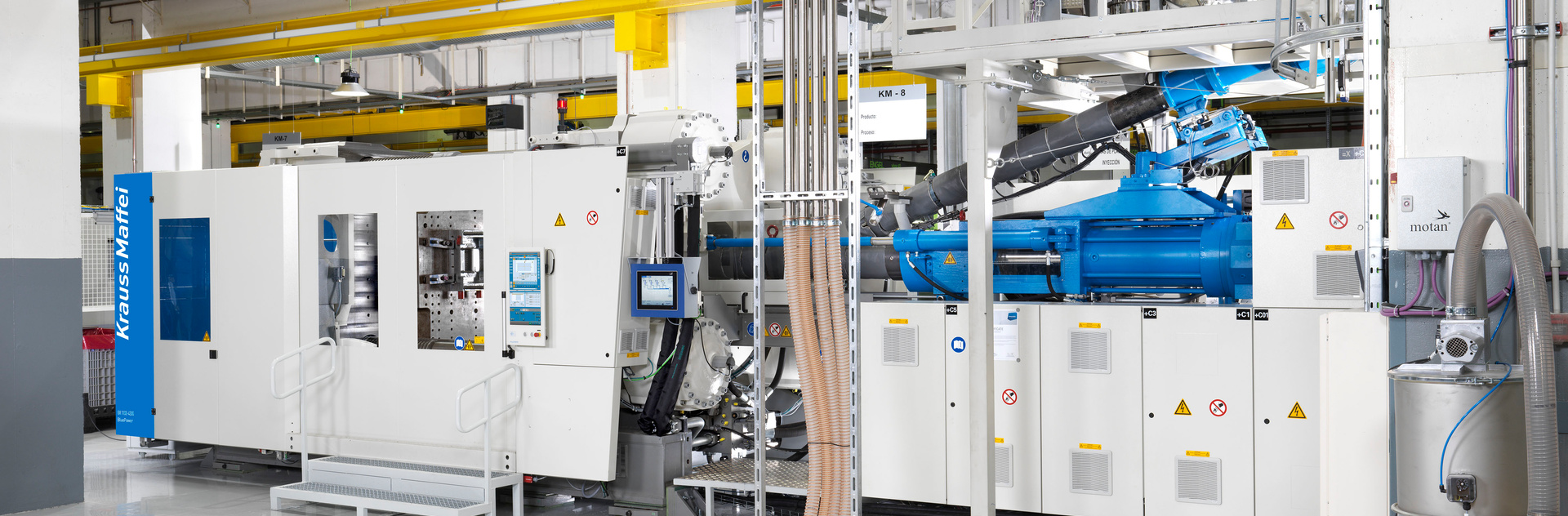
sustainability
Keep the recipe in check
| Petra Rehmet
DCIM direct compounding: ZF Vigo gains control over the material with KraussMaffei
The demands placed on plastics processors for traceability and transparency are growing just as much as the cost pressure. This is why the ZF plant in Vigo, Spain also wants to be in control of the polymers and relies on direct compounding. The new DCIM process from KraussMaffei is economically attractive for components from 50 to 2000 grams—and it has no impact on cycle time.
Standard polymers such as PP, PE and ABS are available from large material manufacturers at any time in constant quality. A PP with 40 percent glass fiber, masterbatch and impact modification - "No problem," the compounder says. But is this reality? Dipl. Ing. (Graduate Engineer) Achim Härtel, Core Engineer Plastics at ZF Alfdorf, Germany, has already been surprised many times: "Sometimes the PP was overheated without anyone having noticed, and multiple times we have found foreign objects such as metal particles in compounds."
Those, like ZF, who manufacture safety-related components for the automotive industry, know what it means if errors result in a recall or even a halt in production. That is why they want to ensure the quality of their own product the best they can. And if this is also economically feasible, even better.
