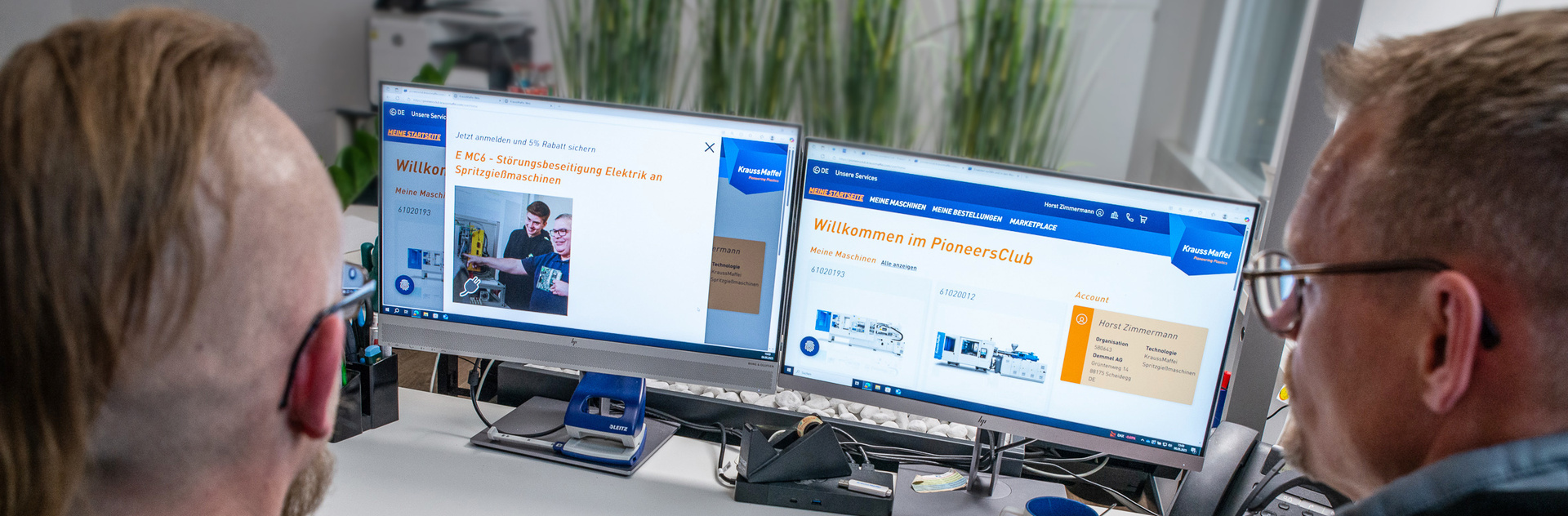
digitalization
In the 2500 pioneersClub
| Petra Rehmet & Dr. Christina Langbein
Tier 1 company Demmel relies on KraussMaffei's pioneersClub with its digital and personal services
The white and blue “propeller” in the BMW logo on the tailgate lifts up, a nozzle sprays cleaning fluid onto the reversing camera underneath. Demmel AG manufactures vehicle emblems like this one using machines and digital services from KraussMaffei. There is now an anniversary at the Heimertingen site: Horst Zimmermann, Manager Competence Center at Demmel AG, is the 2500th user in KraussMaffei's pioneersClub.
Horst Zimmermann is a fan of the digital, free service platform and describes it as unique in the injection molding world. Systems are automatically stored here using the order number and are then recorded with all their special features.
A pullable tie bar, a particularly heavy sliding door or a special unit: all documentation, maintenance agreements and spare parts recommendations relate to this individual machine.
No more puzzling over the right pump design etc. Users can maintain their own machine activities, display the integrated automation or find out about offers for services and retrofits.
We have a very specially configured used machine in our inventory, so we need a spare part from time to time. If I order it through the pioneersClub, I can be absolutely sure that it will fit our needs.Horst Zimmermann
Head of Competence Center Demmel AG
pioneersClub complements personal service contact
The pioneersClub is intended to be a supplement to the human service contacts and always provides the right contact details.
Experience shows that more and more spare parts inquiries and orders are being processed via the pioneersClub. For larger projects, customers still prefer to pick up the phone.Stefan Betzing
Customer consultant KraussMaffei Technologies GmbH
It is also possible to use the service platform to create offers for your own purchasing department.
