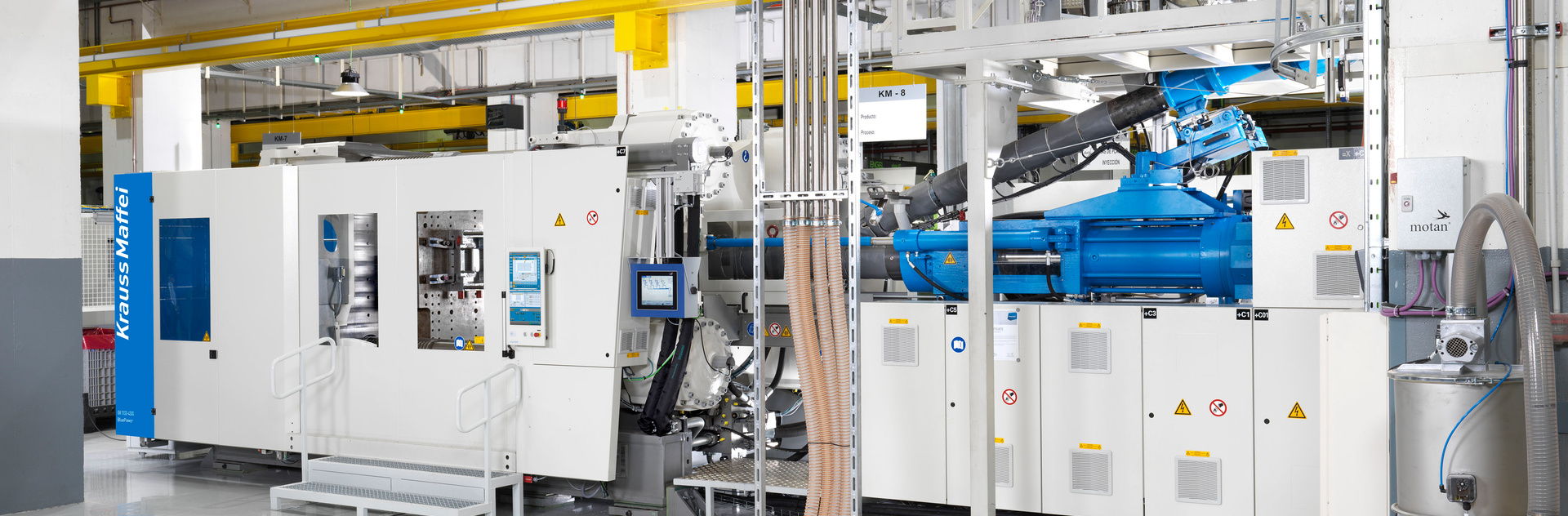
Nachhaltigkeit
Rezeptur in eigener Hand
| Petra Rehmet
DCIM-Direktcompoundieren: ZF Vigo erlangt mit KraussMaffei die Materialhoheit
Die Ansprüche an Rückverfolgbarkeit und Transparenz steigen für Kunststoffverarbeiter ebenso stark wie der Kostendruck. Das ZF-Werk in Vigo / Spanien will deshalb auch polymerseitig die Fäden in der Hand halten und setzt auf Direktcompoundierung. Das neue DCIM-Verfahren von KraussMaffei ist für Bauteile von 50 bis 2.000 Gramm wirtschaftlich attraktiv – und zykluszeitneutral.
Standardpolymere wie PP, PE oder ABS sind bei den großen Materialherstellern jederzeit in gleichbleibender Qualität erhältlich. Ein PP mit 40 Prozent Glasfaser, Masterbatch und Schlagzähmodifizierung – kein Problem, das kommt vom Compounder. Aber ist das wirklich so? Dipl. Ing. Achim Härtel, Core Engineer Plastics bei ZF Alfdorf / Deutschland, hat da schon viele Überraschungen erlebt: „Manchmal war das PP überhitzt, ohne dass es jemand bemerkte, und wir haben auch mehrfach Fremdkörper wie Metallpartikel in Compounds gefunden.“
Wer wie ZF sicherheitsrelevante Bauteile für die Automobilindustrie herstellt, weiß, was es bedeutet, wenn es aufgrund von Fehlern zu Rückrufaktionen oder gar Bandstillständen kommt. Da möchte man das eigene Produkt so gut wie möglich absichern. Und wenn das noch dazu ökonomisch sinnvoll ist, umso besser.
