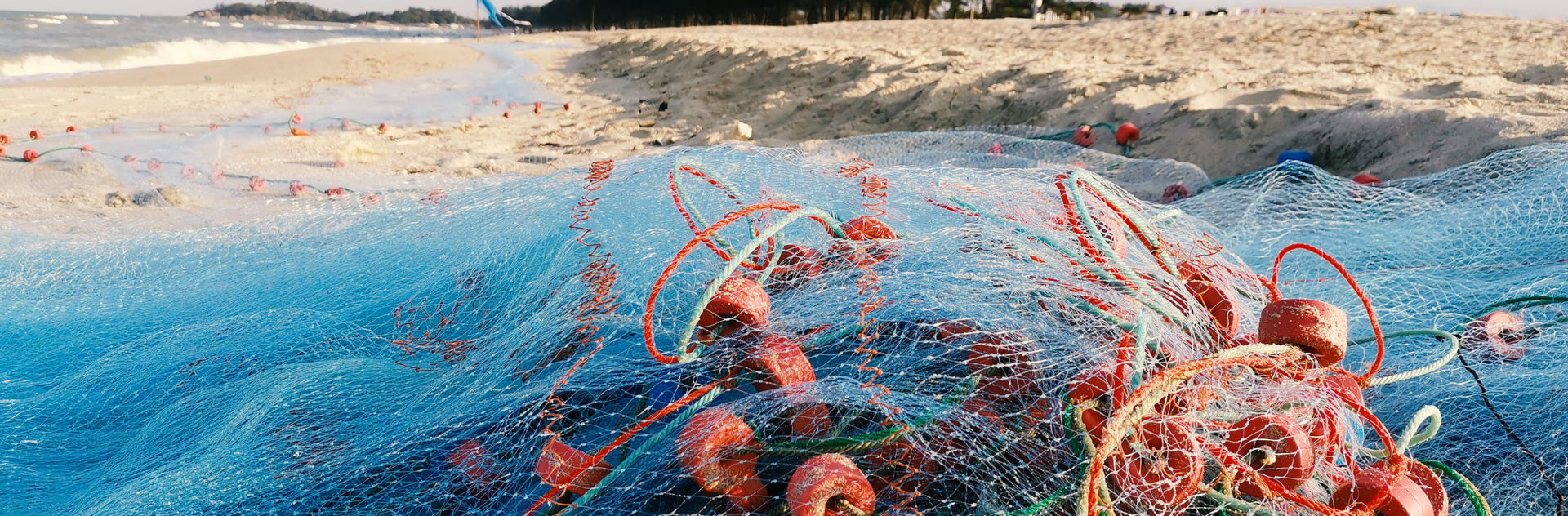
Nachhaltigkeit
Aus dem Meer in den Tunnel
| Petra Rehmet
Oldroyd nutzt 100 Prozent Seaplastics für seine Produkte
Alte Fischernetze und Kunststoffseile: Für die norwegische Firma Oldroyd sind das wertvolle Rohstoffe, aus denen sie auf drei CX 160 Materialien für den Tunnelbau herstellt. Sie sind langlebiger als Stahl und schonen auch dadurch die Umwelt. Bei diesen Vorteilen macht es nichts, wenn es manchmal ein bisschen nach Fisch riecht.
Wo steht der längste Straßentunnel der Welt? Wo gibt es über 900 Verkehrstunnel? In Norwegen. Wer im Auto durch die Betonröhren fährt, sieht nicht, womit der KraussMaffei-Kunde Oldroyd sein Geld verdient: Das Membransystem inklusive spritzgegossener Befestigungsartikel liegt dahinter. Es verhindert, dass durch das Erdreich eindringendes Wasser, die Betonschicht beschädigt. Im Grunde funktioniert das wie ein Goretex-Schuh.
Oldroyd kommt ursprünglich aus der Kunststoffextrusion und hat mit seinen Mehrschicht-Folien für den Tunnelbau den Markt revolutioniert, als es die eine Seite nicht mehr schwarz, sondern weiß machte. Dadurch erhöhte sich die Transparenz und Qualität beim Einbau der Membran, weil man durch Steinspitzen entstandene Löcher nun sehen konnte. Auch ist das Arbeiten in einer hellen Umgebung deutlich angenehmer.