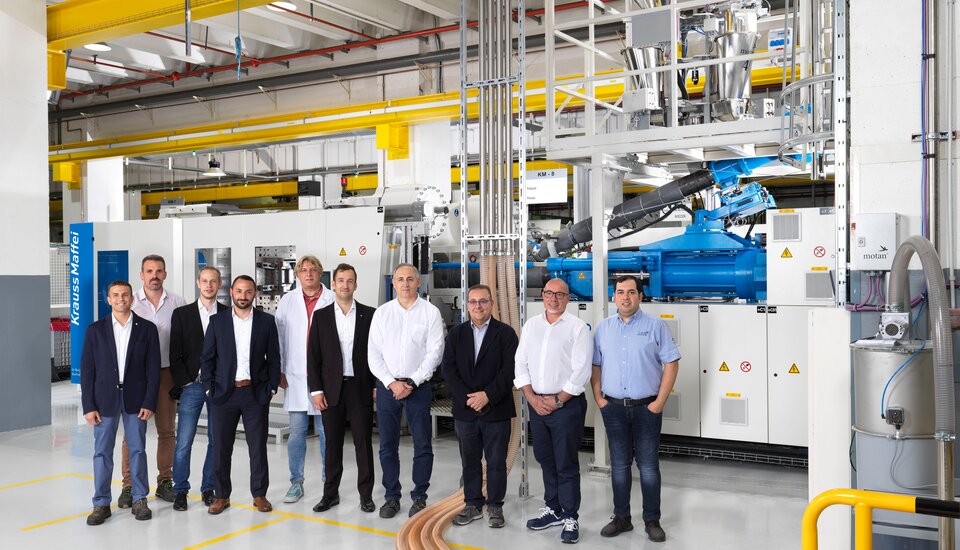
The project team for successful direct compounding at ZF Vigo (from the left): Eduardo Casas (ZF, Injection Molding Specialist), Edgar Lopez (ZF, Manufacturing Engineer), Thomas Drogi (KraussMaffei, Process Engineer), Christian Seyferth (KraussMaffei, Global Expert Sales), Achim Härtel (ZF, Core Engineer Plastics), Jacob Seco (ZF, Manufacturing Engineer Specialist), Jose Trasobares (ZF, Manufacturing Engineering Manager), Angel Lemus (Coscollola, Director Post-Venta), Antonio Muñoz (Coscollola, Director Comercial Inyección), Ramazan Baser (Motan-Colortronic, Project Engineer)
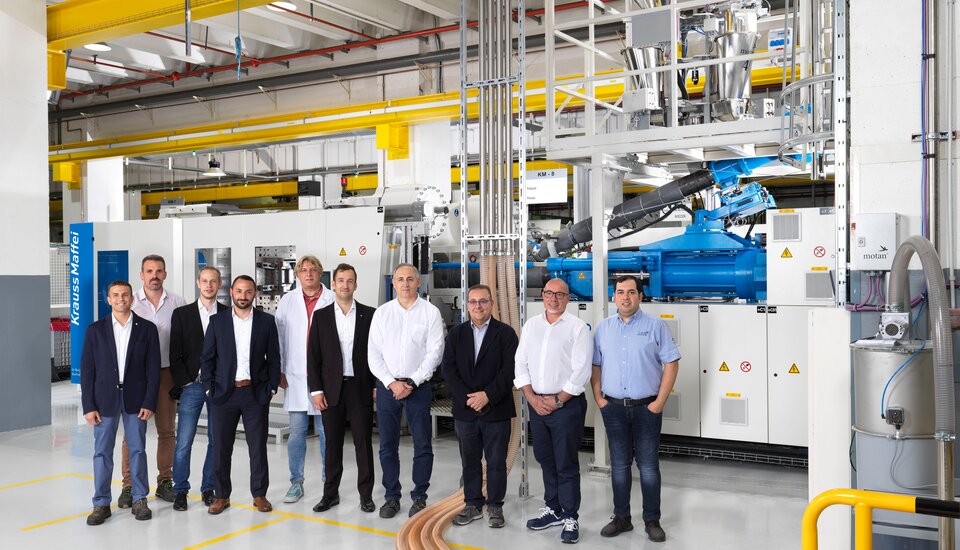
Twenty years of experience in the area of direct compounding
KraussMaffei has two decades of experience in the area of direct compounding, but, due to the investment costs, the familiar IMC system (Injection Molding Compounder) with its twin-screw extruder was suitable in terms of cost-efficiency, particularly for components weighing 1.5 kilograms or more. The new DCIM process (Direct Compounding Inject Molding) expands the portfolio and, since it uses a single-screw extruder, it pays off even for articles from 50 to 2000 grams (based on PP quality).
The demand stays the same: Polymers have to be blended, modified by additives, reinforced or filled and fed into the injection molding process. On the one hand, this saves costs for external compounding; on the other hand, it gives the processor maximum control over the material used.
For new projects or modified requirements, we can now make our own formulation recommendations. These are tailored directly to the specification of the respective component. The material quality stays with ZF and we have the expertise protected in-house, fully documented and tested.Achim Härtel
Core Engineer Plastics ZF Alfdorf / Germany
Special extruder screw ensures perfect mixing
The special extruder screw ensures that all ingredients are perfectly mixed and homogenized. This screw stands out not only because of its optimized design, but also because of its extraordinary length. The ratio of length to diameter is usually about 17-23 L/D for standard injection molding machines but for DCIM it is an enormous 30 L/D. Since technical parts that come into question for direct compounding usually have cycle times of 20 seconds or more, the additional material processing can be done even without affecting cycle time.