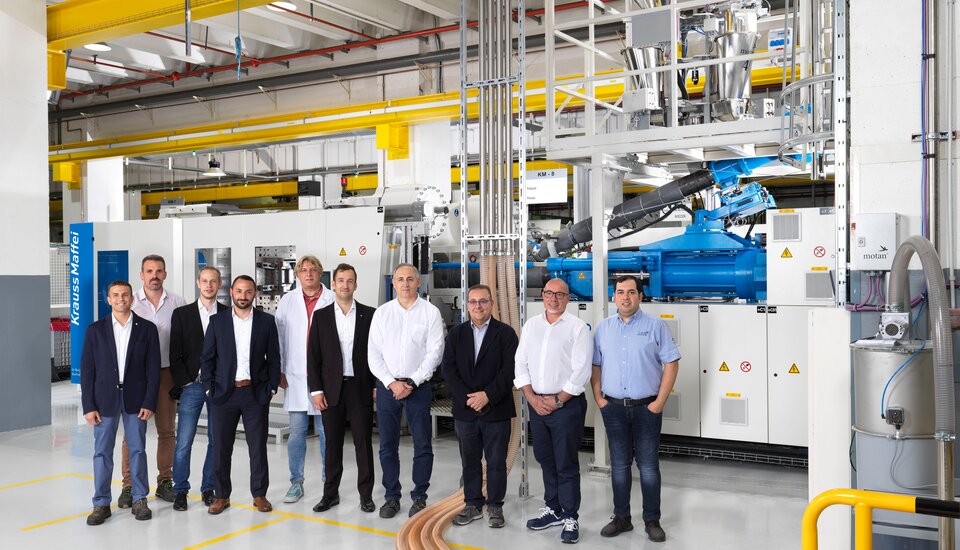
Das Projektteam für die erfolgreiche Directcompoundierung bei ZF Vigo (v.l): Eduardo Casas (ZF, Injection Molding Specialist), Edgar Lopez (ZF, Manufacturing Engineer), Thomas Drogi (KraussMaffei, Process Engineer), Christian Seyferth (KraussMaffei, Global Expert Sales), Achim Härtel (ZF, Core Engineer Plastics), Jacob Seco (ZF, Manufacturing Engineer Specialist), Jose Trasobares (ZF, Manufacturing Engineering Manager), Angel Lemus (Coscollola, Director Post-Venta), Antonio Muñoz (Coscollola, Director Comercial Inyección), Ramazan Baser (Motan-Colortronic, Project Engineer)
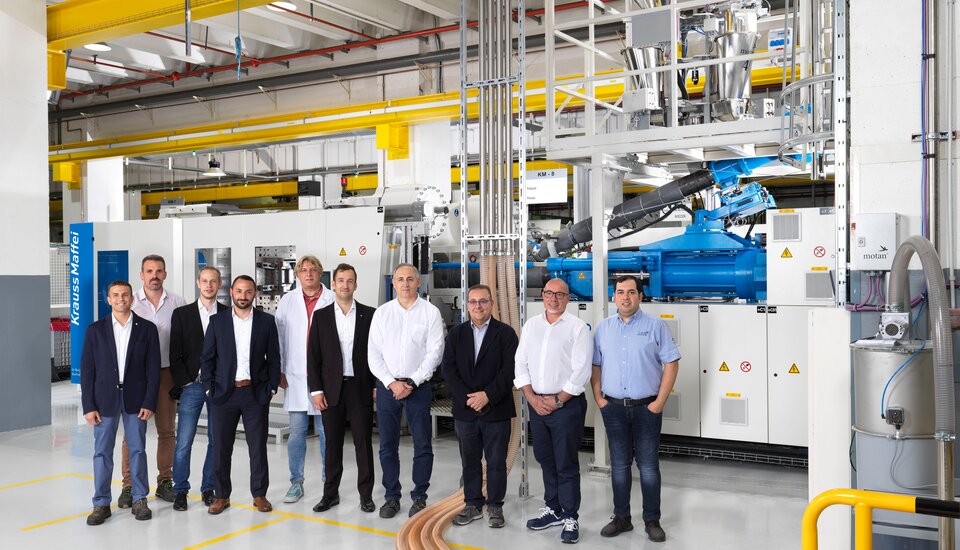
20 Jahre Erfahrung im Bereich Direktcompoundierung
KraussMaffei verfügt über zwei Jahrzehnte Erfahrung im Bereich Direktcompoundierung, allerdings war die bekannte IMC-Anlage (Injection Molding Compounder) mit ihrem Zweischneckenextruder aufgrund der Investitionskosten wirtschaftlich vor allem für Bauteile ab 1,5 Kilogramm Gewicht geeignet. Das neue DCIM-Verfahren (Direct Compounding Inject Molding) erweitert nun das Portfolio. Da es einen Einschneckenextruder verwendet, rechnet es sich schon für Artikel von 50 bis 2.000 Gramm (basierend auf PP natur).
