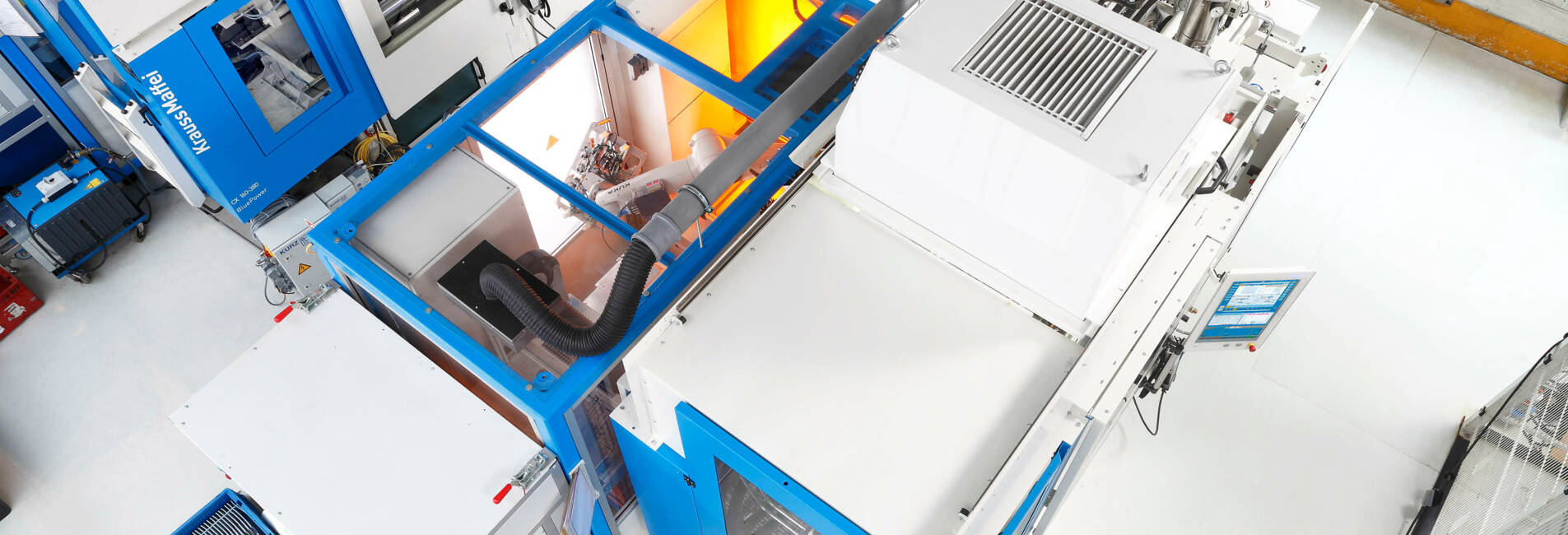
Trendgineering
Automobilzulieferer KDK profitiert von IMD-Technologie
| Petra Rehmet
Zwei identische Anlagen auf Basis der CX 160
Kleiner geht's nicht: Der Oberflächenspezialist KDK in Lennestadt entschied sich für zwei IMD-Anlagen von KraussMaffei. Diese beanspruchen so wenig Stellfläche wie kaum ein anderes Maschinenmodell im Schließkraftbereich und die Automationszellen können zudem abgedockt werden.
In den neuen Fertigungszellen entstehen filigrane Lüfterrahmen sowie mehrere Versionen der Blende Climatronic für den VW Tiguan, die im In-Mold-Decoration-Verfahren (IMD) oberflächenveredelt werden. Dafür läuft eine Folie mit entsprechender Beschichtung vertikal durch das Zwei-Kavitäten-Werkzeug. Das Werkzeug schließt sich und die Beschichtung überträgt sich auf die Oberfläche des Kunststoffteiles mittels Spritzdruck und Temperatur.
Ein Sechs-Achs-Roboter entnimmt die Rahmen und führt sie einer UV-Station zu, wo die Beschichtung glasartig aushärtet, und legt das fertige Bauteil auf ein integriertes Förderband ab. Rund 3000 Bauteile entstehen so pro Tag und Maschine.

In Serie für den VW Tiguan
In einem 1+1 Kavitäten-Werkzeug entstehen filigrane Lüfterrahmen (links). DIe Blende Climatronic wird in einem 1-fach Werkzeug gefahren (rechts).
