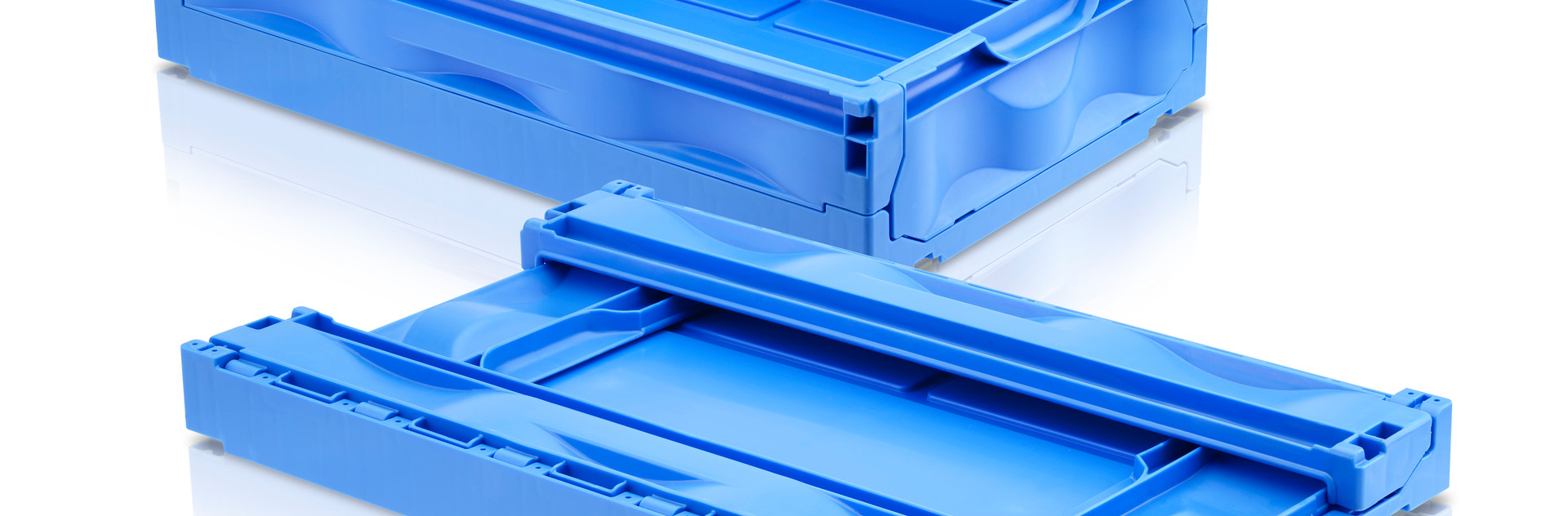
Durabilité
Un nouveau matériau fabriqué à partir de trois produits recyclés
| Petra Rehmet
En direct de la K 2022 : des caisses réutilisables fabriquées à partir de trois produits recyclés
Lorsqu'il s'agit de recycler les matières plastiques, les attentes et la réalité divergent souvent. Cela s'explique par le fait que le polymère pur n'est disponible qu'en quantités limitées. Il faut donc utiliser un maximum de ressources pour atteindre le volume nécessaire de recyclat. Avec le Direct Compounding Injection Molding (DCIM), KraussMaffei démontrera au K 2022 comment un nouveau matériau peut être composé à partir de trois recyclats de viscosités différentes.
Les masques FFP2 sont partout ! Que faire des déchets créés lors de la production ? Il faut les recycler, bien sûr. Le voile de fibres discontinues en polypropylène est aussi liquide que l'eau (taux de fusion volumique MVR 800-1000), totalement différent des déchets déchiquetés de PEHD provenant de la production de pièces moulées par soufflage issu de l'industrie du jouet (MVR < 1). Si vous ajoutez le PEHD provenant de la production de moulage par injection, dont la consistance est similaire à celle du miel (MVR 5-15), vous avez les trois composants qui se mélangent pour former un nouveau matériau.