Der Anspruch ist jeweils der Gleiche: Polymere sollen geblendet, additiviert, verstärkt oder gefüllt und in den Spritzgießprozess eingespeist werden. Dies spart einerseits Kosten für das externe Compounding und gibt andererseits dem Verarbeiter maximale Kontrolle über das verwendete Material.
Wir können bei neuen Projekten oder geänderten Anforderungen nun selbst Rezepturvorschläge machen, die direkt auf die Spezifikation des jeweiligen Bauteils zugeschnitten sind. Die Materialqualität liegt dann bei ZF und wir haben das Know-how geschützt im eigenen Haus, vollständig dokumentiert und geprüftAchim Härtel
Core Engineer Plastics bei ZF Alfdorf / Deutschland
Spezielle Extruder-Schnecke sorgt für perfekte Durchmischung
Dafür, dass alle Inhaltsstoffe perfekt durchmischt und homogenisiert werden, sorgt die besondere Schnecke des Extruders, die sich nicht nur durch ihr optimiertes Design auszeichnet, sondern auch über eine außerordentliche Länge verfügt. Für gewöhnlich liegt das Verhältnis von Länge zu Durchmesser bei etwa 17-23 (bei Standard-Spritzgießmaschinen), bei DCIM aber bei enormen 30L/D. Da technische Teile, die für die Direktcompoundierung in Frage kommen, meist Zykluszeiten von 20 Sekunden und mehr haben, lässt sich die zusätzliche Materialaufbereitung sogar zykluszeitneutral gestalten.
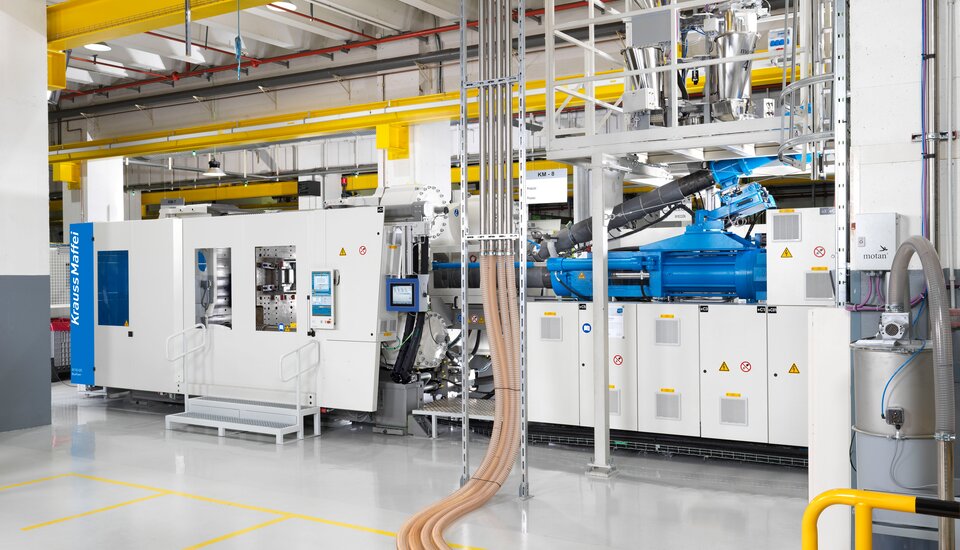
Compoundieren mit DCIM: Der Einschneckenextruder ist bedienerfreundliche in Huckepack-Stellung über der Plastifizierung angebracht.
