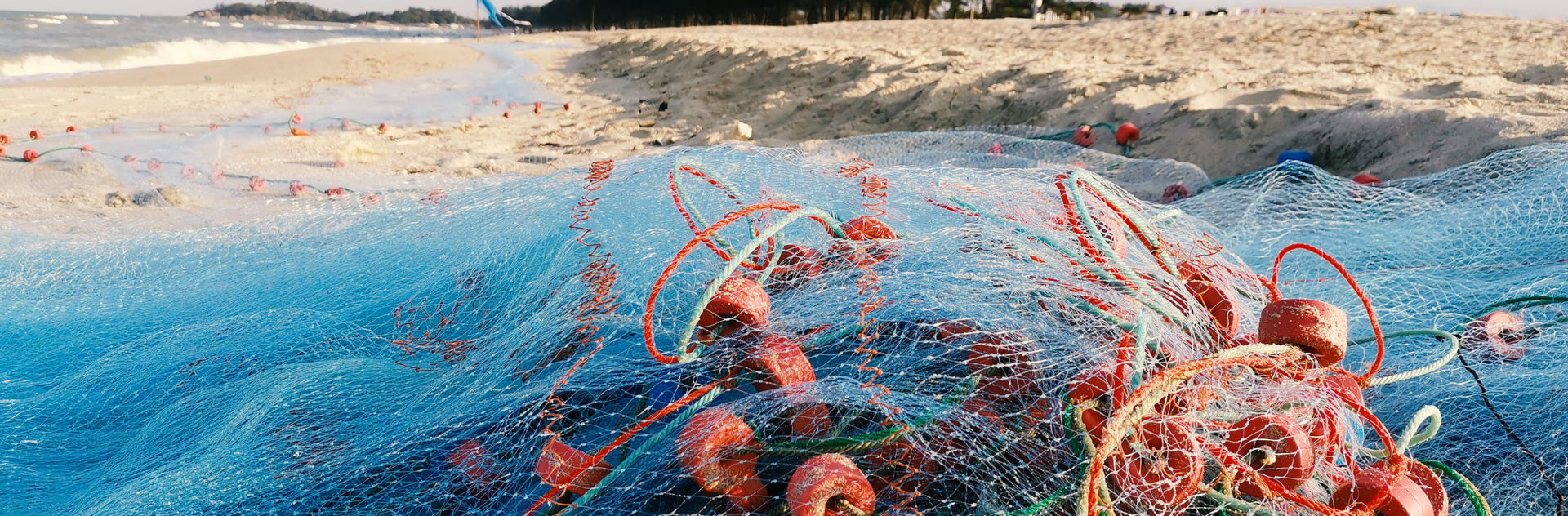
sustainability
From the sea into the tunnel
| Petra Rehmet
Oldroyd uses 100% seaplastics for its products
Old fishing nets and plastic ropes: These are valuable raw materials for the Norwegian company Oldroyd who uses them to manufacture products for tunnel construction on three CX 160-750. They are more durable than steel and at the same time protect the environment. With these advantages, it does not matter if from time to time they give off a faint fishy smell.
Where is the longest road tunnel in the world? Where are there over 900 traffic tunnels? Norway. Anyone driving through the concrete pipes in a car does not see where KraussMaffei's customer Oldroyd earns their money: The membrane system including injection molded fastening material lies behind the concrete pipes. It prevents water penetrating through the soil causing damage to the concrete layer. Basically it works like a Goretex shoe.
Oldroyd originally comes from the area of plastic extrusion and revolutionized the market with its multilayer films for tunnel construction when it made one side no longer black but white. This increased the transparency and quality in the installation of the membrane because one could now see holes forming from stone points. Working in a bright environment is also much more pleasant.
In order to secure the film to the subsurface, corresponding supporting elements are required – and this is where company founder John Oldroyd Cheetham comes into play. The tech-savvy inventor developed innovative solutions and recognized that injection molding would be the appropriate technology to manufacture them.
Our strength is thinking outside the box and then also making quick decisions as a family-run company about which plan we want to further pursue.John Oldroyd Cheetham
Company founder Oldroyd
Higher degree of automation ensures smooth ghost shifts
John Cheetham and his team consulted the Saxe Group with Rolf Kjønnerud as a local contact partner to get advice about the necessary machines. Saxe represents KraussMaffei in Scandinavia and in addition to the machines also provides a comprehensive technical service. The cooperation between Oldroyd, Saxe and KraussMaffei is exceptional.