Um die Folie am Untergrund zu befestigen, braucht es entsprechende Halteelemente – und hier kommt Firmengründer John Oldroyd Cheetham ins Spiel. Der technisch versierte Tüftler entwickelte dafür innovative Lösungen und erkannte, dass Spritzguss die geeignete Technologie wäre, um sie herzustellen
Unsere Stärke ist es, 'outside the box' zu denken und dann als Familienunternehmen auch schnell zu entscheiden, welchen Plan wir weiter verfolgen wollen.John Oldroyd Cheetham
Firmengründer Oldroyd
Hoher Automationsgrad sorgt für sichere Geisterschichten
Um sich hinsichtlich der nötigen Maschinen beraten zu lassen, konsultierten John Cheetham und sein Team die Saxe Group mit Rolf Kjønnerud als Ansprechpartner vor Ort. Saxe vertritt KraussMaffei in Skandinavien und bietet neben den Maschinen auch einen umfassenden technischen Service. Die Zusammenarbeit zwischen Oldroyd, Saxe und KraussMaffei ist außergewöhnlich.
Gemeinsam versuchen die Partner permanent, neue Ideen zu wagen und vermeintliche Grenzen zu verschieben. Kevin Beuchel, Regional Sales Manager KraussMaffei: „John reizt auch bei unseren Maschinen immer wieder die Möglichkeiten aus, aber das ist gut so und bringt alle voran.“
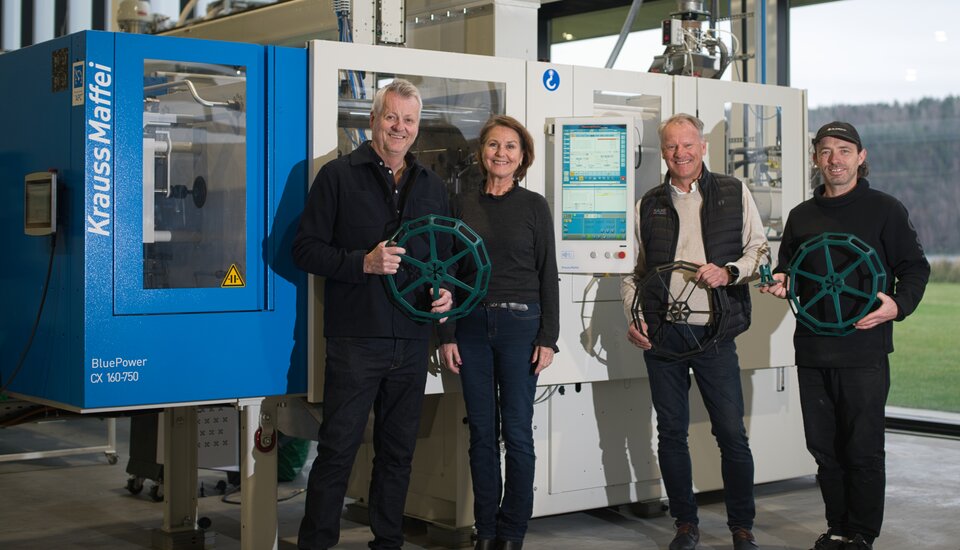
