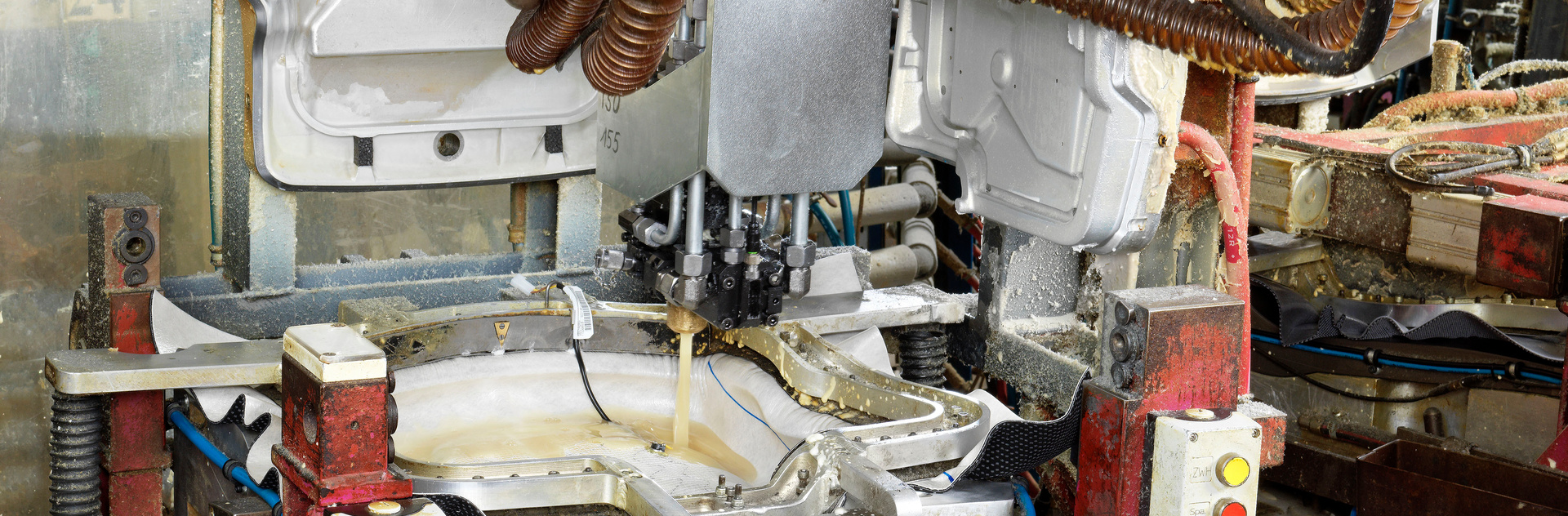
trendgineering
Schlank und leistungsfähig
| Michaela Huber
Grammer testet neu entwickelten Hochdruckmischkopf in der Serie
Auf Traktoren und Gabelstaplern oder im großen LKW: Überall dort, wo sich ein Sitz mit markantem Rippenmuster in der Lehne zeigt, blickt man auf ein Produkt des Marktführers Grammer AG. Bereits in 400.000 Fällen wurde das PUR-Schaumpolster mit dem neu entwickelten precisionMixhead 8/12-2K-40 von KraussMaffei gefertigt, der beim langjährigen Kunden und Partner seinen ersten Serieneinsatz erlebt.
Kleiner, leichter und mit noch besserer Mischqualität: So lautete die Zielsetzung als Ende 2020 das Projekt Mischkopf-Redesign begann. Das Team um Ralf Moser (Entwicklungsleiter Mischköpfe) nahm damit die Wünsche von Kunden auf, für die eine bequeme Handhabung im Fertigungsalltag wichtig ist. Meist hängt der Mischkopf an einem sich schnell bewegenden Roboter, der ihn von Form zu Form transportiert, wo er dann offene Schäumbahnen einträgt.
Gelegentlich muss er, bei geschlossenem Werkzeug, sogar präzise in eine Öffnung eintauchen: Da zahlt sich eine „schlanke Linie“ aus. Obwohl das bisherige Modell über eine ausgezeichnete Mischgüte verfügte, sollte diese noch einmal gesteigert werden – was ebenfalls gelang. Dadurch öffnet sich ein größeres Produktionsfenster, vor allem im Hinblick auf Austragsleistung und Drücke. Entsprechend positiv sind die Rückmeldungen nach dem ersten Serieneinsatz bei Grammer, der inzwischen über 400.000 Schuss andauert.
Wir finden, dass der Mischkopf wegen vieler Details noch einmal eine Verbesserung gegenüber der älteren Version ist, mit der wir auch schon sehr zufrieden waren.Heinrich Hammer
Leiter Verfahrenstechnik Grammer
Als weltweit führender Anbieter von Sitzlösungen für Nutzfahrzeuge sowie einem noch größeren Bereich, der sich mit Interieurelementen für Automotive befasst, ist Grammer ein Schwergewicht mit 14.000 Mitarbeitern und 46 Fertigungsstandorten in 19 Ländern. Seit der Gründung als Sattlerei im Jahr 1880 hat sich das Unternehmen kontinuierlich weiterentwickelt und neue Technologien erschlossen – wie auch die Herstellung von Polyurethan (PUR). Im Werk Haselmühl bei Amberg fertigen über 1.000 Mitarbeiter unter anderem mehr als 600.000 Sitze pro Jahr.