Together the partners are always trying to realize new ideas and to push perceived boundaries. Kevin Beuchel, Regional Sales Manager at KraussMaffei: "John regularly pushes the limits with our machines, but that's a good thing and everybody benefits."
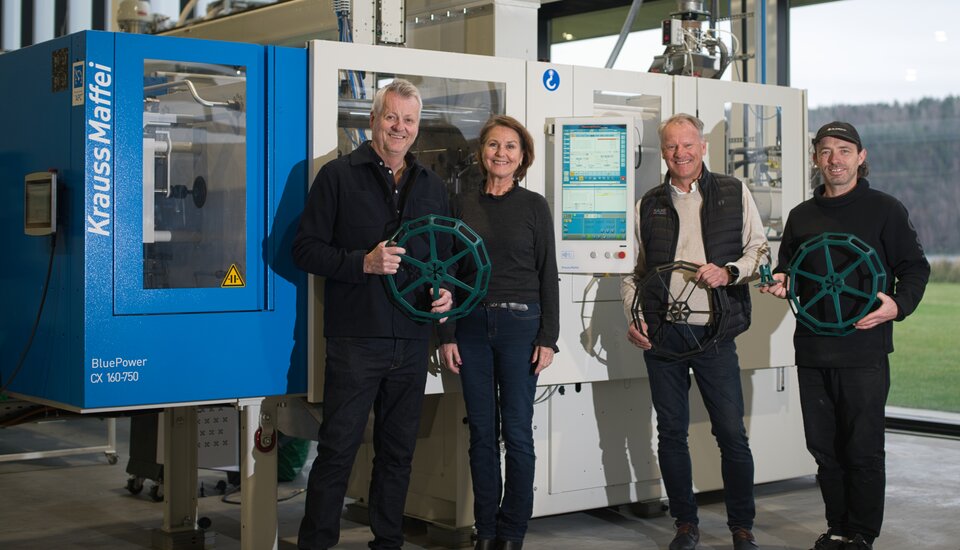
Working together to promote sustainable tunnel construction (from left): John Oldroyd Cheetham (founder of Oldroyd), Linda A. Celin (CEO Oldroyd), Rolf Kjønnerud (KraussMaffei Agent SAXE) and Carl Kremer (Product Development/Operator Oldroyd) in front of one of the CX 160-750
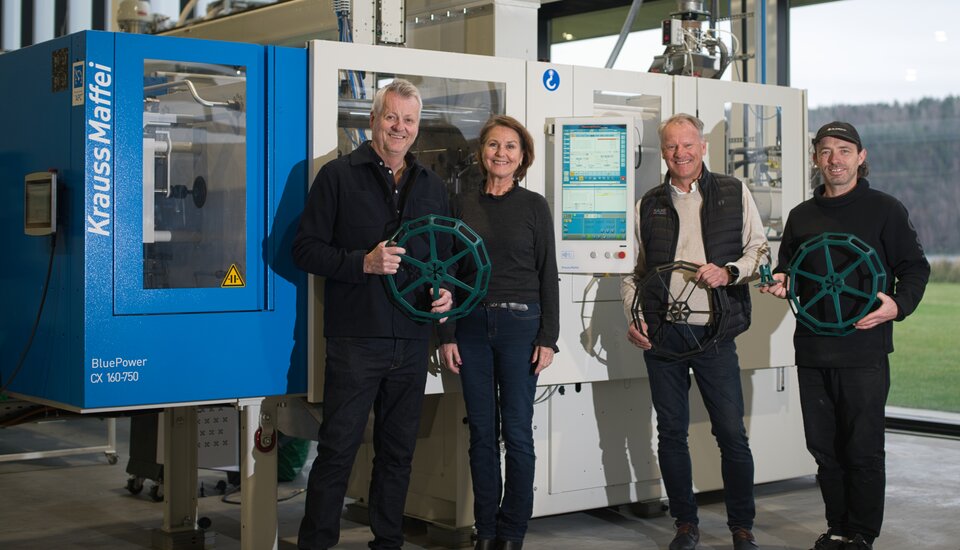
Three identical CX 160-750 have been in operation in Stathelle (around 160 kilometers south-west of Oslo) for a few years now and another two-component machine will be added soon. All machines are equipped with the KraussMaffei LRX robots which are made in Germany (oversized variant). Thanks to the very long vertical axles, they can stack the products up to a height of 2 meters starting on a ground-level pallet.
The sturdy design and the enormously high availability of the KraussMaffei robots enable the customer to produce over the weekend without any manual intervention. European production facilities are able to compete worldwide thanks to these "ghost shifts".
