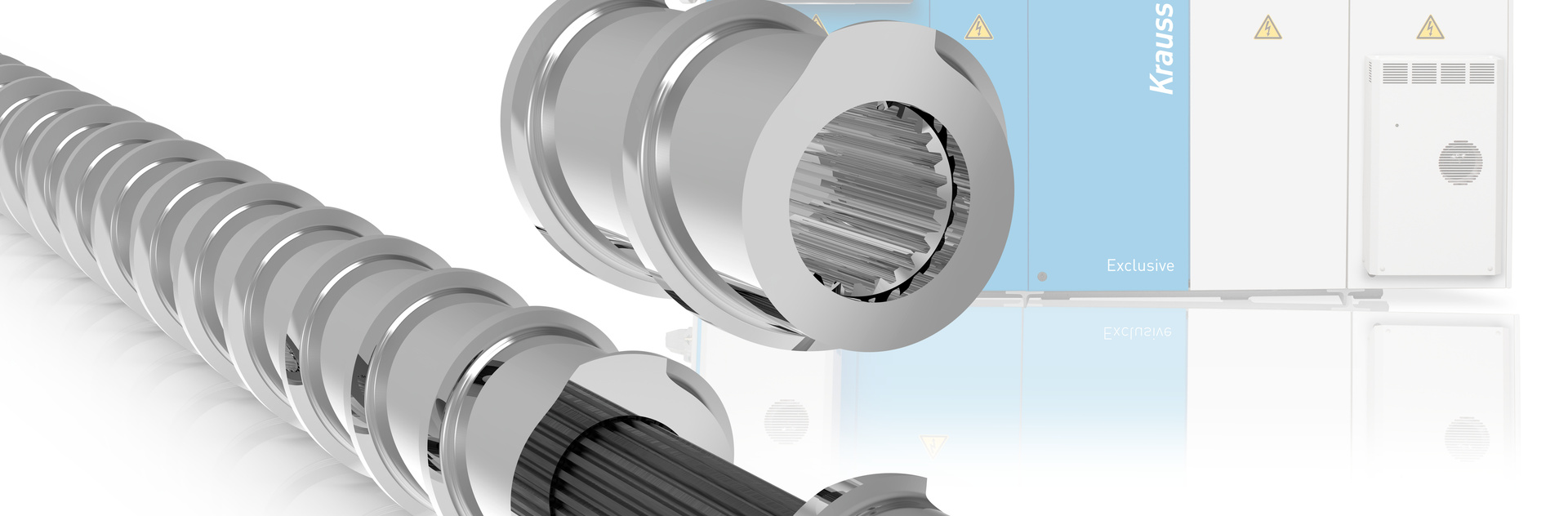
trendgineering
Design screw geometries faster
| Andreas Weseler
Modular single-screw design gives know-how edge
At K 2022 in Düsseldorf KraussMaffei will demonstrate an exciting current development project. For the first time, the machine manufacturer has produced a multi-spline shaft and different screw elements for a single-screw extruder. A decisive advantage is the enormous gain in knowledge, which allows the screw geometry to be adapted to new or customer-specific materials.
Modular screw geometries, which are flexibly assembled with specific screw elements that can be changed at any time, have long been state of the art for twin-screw extruders. The situation is different for single-screw extruders, which use universal screws that can process a wide variety of materials.
These are made from a single piece with bolted-on shear and mixing parts that allow homogenization to be optimized. A quick adjustment of the feed section or the compression ratio is thus not possible, which in turn leads to the fact that a new screw has to be designed and manufactured when changes are made. A procedure that drives up costs and time frames in development.