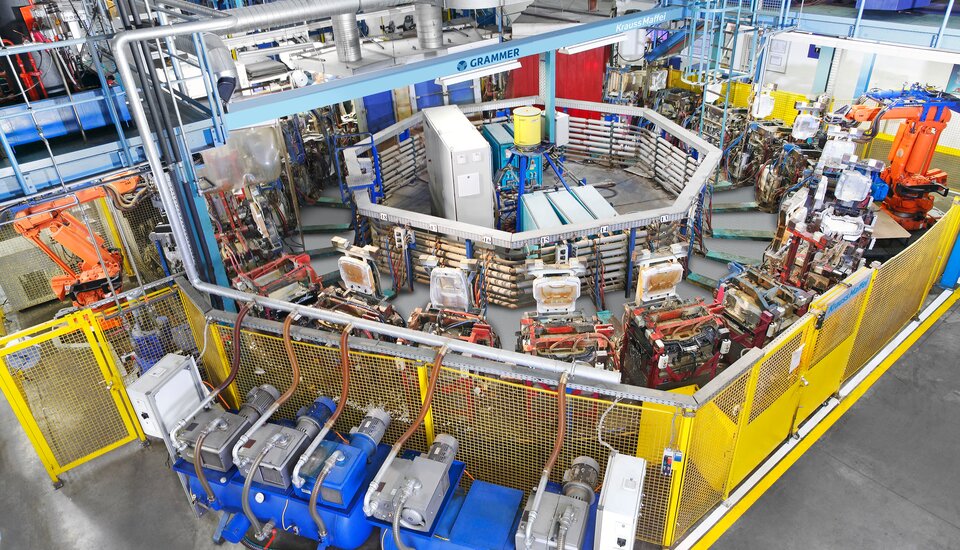
In einer Rundtischanlage mit 24 Stationen entstehen die Sitze mit dem bekannten Grammer-Muster in der Rückenlehne. Links im Bild der Roboter mit dem neuen Mischkopf von KraussMaffei.
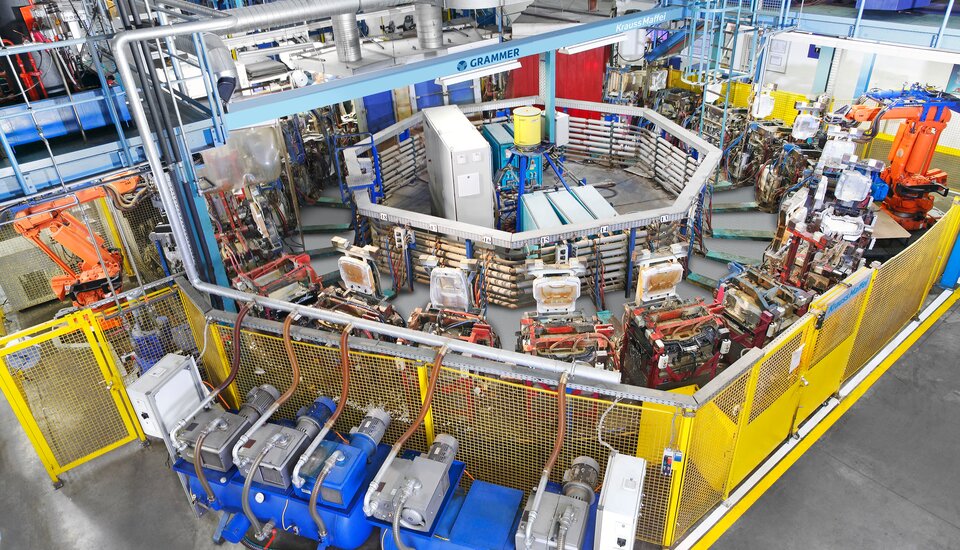
Der precisionMixhead 8/12-2K-40 bedient hier eine der beiden Rundtischanlagen (ebenfalls von KraussMaffei) für Traktoren-, Baumaschinen- und Gabelstaplersitze. Um jeden Drehteller sind über 20 Formen angeordnet. Hier fährt zunächst der neue Mischkopf in das offene Werkzeug, in das bereits der Bezug eingelegt und über Vakuum eingezogen wurde, und füllt es mit Weichschaum. Ein Deckel schließt die Form nach oben ab und das PUR reagiert aus.
Nach jedem Füllvorgang dreht sich der Tisch um eine Station weiter und das Werkzeug erhält eine Abdeckung mit neuer Geometrie, die diesmal gleich geschlossen wird. In den dadurch entstandenen Hohlraum trägt ein zweiter, in den Deckel eingetauchter Mischkopf (ebenfalls 8/12 von KraussMaffei) einen Kompaktschaum ein, der als Rahmen für die Befestigung des Sitzes dient. Nach sechs Sekunden ist dieser Schaum fest genug, dass der Mischkopf seine Öffnung wieder freigeben kann, etwas später öffnet sich der Deckel und das nun fast fertige Polster fährt weiter zum vollautomatischen Laserbeschnitt. Auf diese Weise entstehen jeden Tag mehrere Tausend Teile – mit einem äußerst geringen Ausschuss auf die gesamte Prozesskette.