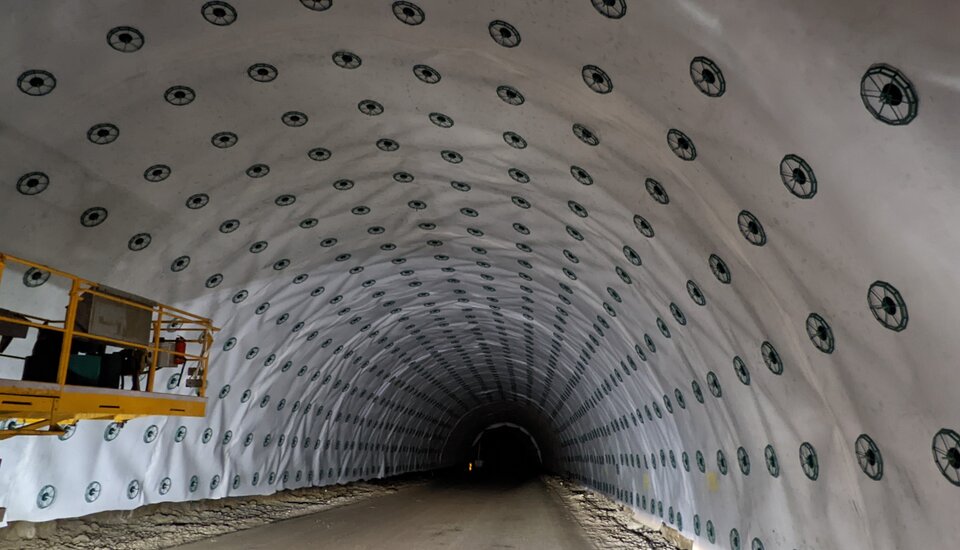
The so-called spacers, curved products with grid structure, create a distance between rock and membrane, like here, e.g., in the Sandoy tunnel on the Faroe Islands
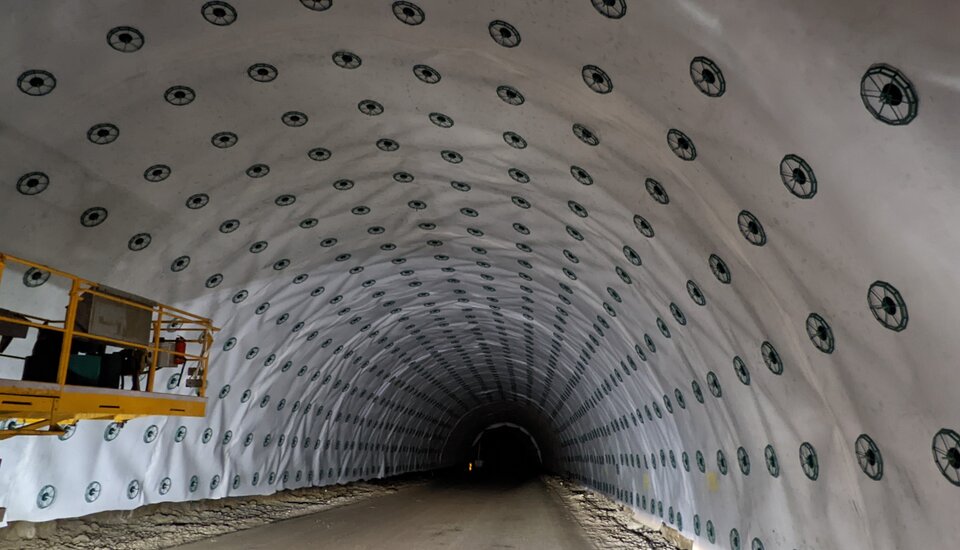
100 percent seaplastics
Anyone who has never worked on the topic of civil engineering may underestimate the number of units actually involved at Oldroyd. 300,000 to 400,000 so-called spacers alone are required for a tunnel. The curved products with grid structure create distance between stone and membrane.
With its weight of 150 grams, the spacer is created in a cycle time of around 15 seconds. The diameter and height vary, there are approximately 20 different models.
The material is unique at Oldroyd: 100 percent seaplastics, which is roughly half PP and half PE. The remnants of broken fishing nets and plastic ropes are collected on the coast of Norway by specialist companies and crushed, washed, and regranulated. The subtle fish scent does not need to be removed for the tunnel construction.
