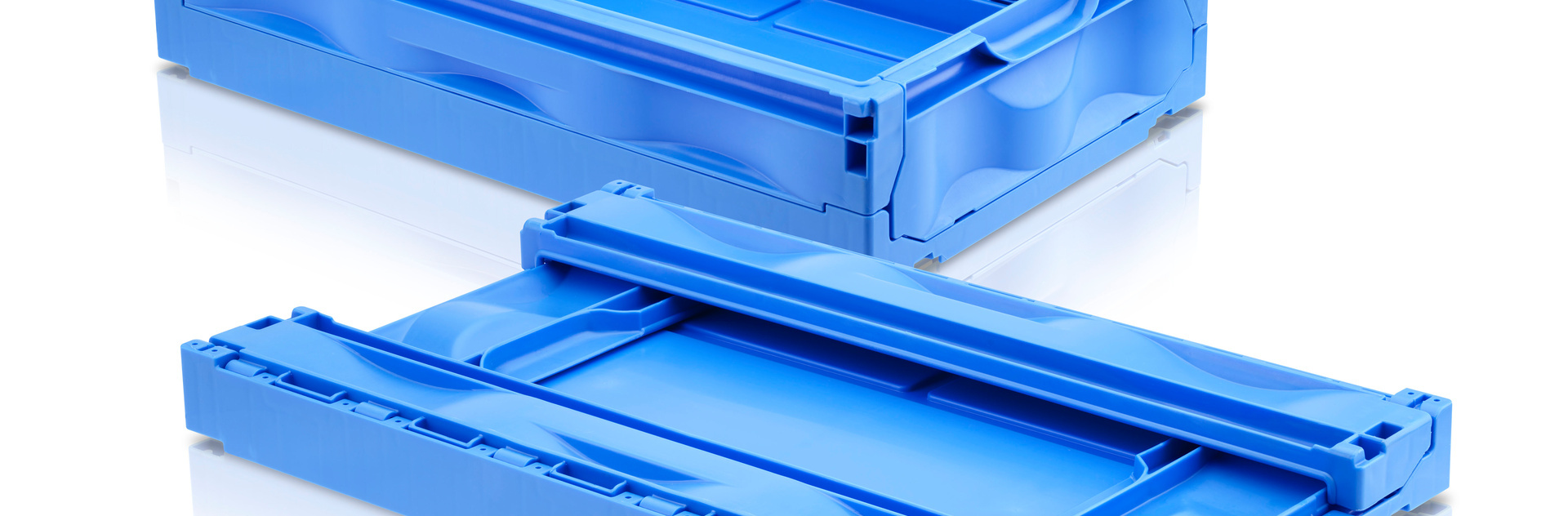
Nachhaltigkeit
Neues Material aus drei Rezyklaten
| Petra Rehmet
Live auf der K 2022: Mehrwegkisten aus drei Rezyklaten
Beim Recycling von Kunststoffen gehen Anspruch und Wirklichkeit oft auseinander. Denn sortenreines Polymer ist nur begrenzt verfügbar. Deshalb müssen möglichst viele Quellen genutzt werden, um das nötige Volumen an Rezyklat zu erreichen. KraussMaffei zeigt mit der Direct Compounding Injection Molding (DCIM) auf der K 2022, wie sich aus drei Rezyklaten unterschiedlicher Viskosität ein neues Material compoundieren lässt.
FFP2-Masken sind allgegenwärtig. Aber was tun mit dem Verschnitt, der bei der Fertigung anfällt? Natürlich recyceln. Das Spinnfaservlies aus PP wird so flüssig wie Wasser (Schmelze-Volumenfließrate MVR 800-1.000), ganz anders als geschredderte kaugummiartige HDPE-Reste aus der Produktion blasgeformter Spielzeuge (MVR < 1). Wenn man noch HDPE aus der Spritzgießfertigung hinzufügt mit einer Konsistenz ähnlich wie Honig (MVR 5-15), hat man die drei Komponenten, die auf der K 2022 zu einem neuen Werkstoff vereint werden.