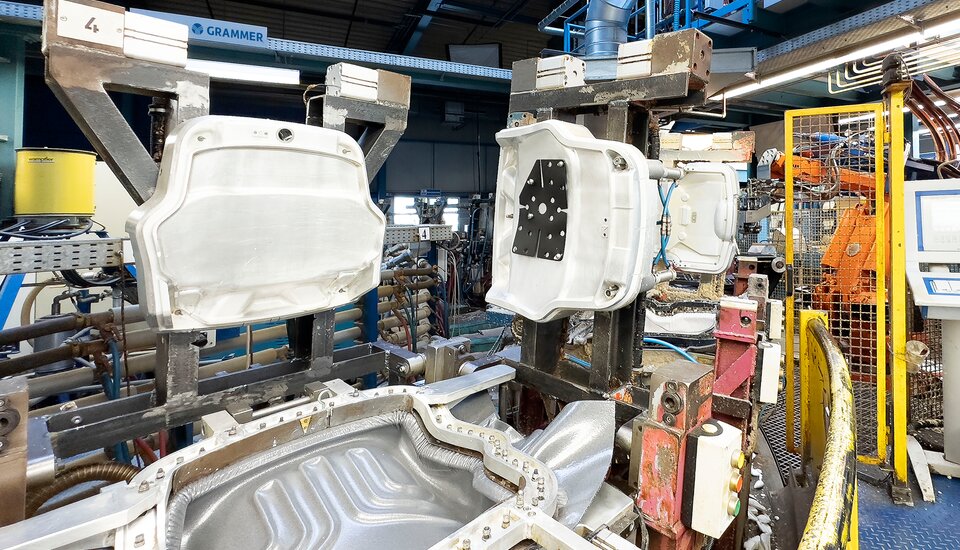
Jede Form verfügt über zwei Deckel mit unterschiedlicher Geometrie, um per Hartschaum auch die Halteelemente fertigen zu können.
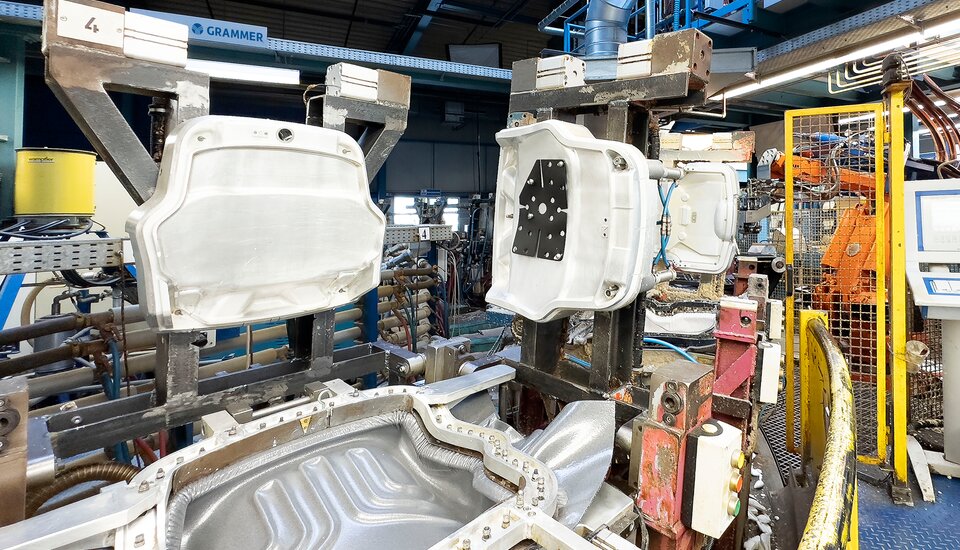
Die Mischköpfe sind dabei das Herz der PUR-Schäumanlage, denn hier entscheidet sich, ob die Komponenten Polyol und Isocyanat homogen und im gewünschten Verhältnis vermischt werden. Geschieht das nicht, zeigen sich am ausgetragenen Material beispielsweise klebrige Stellen (wenn das Polyol vorläuft) oder das Schaumkissen ist entweder zu hart oder zu weich. Letzteres darf schon deshalb nicht passieren, weil jeder der großen Hersteller von Gabelstaplern und Traktoren eigens definierte Härtegrade für seine Sitzpolster hat.
Wie vollzieht sich der Mischungsprozess?
Polyol und Isocyanat befinden sich in einem Kreislaufsystem vom jeweiligen Tagesbehälter zum Mischkopf und zurück, über (per Nadel gedrosselte) Düsen erfolgt das Einströmen in die Mischkammer. Allerdings nur dann, wenn der mit Rezirkulationsnuten versehene Steuerkolben den Weg freigibt. Wenn nicht, bleibt es beim Kreislauf. Dieses System gewährleistet, dass Druck, Menge, Temperatur und Strömungsgeschwindigkeit der Komponenten immer konstant an der Düse anstehen.
