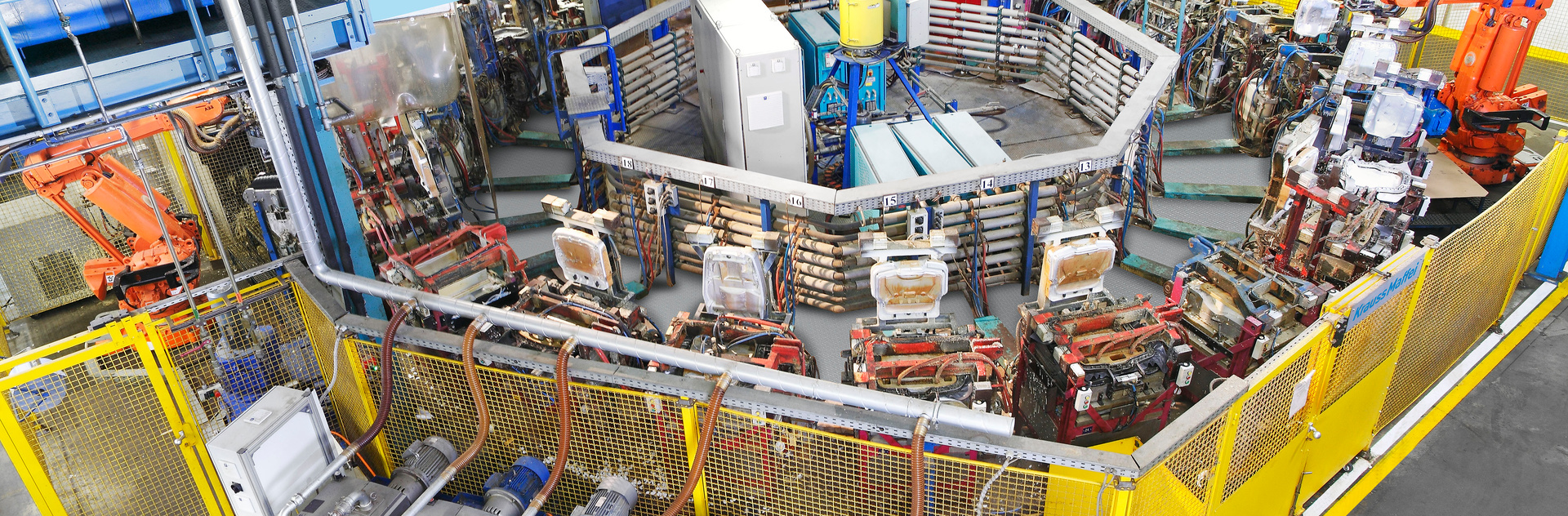
trendgineering
More streamlined and powerful
| Michaela Huber
Grammer tests newly developed high-pressure mixing head in series production
On tractors and forklifts or in large trucks: Wherever you see a seat with a distinctive rib pattern in the backrest, you're looking at a product from market leader Grammer AG. The polyurethane foam cushion has already been produced 400,000 times with KraussMaffei's newly developed precisionMixhead 8/12-2K-40, since this is seeing its first series application at the long-standing customer and partner.
Smaller, lighter and with even better mixing quality—these were the objectives when the mixing head redesign project began at the end of 2020. The team headed by Ralf Moser (Head of Mixing Head Development) thus took on board the wishes of customers for whom convenient handling in everyday production is important. In most cases, the mixing head is attached to a fast-moving robot that transports it from mold to mold, where it then pours foam into open pour patterns.
Occasionally, it even has to plunge into an opening with precision when the mold is closed. That's where a streamlined design pays off. Even though the previous model had an excellent mixing quality, the goal was to increase this once again—which was also successful. This opens up a wider production window, especially in terms of output capacity and pressures. The feedback after the first series production at Grammer, which has now lasted for over 400,000 shots, is correspondingly positive.
We find that the mixing head is yet another improvement over the older version, with which we were also already very satisfied, because of many details.Heinrich Hammer
Head of Process Engineering at Grammer
As the world's leading provider of seating solutions for commercial vehicles and an even larger division dedicated to interior automotive elements, Grammer is a heavyweight with 14,000 employees and 46 manufacturing sites in 19 countries. Since its foundation in 1880 as a saddlery, the company has continuously developed and opened up new technologies, such as the production of polyurethane (PU). At the Haselmühl plant near Amberg, more than 1,000 employees manufacture more than 600,000 seats per year, among other components.
