially for recycling composite materials that cannot be separated mechanically. Solvents are used to separate polymers from plastics composites or plastics compounds. However, the solvent has to be removed again afterwards," explains Franz-Xaver Keilbach. Here, too, the ZE BluePower twin-screw extruder comes into action. The rotating movement of its screws creates a large and permanently renewed melt surface, from which trapped volatile matter can escape more easily. Via openings in the housing that are connected to a vacuum, the solvents are removed from the process. The solvent removal is carried out in different pressure stages. The contaminated solvents are evaporated and subsequently condensed before they can be reused.
Here again the exact process characteristics are determined by the required properties of the polymer produced. To reduce the original 30 percent residual solvent content in the material to 2 percent, for example, a twin-screw extruder will be sufficient. However, if purity levels in the ppm range are required, a two-stage cascade configuration is recommended. KraussMaffei Extrusion implements this cascade solution by using a combination of a single-screw extruder with a twin-screw extruder. “Regardless of whether the material is recycled by a thermomechanical or a solvent-based process, the result is always an optimally cleaned melt. This melt can either be repelletized to a standard polymer or upgraded in an additional compounding step.”
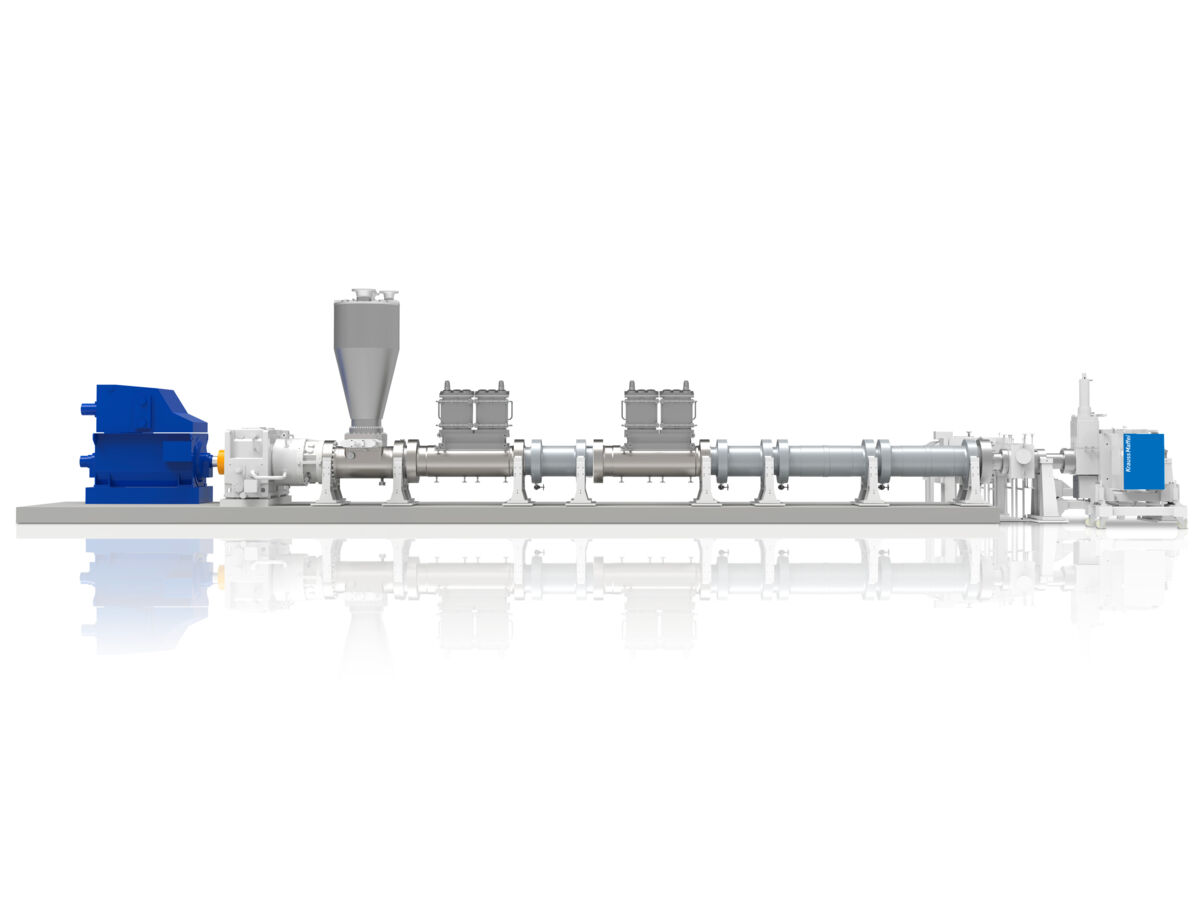
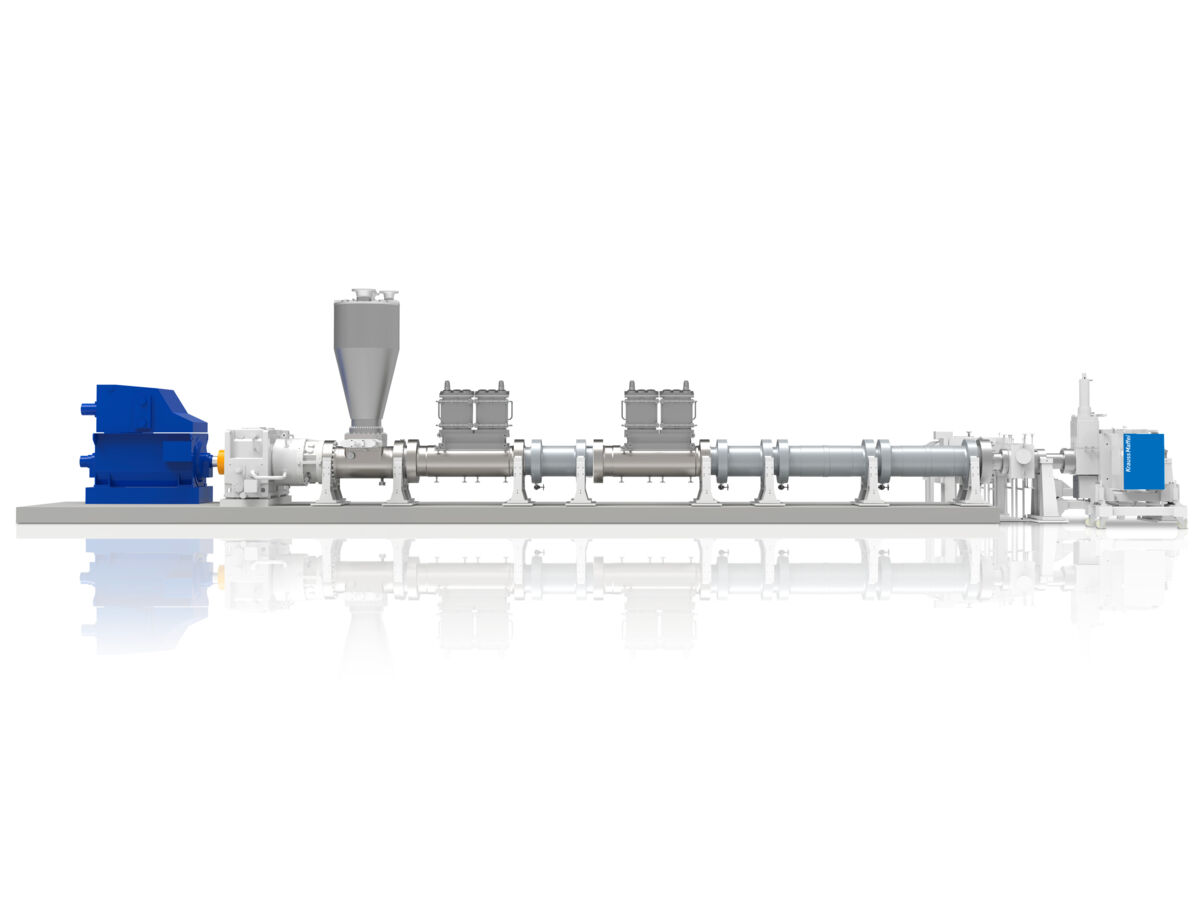
First-class machine concept for recycling applications
The high energy efficiency is one of the outstanding advantages of the ZE BluePower extruder series. Operating costs are substantially reduced thanks to numerous innovations in terms of energy efficiency and process-engineering features like power trains with optimized operating point, water-cooled three-phase a. c. motors and gear units with maximum efficiency. The modular range of barrel sections with 4 and 6D lengths and the wide variety of available screw elements ensure uncompromising flexibility in the development of customized ZE BluePower twin-screw extruder solutions for specific applications. The combination of large free volume in the processing section and high torque density gives optimum conditions for extremely cost-effective recycling and compounding processes.