KraussMaffei legt seinen Messe-Fokus auf Circular Economy - der Direktcompounder DCIM mit seinem Einschneckenextruder spielt dabei eine zentrale Rolle. Er eignet sich für Schussgewichte von 50 bis 2.000 Gramm und ergänzt damit die seit 20 Jahren bewährte IMC-Anlage (Injection Molding Compounder, mit Zweischneckenextruder), die bei Schussgewichten ab 1.500 Gramm wirtschaftlich interessant ist.
Kosten sparen mit DCIM
Die aktuellen Polymerpreise führen dazu, dass Materialhändler nicht mehr genug Recyclingware beschaffen können, um den Bedarf zu decken. Da hilft nur selber aktiv werden. Das DCIM-Verfahren (Direct Compounding Injection Molding) macht das einfach, indem es blendet, additiviert, verstärkt oder füllt und das Material direkt in den Spritzgießprozess einspeist.
Das DCIM-Verfahren spart einerseits Kosten für das externe Compounding (im Durchschnitt etwa 0,6 €/kg) und gibt dem Verarbeiter andererseits maximale Kontrolle über das verwendete Material.Franz-Xaver Keilbach
Global Product Owner Circular Economy / Recycling
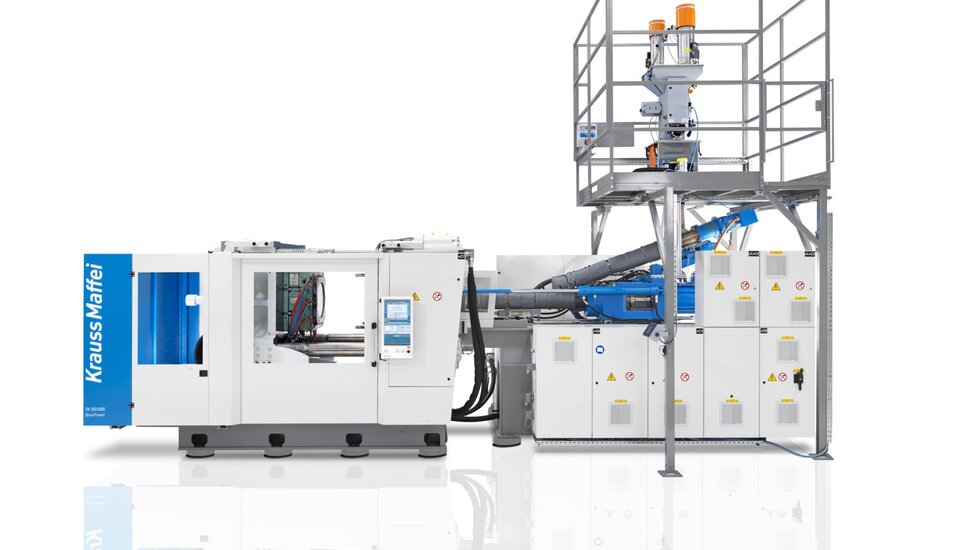
Spritzgießen und Compoundieren in einer Wärme:
Produktion in einer Wärme: Die DCIM-Technologie von KraussMaffei spart wertvolle Zykluszeit und reduziert die Materialkosten um bis zu 50 Prozent.
