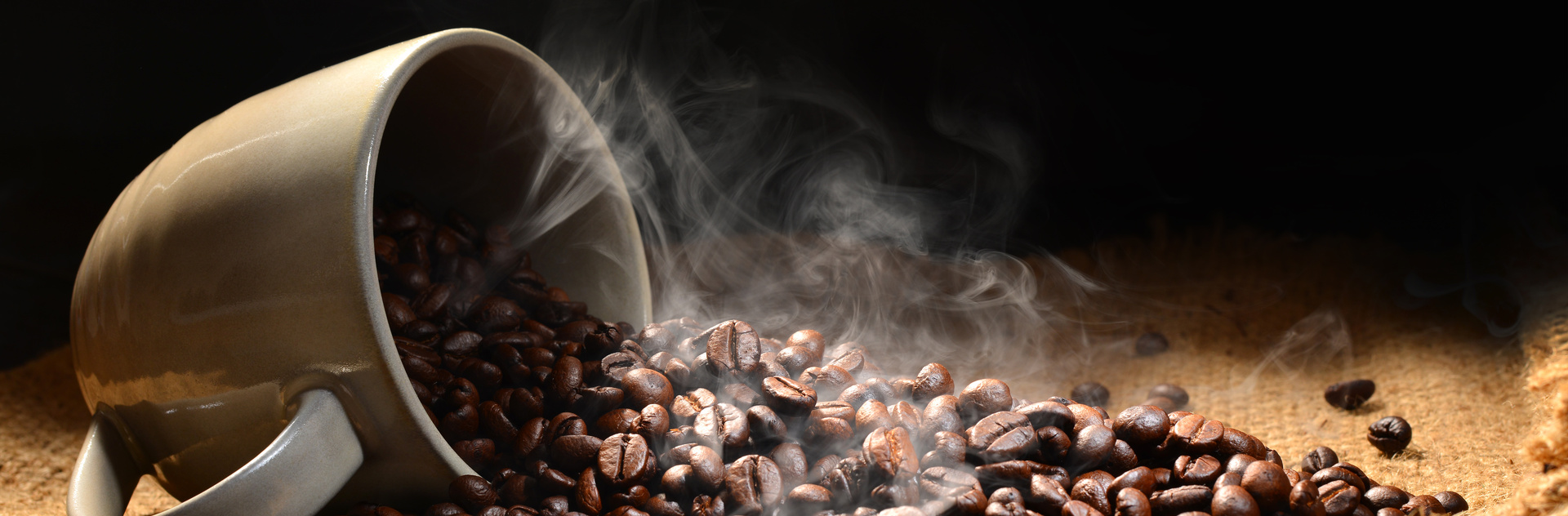
sustainability
For more sustainable coffee enjoyment
| Petra Rehmet
How Gebaplast uses coffee grounds to produce new stylish cup coasters
Reusing something good makes sense — and that is also how they see it at Gebaplast BV in Oud-Beijerland, Netherlands. The family-owned company produces coffee-cup coasters made of biopolymers based on ground coffee. For production they use a CX 130-750 injection molding machine from KraussMaffei. An interview with company owner Wouter Geldhof.
ahead
Coasters based on ground coffee beans are certainly a rather unusual project for an injection molding company. How did this start?
Wouter Geldhof
The request came from a customer. That customer, in turn, had been approached by a major provider of coffee and fully automatic coffee machines to produce stylish coasters for cups for its collection of accessories. What is extraordinary about this is that used coffee bean grounds are to serve as the material. This is an excellent project, which we at Gebaplast as an agile family-owned company were glad to accept. We like thinking outside the box and developing new solutions for and with our customers.
ahead
I guess this is a biopolymer. What exactly is the material?
Wouter Geldhof
We fully process a biopolymer, and it is called a bio-PE. The percentage of used coffee bean grounds is 25 percent. A nice side effect is that the coffee aroma is not lost, so the coasters still smell like coffee.
The coasters are designed for a long service life and are dishwasher-safe. But if a product ever needs to be disposed of, they are 100 percent recyclable.
