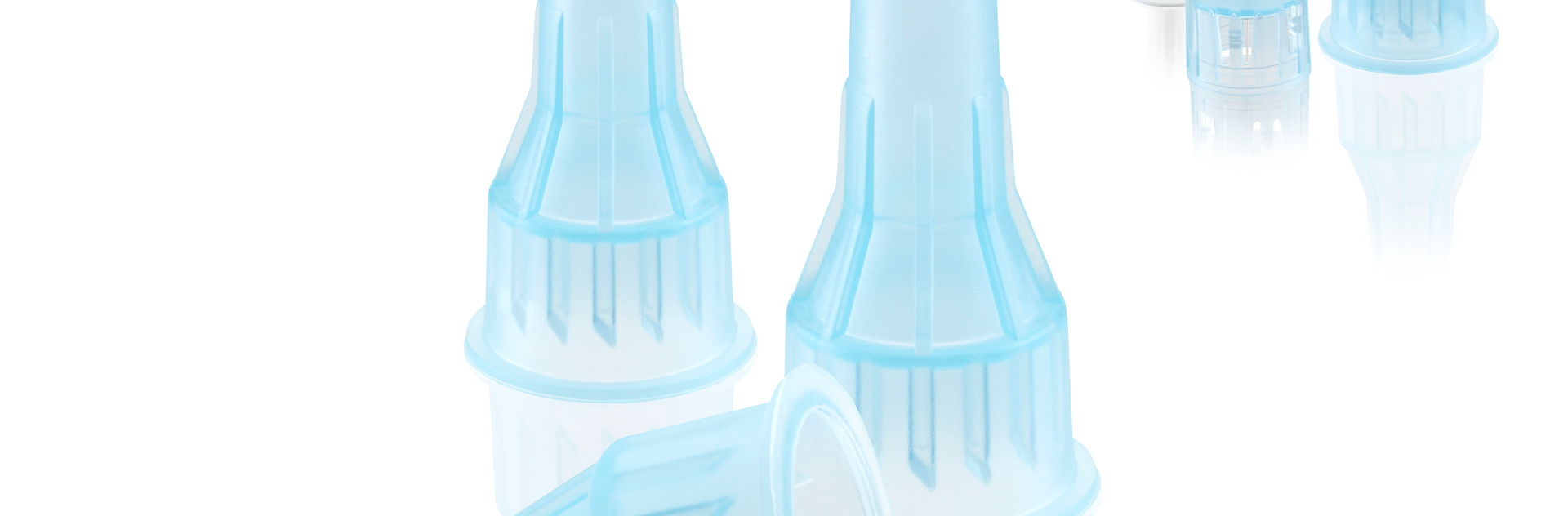
trendgineering
How to optimize costs per part
| Petra Rehmet
All-electric PX 200 with medical application at the K-show
Sensitive products in medical technology place high demands on the purity and quality of the injection molding process. At the same time, processors face the challenge of minimizing the costs per component. At K 2022, KraussMaffei will be demonstrating how both requirements can be combined using the example of insulin caps.
The all-electric PX 200-1400 with a clamping force of 2000 kN on the KraussMaffei booth is designed for precision and performance. At the same time, the special performance equipment ensures short cycle times and thus greater cost-effectiveness. For example, the plasticizing drive with increased drive power brings greater speed to the process, resulting in higher throughputs due to faster plasticizing.
Another feature of the efficient equipment package is the high-performance screw. It features a special design for throughput-intensive applications and allows high melt quality with short cycle times.
Precision and speed
The insulin pen caps are made of new PP are produced in a 96-cavity mold from our partner company Männer. Particularly important is the precise and fast filling of the cavities – an important quality requirement that is reliably met by the increased injection speed.
Precision and speed are also critical during demolding, using an electric ejector drive with greatly increased power. Thus, all cavities are always the same, shot for shot, and the high quality of the components is ensured.