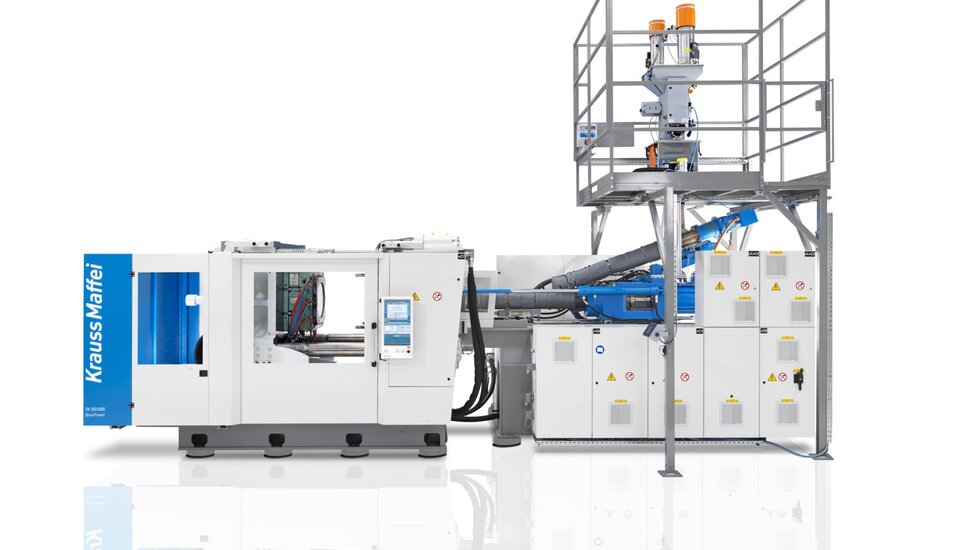
Bei DCIM sitzt ein Einschneckenextruder in Huckepack-Stellung direkt über der Einspritzeinheit einer hydraulischen Standard-Maschine (meist der GX-Baureihe). Beide produzieren im diskontinuierlichen Betrieb, das heißt, der Extruder stoppt, wenn das Schussvolumen für den nächsten Zyklus erreicht ist.
Bei der Messeanwendung werden die drei Materialien zusätzlich mit Masterbatch, Stabilisatoradditiv und Eisenglimmer als Füller versetzt. Letzterer bewirkt um eine bis zu zehn Prozent reduzierte Kühlzeit. Dafür, dass aus den sechs Einzelkomponenten eine homogene Masse wird, sorgt die besondere Schnecke des Extruders. Sie verfügt über ein optimiertes Design und ist außerordentlich lang. Für gewöhnlich liegt das Verhältnis von Länge zu Durchmesser bei etwa 17-23 (Standard-Spritzgießmaschinen), bei DCIM sind es beeindruckende 30 L/D.
Produktion in einer Wärme spart wertvolle Energie
Besonders interessant angesichts der gegenwärtigen Energieproblematik ist, dass sich die gesamte Produktion in einer Wärme vollzieht. Die compoundierte Schmelze wird ohne Unterbrechung oder Wärmeverlust aus dem Extruder in die Plastifizierung der Spritzgießmaschine gebracht. Dieser Einstufenprozess spart Energie und CO2 und ist materialschonend, weil der Polymerabbau verringert wird.
Nachhaltige Transportkisten aus drei verschiedenen Rezyklaten
Am Messestand entstehen aus dem so gewonnenen neuen PO-Kunststoff praktische fünfteilige Klappboxen, wie sie für den Transport von Frischfisch verwendet werden. Die Zykluszeit der GX 1100-4300 DCIM beträgt rund 35 Sekunden und ist damit ideal für DCIM geeignet, denn ab etwa 20 Sekunden vollzieht sich die zusätzliche Materialaufbereitung zykluszeitneutral.
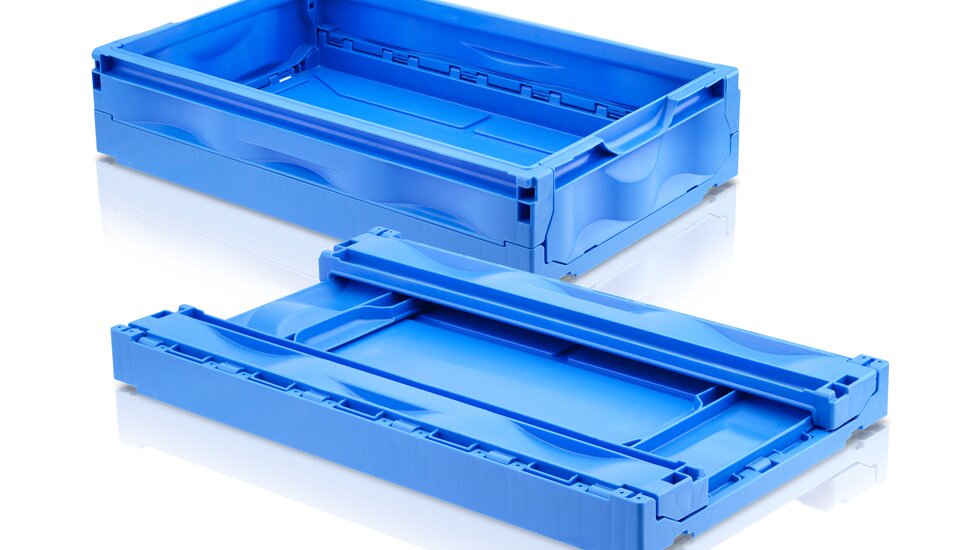
Robust und nachhaltig
Auf der K 2022 produziert eine GX 1100-4300 DCIM Mehrwegkisten aus drei verschiedenen Rezyklaten.