Treiben gemeinsam den nachhaltigen Tunnelbau voran (v.l.): John Oldroyd Cheetham (Firmengründer Oldroyd), Linda A. Celin (CEO Oldroyd), Rolf Kjønnerud (KraussMaffei Agent SAXE) und Carl Kremer (Product Development/Operator Oldroyd) vor einer der CX 160-750
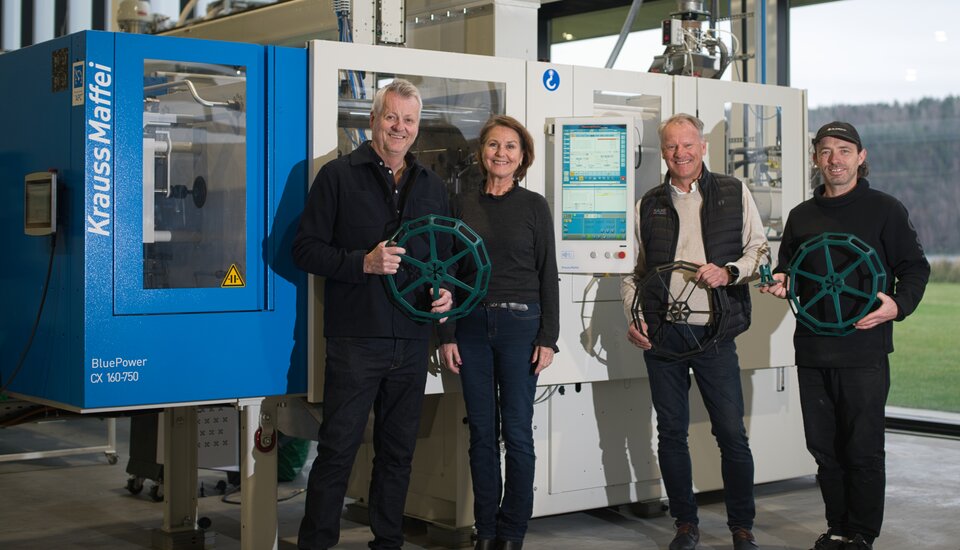
Seit einigen Jahren laufen also in Stathelle (rund 160 Kilometer südwestlich von Oslo) drei identische CX 160-750 und bald kommt eine weitere mit Zweikomponenten-Ausstattung hinzu. Alle Maschinen sind mit den in Deutschland gebauten eigenen KraussMaffei Robotern vom Typ LRX in Übergröße ausgerüstet. Durch die sehr lange vertikale Achsen können diese die Artikel beginnend auf einer ebenerdigen Palette bis zu einer Höhe von 2 Meter stapeln.
Die massive Ausführung und die enorm hohe Verfügbarkeit der KraussMaffei-Roboter versetzen den Kunden in die Lage, sogar über das Wochenende mannlos zu produzieren. Durch die so genannten „Geisterschichten“ werden europäische Produktionen weltweit konkurrenzfähig.
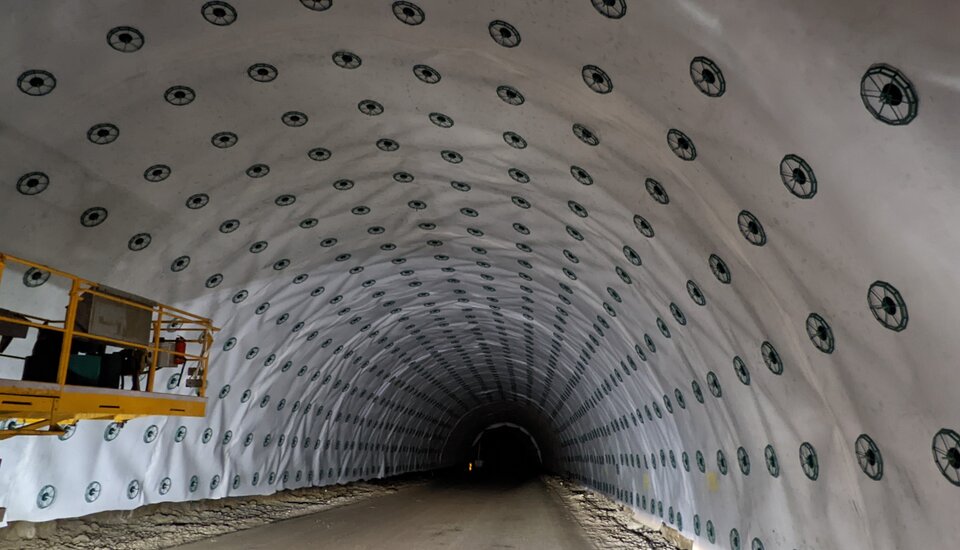
Die sogenannten Spacer schaffen einen Abstand zwischen Gestein und Membran, so wie hier zum Beispiel in den Sandøya Tunnillen auf den Faröer Inseln.
