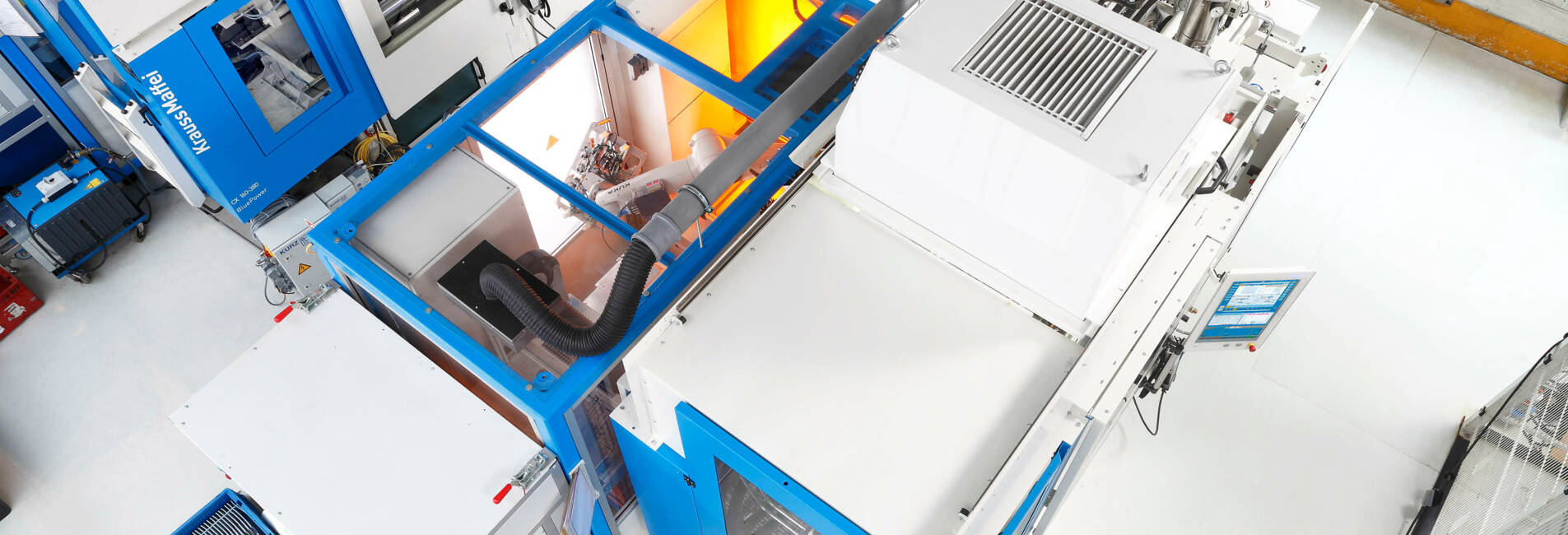
Trendgineering
Automotive component supplier KDK relies on IMD technology
| Petra Rehmet
Two identical IMD systems on the basis of the CX 160
There is no smaller footprint: Surface specialist KDK Automotive from Lennestadt, Germany decide in favor of two identical IMD systems from KraussMaffei. The floor space it demands is smaller than any other machine model in this clamping force range. Furthermore, the automation cells are dockable.
In the new manufacturing cells, delicate air vent frames as well as multiple versions of the Climatronic cover flaps for the VW Tiguan are formed, which are surface finished in the in-mold decoration process (IMD). For this purpose, a film with corresponding coating runs vertically through the two-cavity mold. The mold closes and the coating is transmitted to the surface of the plastic part by means of injection pressure and temperature.
A 6-axis robot demolds the frame and feeds it into a UV station, where the coating is cured as a glaze, and deposits the finished component onto an integrated conveyor belt. Approx. 3,000 components are molded in this way – per day and per machine.

In series for the VW Tiguan
In a 1+1 cavity mold forms delicate air vent frames (left). The Climatronic cover flap is moved into a 1-cavity mold (right).