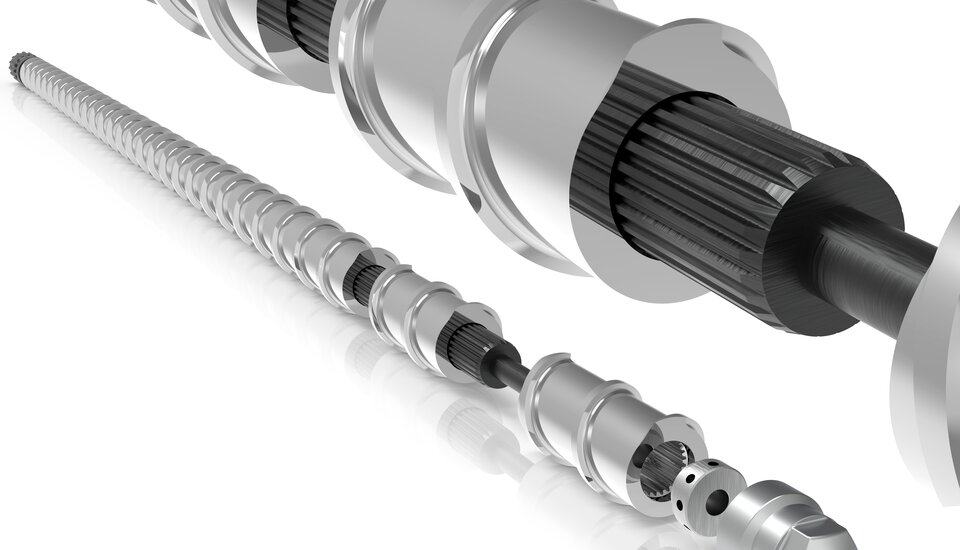
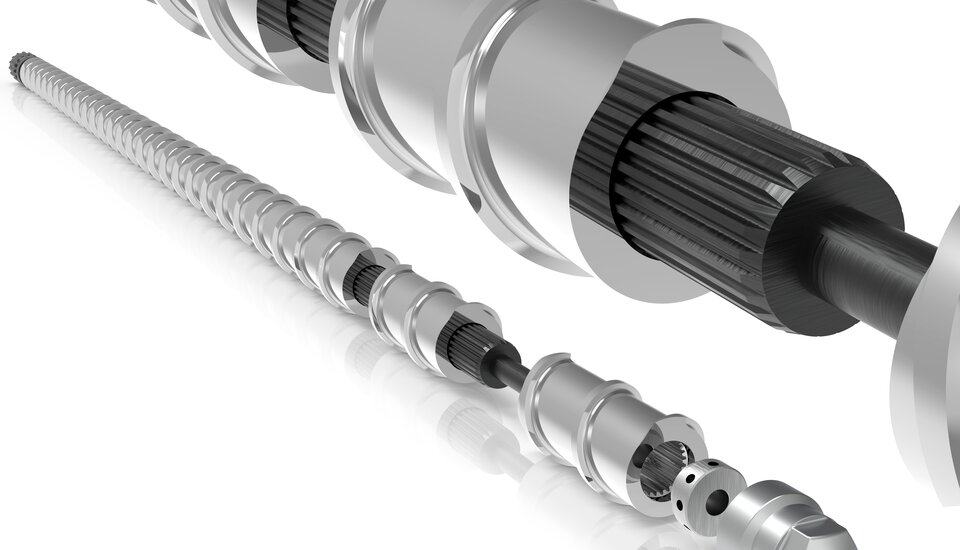
Fast and flexible screw configuration
For this reason, a modular single-screw extruder that can be equipped with a large number of different screw elements is now available at the KraussMaffei Technical Center. "With this project, we are able to take a close look at the process parameters of a new material or a new material type and develop a precise screw geometry adapted to it," says Annette Beierling. Initial tests with PC have already been carried out and further screw elements developed on the basis of the results.
"The experimental investigations with PC have shown that simulating a screw design does not always lead to the best result." With the modular single screw, the machine builder will be able to design screws flexibly and at short notice in the future. An enormous time advantage. This is particularly interesting for new materials that are increasingly being used in the pipe industry.
"At the same time, we can run individual tests for customers who process very specific materials and, if necessary, even manufacture special screws," explains Annette Beierling. This brings great advantages, especially for customers who operate in niche markets and require special screw geometries for them.