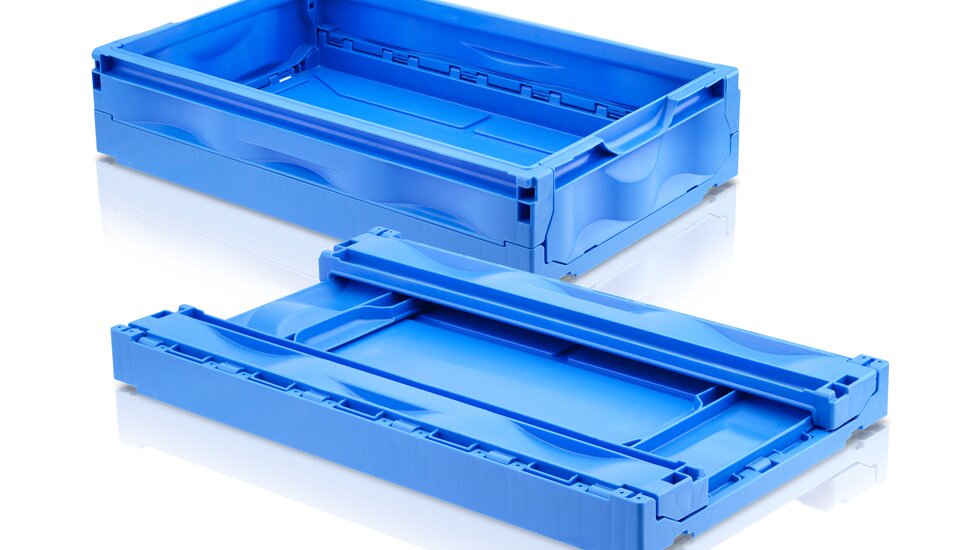
Die meisten technischen Teile, die für das Direktcompoundieren in Frage kommen, liegen oberhalb dieser Grenze. Auf der K entnimmt ein Linearroboter LRX 350 die fünf Einzelteile aus dem Werkzeug (SCS Werkzeugbau) und übergibt sie an eine Automation von Campetella, die das Einlegen, Klipsen und Stapeln der Kisten übernimmt.
Eigene Materialverantwortung und Rezepturhoheit
Für die preisgetriebene Verpackungs- und Logistikbranche stehen die Kostenvorteile des Direktcompoundierens (ca. 30 bis 50 Prozent) im Vordergrund, doch bei Herstellern technischer Teile gibt es einen weiteren wichtigen Aspekt: die Produktverantwortung. Wer – etwa im Bereich sicherheitsrelevanter Bauteile – im Streitfall beweisen muss, dass sein gelieferter Artikel IO war, möchte vielleicht auch die Materialhoheit haben und sich nicht auf einen externen Compounder verlassen. Bei neuen Projekten oder geänderten mechanischen Anforderungen ist es so zudem möglich, eigene neue Rezepturen zu entwickeln und dem Kunden vorzuschlagen.