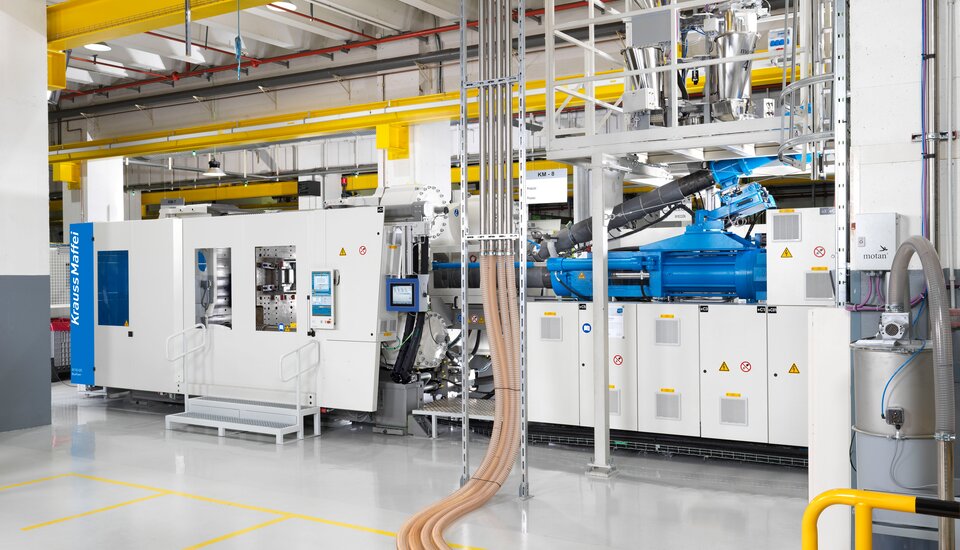
Das DCIM-Konzept bietet dem Kunststoffverarbeiter maximale Flexibilität. Auf eine hydraulische Standard-Maschine - meist der GX-Baureihe - ist der Einschneckenextruder bedienerfreundlich in Huckepack-Stellung über der Einspritzeinheit montiert. Beide produzieren diskontinuierlich. Das heißt der Extruder stoppt jeweils automatisch, wenn das Schussvolumen für den nächsten Zyklus erreicht ist, und die compoundierte Schmelze gelangt ohne Abkühlung oder Zwischenlagerung direkt in die Plastfizierung der Spritzgießmaschine.
Produktion in einer Wärme reduziert den CO2-Fußabdruck
Durch den Einstufenprozess erfolgt die Produktion in einer Wärme, wodurch sich nicht nur der Polymerabbau verringert, sondern zudem wertvolle Energie gespart und der CO2 Ausstoß reduziert wird. Wenn man nicht compoundieren möchte, lässt sich die Maschine ohne aufwändige Umbauarbeiten im Standardbetrieb nutzen. Durch den Z-Aufbau des Aggregats ist die Spritzmaschine sehr kompakt – mit entsprechend kleinem Footprint.
2019 auf den Markt gebracht, wurde DCIM in der Corona-Zeit etwas ausgebremst, findet nun aber immer mehr Interessenten. Für Achim Härtel von ZF zeichnet es sich gegenüber Verfahren anderer Anbieter, die Endlosfasern mit niedrigviskosem Matrixmaterial imprägnieren, dadurch aus, dass man auch Kunststoffe mit mittlerer Viskosität verarbeiten kann, die im Hinblick auf sicherheitsrelevante Bauteile über bessere mechanische Eigenschaften verfügen.
Bei ZF Vigo, die zur sogenannten Division „R“ (R gleich „Restraint“) innerhalb des ZF-Konzerns gehören, und entsprechende Personenschutzsysteme fertigen, ist das ein wichtiger Gesichtspunkt. Zudem wird DCIM für Maschinen mit Schließkräften von 1.600 bis 11.000 kN angeboten, eignet sich also auch für größere Anwendungen oder Mehrkavitätenwerkzeuge.