Multinationaler Experte
Die KDK-Unternehmensgruppe beliefert von ihren Standorten in Lennestadt, Wächtersbach, Tachov/Tschechien und Borja/Spanien aus alle namenhaften OEMs und Tier-One-Supplier mit Produkten für den Autoinnenraum – wie z.B Dekorteilen, Mittelkonsolen oder Kofferraumsystemen. KDK Lennestadt ist dabei der Spezialist für die Oberflächendekoration mittels Folie und verfügt über alle technischen Möglichkeiten für IMD und IML (In Mold Labeling). Die rund 300 Mitarbeiter haben den Anspruch, jede vom Kunden gewünschte Oberfläche zu realisieren, wobei der Schwerpunkt auf kratzfesten und chemikalienbeständigen Dekoren liegt. Neben den Folienfachleuten sind im Sauerland auch die Abteilungen für Entwicklung und Projektmanagement ansässig, so dass viele Projekte zentral über diese Fertigungsstätte gestartet und dann transferiert werden.
Innerhalb der Unternehmensgruppe sieht man sich durchaus im Wettbewerb zu den „Low-cost“-Betrieben in Tschechien und Spanien, weshalb das Thema Automation eine besondere Rolle spielt. Schon seit 20 Jahren verfügen alle Spritzgießmaschinen über einfache Entnahmesysteme – frei fallende Teile gibt es nicht.
Erleichterte Handhabung dank abdockbarer Automationszelle
Seit gut fünf Jahren stellt der heutige Werkleiter Andre Winkelmann fest, dass die Anwendungen immer komplexer werden. Um für alle Herausforderungen flexibel zu bleiben, legte KDK beim aktuellen Projekt als Grundanforderung eine abdockbare Automationszelle fest, welche auf Schwerlastrollen gelagert frei beweglich ist. So ist die Nutzung der Spritzgießmaschine ohne Automation ebenso möglich wie das Verlagern der Zelle an einen anderen Einsatzort und bietet maximale Flexibilität beim Produkt- oder Werkzeugwechsel.
KraussMaffei lieferte als Generalunternehmer das Gesamtpaket mit CX 160-Spritzgießmaschine und Laminar-Flow-Box zur Staubreduzierung, mit einer Folienabrolleinheit (Kurz), einem Sechs-Achsroboter (Kuka) mit artikelspezifischen Greifer, einer produktspezifischen Angussbeschnittlösung einer UV-Station mit integriertem Förderband und einem Handarbeitsplatz.

Platzsparend und ergonomisch:
Die CX 160 bietet eine gute Zugänglichkeit zum Wechseln der Folienrollen. Die gesamte Folienperipherie (Aufwicklung, Steuergerät) lassen sich unter der freitragenden Schließeinheit integrieren.
Die CX 160 mit ihrer frei tragenden Schließeinheit und dem Raumangebot darunter ermöglichte eine optimale Integration der Folien-Peripherie. Die Zwei-Platten-Bauweise erlaubt einen schnellen Zugang zu den Folienrollen. In Kombination mit der für den IMD-Prozess optimierten Maschineneinhausung erleichtert das wiederum den Wechsel der Folien.
"Wir haben zum ersten Mal eine 160-Tonnen-Maschine, die mit der gesamten Technologie (IMD + Automation) ausgestattet ist, alle Sicherheitsanforderungen erfüllt, maximale Funktionalität aufweist und das auf kleinster Stellfläche."Andre Winkelmann, KDK-Werkleiter in Lennestadt
Geringste Ausschusswerte in Produktion
Bei der Lieferantenauswahl stand neben dem kompakten und praxisnahen Konzept auch die Einhaltung eines engen Liefertermins im Vordergrund, schließlich mussten zum Projektstart einsatzbereite Maschinen und validierte Produktionsprozesse verfügbar sein. Von der Performance ist Andre Winkelmann ebenfalls überzeugt: "Ein 1:1 Leistungsvergleich kann leider nicht gemacht werden, da der Tiguan-Rahmen eine neues Bauteil ist. Wir konnten aber im Bereich Zykluszeit, aber auch Bauteilqualität sehr gute Ergebnisse erzielen. Durch die einmalige Verwendung der IMD-Folie sind Ausschuss und Prozessfähigkeit bei uns ein großes Thema. Die Anlagen von KraussMaffei erzielen aktuell die geringsten Ausschusswerte in unserer Produktion."
Diese Werte fließen in die KDK-Datenbank ein, in der bereits 12 Millionen Folienbauteile mit den dazugehörigen Prozessinformationen gespeichert sind. Auf diesen Datenschatz kann das KDK-Team bei der Beurteilung von Ausschusszahlen ebenso zurückgreifen wie bei der Entwicklung neuer Bauteile.