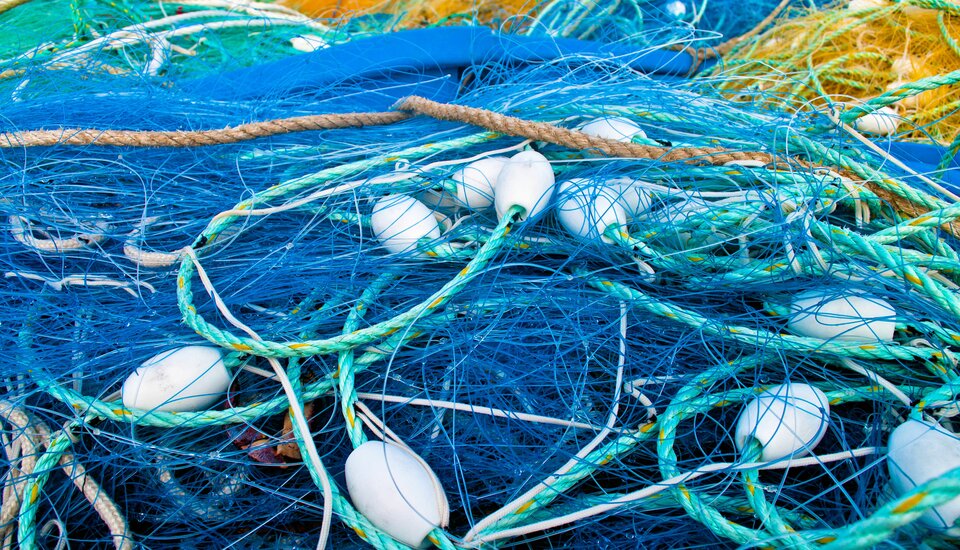
Old fishing nets and ropes are collected, recycled and then used to 100 percent for the production of the spacers.
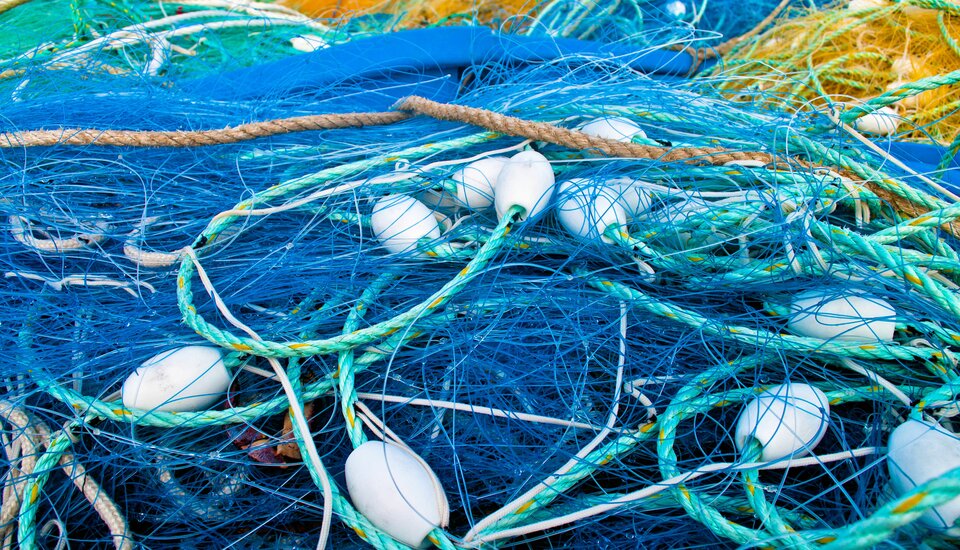
Every part is a good part with APCplus
The APCplus machine feature from KraussMaffei is very helpful for the changing material compositions and resulting viscosity fluctuations. It ensures a very constant shot weight by adapting the switchover point and the pressure level from shot to shot. The team also allowed tests to be conducted and other materials to be added, just to see whether it works with the APCplus.
It is very reassuring for us to know that the machine controls everything itself and we will definitely have good parts after a weekend.Carl Kremer
Product Development/Operator Oldroyd
Oldroyd's dream figure of 35-15-90 shows that a company does not have to be large to be successful. This figure stands for 35 employees, a total of ten to 15 customers, 90 percent market share in Scandinavian countries.