KraussMaffei concentre sa présence au salon sur l'économie circulaire. De plus, la technologie DCIM avec son extrudeuse à vis unique joue un rôle central. Il convient pour des poids d'injection de 50 à 2000 grammes et complète ainsi le système IMC (Injection Molding Compounder, avec extrudeuse à double vis), qui fait ses preuves depuis plus de 20 ans et qui est économiquement attractif pour des poids d'injection de 1500 grammes ou plus.
Réduire les coûts avec DCIM
En raison du coût actuel des polymères, les négociants en matériaux ne sont plus en mesure d'acheter suffisamment de matériaux recyclés pour couvrir les demandes. Il est donc nécessaire d'agir soi-même. Le procédé DCIM (Direct Compounding Injection Molding) facilite cette démarche en mélangeant, modifiant avec des additifs, renforçant (ou remplissant) le matériau et en l'introduisant directement dans le processus de moulage par injection.
Le processus DCIM permet d'économiser les coûts de composition externe (en moyenne, environ 0,6 €/kg) et donne au transformateur un contrôle maximal sur les matériaux utilisés.Franz-Xaver Keilbach
Global Product Owner - Économie circulaire / Recyclage
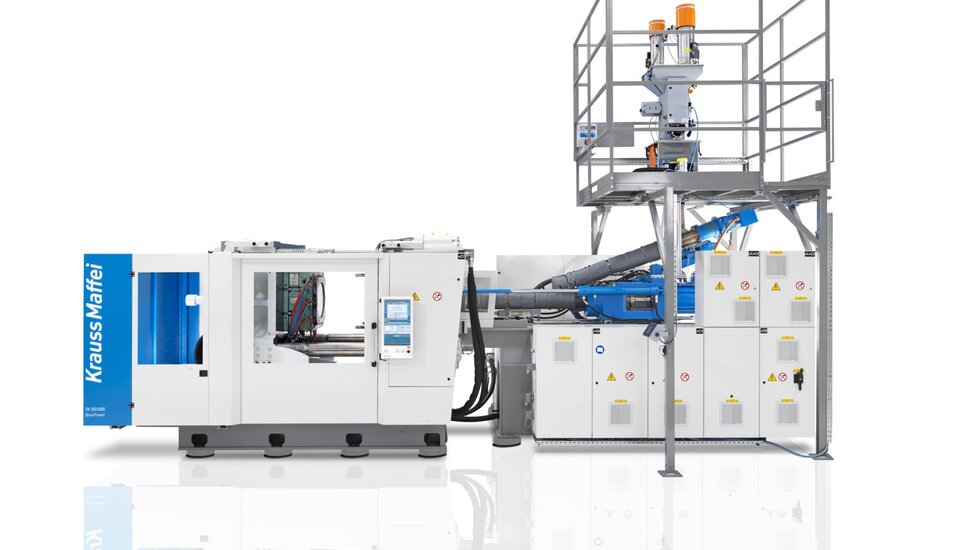
Moulage par injection et compoundage dans un même processus de chauffage
La technologie DCIM de KraussMaffei permet de gagner un temps de cycle précieux et de réduire les coûts des matériaux jusqu'à 50 %.