Soll ein Materialaustrag erfolgen, dann öffnet der Steuerkolben den Weg zur Mischkammer so lange bis das Schussgewicht erreicht ist. Dieses berechnet sich aus Austragsleistung mal Zeit, beispielsweise 200 Gramm mal fünf Sekunden ergibt ein Kilogramm PUR. In der Mischkammer werden die Komponenten bei 100 bis 200 bar ineinander verdüst und vermischt. Für die Anwendung in offenen Formen braucht es einen L-förmig aufgebauten Umlenkmischkopf wie auch der precisionMixhead einer ist.
KraussMaffei hält für diese Technologie seit den 1980er Jahren zahlreiche Patente. Hier wird der entstehende Schaum im 90-Grad-Winkel in die Auslaufkammer umgelenkt und durch einen Reinigungskolben vollständig ausgetragen. Wenn man den Übergang von Misch- zu Ausgangskammer verengt, indem man den Reinigungskolben etwas vorstehen lässt, findet hier eine zusätzliche Nachvermischung statt und das Auslaufverhalten beruhigt sich.
Die Schilderung zeigt: Es ist ein komplexer Prozess. Bei der Optimierung eines bestehenden und bewährten Hochdruckmischkopfes gilt es also analytisch vorzugehen, weshalb das Team um Ralf Moser Strömungssimulationen als Grundlage nutzte. Der Komponenten-Mix lässt sich am besten bewerten, wenn die Durchflussmenge möglichst gering ist.
Heinrich Hammer erläutert: „Wir fahren in der Serie mit 220 bis 250 Gramm pro Sekunde. Beim neuen Mischkopf haben wir versucht, extreme Grenzbereiche auszuloten und sind bis auf 60 Gramm runtergegangen. Hier kann es manchmal passieren, dass inhomogene Bereiche mit Härteabweichungen (Hart-Weich-Unterschiede links/rechts) auftreten. Beim neuen Mischkopf waren Homogenität und Gleichmäßigkeit aber immer noch top.“
Einen ersten Eindruck von der Schaumgüte erhält man durch einen sogenannten Becherschuss von etwa 60 Gramm in ein transparentes Gefäß oder einen „Fisch“, also flächig auf einen beschichteten Karton ausgetragenes PUR. Die Praxiserfahrung mit dem precisionMixhead 8/12-2K-40 deckt sich mit den Strömungssimulationen, die das Team von KraussMaffei und die TU Chemnitz im Zuge der Entwicklung gemacht hatten. Die Mischqualität konnte tatsächlich um den Faktor drei verbessert werden.
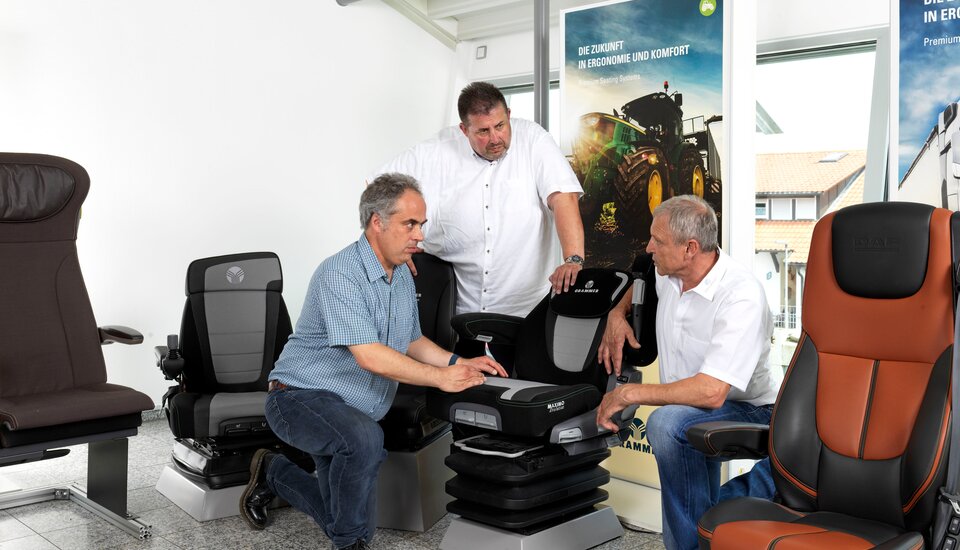
Rolf Moser (Entwicklungsleiter Mischköpfe bei KraussMaffei Technologies GmbH, ganz links) und Wolfgang Rößler (Area Sales Manager RPM, KraussMaffei Technologies GmbH, Mitte) tauschen sich kontinuierlich mit den Experten von Grammer wie Heinrich Hammer (Teamleiter Verfahrenstechnik Schaum, Grammer Deutschland GmbH, rechts) aus, denn moderne Sitze sind Hightech.