For Horst Zimmermann, the pioneersClub currently leaves nothing to be desired, but Daniel Bachmann, Product Owner of the pioneersClub at KraussMaffei, is happy to exchange ideas with customers in order to obtain and implement feedback.
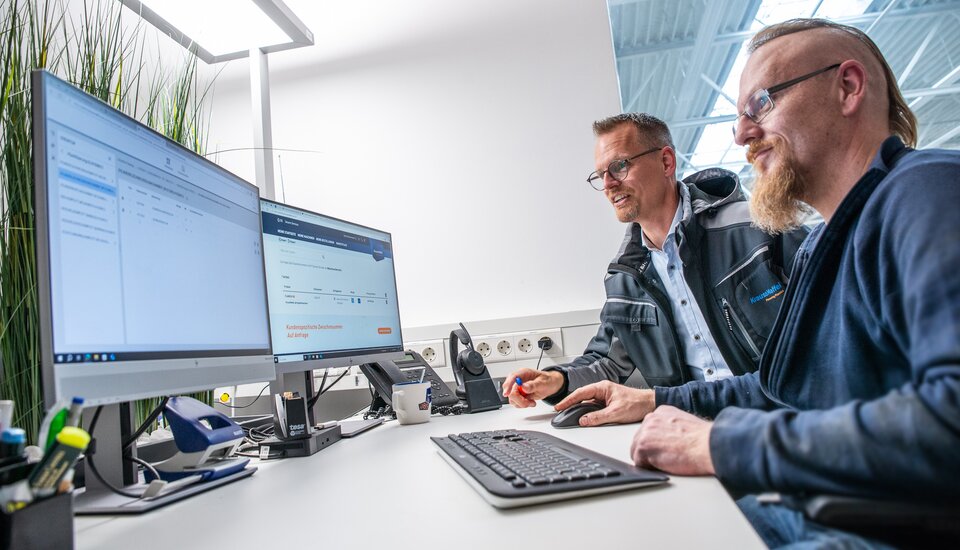
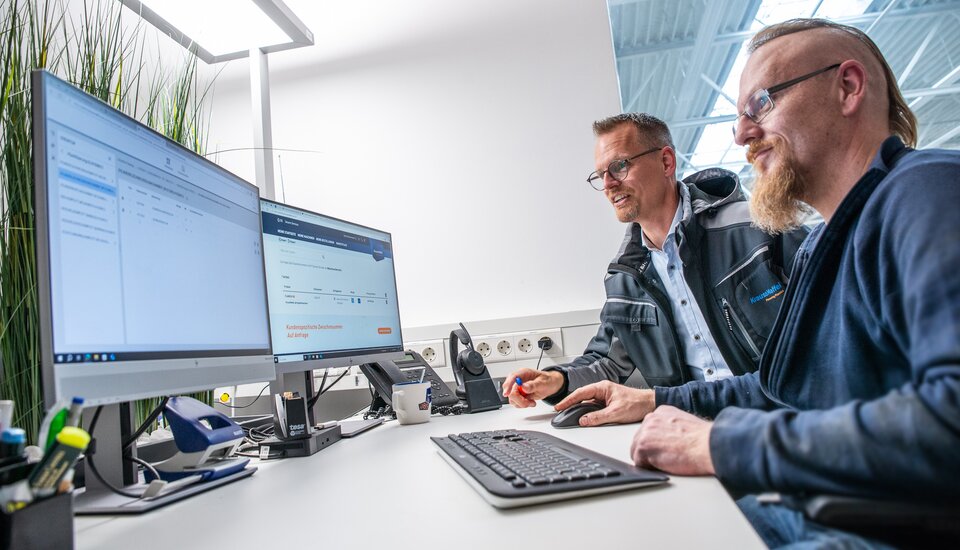
Core competence aluminum-plastic connections
Demmel Heimertingen (near Memmingen, Germany) occupies a special niche in the automotive industry with its products. Decorative parts such as brand logos and aerodynamic wheel inserts are the main focus and are supplied directly to OEMs.
In terms of production technology, it is always a question of combining aluminum and plastic. A semi-finished aluminum product is decorated using screen printing, coated with self-healing protective lacquer, die cut and back-injected with the help of an adhesion promoter.
For the wheel inserts, one or more screw bushes are also required, which are shot in. The challenge with the mechanically operated BMW rear emblem pot is to position the camera hole exactly in the center under the propeller.