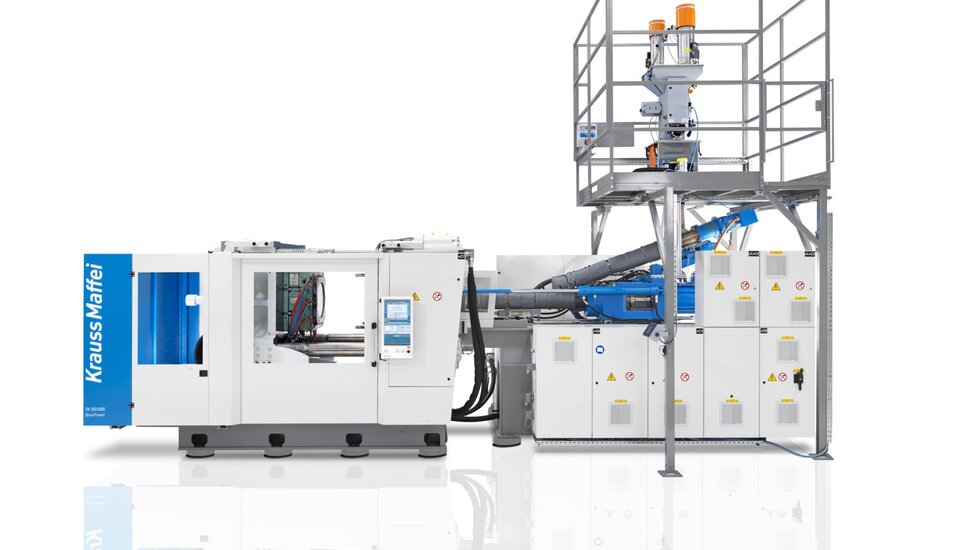
Pour le procédé DCIM, une extrudeuse à vis unique est installée en position "piggyback" directement au-dessus de l'unité d'injection d'une machine hydraulique standard (généralement de la série GX). Les deux produisent en mode intermittent, ce qui signifie que l'extrudeuse s'arrête lorsque le volume d'injection pour le cycle suivant est atteint.
Pour le salon, les trois matériaux sont en outre mélangés avec le mélange principal, l'additif stabilisant et l'oxyde de fer micacé comme charges. Ce dernier élément permet de réduire le temps de refroidissement jusqu'à 10%. La vis spéciale de l'extrudeuse permet de transformer les six composants individuels en une masse fondue homogène. Elle a une conception optimisée et une longueur extraordinaire. Le rapport entre la longueur et le diamètre est généralement de 17 à 23 L/D (presse à injecter standard), mais pour la technologie DCIM, le rapport est de 30 L/D, un chiffre remarquable.
La production de chaleur unique permet d'économiser une énergie précieuse
Compte tenu du problème énergétique actuel, il est également particulièrement intéressant que toute la production soit réalisée en un seul processus de chauffage, de sorte que la masse fondue composée passe directement de l'extrudeuse à l'unité de plastification de la presse à injecter, sans interruption et sans perte de chaleur. Ce processus en une seule étape permet d'économiser de l'énergie, de réduire l'empreinte de CO2 et de ménager le matériau puisque la dégradation du polymère est réduite.
Des caisses de transport durables composées de trois matériaux recyclés différents
Sur le stand du salon, le nouveau plastique polyoléfine ainsi créé est transformé en caisses pliables, comme celles utilisées pour le transport de poisson frais. Le temps de cycle de la GX 1100-4300 DCIM est d'environ 35 secondes. Elle convient donc parfaitement au procédé DCIM car, à partir de 20 secondes environ, le traitement supplémentaire des matériaux n'a aucun impact sur le temps de cycle.
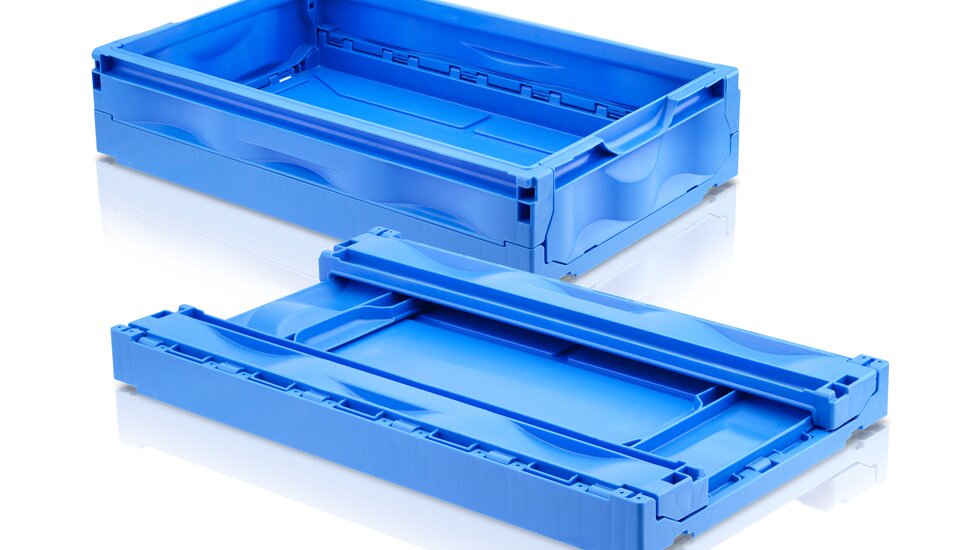
Au K 2022, un GX 1100-4300 DCIM produit des caisses réutilisables à partir de trois recyclats différents.