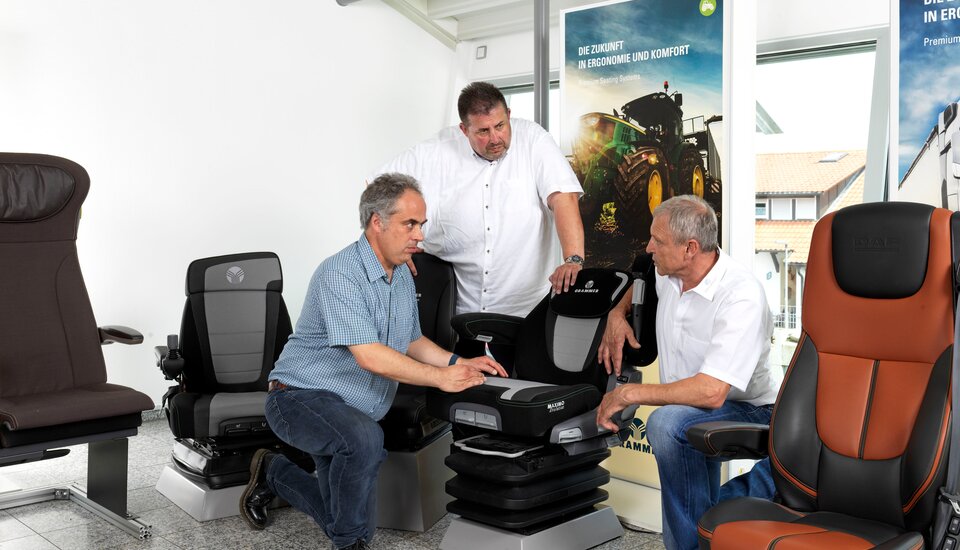
Damit dies präzise gelingt, setzt Grammer seit Jahren Variodüsen von KraussMaffei ein. Im Unterschied zu federbelasteten Standarddüsen (die ausreichend Genauigkeit für viele Anwendungen bieten), arbeiten diese mit einem Luftpolster, das sich in einem Gasraum hinter der Düse befindet. Es steht unter einem Druck von 160 bar, der über eine Membran auf die Nadel übertragen wird.
Diese kann sich so vor- und zurückbewegen, um Druckänderungen auszugleichen, die sich bei Schwankungen des Komponentendurchsatzes ergeben. Da auch fast keine Reibung im System vorhanden ist, herrschen beim Schuss von Anfang bis Ende konstante Druckverhältnisse. Bei federbelasteten Düsen kann es im ungünstigen Fall zu ruckartigen und verzögerten Bewegungen kommen, die dann in Druckänderungen und dadurch ungleichmäßiger Vermischung von Komponenten resultieren.
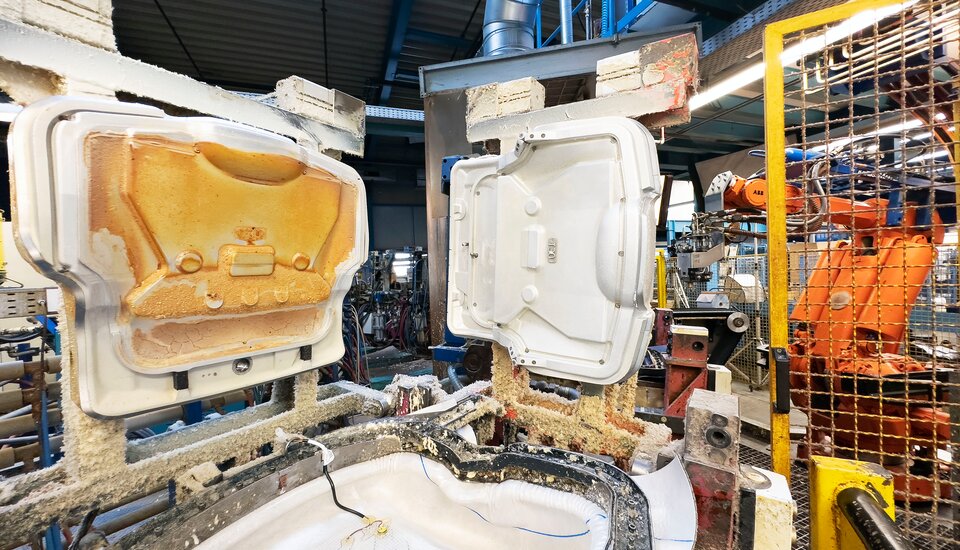
Auch Elemente für die Sitzheizung lassen sich mit etwas Know-how in den Schaum integrieren.
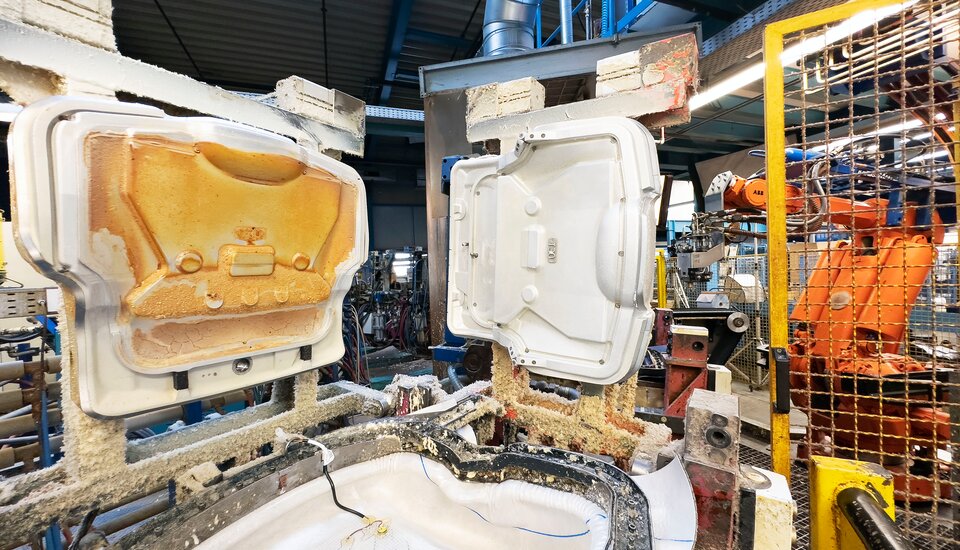
Neben der Mischgüte sollte beim Redesign auch die geometrische Dimension des neuen Kopfes verändert und vor allem verkleinert werden. Gleich beides lässt sich durch die Stellung der Düsen beeinflussen, durch die Polyol und Isocyanat in die Mischkammer strömen. Stehen Sie einander frontal gegenüber, birgt das die Gefahr, dass jede Komponente in den Strömungskanal der anderen eindringt. Besser gelingt die Vermischung, wenn die Düsen in einem Winkel angeordnet sind.