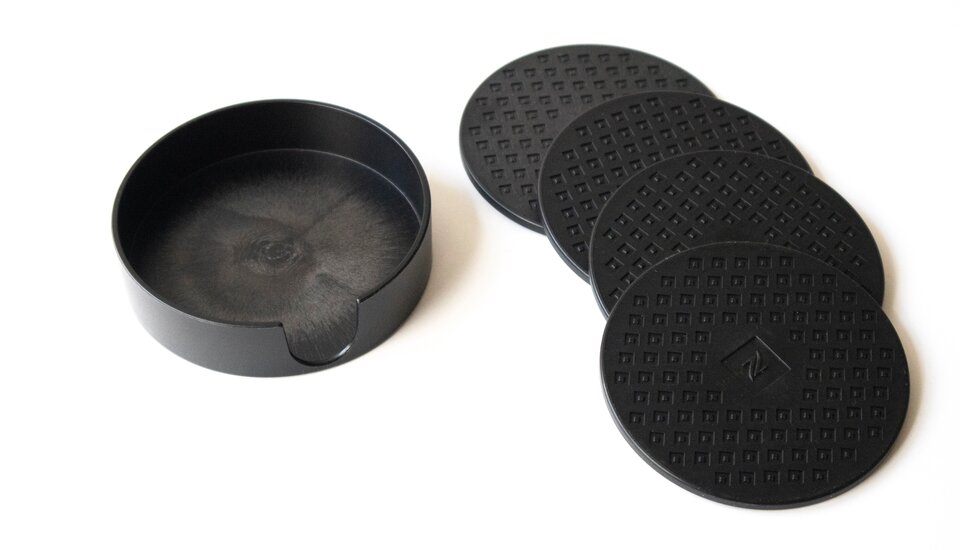
Coffee grounds instead of new polymers: The coffee coaster consists of a bio PE with a percentage of 25 perCent coffee grounds
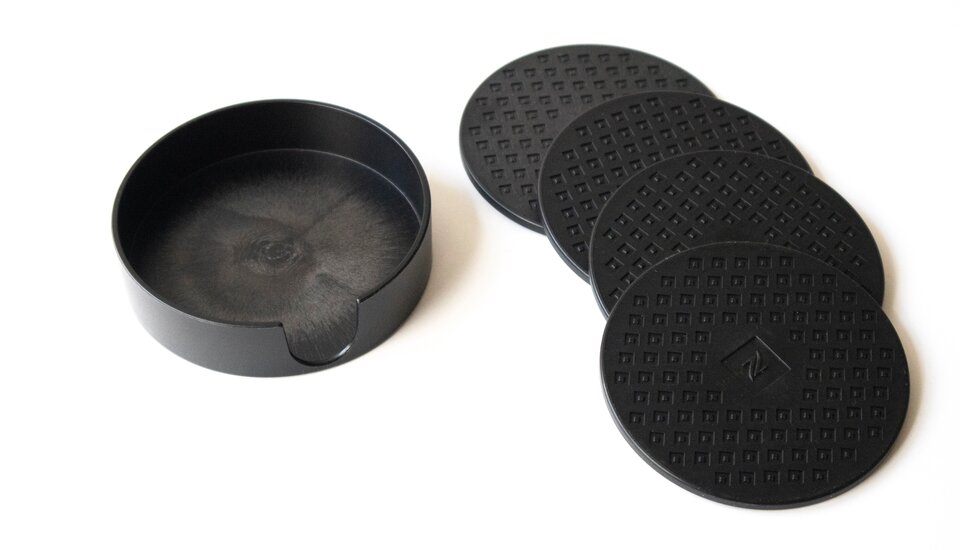
ahead
What is so special about processing this biopolymer? Is there anything in particular that has to be observed?
Wouter Geldhof
The greatest challenge, of course, lies in the coffee component, that is, in making sure the material stays dry and does not degrade. The material varies in viscosity, which is not easy to manage, and so the injection molding process and the injection molding pressure have to be brought under control. All of that while maintaining low temperature margins.
ahead
How was KraussMaffei able to support you? Are you happy with the results?
Wouter Geldhof
The KraussMaffei team provided us with excellent support in the design process and project engineering. The same is true for their service. Together we found an optimal solution.
Since the beginning of this year, the CX 130-750 has been producing the coasters in a four-cavity mold with a clamping force of 1300 kN and cycle times of 30 seconds. By the end of the project, we have produced about 200.000 pieces. The global demand exists.
We are very satisfied with the hydraulic injection molding machine CX 130-750 from KraussMaffei. With its cantilevered, compact clamping unit, the powerful injection unit and the compact installation area, it is ideal for our requirements of maximum efficiency in the smallest floor space.