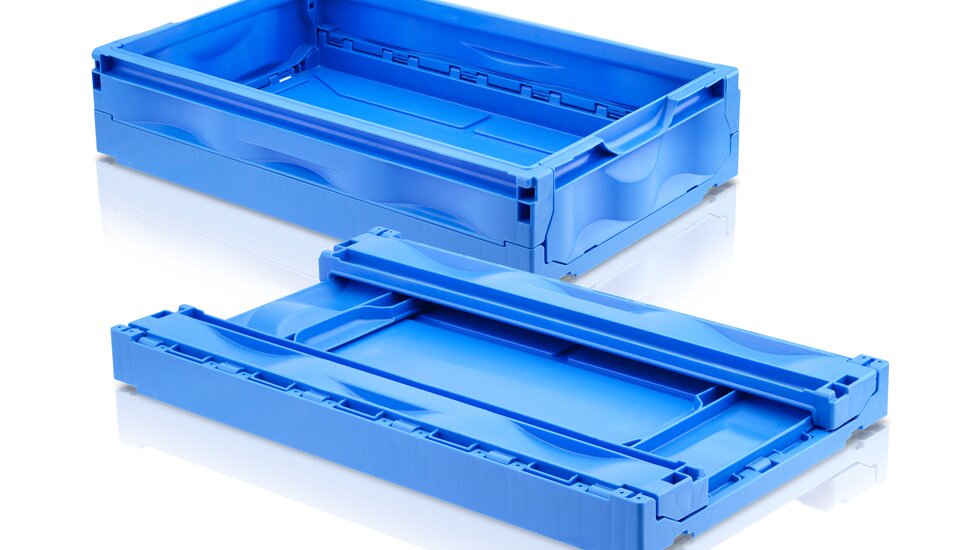
La plupart des pièces techniques qui entrent en jeu pour le compoundage direct se situent au-dessus de cette limite. Ici, un robot linéaire LRX 350 démoule les cinq pièces individuelles (SCS moldmaking) et les transfère à un système d'automatisation de Campetella, qui se charge de l'insertion, du clippage et de l'empilage des caisses.
Assumer la responsabilité des matériaux et contrôler les formulations
Il est certain que les avantages financiers du compoundage direct (environ 30 à 50 %) sont primordiaux pour l'industrie de l'emballage et de la logistique, qui est tributaire des prix. Toutefois, pour les fabricants de pièces techniques, un autre facteur peut entrer en jeu : l'intendance des produits. Les entreprises - comme les fabricants de composants liés à la sécurité - confrontées à un litige et devant prouver que les articles qu'elles ont livrés étaient parfaitement corrects, peuvent également souhaiter contrôler les matériaux et ne pas dépendre d'un fabricant externe. Par ailleurs, en cas de nouveaux projets ou de modifications des exigences mécaniques, ces entreprises pourront également développer leurs propres formulations et les proposer au client.