Durch entsprechende Optimierungen gelang es dem Team nun, beide L-Schenkel des Umlenk-Mischkopfes auf 92 beziehungsweise 65 Prozent der ursprünglichen Werte zu reduzieren. Das bedeutet eine Reduzierung des Volumens bis zu 25%. Damit sank auch das Gewicht von 13 auf rund 10,5 Kilogramm.
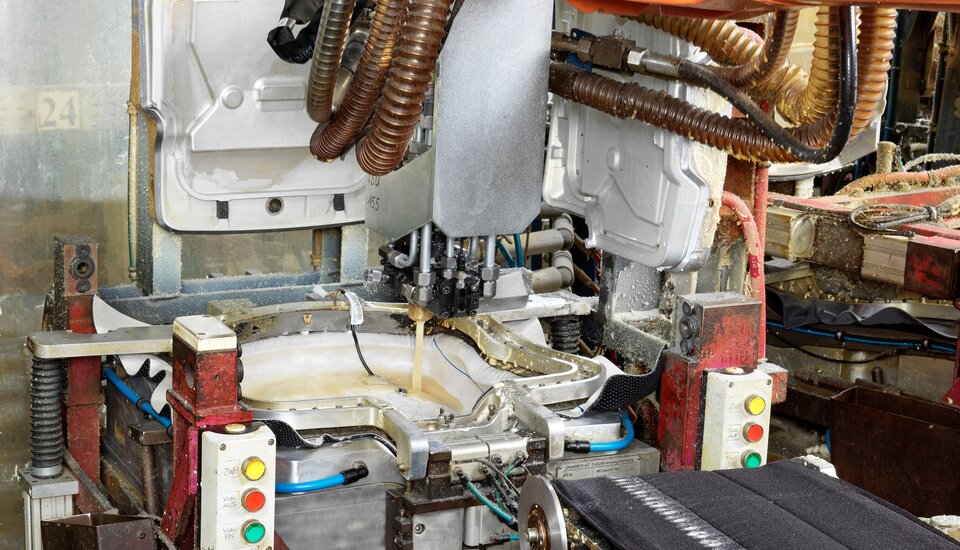
Beim Eintrag bestimmt der Mischkopf über die Homogenität des Schaums – und damit die Qualität des Sitzes.
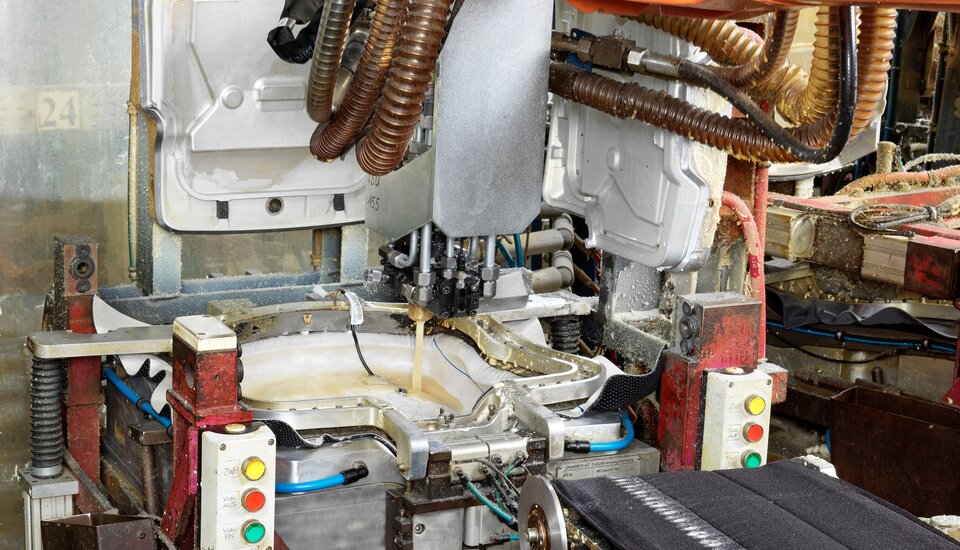
Für Nutzer besonders interessant sein dürfte der schnelle Service, der mit der neuen Generation möglich wird. Mischköpfe müssen regelmäßig gewartet werden, damit sie mit konstanter Leistungsfähigkeit produzieren. Beim precisionMixhead wurden insbesondere die verschleißbehafteten Teile für einen schnellen Tausch konzipiert. Erstmals lassen sich Mischkammer, Auslaufkammer und Steuerkolben bei Verschleiß komplett ersetzen.