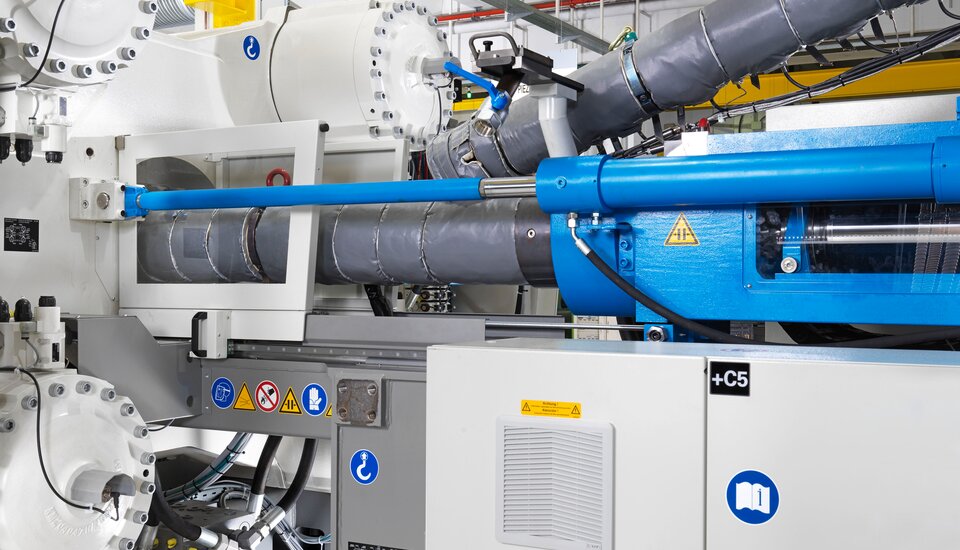
Die compoundierte Schmelze gelangt direkt vom Einschneckenextruder in die Plastifizierung der Spritzgießmaschine, sodass der gesamte Prozess in einer Wärme erfolgt. Dadurch verringert sich der Polymerabbau, man benötigt weniger Energie und spart CO2.
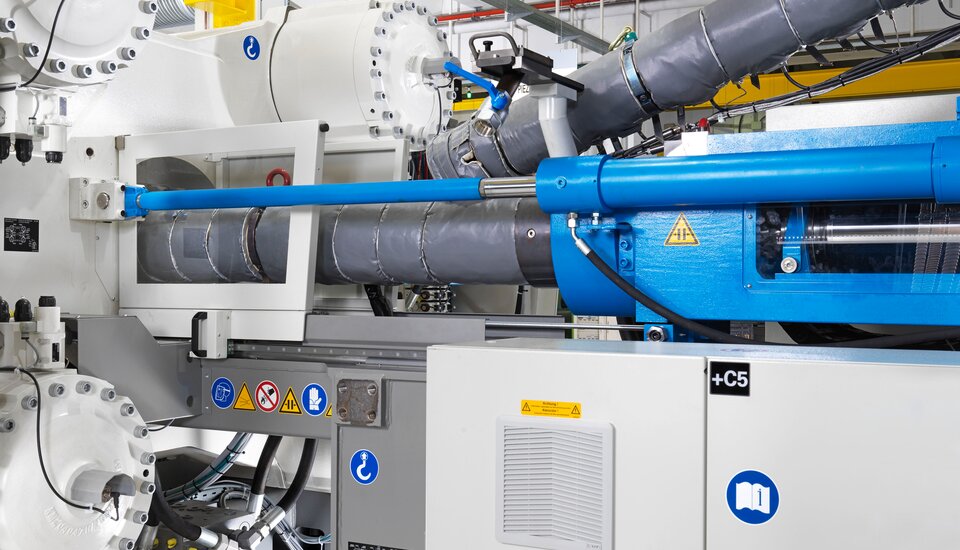
Niedrige Materialkosten und schneller ROI
Dass sich neben der Hoheit über die Materialeigenschaften außerdem Kostenvorteile ergeben, zeigt ein Anwendungsbeispiel von KraussMaffei: Bei einem Kunststoffteller für die Montage von Mineralwolle, der aus PA6 mit 50 Prozent Glasfaseranteil, zwei Prozent Fließhilfe, 0,5 Prozent Masterbatch und 0,5 Prozent Wärmestabilisator compoundiert und gespritzt wird, ließen sich die Materialkosten mit DCIM um 20 Prozent senken. Dadurch amortisiert sich der Mehraufwand für die DCIM-Anlage (gegenüber einer Standardmaschine) in weniger als einem Jahr.
Interessant für Recycling-Material und Biokunststoffe
Besonders interessant ist die Technologie auch im Hinblick auf Recycling und die Verwendung von Biokunststoffen und Naturfasern. Jacob Luis Lopez, Manufacturing Engineer Specialist bei ZF Vigo, hat diese Themenfelder bereits im Auge: „Der Wettbewerb ist so hart geworden, dass man immer einen Schritt voraus sein muss.“ Zunächst gilt es aber, die Technologie zu etablieren und auf andere ZF-Standorte zu übertragen. Für das ZF Werk in Timisoara/ Rumänien sind bereits zwei DCIM-Maschinen bestellt und auch der Vorreiter-Standort Vigo hat schon eine weitere DCIM Maschine angefragt.
Kontakt
franz-xaver.keilbach@kraussmaffei.com