The aluminum blank is therefore held in position in the tool with a vacuum and a core retracts so that the plastic does not flood the recess.
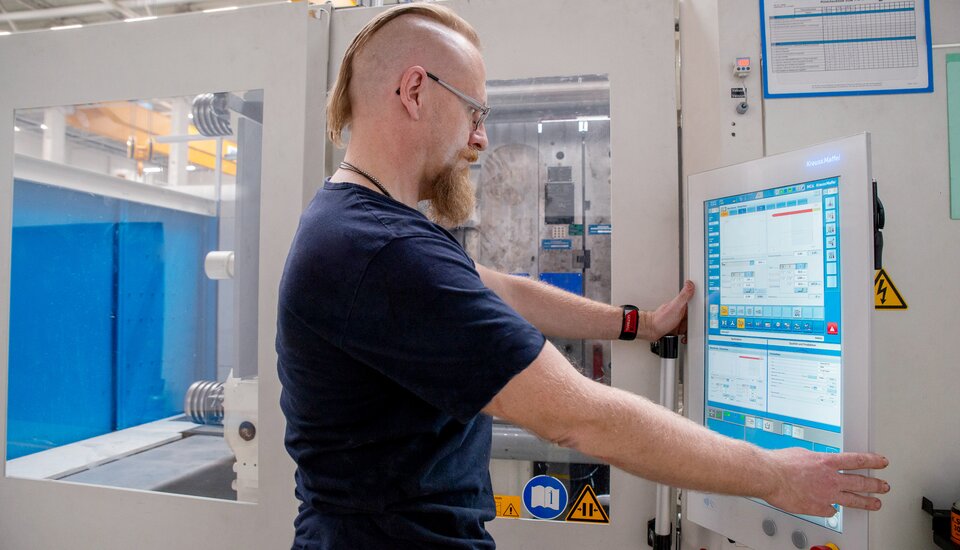
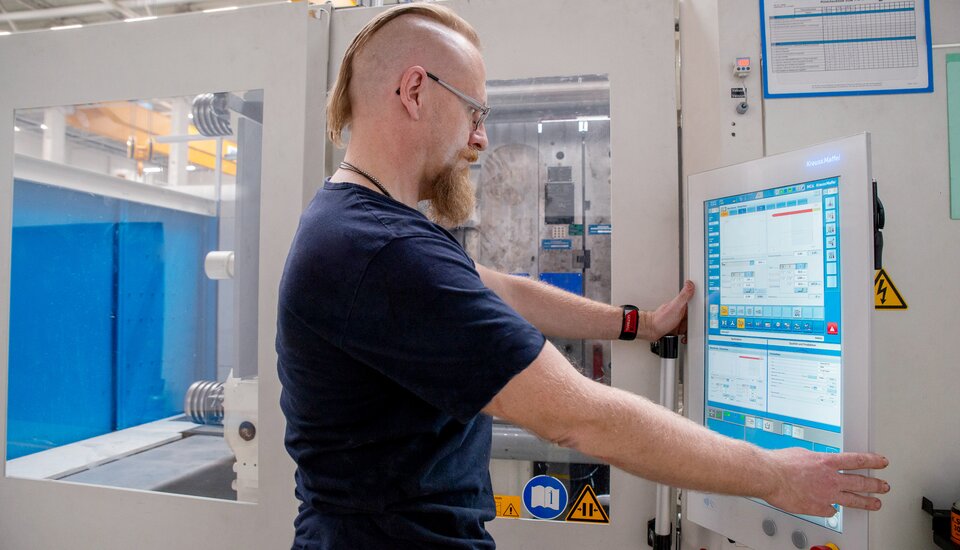
The rear emblem must be absolutely flat to ensure that the trunk is rainproof. There must also be no open edge between the plastic and aluminum on the propeller, otherwise water would penetrate, freeze in winter and blow off the aluminum layer.
The stern pot is produced on a GX 500, the propeller on a CX 250 - both proven injection molding machines from KraussMaffei. Initially, there was a problem with the flatness of the component, but an application engineer from KraussMaffei found the solution on site.