Die beiden letzteren sind nun einteilig (vormals mehrteilig) ausgeführt, was wiederum Platz und Gewicht spart. Durch die hohe Verfügbarkeit muss der Kunde auch weniger in Backuplösungen investieren. Für mehr Bedienkomfort wurde das Auslaufrohr mit Durchmesser 25 Millimeter von 32 auf 40 Millimeter zylindrische Länge vergrößert.
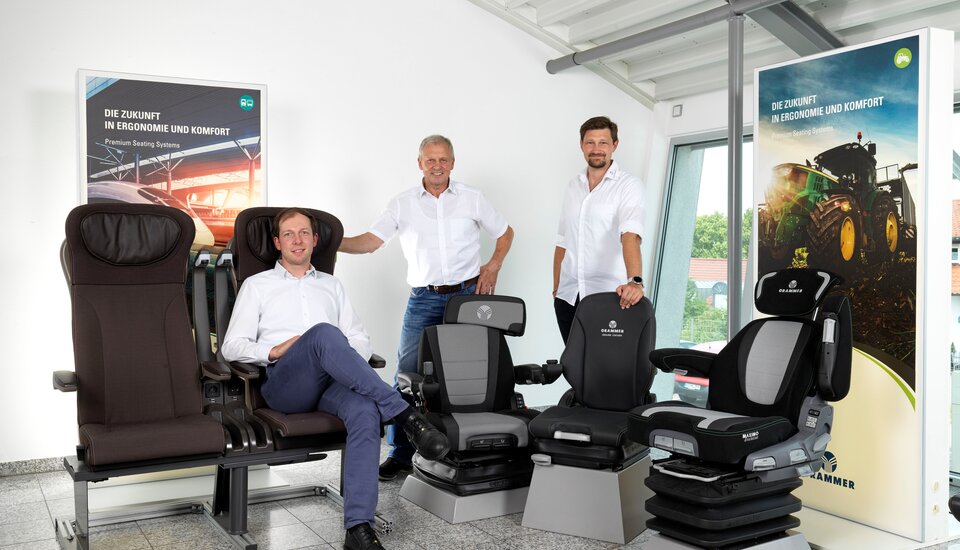
Sie testen den neuen Mischkopf in der Serienproduktion auf Herz und Nieren (v.l.): Martin Wiendl, Leiter Engineering, Grammer Deutschland GmbH, Heinrich Hammer, Teamleiter Verfahrenstechnik Schaum, Grammer Deutschland GmbH, Sebastian Keck, Verfahrenstechniker Schaum und Schäumwerkzeig, Grammer Deutschland GmbH
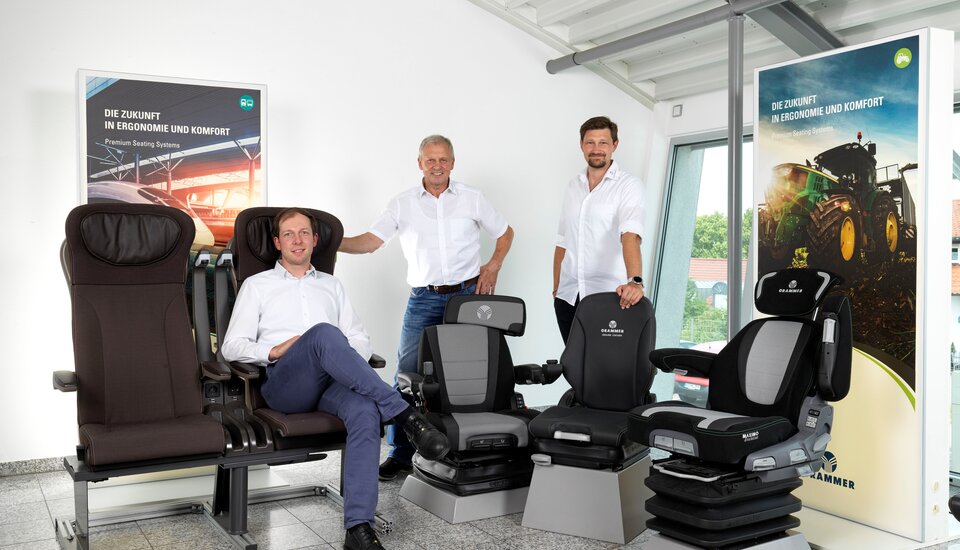
Bei Grammer ist Sebastian Keck (Verfahrenstechniker Schaum und Schäumwerkzeug) nun sehr auf die Standzeit gespannt: „Die Vorgängermodelle haben wir immer nach etwa einer Million Schuss ersetzt, vielleicht hält der neue ja sogar noch länger.“ Die Robustheit der Anlagen ist für Martin Wiendl (Leiter Engineering) ein wesentlicher Pluspunkt von KraussMaffei: „Wir betreiben unsere Rundtische bereits seit 2001, sie sind extrem zuverlässig, mit hoher Anlagen- und Ersatzteilverfügbarkeit, und auch die vertrauten Ansprechpartner sind immer für uns da.“
Im Technikum stehen sogar Dosierveteranen von EMB die seit 1978 (!) laufen und jetzt noch Musterteile fertigen. EMB gehört seit 2002 zu KraussMaffei, sodass Wartung und Ersatzteilversorgung von München aus geschehen. Für die aktuelle Produktion sind inzwischen natürlich neue RimStar-Dosieranlagen zuständig.