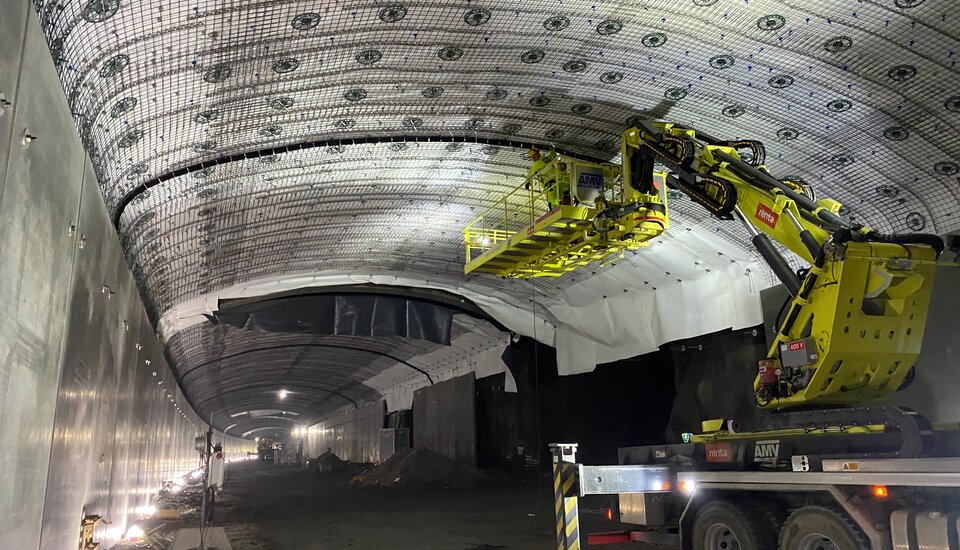
The construction of the Stockholm Bypass (a series of underground motorway tunnels) is currently the world's largest tunnel project. Thousands of spacers from Oldroyd are also used here.
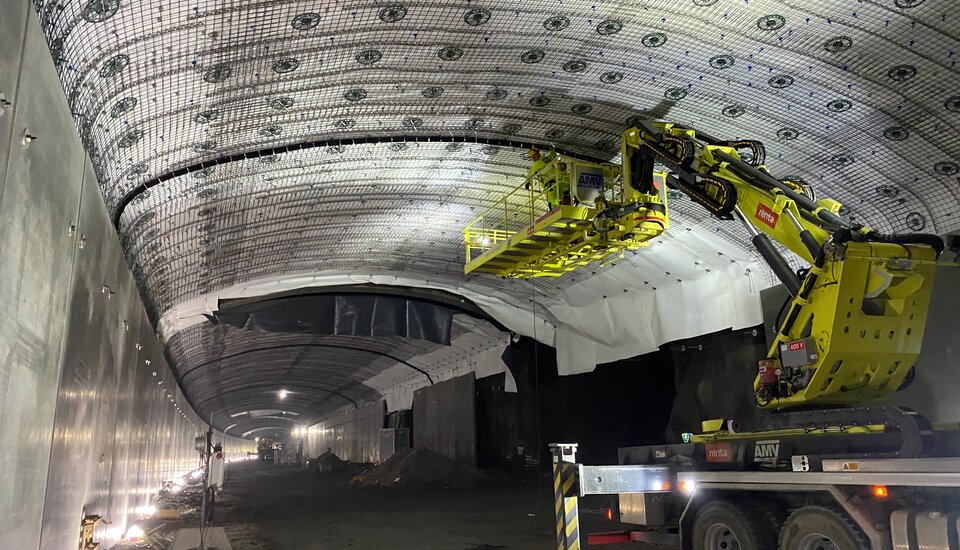
120-year product RoadStar
Tunnels are an everyday phenomenon in Scandinavia because they are used to get around the many fjords. Tedious alternatives would be long detours or ferries. 90 percent of the water protection equipment of tunnels in Scandinavia comes from Stathelle. To ensure that remains the case, there are continuously new developments.
Just recently a two-component platen, called RoadStar, which is secured to the steel rods which connect the concrete wall to the stone layer. Up to now these platens were made of metal and corroded accordingly, which is why maintenance is required and a replacement after roughly 50 years.
The service life of the RoadStars invented by John Cheetham was estimated at 120 years in special aging tests. This alone helps save a lot of resources. In order to test innovations, Oldroyd relies on the help of its customers. They have been working together in a trusting partnership for years and therefore it is not a problem sometimes to get access to a special tunnel section in order to introduce a new technology.
The RoadStar was well received, also because the integrated TPE layer has a sealing effect on one side, and is impact-resistant on the other thanks to PE. In spring 2023 a two-component CX machine will start series production at Oldroyd. The customer decided on KraussMaffei in order to meet the high quantity requirements and on account of their extensive technical advice.
Success on the market will definitely mean more machines will make their way north. The next project is already in the planning stages – however, it is still top secret so we cannot talk about it just yet!