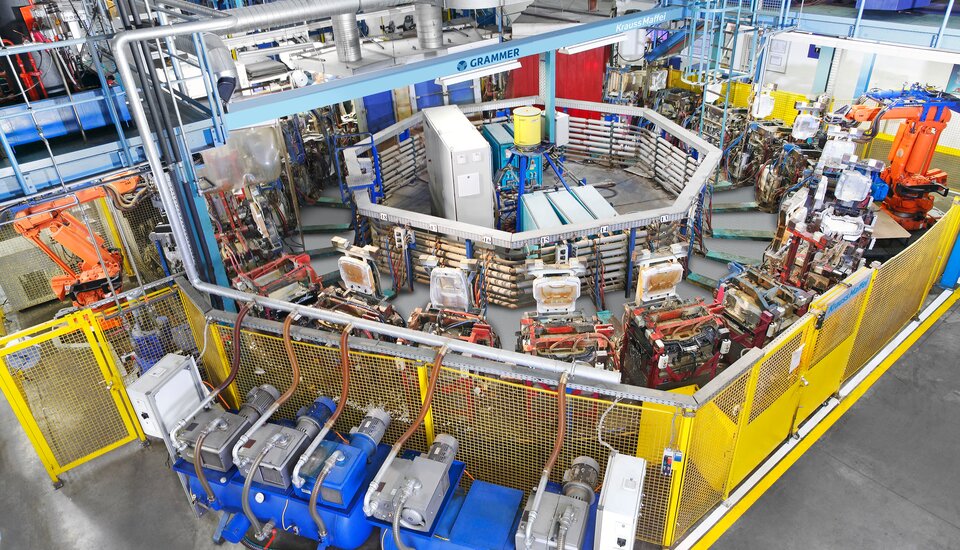
The seats with the familiar Grammer pattern in the backrest are produced in a rotary table system with 24 stations. The robot with the new mixing head from KraussMaffei is on the left side of the picture.
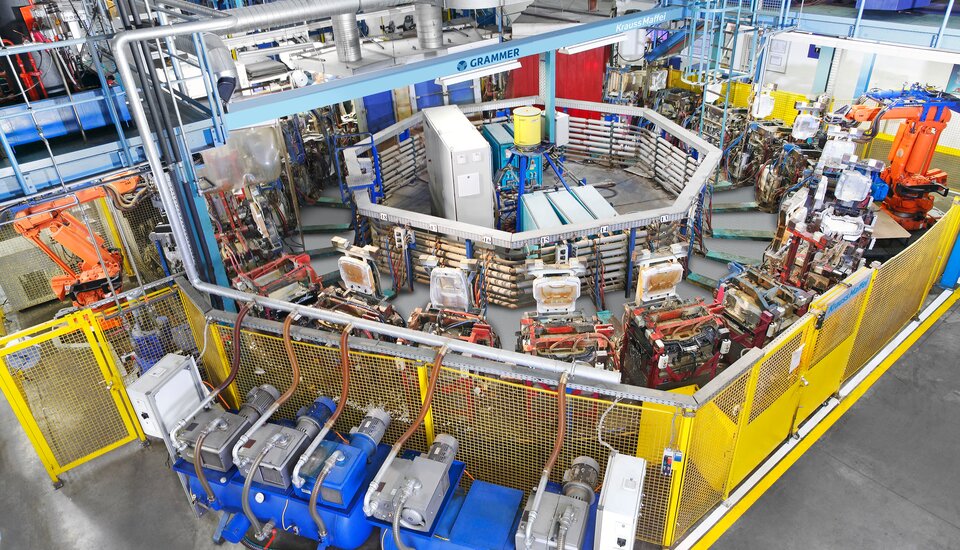
Here, the precisionMixhead 8/12-2K-40 operates one of the two rotary table systems (also from KraussMaffei) for tractor, construction machinery and forklift seats. More than 20 molds are arranged around each rotary table. Here, the new mixing head first moves into the open mold, into which the cover has already been inserted and sucked in by vacuum, and fills it with flexible foam. A cover closes the mold at the top and the polyurethane fully cures.
After each filling procedure, the table rotates one station further and the mold is fitted with a cover with a new geometry, which is closed immediately this time. A second mixing head (also 8/12 from KraussMaffei), which is plunged into the cover, pours a compact foam into the resulting cavity, and this foam serves as a frame for fastening the seat. After six seconds, this foam is firm enough for the mixing head to allow it to open. A little later, the cover opens and the cushion that is now almost finished moves on to the fully automatic laser trimming unit. This is how several thousand parts are produced every day—with an extremely low reject rate along the entire process chain.