Die Zusammenarbeit zwischen Grammer und KraussMaffei läuft partnerschaftlich und erfolgreich seit rund 30 Jahren – und bestimmt auch in Zukunft. Insofern ist es nur logisch, dass der neu entwickelte Präzisionsmischkopf einen seiner ersten Serieneinsätze hier erlebt.
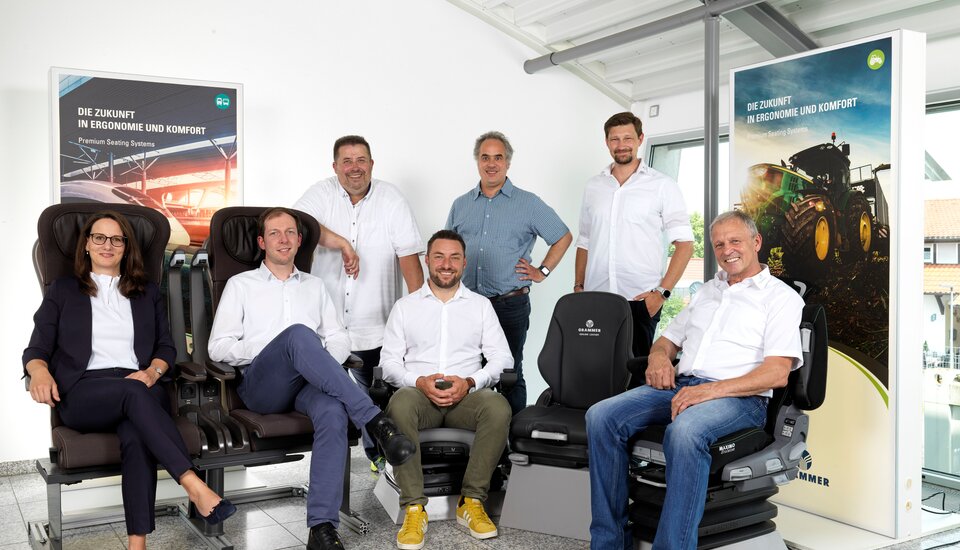
Man kennt und schätzt sich als verlässliche Partner (v.l.): Daniela Horvat, Product Manager RPM, KraussMaffei Technologies GmbH, Martin Wiendl, Leiter Engineering, Grammer Deutschland GmbH, Wolfgang Rößler, Area Sales Manager, KraussMaffei Technologies GmbH, Michael Fuchs, Global Application Owner Composite & Surface, KraussMaffei Technologies GmbH, Ralf Moser, Entwicklungsleiter Mischköpfe, KraussMaffei Technologies GmbH, Sebastian Keck, Verfahrenstechniker Schaum und Schäumwerkzeig, Grammer Deutschland GmbH, Heinrich Hammer, Teamleiter Verfahrenstechnik Schaum, Grammer Deutschland GmbH
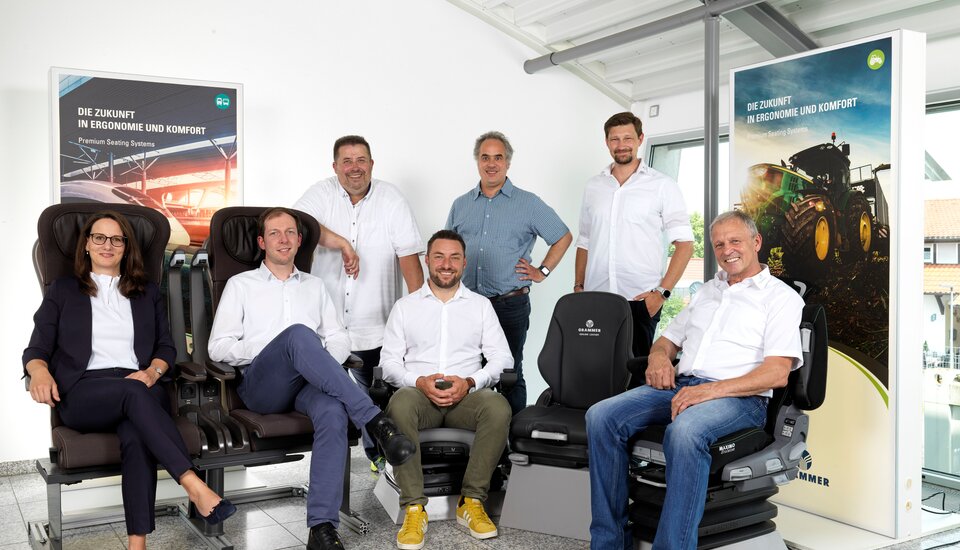
Kontakt
ralf.moeser@kraussmaffei.com