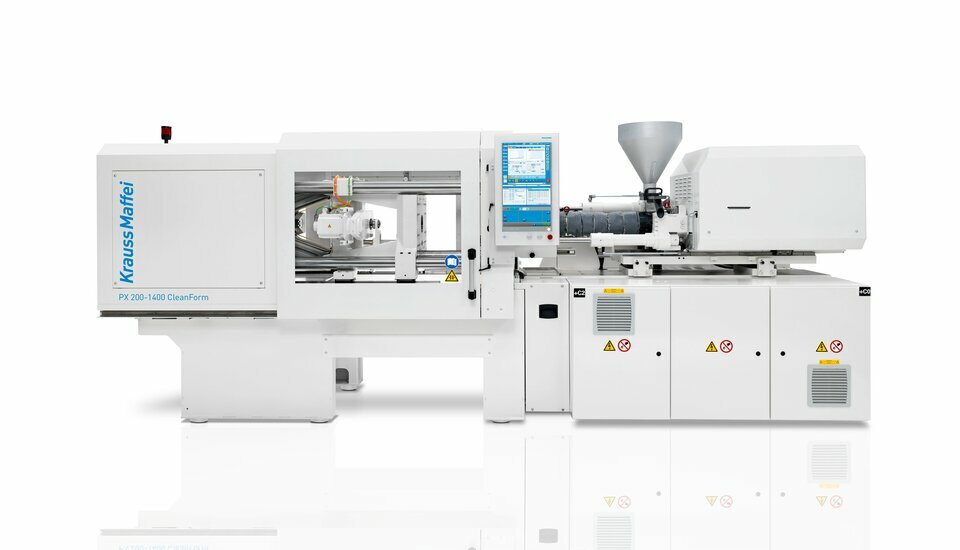
Perfectly suited to maximum precision in the cleanroom:
The all-electric PX 200-1400 in medical design
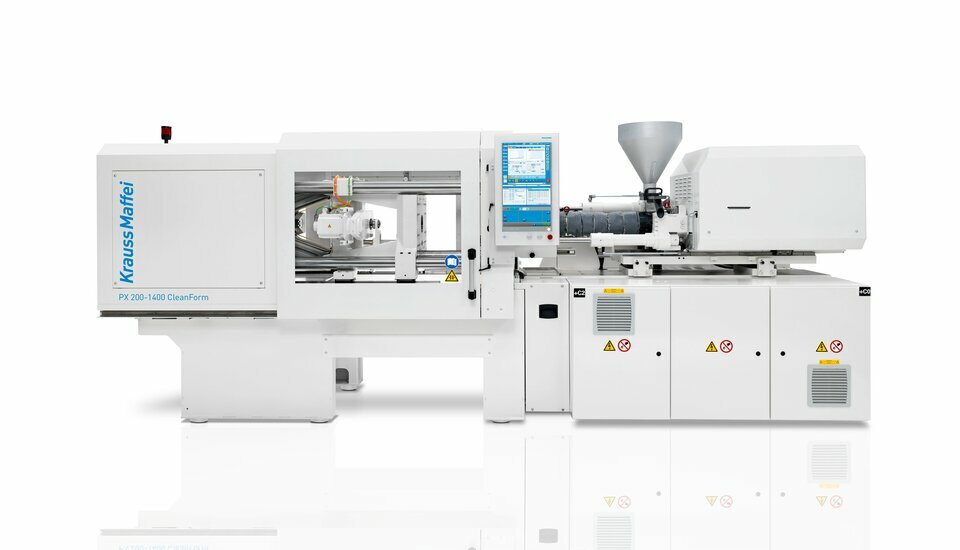
Intelligent material savings with APCplus
The intelligent APCplus machine function helps to further reduce manufacturing costs. The function compensates for external influences on part quality during the injection molding process, thus guaranteeing a constant manufacturing process.
"The APCplus machine function ensures consistently high component quality and thus reduces scrap to a minimum. This optimizes material consumption and reduces costs per component."Christian Krampfl
Global Application Owner MEDICAL
The validated process is also adhered to with APCplus, as such a process can also be actively controlled. Instead of concrete setting parameters that have to be manually readjusted by the operator, process windows are defined here in which the machine is allowed to operate and intervene.
In addition, the APCplus function enables seamless documentation of the material quality, which makes it possible to recognize major fluctuations at an early stage.