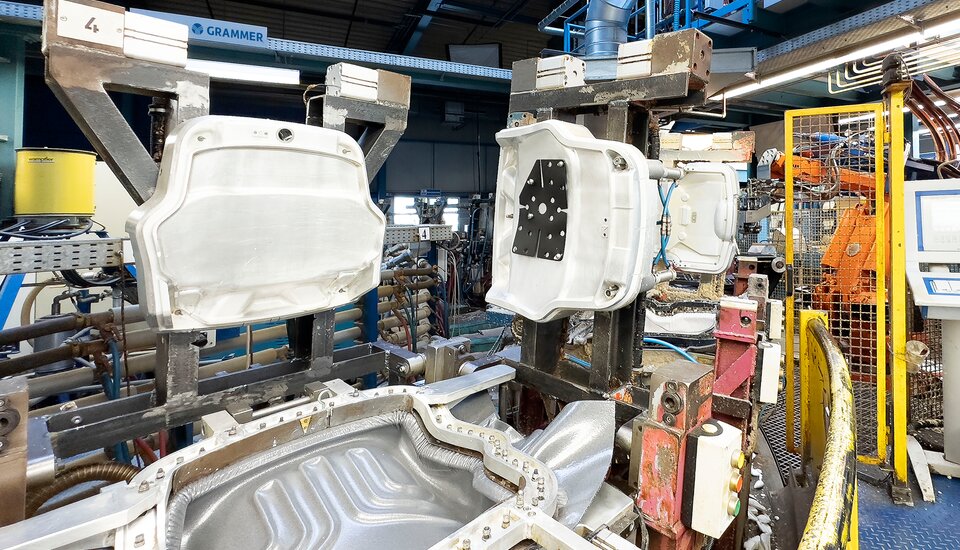
Each mold has two covers with different geometry so that rigid foam can also be used to produce the holding elements.
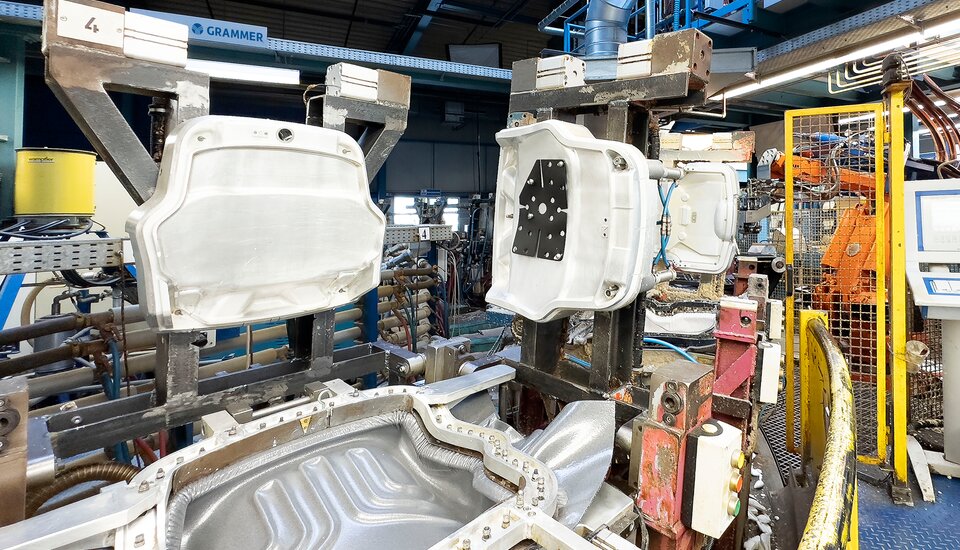
The mixing heads are the heart of the PU foaming system because this is where it is decided whether the polyol and isocyanate components are mixed homogeneously and in the desired ratio. If this does not happen, the discharged material may have sticky spots (if the polyol is running ahead) or the foam cushion may be too hard or too soft. The latter must not happen, since each of the major manufacturers of forklifts and tractors has specially defined degrees of hardness for its seat cushions.
How does the mixing process take place?