It was previously our company's philosophy to buy used machines, but I never had the feeling that I was a second-class customer because of KraussMaffei's service.Horst Zimmermann
Head of Competence Center Demmel AG
Team spirit convinces - Successful overhaul of a used GX 500
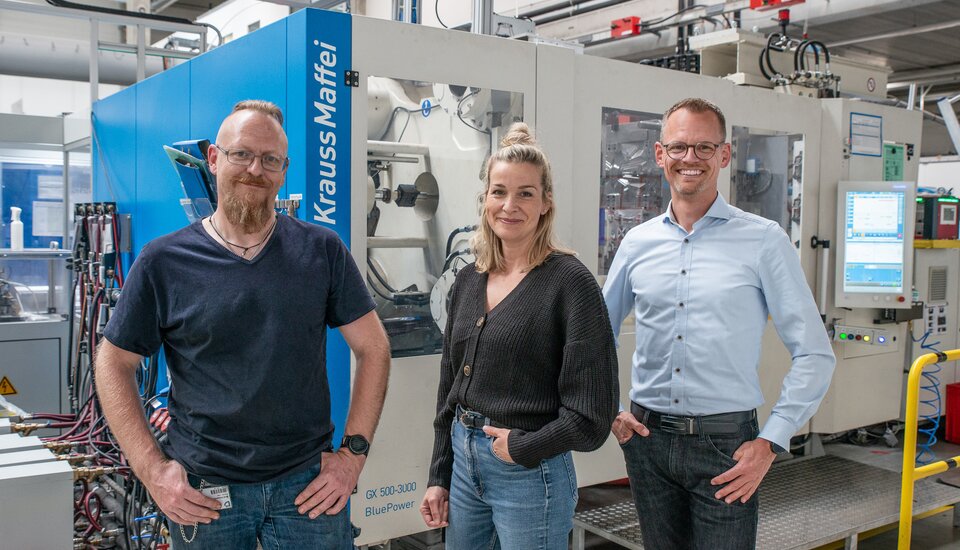
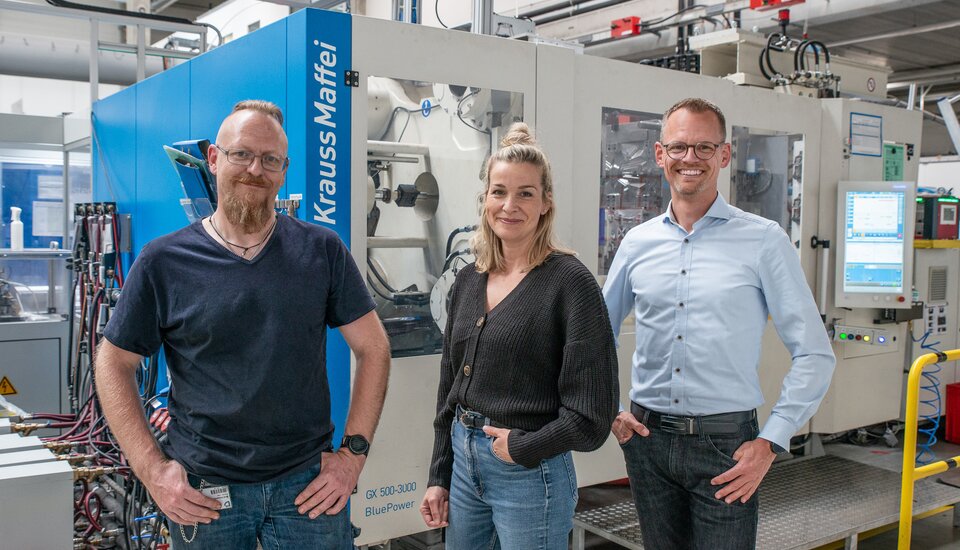
This even applies to difficult cases. The GX 500 (built in 2014) spent its first life in the electroplating shop of an automotive supplier. When it came to Demmel, it was in a terrible state.
The aggressive fumes had not only caused the mold mounting plates to rust, but had also caused extensive damage to the interior. The result was a complex electrical problem.