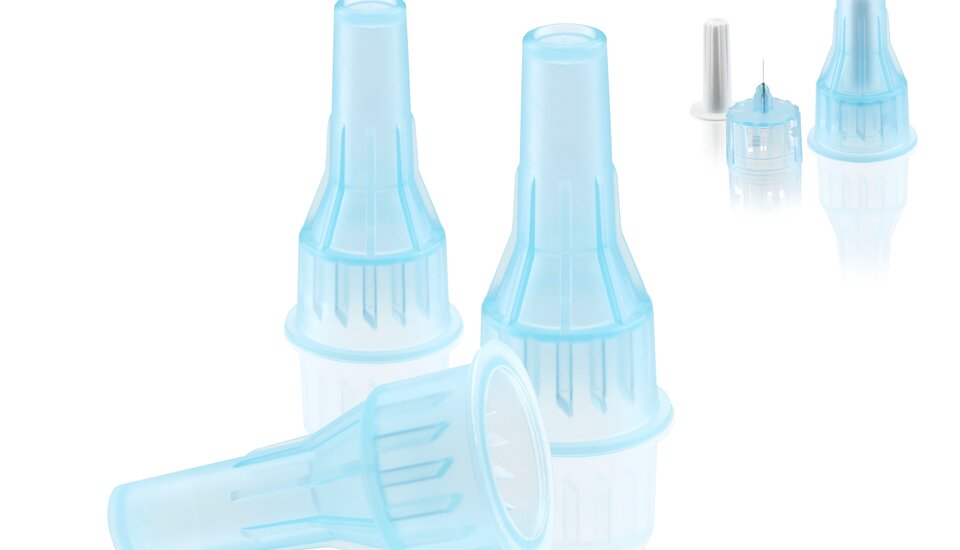
Fast cycle times and low energy and material consumption
At K, the PX 200-1400 produces caps for insulin pens with maximum efficiency and cost-efficiency.
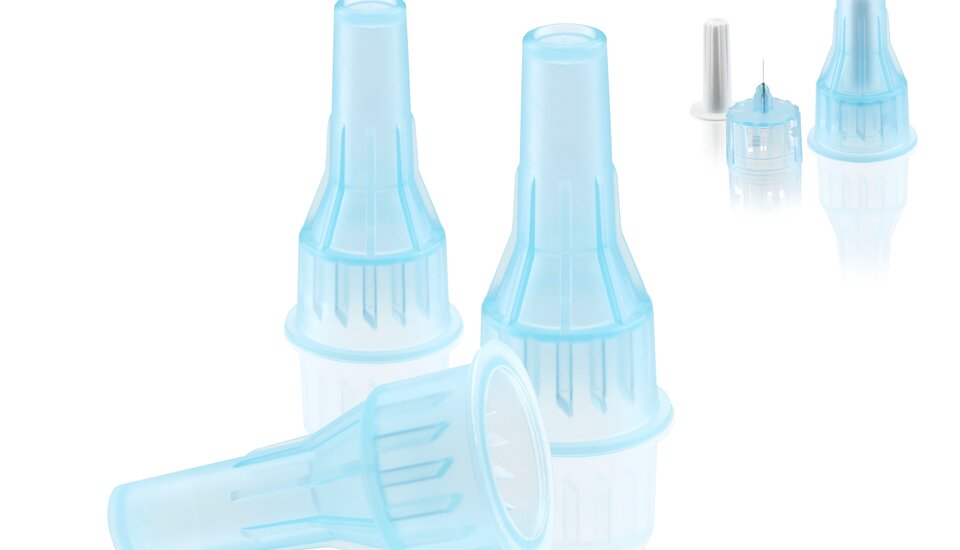
Best energy efficiency
In times of increasing energy prices, energy savings are gaining importance in addition to material savings. The PX 200 on the KraussMaffei booth is therefore designed to save energy. The hydraulic unit in servo design and the recuperation system for recovering brake energy contribute significantly to this.
Another feature are the proven Eco-Pac insulating strips on the injection unit. They stabilize the temperature profile and increase process stability, which reduces the heating time by up to 30 percent.
With the Orca mold cooling system from partner Jurke Engineering fully integrated into the MC6 machine control system, even more energy can be saved. Unlike a conventional water battery, the system measures flow rate and quantity by ultrasound.
This takes place from the outside and without making contact with the medium. As a result, the Orca distributor block does not have any cross-section narrowing, meaning fewer pressure losses.