Gerade bei Folientechnologien ist es sinnvoll, den späteren Produzenten so früh wie möglich in den Design- und Konstruktionsprozess einzubeziehen, weil zum Beispiel beim IMD dafür gesorgt werden muss, dass sich eine 2D-Folie an ein 3D-Bauteil anschmiegen kann.
Wie früh KDK oft mit an Bord ist, zeigte auch der neue Opel Insignia, der 2017 in die Autohäuser kam. Hier wirkte das Team bereits seit drei Jahren an der Entwicklung der Innenraumkomponenten mit und hat die Wünsche des Kunden umgesetzt sowie die Produktion dieser Bauteile erfolgreich gestartet.
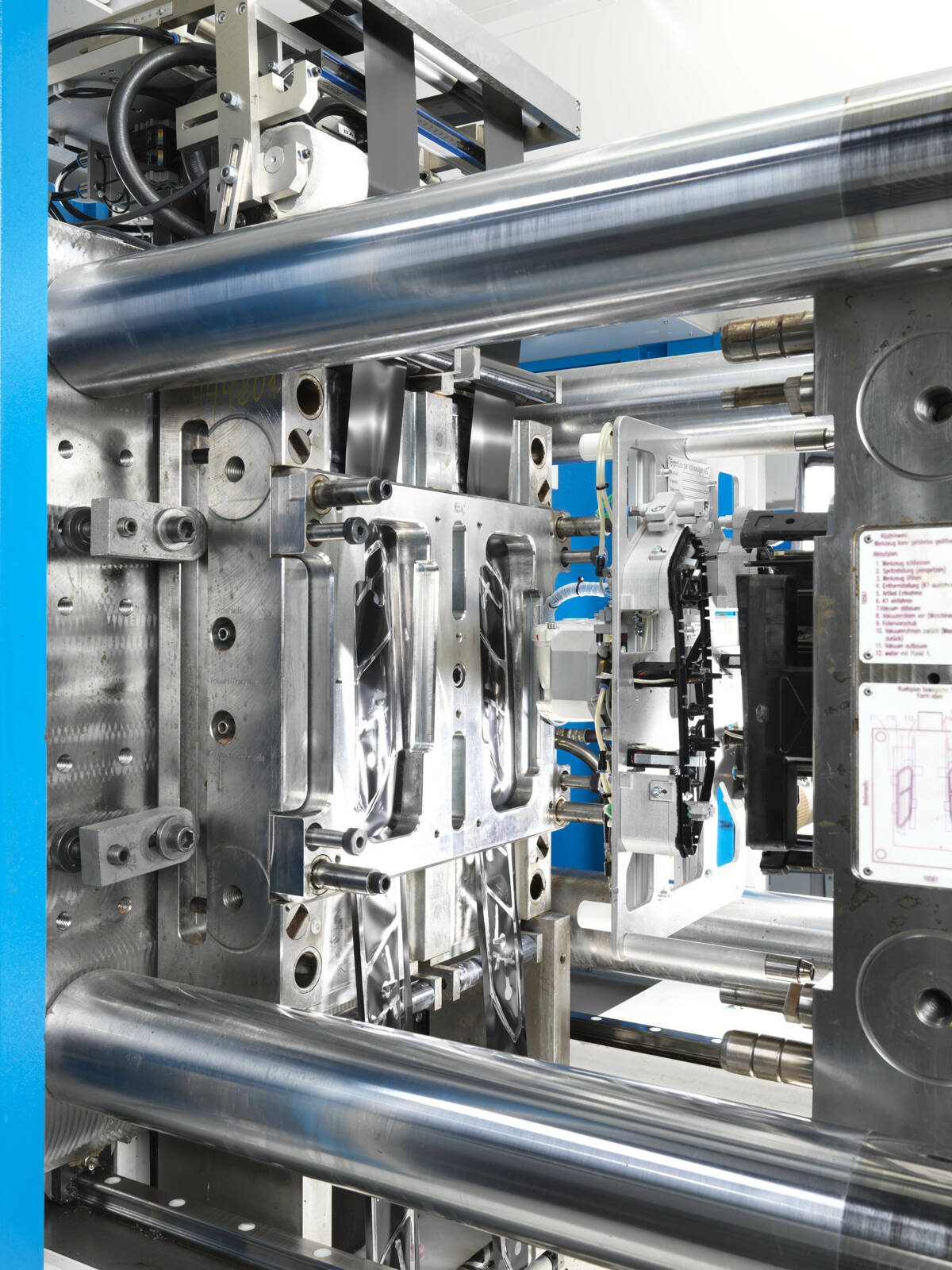
Blick ins Werkzeug:
Die zwei Kavitäten sorgen für erhöhten Output. Der artikelspezifische Greifer entnimmt die Bauteile präzise und legt sie ab.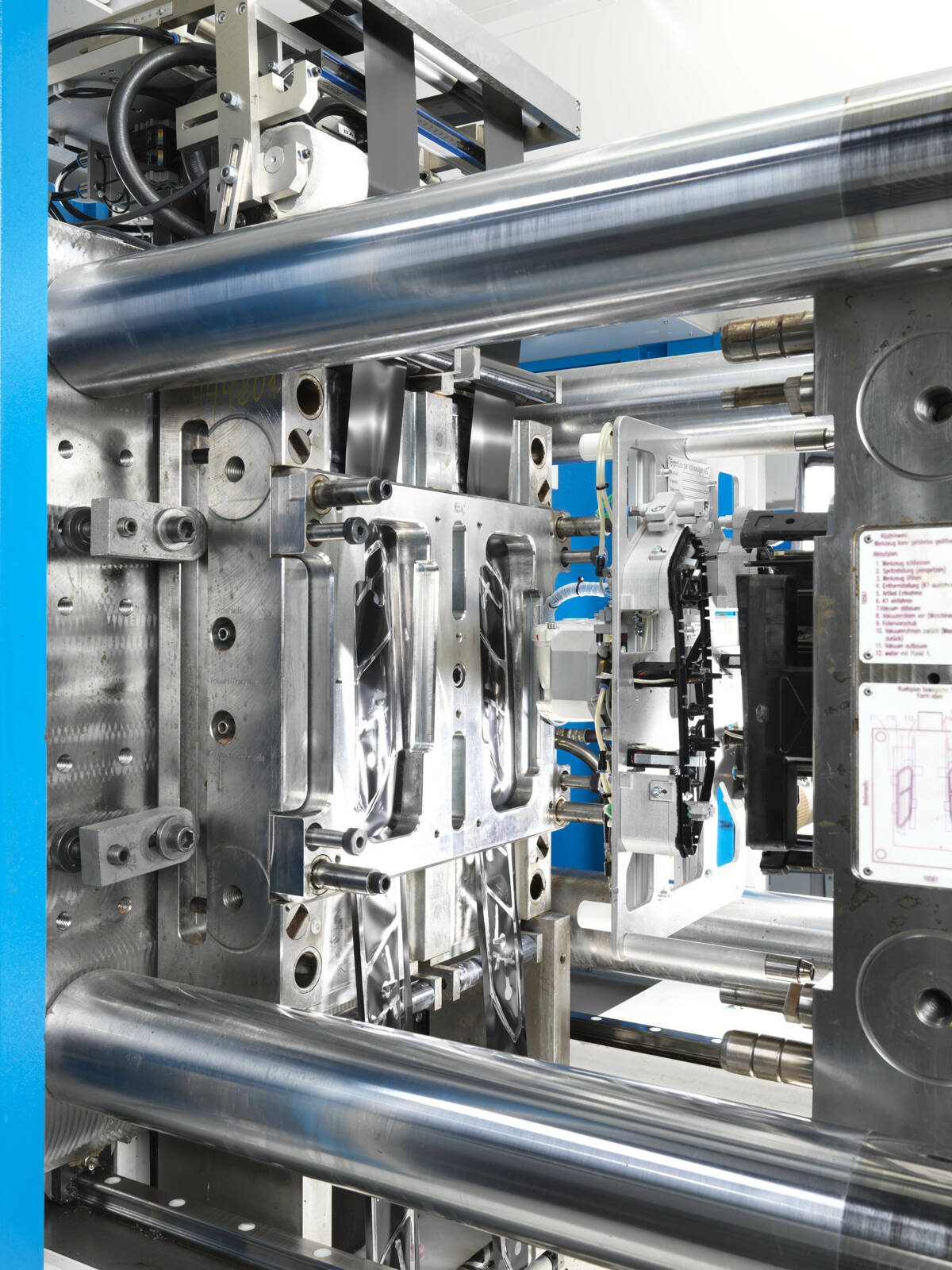
Sofern es die Teilegeometrie zulässt, bietet IMD im Vergleich zu IML meist die günstigere Alternative, weil es bei letzterem erforderlich ist ein Inlay (Folie die tiefgezogen und beschnitten wurde) zu fertigen und anschließend in einem 2. Produktionsschritt in ein Spritzgusswerkzeug einzulegen und zu hinterspritzen.
Find articles with similar topics:
Ähnliche Artikel
Transparenz mit Tiefenwirkung: Hochwertige Oberflächen nachhaltig produzieren
20.08.2025 | Michael Fuchs, Gerhard Konrad