I kept KraussMaffei's telephone support busy for several day and the support was excellent. They never gave up and also sent us spare parts unbureaucratically. We all wanted to find the fault together and finally managed to do so.Horst Zimmermann
Head of Competence Center Demmel AG
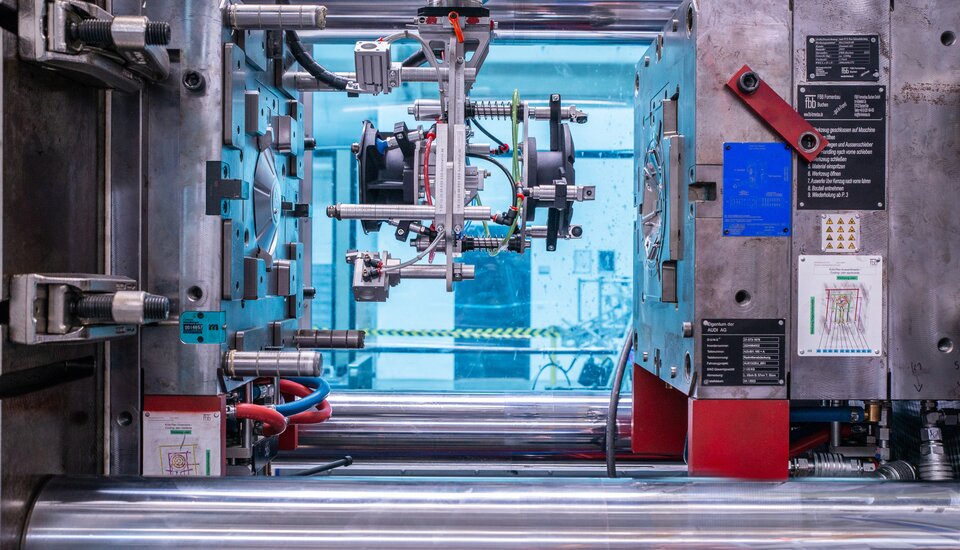
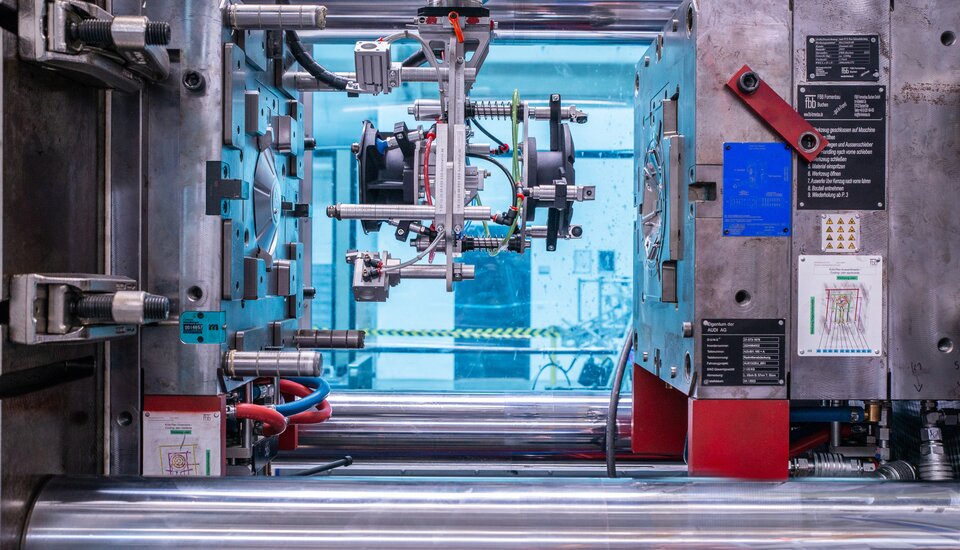
Since then, the GX 500 has been able to manufacture Demmel Heimertingen's main product, so-called wheel inserts, which have names such as “spaceship” or “molar” within the company.
The inserts are bolted onto aluminum rims and are used - especially in electric vehicles - to reduce air resistance and thus increase the range of the cars. Aluminum and plastic are also combined for this purpose.
The GX 500 now looks and functions very well, and a retrofit has even increased the clamping force to 5,500 kN. Of course, this is also noted in the pioneersClub.
His profile even included a 650-ton machine (built in 2000) that was recently sold to China. Horst Zimmermann was able to remove it from his pioneersClub profile directly on the platform.