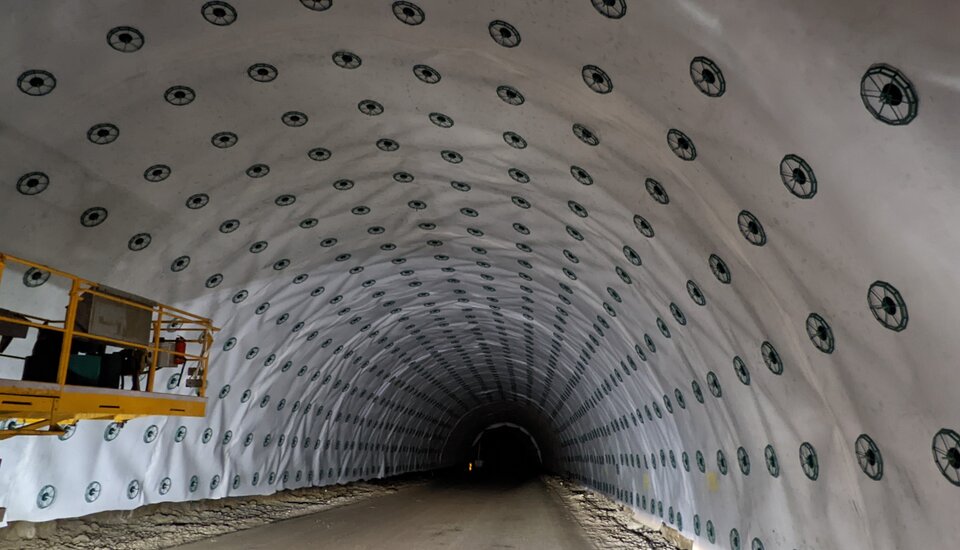
100 Prozent Seaplastics
Wer sich noch nie mit dem Thema Tiefbau beschäftigt hat, mag unterschätzen, um welche Stückzahlen es bei Oldroyd geht. Für einen Tunnel werden allein 300.000 bis 400.000 sogenannte Spacer benötigt. Der gewölbte Artikel mit Gitterstruktur schafft einen Abstand zwischen Gestein und Membran.
Mit seinen 150 Gramm Gewicht entsteht er in etwa 15 Sekunden Zykluszeit. Der Durchmesser und die Höhe variieren, es gibt etwa 20 verschiedene Modelle.
Das Material ist bei Oldroyd eindeutig: 100 Prozent „Seaplastic“, das etwa hälftig aus PP und PE besteht. Die Überbleibsel von kaputten Fischernetzen und Kunststofftauen werden an Norwegens Küste von darauf spezialisierten Firmen gesammelt, zerkleinert, gewaschen und regranuliert. Der dezente Fischduft muss für den Tunnelbau nicht extra entfernt werden.
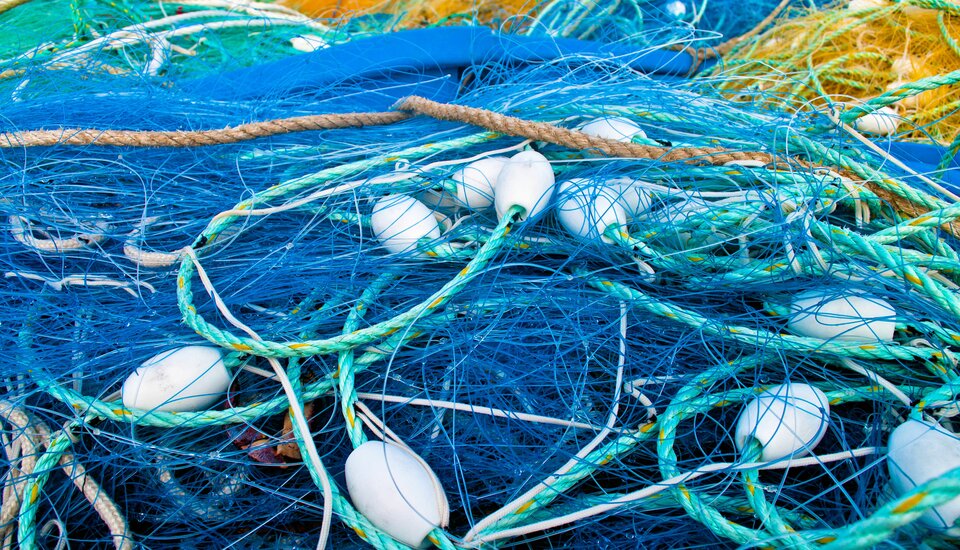
Die alten Fischernetze und -seile werden gesammelt, recycelt und zu 100 Prozent für die Produktion der Spacer genutzt.