Polyol and isocyanate are in a closed-loop system from the respective daily tank to the mixing head and back; they flow into the mixing chamber through nozzles (throttled by needle). But this only happens when the control piston, which is fitted with recirculation grooves, clears the way. If it does not, the flow remains in the circuit. This system ensures that the pressure, quantity, temperature and flow rate of the components are always constant at the nozzle.
If material is to be discharged, the control piston opens the path to the mixing chamber until the shot weight is reached. This is calculated from the output capacity multiplied by time; for example, 200 grams multiplied by five seconds equals one kilogram of polyurethane. In the mixing chamber, the components are atomized and mixed together at 100 to 200 bar. An attached L-shaped transfer mixing head, such as the precisionMixhead, is required for use in open molds.
KraussMaffei has held numerous patents for this technology since the 1980s. Here, the resulting foam is deflected into the outlet chamber at a 90-degree angle and completely discharged by a cleaning piston. If you narrow the transition from the mixing chamber to the outlet chamber by allowing the cleaning piston to protrude somewhat, additional post-mixing takes place here and the discharge behavior calms down.
This description shows that it is a complex process. To optimize an existing and proven high-pressure mixing head, therefore, it is necessary to proceed analytically, which is why Ralf Moser and his team used flow simulations as a basis. The component mix is best evaluated when the flow rate is as low as possible.
Heinrich Hammer explains: "In series production, we run at 220 to 250 grams per second. With the new mixing head, we tried to explore extreme limits and went down to 60 grams. In this case you sometimes get inhomogeneous areas with hardness deviations (hard/soft differences between left and right). But with the new mixing head, homogeneity and uniformity were still top-notch."
You can get a first impression of the foam quality from a so-called cup shot of about 60 grams into a transparent vessel or from a "fish", that is, polyurethane applied flat to a coated piece of cardboard. The practical experience with the precisionMixhead 8/12-2K-40 coincides with the flow simulations that the team from KraussMaffei and the Chemnitz University of Technology had made during the development. The mixing quality was actually improved by a factor of three.
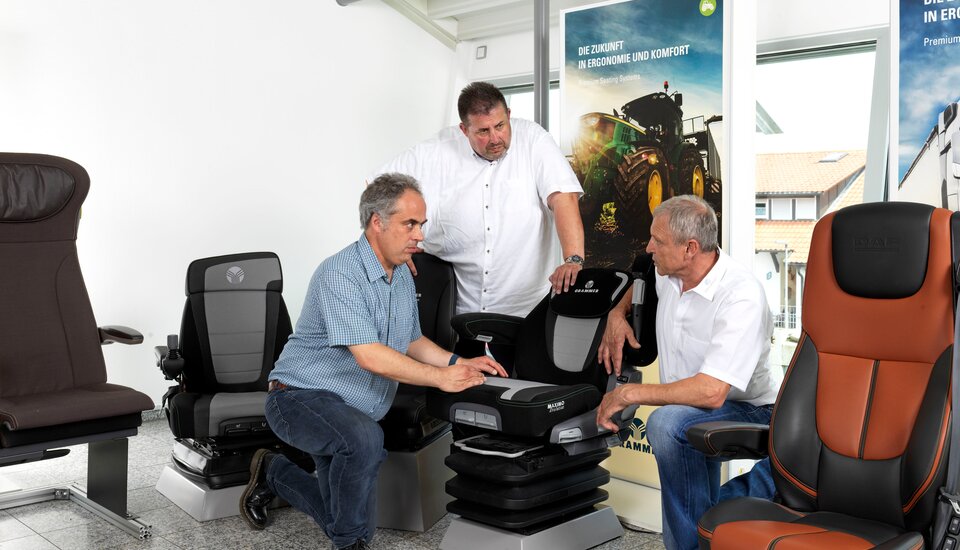
Rolf Moser (Development Manager of Mixing Heads at KraussMaffei Technologies GmbH, far left) and Wolfgang Rößler (Area Sales Manager of RPM, KraussMaffei Technologies GmbH, center) continuously exchange ideas with the experts like Heinrich Hammer (Team Leader for Process Engineering of Foam, Grammer Deutschland GmbH, right) from Grammer, because modern seats are high-tech.