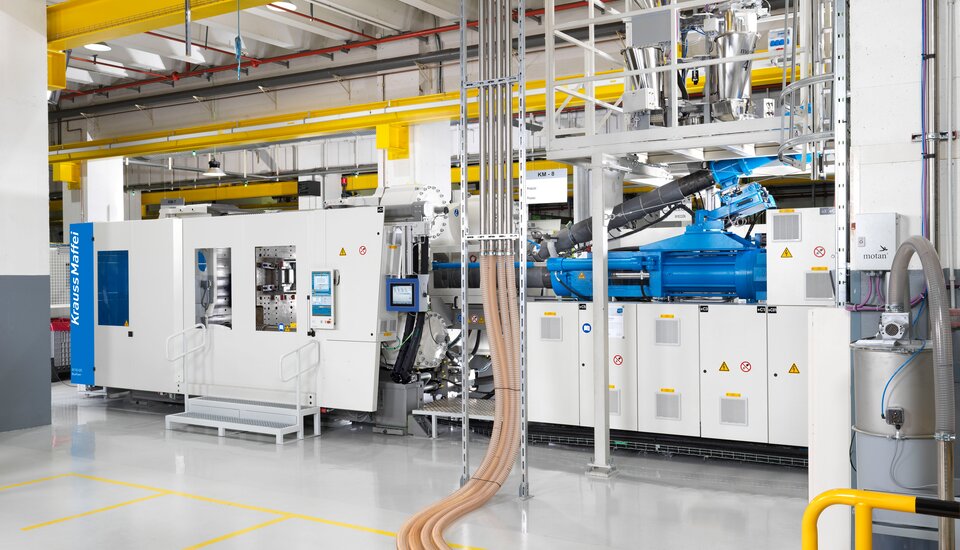
Compounding with DCIM: The single-screw extruder is installed in a user-friendly piggyback position over the plasticizing unit.
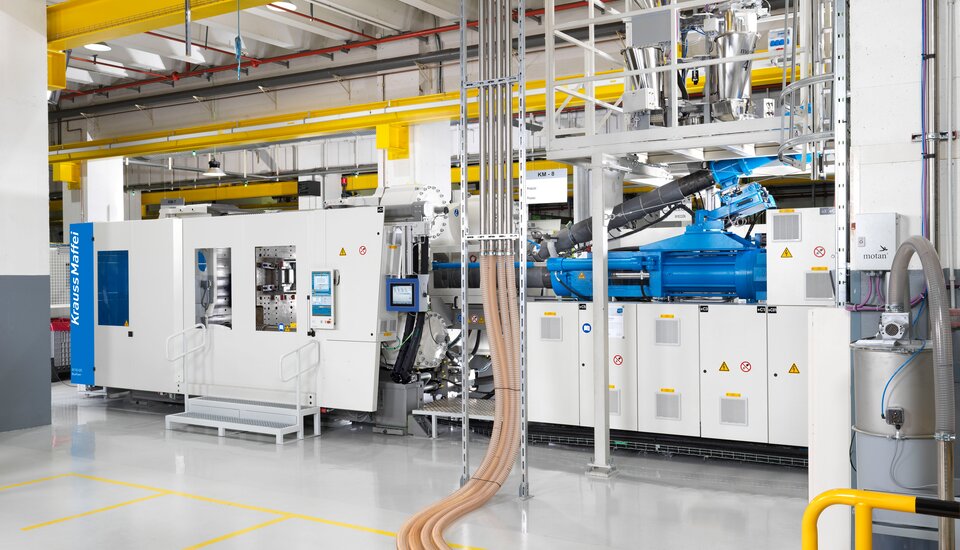
The DCIM concept offers the plastics processor maximum flexibility. On a standard hydraulic machine, usually the GX series, the single-screw extruder is installed in a user-friendly piggyback position over the injection unit. Both produce intermittently, stopping the extruder automatically every time the injection volume for the next cycle is reached. The compounded melt goes directly into the plasticizing unit of the injection molding machine without any cooling or buffer storage.
Production in one heat reduces CO2 footprint
Due to the one-step process, production is performed in one heat, which not only reduces polymer degradation, but also conserves valuable energy and reduces the CO2 emissions. If you don´t want to compound at the moment, the machine can be easily used for standard operation without any elaborate conversion work. Due to the units Z configuration, the injection machine is very compact - with a small footprint.
DCIM was brought to market in 2019 and got somewhat sidelined by the COVID period, finding more and more interested parties now. For Achim Härtel from ZF, it distinguishes itself from processes of other providers who impregnate continuous fibers with low-viscosity matrix material by processing of plastics with medium viscosity. These have better mechanical properties with respect to safety-related components.
At ZF Vigo, which belongs to what is called Division "R" (R stands for "restraint") within the ZF Group and manufactures corresponding personal safety systems, this is an important point. In addition, DCIM is offered for machines with clamping forces from 1,600 to 11,000 kN, being suitable for larger applications or multi-cavity molds.