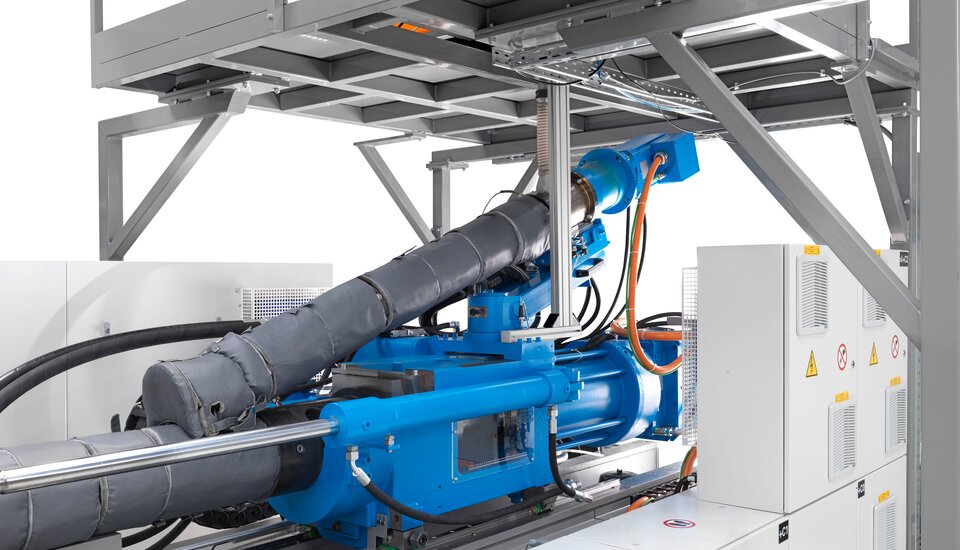
Besonders wirtschaftlich für Teile mit einem Bauteilgewicht von 50 bis 2000g
Beim DCIM-Verfahren von KraussMaffei kommt ein Einschneckenextruder zum Einsatz.
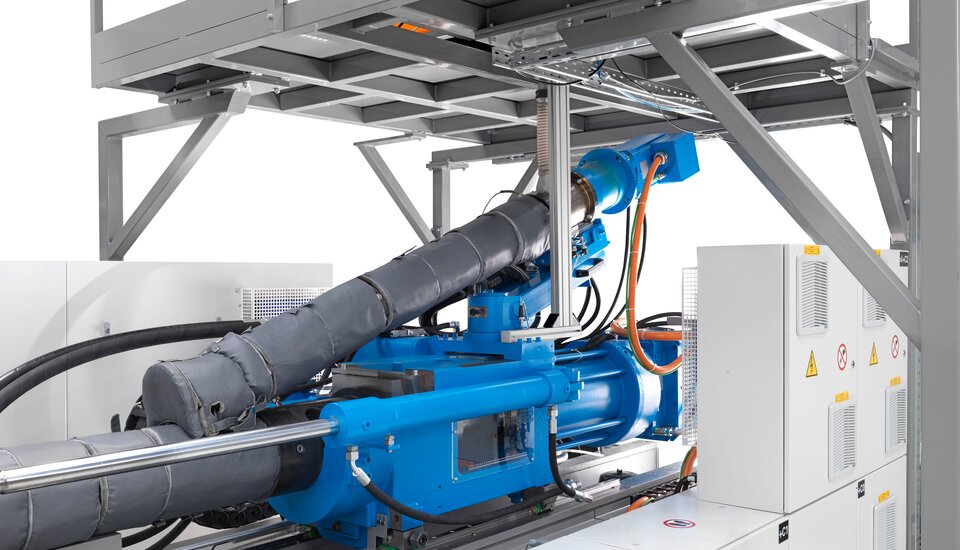
Da das Konzept auf einer Standard-Maschine beruht, sind die Mehrkosten für die DCIM-Ausstattung gering und amortisieren sich in kurzer Zeit. Wenn gerade kein Compound benötigt wird, lässt sich die Maschine ohne größere Umbauarbeiten im Standard-Spritzgieß-Betrieb nutzen. Der Anwender erhält so maximale Flexibilität und ist gerüstet für weitere Entwicklungen innerhalb der Circular Economy.
Dank an unsere Partner
BIG-SPIELWARENFABRIK GmbH & Co. KG (Blasfolien); Schoeller Allibert Services B.V. (HDPE Spritzgussware); Zettl Meditec GmbH (FFP Maskenvlies); almaak international (Maskenvlies Agglomerat); Audia Plastics s.r.o. (Farbmasterbatch); Byk Chemie (Additive); Kärtner Montanindustrie (Eisenglimmer); Campetella Robotic Center srl (Automation) und S.C.S. Societa Construzione Stampi (Werkzeug)Kontakt
franz-xaver.keilbach@kraussmaffei.com