Multinational expert
The KDK group supplies all major OEMs and Tier 1 suppliers with products for automobile interiors, for instance, decorative parts, center consoles or trunk systems – all from its locations in Lennestadt in Germany, Wächtersbach in Germany, Tachov, Czech Republic and Borja, Spain. KDK Automotive Lennestadt (in Germany) is the specialist for the decoration of surfaces using film, and already has all technical options for IMD and IML (in-mold labeling) available. The approximately 300 employees are tasked with implementing every surface desired by the customer, whereby the focus is on scratch-resistant and chemical-resistant decoration. In addition to the film specialists, the departments for development and project management are also located in the Sauerland region so that many projects are able to be started centrally via this production site and then transferred elsewhere.
Within the group, Lennestadt is very much in competition with the low-cost operations in the Czech Republic and Spain, which is why the topic of automation plays a special role. All injection molding machines have had simple removal systems for over 20 years now – there are no free-falling parts.
Easier handling due to undockable automation cell
Andre Winkelmann, current Plant Manager, says that over at least the last five years, applications have become increasingly complex. To remain flexible enough to take on all challenges, for its current project, KDK has specified the requirement that an automation cell be dockable and mounted on freely-movable heavy-duty casters. Thus, the use of the injection molding machine without automation is just as possible as the relocation of the cell to another production site – offering maximum flexibility when changing products or molds.
As a general contractor, KraussMaffei supplied the total package with the CX 160-injection molding machine and laminar flow box for dust reduction with a film rolling unit from Kurz, a 6-axis robot from Kuka using article-specific grippers, a product-specific sprue trimming solution, a UV station with integrated conveyor belt and a manual work station.

Space-saving and ergonomic:
The CX 160 offers excellent accessibility for changing film rolls. The entirety of film peripherals (spool core, control unit) can be integrated below the cantilevered clamping unit.
With its cantilevered clamping unit and the space provided below it, the CX 160 enables optimum integration of film peripherals. The two-platen design allows fast access to the film rolls. In combination with the machine housing, optimized for the IMD process, changing film is in turn simplified.
"For the first time, we have a 160-ton machine equipped with complete technology, IMD plus automation, in which all safety requirements are fulfilled and maximum functionality is achieved – and all this on the smallest floor space."Andre Winkelmann, KDK Plant Manager in Lennestadt
Lowest scrap values in production
Key factors in selecting a supplier included the concept of being compact and practically oriented as well as the adherence to a tight delivery date. In the end, machines that are ready to operate and validated production processes must be available at the start of project are the crucial factor. Winkelmann is likewise impressed with the performance. "Unfortunately, a one-to-one performance comparison cannot be made, since the Tiguan vent frame is a new component. However, we were able to achieve very good results in both the cycle time area as well as the area of component quality. Scrap and process capability are a big topic for us, due to the one-time use of IMD film. KraussMaffei systems currently achieve the lowest scrap values in our production."
These values are incorporated in the KDK database, in which there are currently 12 million film components stored along with the associated process information. The KDK team can draw on this treasure trove of data during the assessment of scrap numbers as well as while developing new components. For film technologies in particular, it is advisable to integrate later producers as early as possible into the design and engineering process because, for instance, IMD needs to ensure that a 2D film is able to cling to a 3D component.
For film technologies in particular, it is advisable to integrate later producers as early as possible into the design and engineering process because, for instance, IMD needs to ensure that a 2D film is able to cling to a 3D component.
The new Opel Insignia, which first arrived at auto dealerships in 2017, showed how early KDK is often on board. By that time, the team had already been collaborating in the development of interior components for three years, having implemented the requirements of the customer and having successfully started production of these components.