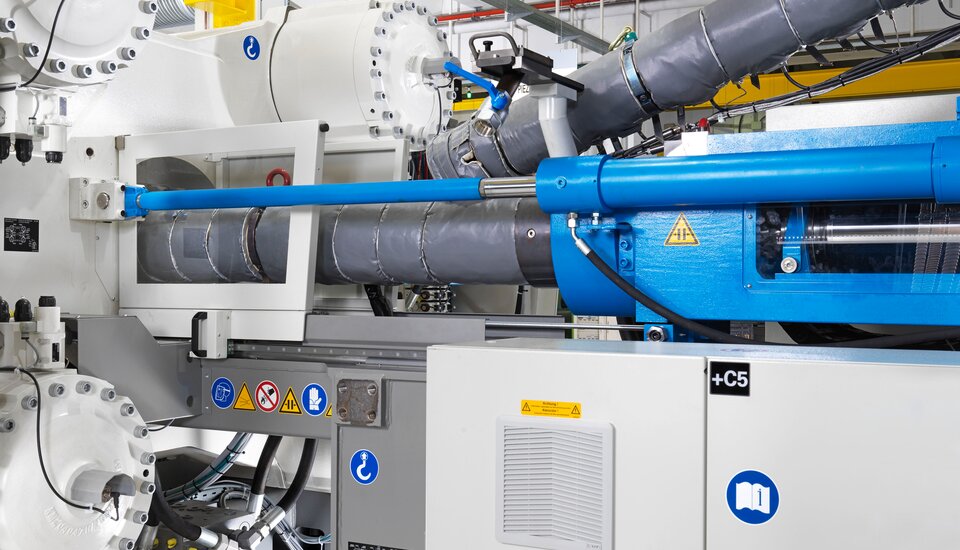
The compounded melt goes directly from the single-screw extruder into the plasticizing unit of the injection molding machine. This way the entire process is performed in one heat. As a result, polymer degradation is reduced, less energy is needed and CO2 emissions are cut.
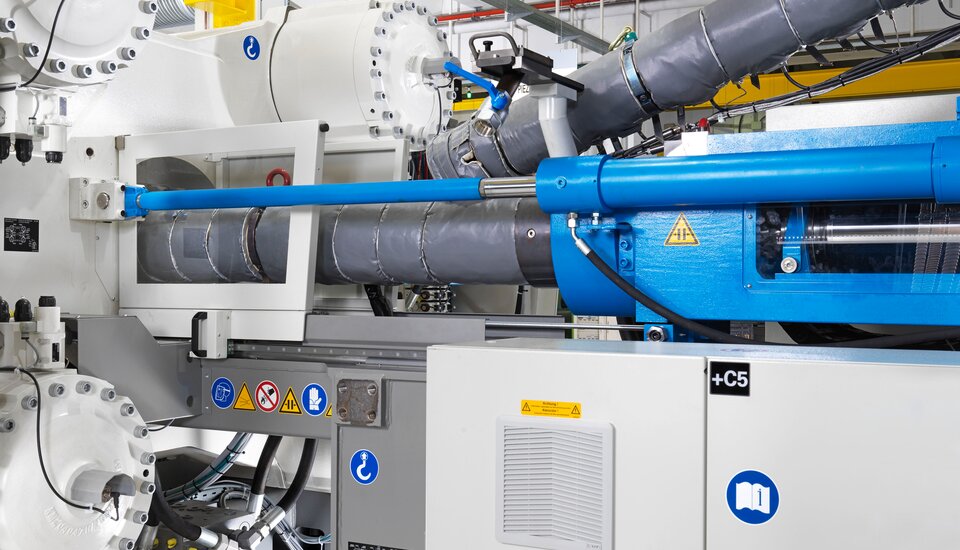
Reduced material costs and a fast ROI
The fact that, aside from gaining control over material properties, you also receive cost benefits, is shown by an application example from KraussMaffei: A plastic plate for mineral wool assembly compounded and injection molded from PA6 with 50 percent glass fiber, two percent flow promoter, 0.5 percent masterbatch and 0.5 percent heat stabilizer has 20 percent lower material costs with DCIM. As a result, the added expense for the DCIM system (compared to a standard machine) pays for itself in less than one year.
Interesting for recycling materials and bioplastics
The technology is particularly interesting with respect to recycling and the use of bioplastics and natural fibers. Jacob Luis Lopez, Manufacturing Engineer Specialist at ZF Vigo, already has his eye on these topics: "The competition has gotten so fierce that you always have to be one step ahead." First, however, the technology has to be established and transferred to other ZF locations. For the ZF plant in Timisoara, Romania, two DCIM machines have already been ordered and the trailblazing location Vigo has also already requested another DCIM machine.
Contact
franz-xaver.keilbach@kraussmaffei.com