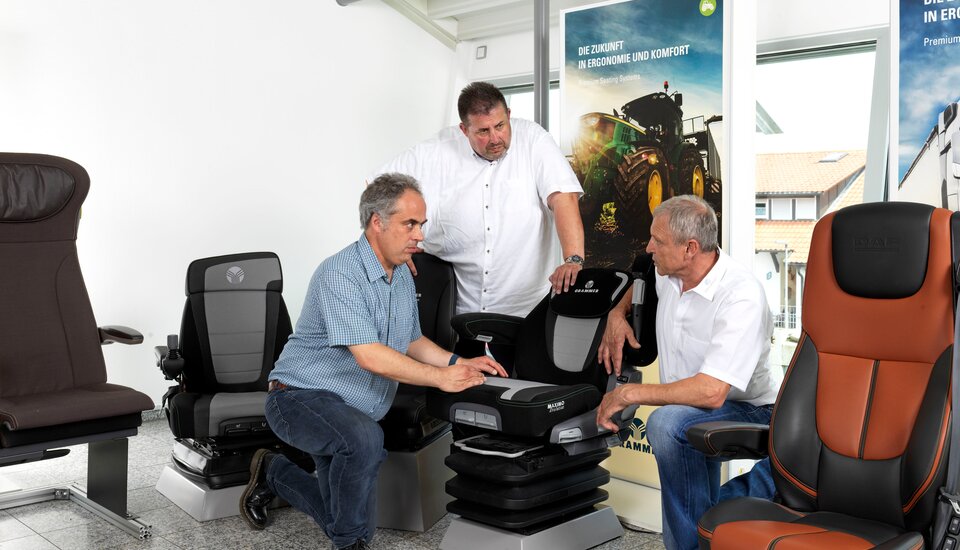
To ensure that this is achieved with precision, Grammer has been using Vario nozzles from KraussMaffei for years. Unlike standard spring-loaded nozzles (which provide sufficient accuracy for many applications), these operate with an air cushion located in a gas chamber behind the nozzle. It is under a pressure of 160 bar, which is transmitted to the needle by means of a diaphragm. As a result, this needle can move back and forth to compensate for pressure changes that occur as the component flow rate fluctuates.
Since there is also almost no friction in the system, the pressure conditions during the shot remain constant from start to finish. In the case of spring-loaded nozzles, jerky and delayed movements can occur in the worst case, which then result in pressure changes and thus uneven mixing of components.
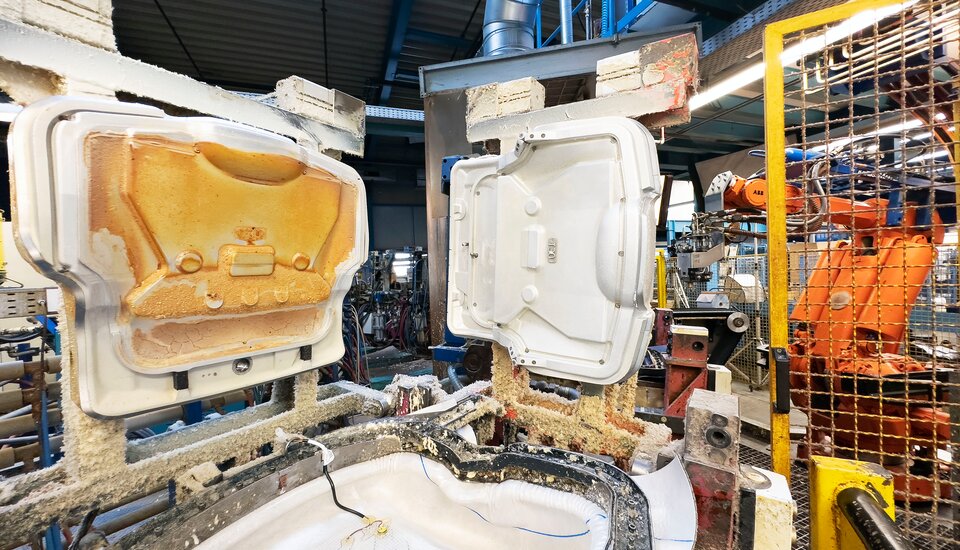
Even elements for seat heating can be integrated into the foam with a little know-how.