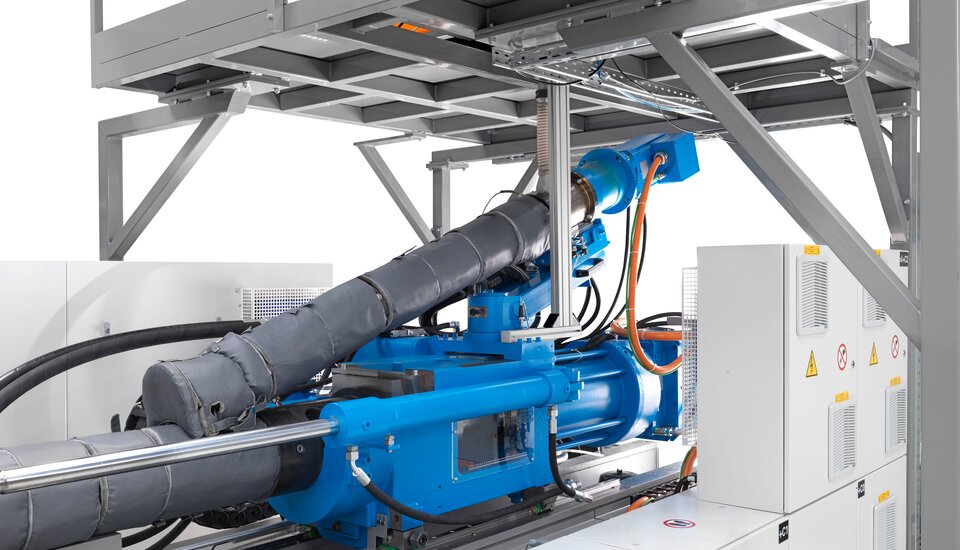
Economiquement attractif, notamment pour les pièces de 50 à 2000g.
Le procédé DCIM de KraussMaffei utilise une extrudeuse à une vis.
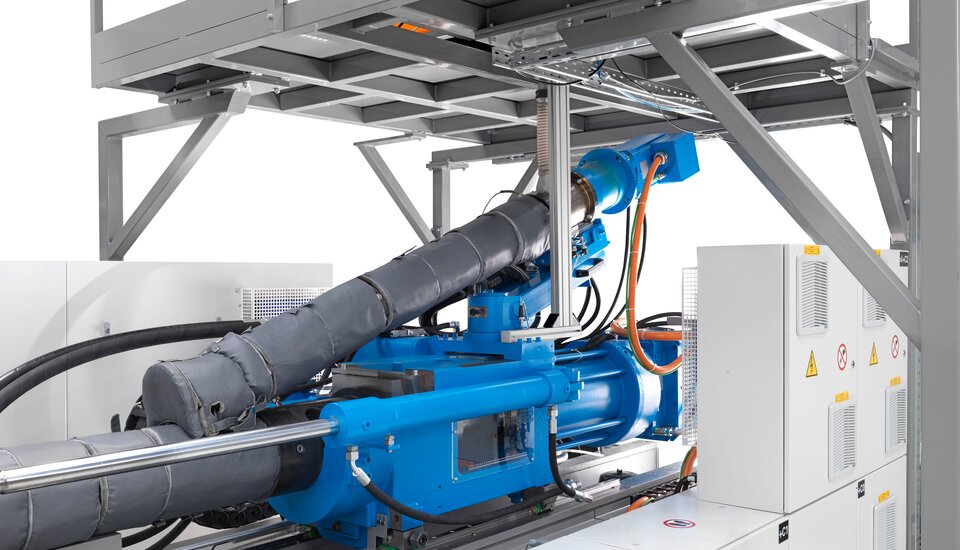
Le concept étant basé sur une machine standard, les coûts supplémentaires pour l'équipement DCIM sont faibles et s'amortissent en peu de temps. Si aucun composé n'est nécessaire pour le moment, la machine peut également être utilisée dans le cadre d'un moulage par injection standard sans nécessiter de transformation complexe. L'utilisateur bénéficie ainsi d'une flexibilité maximale et est équipé pour faire face aux évolutions futures liées à l'économie circulaire.
Nous remercions nos partenaires
BIG-SPIELWARENFABRIK GmbH & Co. KG (film soufflé) ; Schoeller Allibert Services B.V. (produits de moulage par injection en PEHD) ; Zettl Meditec GmbH (masque FFP) ; Audia Plastics s.r.o. (mélange principal de couleurs) ; Byk Chemie (additifs), Kärtner Montanindustrie (oxyde de fer micacé) ; Campetella Robotic Center srl (automatisation) et S.C.S. Societa Construzione Stampi (moules).Contact
franz-xaver.keilbach@kraussmaffei.com