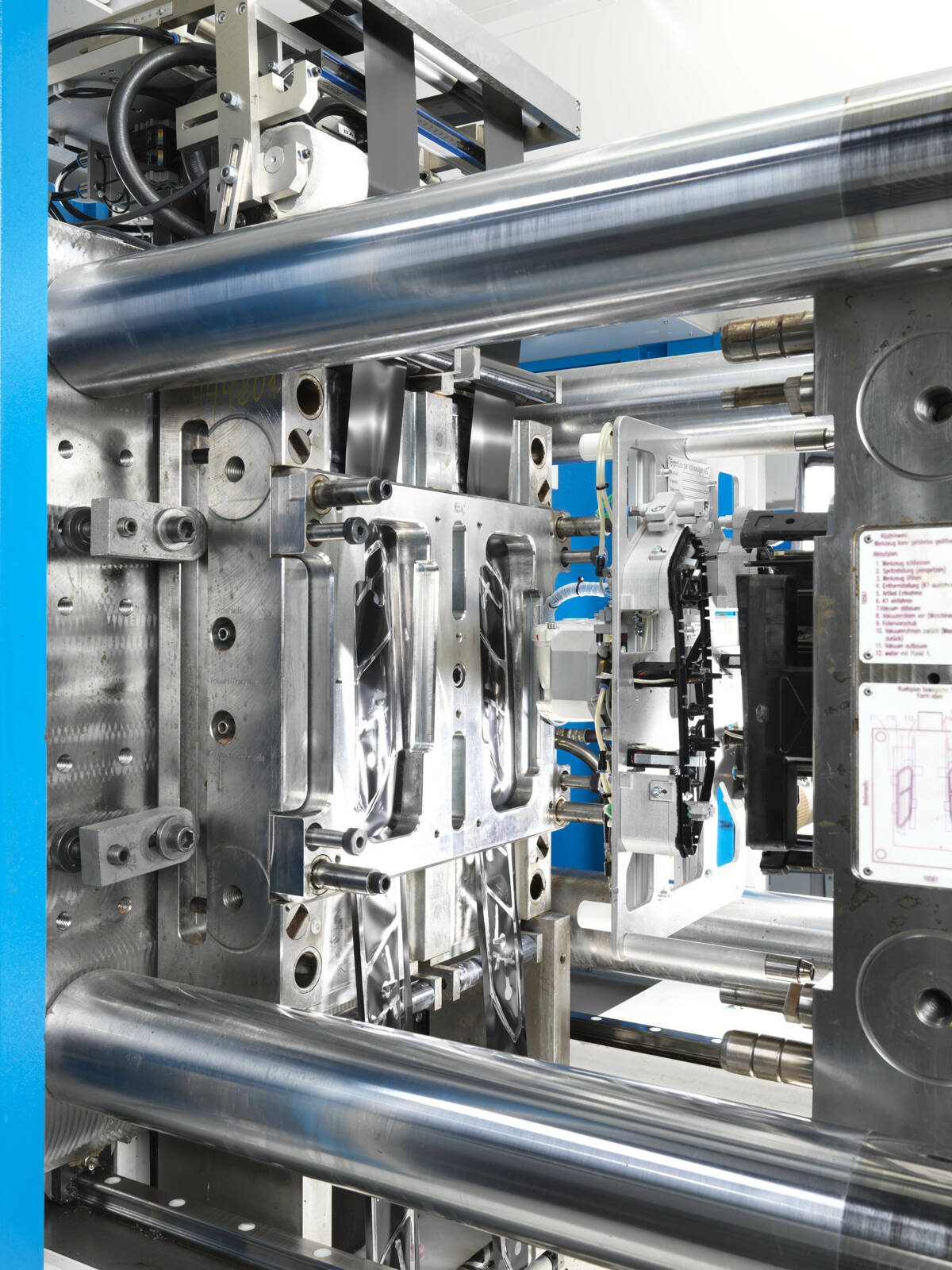
Glance into the mold:
The dual cavities ensure increased output. The article-specific gripper precisely extracts components and deposits them.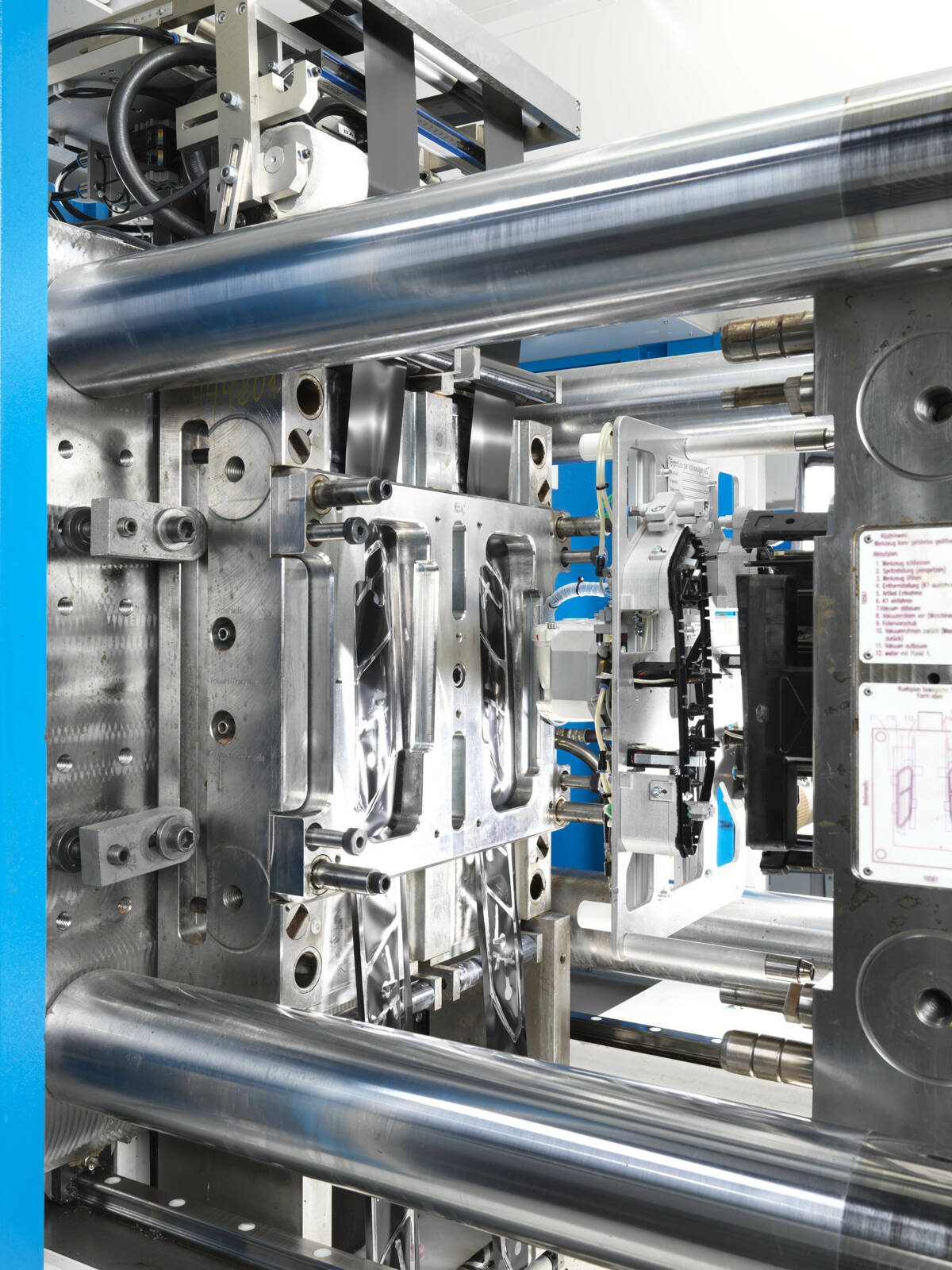
Provided that the parts geometry allows for it, IMD is usually the less expensive alternative when compared to IML. This is because the latter requires an inlay, i.e. a film that has been thermoformed and trimmed. Then, in a second production step, the inlay has to be inserted into an injection mold and back-injected.
Find articles with similar topics:
More articles like this
More efficiency in injection molding thanks to intelligent mold temperature control
31.08.2025 | ahead
Transparency with depth effect: Producing high-quality surfaces sustainably
31.08.2025 | Michael Fuchs, Gerhard Konrad