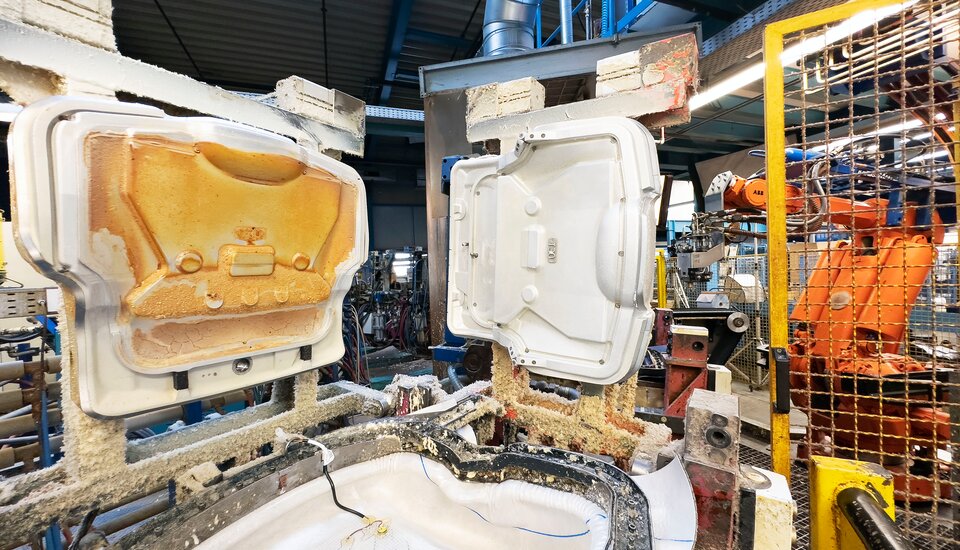
Aside from improving the mixing quality, the goal of the redesign was also to change and, above all, decrease the geometric dimensions of the new head. Both the mixing and the dimensions can be influenced by the position of the nozzles through which the polyol and isocyanate flow into the mixing chamber.
If they are directly facing each other, there is a risk that each component will get into the flow channel of the other. Mixing is more successful when the nozzles are arranged at an angle. By making appropriate optimizations, the team has succeeded in reducing both L-legs of the transfer mixing head to 92 and 65 percent of the original values, respectively. This means a reduction in volume of up to 25%. This also reduced the weight from 13 to about 10.5 kilograms.
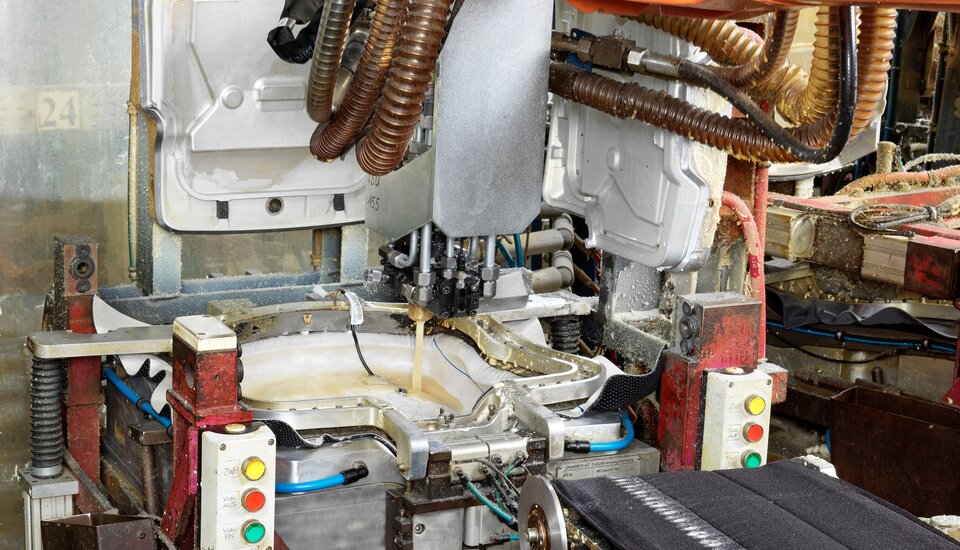
During pouring, the mixing head determines the homogeneity of the foam — and thus the quality of the seat.