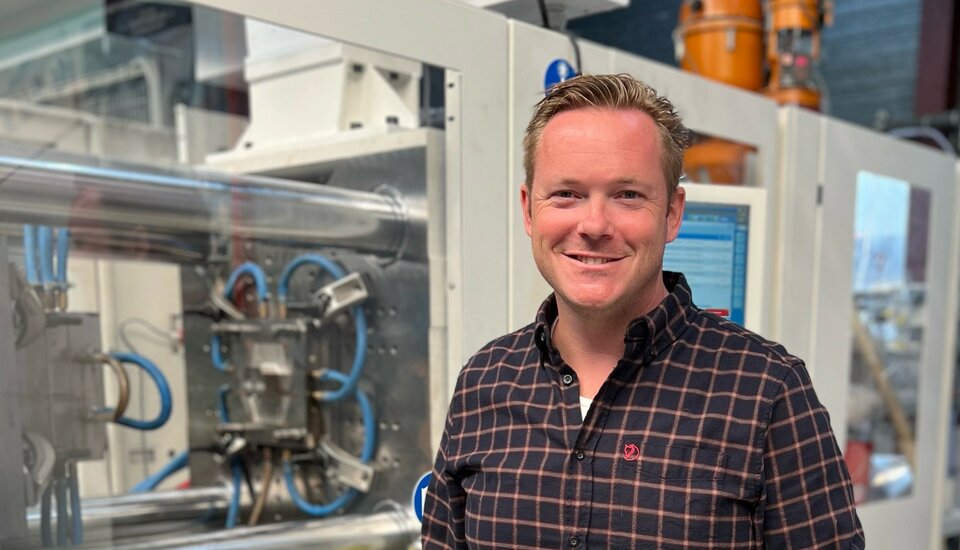
Wouter Geldhof in front of one of the CX 130
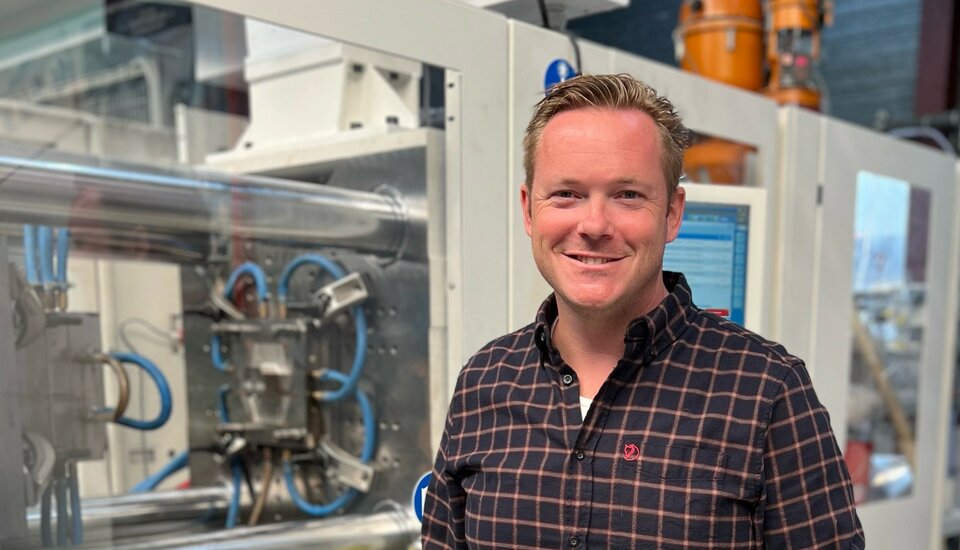
The intelligent energy management has further advantages, which we are benefiting from now in particular in these times of rising energy prices. Overall we have three CX 130-750 injection molding machines of a nearly identical design from KraussMaffei.
ahead
The CX series is evidently perfect for producing these coffee coasters. What other industries do you serve with this machine?
Wouter Geldhof
One of our flagships, we are very proud of, are the so-called Drumclips. They are also produced on a CX 130-750. These can be used to secure (oil, chemical, additive) drums on pallets and trailers. The system is certified and gives our customers a maximum degree of security and safety.
ahead
Do you use digital solutions? What advantage do they bring to your daily business?
Wouter Geldhof
For the production of the Drumclips, we use the APCplus machine function. It is ideal and reliably supports us in the production of these safety-related and certified components by means of a consistently high component quality and comprehensive documentation. I can always recommend APCplus.
We have also tested the socialProduction app from KraussMaffei. Particularly for us as a smaller company, where there cannot always be someone on-site at the machine, these kind of digital service and maintenance programs are of particular interest.
ahead
What are your plans for the future? Are any further innovative products in your pipeline?
Wouter Geldhof
There is a big demand for our Drumclips. Thus, we are considering expanding our production. That could also include an expansion of the clamping force to 2500 or 3000 kN, that is, a CX 250 or CX 300 or even a PX machine.
Currently we are working on another very interesting project, a sustainable follow-up project to the coasters. This time it concerns coffee cups also made on the basis of ground coffee beans. Then we would have another stylish and sustainable part of the accessories collection and thus another perfect example of our solutions developed "outside the box."