True hands-on mentality
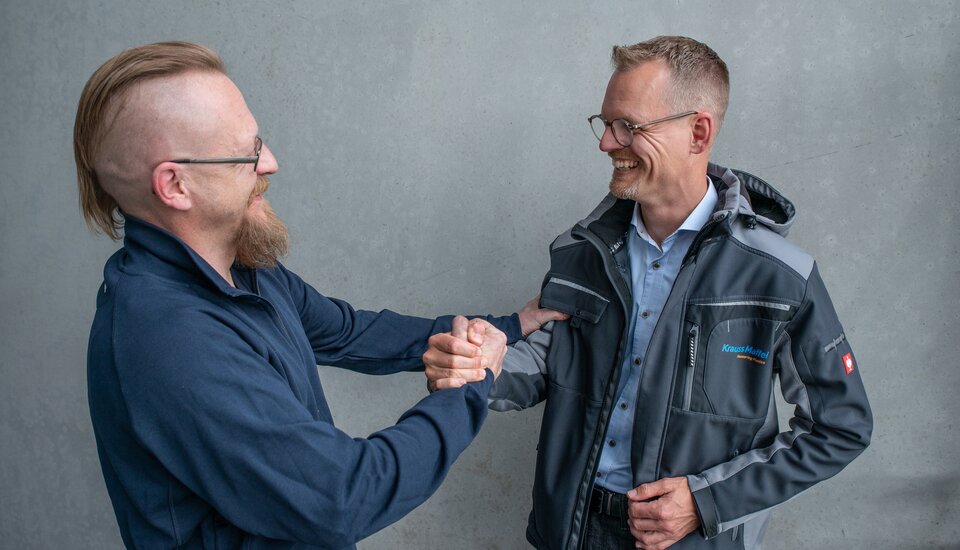
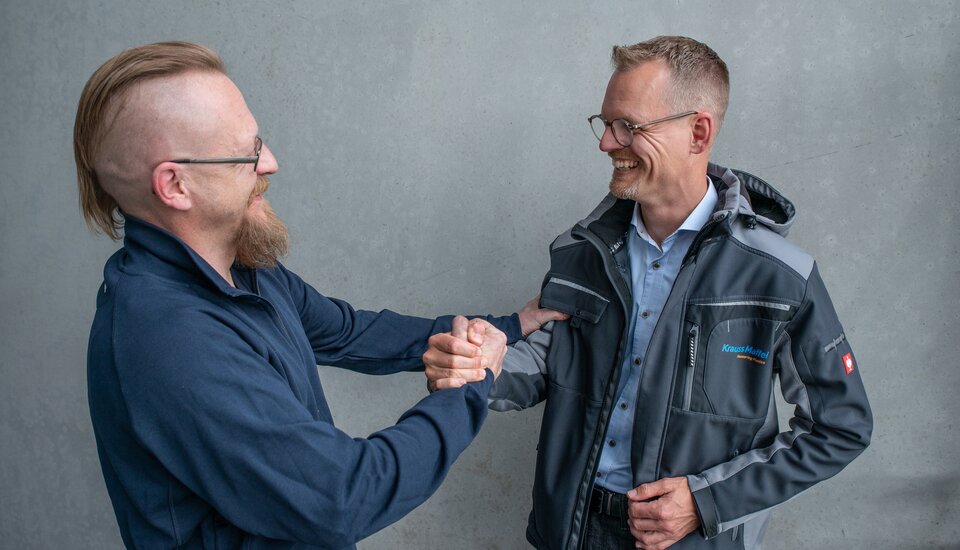
The sense of cohesion is deeply rooted in the Demmel company itself. Around 60 colleagues work for success in Memmingen, 750 across Germany and 1500 at the Demmel Group's international locations.
The production manager emphasizes: “We still have a real hands-on mentality, from the management board to the test personnel. And we live teamwork, regardless of responsibilities. That's what makes Demmel so special for me.”
Based on his experience from previous jobs, Horst Zimmermann describes himself as “very demanding when it comes to customer service.” It is therefore all the more pleasing that the service provided by KraussMaffei, including the pioneersClub, fully inspires him and currently leaves nothing to be desired.
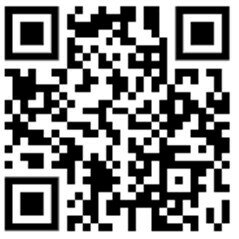
Click here to sign up for the free pioneersClub.
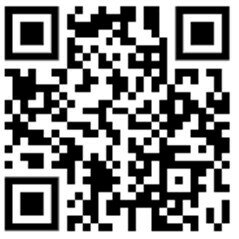
Contact
Stefan.Betzing@kraussmaffei.com
Contact
Daniel.Bachmann@kraussmaffei.com