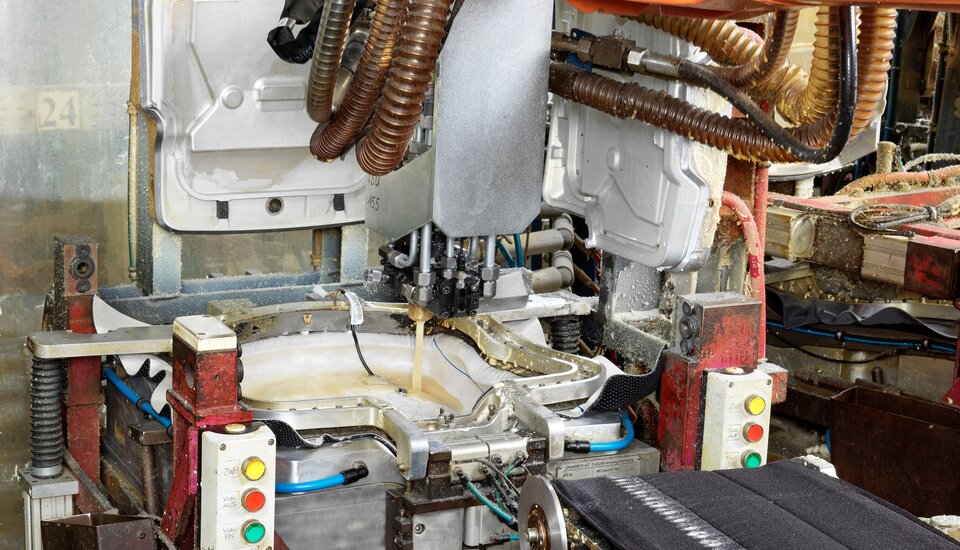
The fast service that can be achieved with the new generation should be of particular interest for users. Mixing heads require regular maintenance to produce at a consistent performance capacity. In the precisionMixhead, the wear-prone parts in particular were designed for quick replacement.
For the first time, the mixing chamber, outlet chamber and control piston can be completely replaced when worn. The latter two are now single-piece (previously multi-piece), which in turn saves space and weight. The high availability also means that the customer ends up investing less in backup solutions. For greater ease of use, the 25-millimeter-diameter outlet pipe has been increased from a cylindrical length of 32 to 40 millimeters.
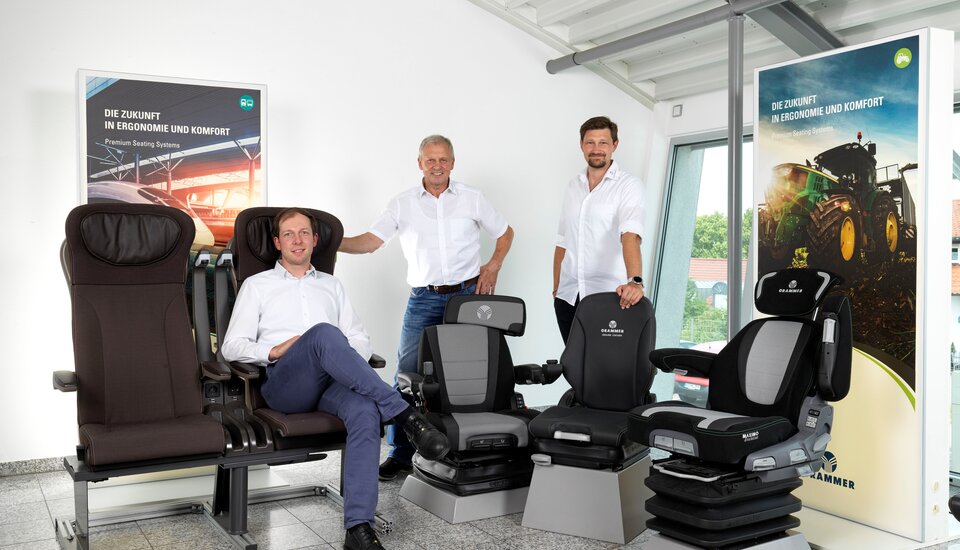
They are putting the new mixing head through its paces in series production (from left): Martin Wiendl, Head of Engineering Grammer Deutschland GmbH, Heinrich Hammer, Team Leader for Process Engineering of Foam Grammer Deutschland GmbH, Sebastian Keck, Process Engineer of Foam and Foam Mold Grammer Deutschland GmbH
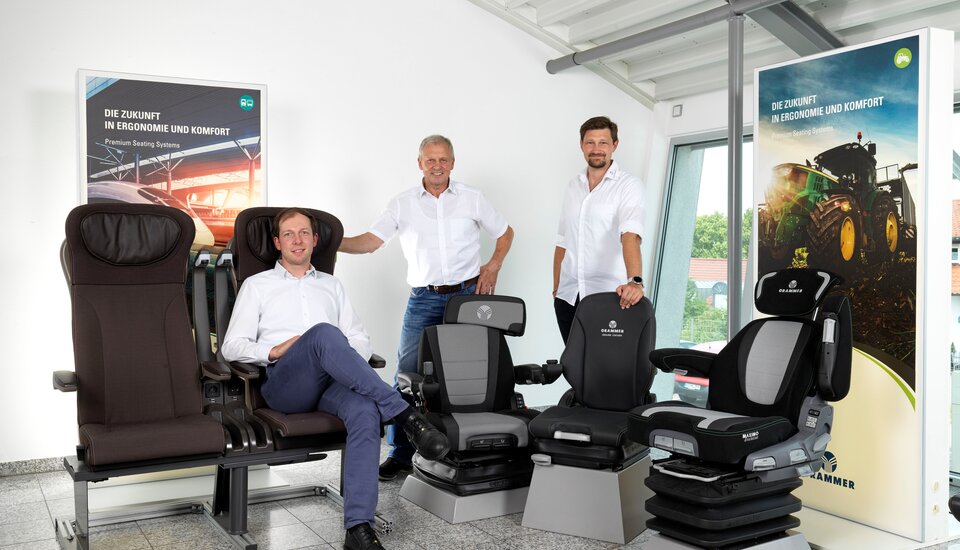
At Grammer, Sebastian Keck (Process Engineer of Foam and Foam Mold) is now very curious about the service life: "We always used to replace the previous models after about a million shots, so maybe the new one will last even longer." For Martin Wiendl (Head of Engineering), the robustness of the systems is a major benefit of KraussMaffei: "We have been operating our rotary tables since 2001, they are extremely reliable, with high system and spare parts availability, and the familiar contact partners are also always there for us."