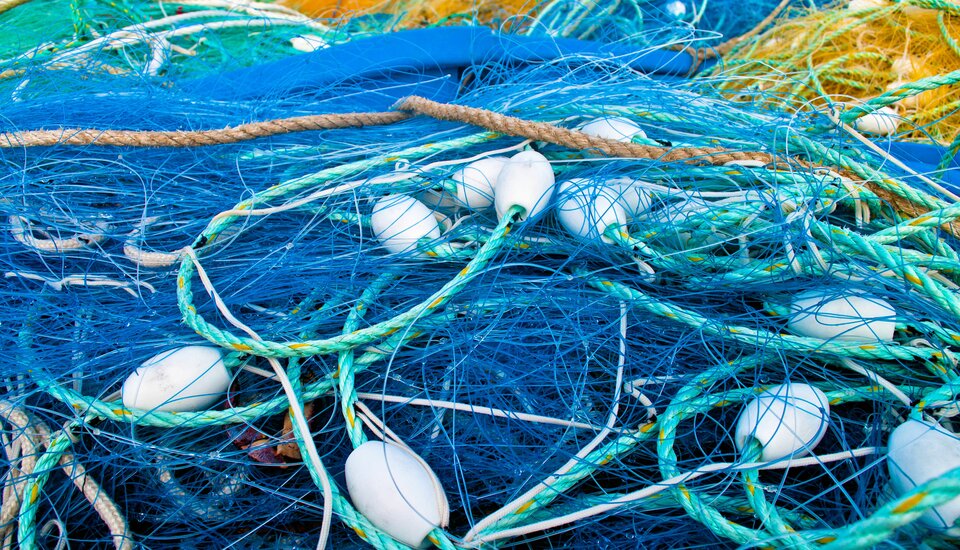
Jedes Teil ein Gutteil dank APCplus
Bei den wechselnden Materialzusammensetzungen und daraus folgenden Viskositätsschwankungen ist die Maschinenfunktion APCplus von KraussMaffei sehr hilfreich. Sie sorgt für ein sehr konstantes Schussgewicht, indem sie den Umschaltpunkt und die Nachdruckhöhe von Schuss zu Schuss anpasst. Das Team hat zusätzlich bereits Tests durchgeführt und anderes Material beigemischt, nur um zu sehen, ob das mit dem APCplus funktioniert.
Es ist für uns sehr beruhigend zu wissen, dass die Maschine alles selbst regelt und wir nach einem Wochenende ganz sicher Gutteile haben werden.Carl Kremer
Product Development/Operator Oldroyd
Dass ein Unternehmen nicht groß sein muss, um erfolgreich zu sein, zeigen Oldroyds Traummaße: 35-15-90. Das bedeutet: 35 Mitarbeiter, insgesamt zehn bis 15 Kunden, 90 Prozent Marktanteil in den skandinavischen Ländern.
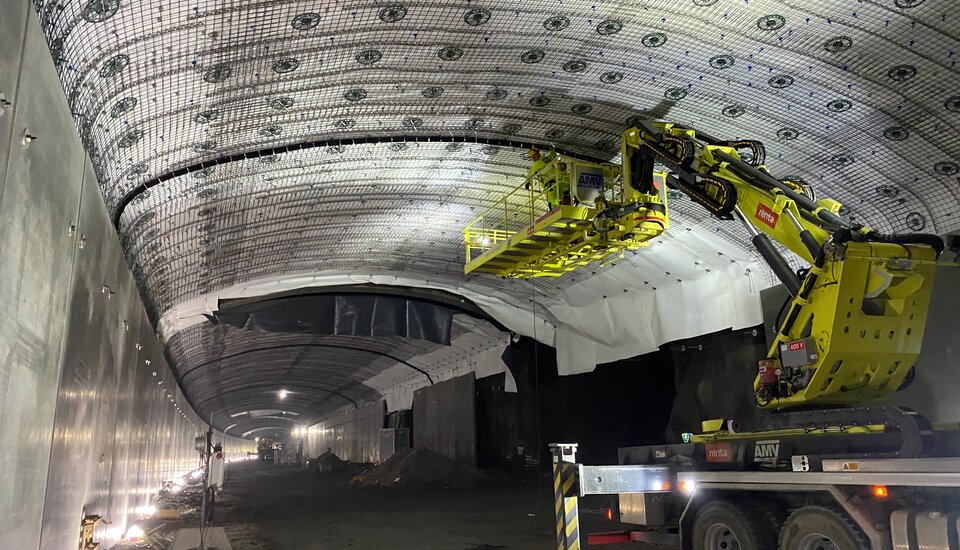
Der Bau des Stockholm Forbifarten ist das derzeit weltweit größte Tunnelprojekt. Auch hier werden die Spacers von Oldroyd zu Tausenden verbaut.