"The integrated Orca mold cooling improves energy efficiency. As a result of optimal mold cooling management, the cycle time drops and the quantity produced per hour is boosted."Christian Krampfl
Global Application Owner MEDICAL
The global demand for disposables, especially in the healthcare sector, is tremendous. The products are often only used for a short time and are hardly ever soiled. These are ideal conditions for the caps produced for insulin pens to be used as a raw material for components with a longer service life.
These caps for insulin pens are used to produce front-end carriers for the automotive industry at the KraussMaffei booth. Visitors to the booth can observe the entire material cycle. The process is accompanied by new digital solutions that reduce energy consumption and lower the CO2 footprint.
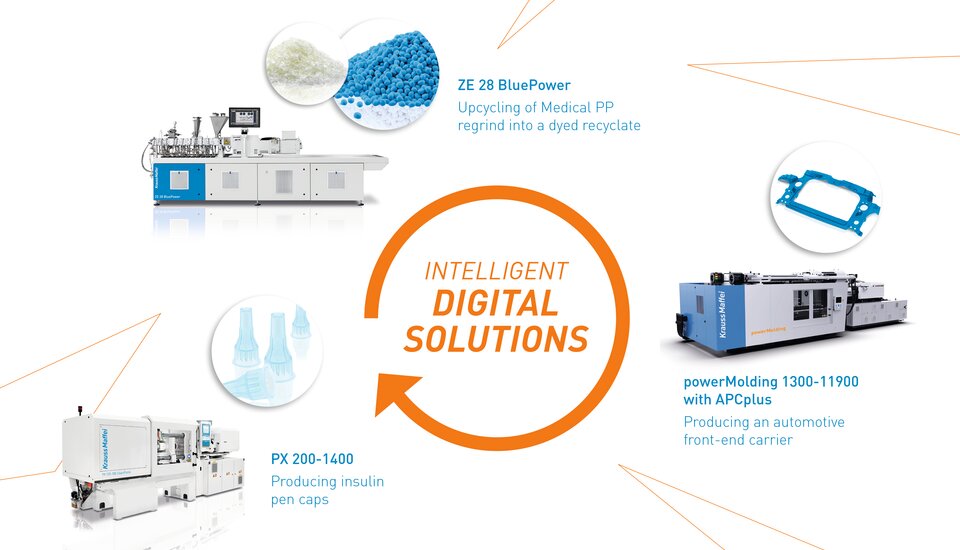
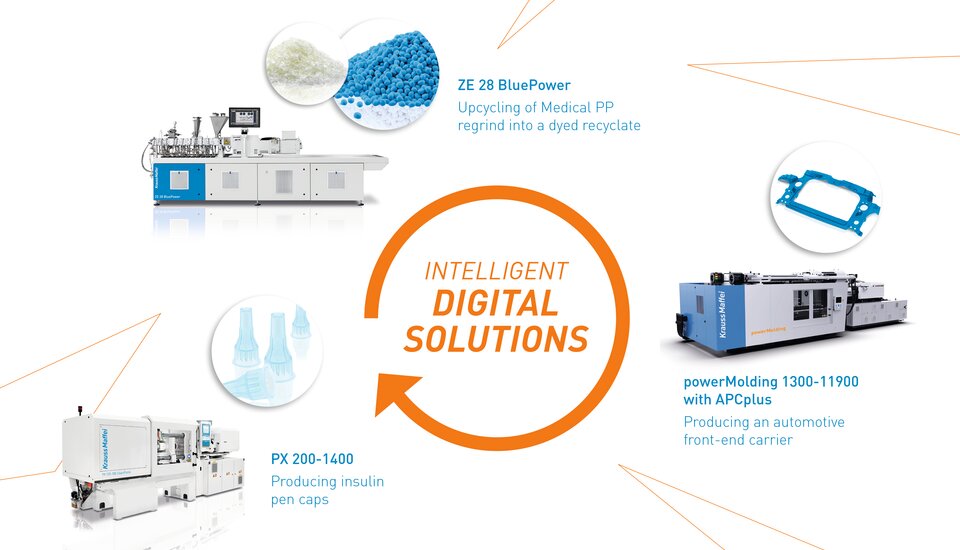