carl.poepel@kraussmaffei.com
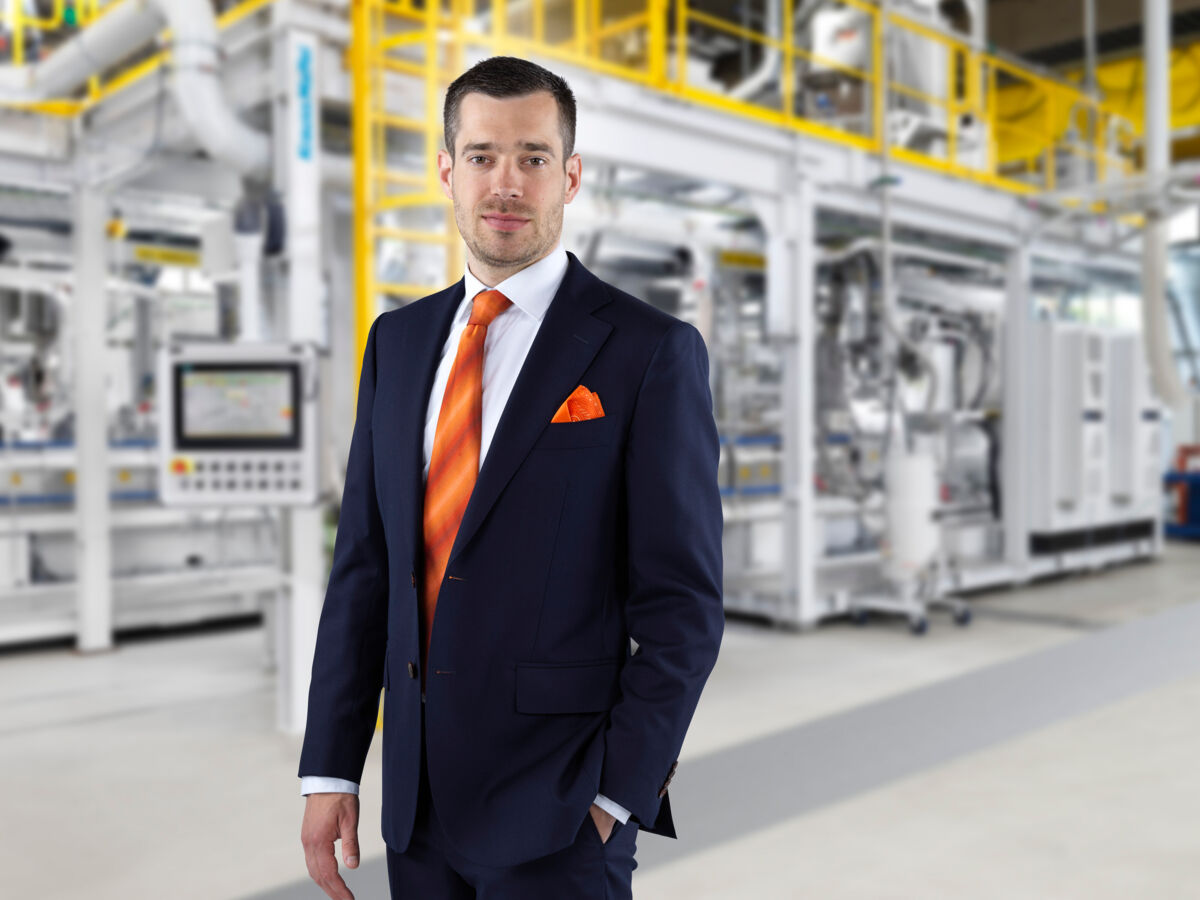
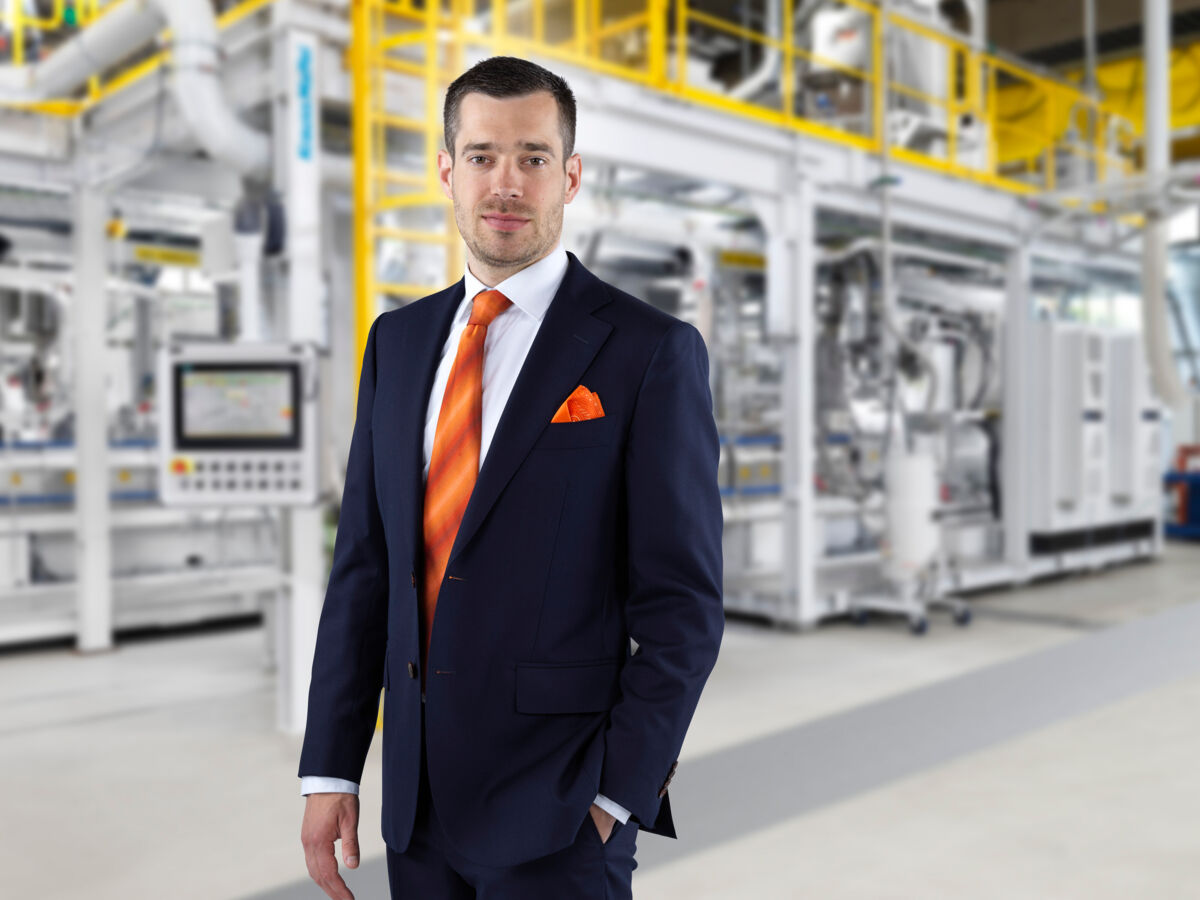
franz-xaver.keilbach@kraussmaffei.com
Trouver des articles sur des sujets similaires:
CES ARTICLES POURRAIENT VOUS INTERESSER
Polyplastic LTD opts for KraussMaffei twin-screw extruders to extend its production capacity
31.08.2025 | Andreas Weseler