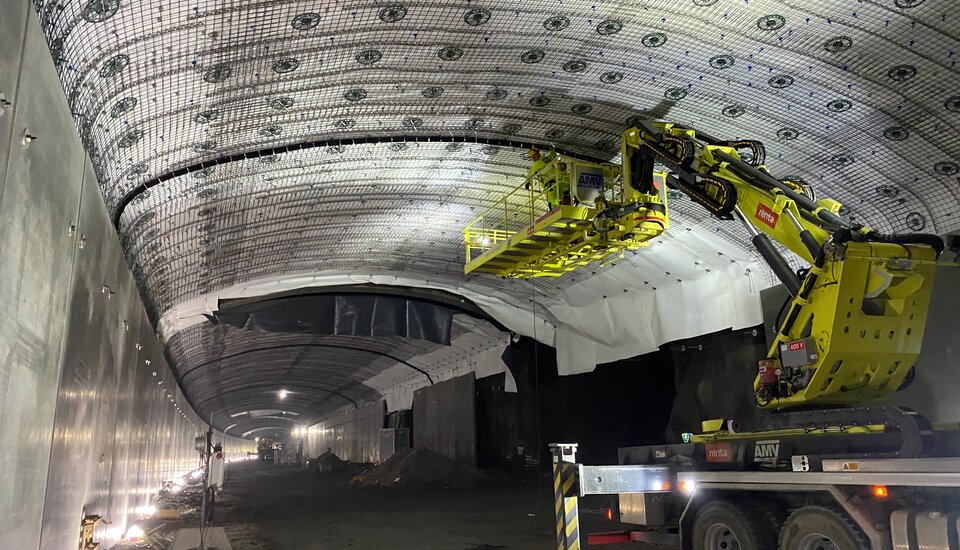
120-Jahre-Produkt RoadStar
In Skandinavien sind Tunnel ein Alltagsphänomen, weil sie genutzt werden, um die vielen Fjorde zu umgehen. Lästige Alternativen wären lange Umwege oder Fähren. 90 Prozent der Wasserschutzausrüstung von Tunneln in Skandinavien kommt aus Stathelle. Damit das so bleibt, gibt es kontinuierlich neue Entwicklungen.
Ganz aktuell eine Zwei-Komponenten-Platte, genannt RoadStar, die auf den Stahlstäben fixiert wird, die die Betonwandung mit der Gesteinsschicht verbinden. Bislang bestehen diese Platten aus Metall und korrodieren entsprechend, weshalb es Wartung und nach etwa 50 Jahren einen Austausch braucht.
Die von John Cheetham erdachten Roadstars wurden in speziellen Alterungstests auf eine Lebensdauer von 120 Jahren veranschlagt. Allein dadurch werden viele Ressourcen eingespart. Um Innovationen zu prüfen, setzt Oldroyd auf die Mithilfe seiner Kunden. Mit diesen arbeitet das Unternehmen seit Jahren vertrauensvoll zusammen und so ist es kein Problem manchmal einen speziellen Tunnelabschnitt für die Einführung einer neuen Technik zur Verfügung gestellt zu bekommen.
Der RoadStar stieß dabei auf Zustimmung, auch weil die integrierte TPE-Schicht auf der einen Seite abdichtend, die andere Seite schlagfest durch PE wirkt. Im Frühling 2023 wird daher eine Zweikomponenten-CX-Maschine die Serienproduktion bei Oldroyd aufnehmen.
Um den hohen Stückzahlenanforderungen gerecht zu werden und durch die vollumfänglich technische Beratung, entschied sich der Kunde für KraussMaffei. Bei einem Markterfolg werden sicher weitere Maschinen den Weg nach Norden antreten. Das nächste Projekt ist übrigens schon in Planung – allerdings noch zu geheim, um darüber zu sprechen.