The TechCenter even has veteran metering units from EMB that have been running since 1978 (!) and are still producing sample parts today. EMB has been part of KraussMaffei since 2002, so maintenance and spare parts supply are provided from Munich. Of course, new RimStar metering systems are now responsible for current production.
Grammer and KraussMaffei have been in a successful business partnership for about 30 years — and will certainly continue this partnership in the future. In this respect, it is only logical that the newly developed precision mixing head should undergo one of its first series applications here.
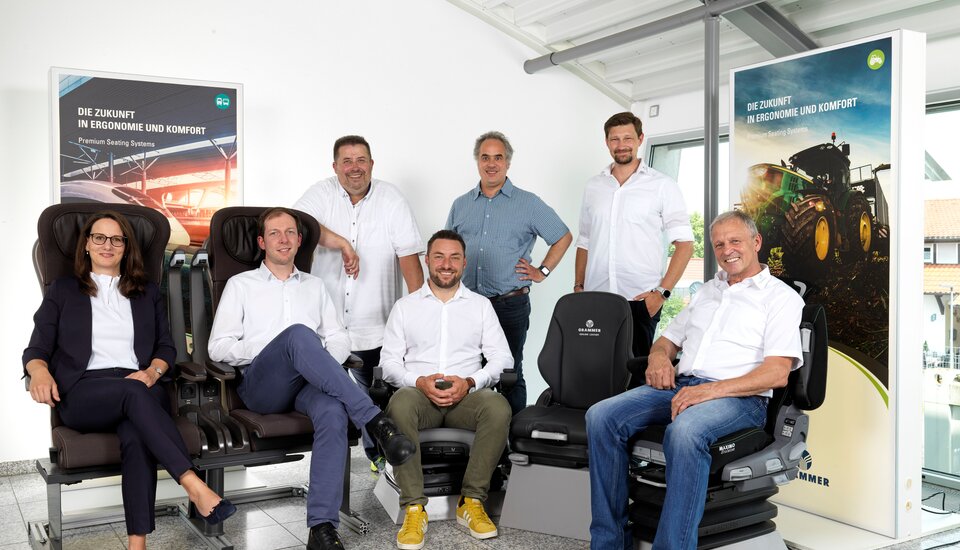
They know and appreciate each other as reliable partners (from left): Daniela Horvat, Product Manager of RPM, KraussMaffei Technologies GmbH, Martin Wiendl, Head of Engineering; Grammer Deutschland GmbH, Wolfgang Rößler, Area Sales Manager, KraussMaffei Technologies GmbH, Michael Fuchs, Global Application Owner Composite & Surface, KraussMaffei Technologies GmbH, Ralf Moser, Head of Mixing Head Development, KraussMaffei Technologies GmbH, Sebastian Keck, Process Engineer of Foam and Foam Mold, Grammer Deutschland GmbH, Heinrich Hammer, Team Leader for Process Engineering of Foam, Grammer Deutschland GmbH
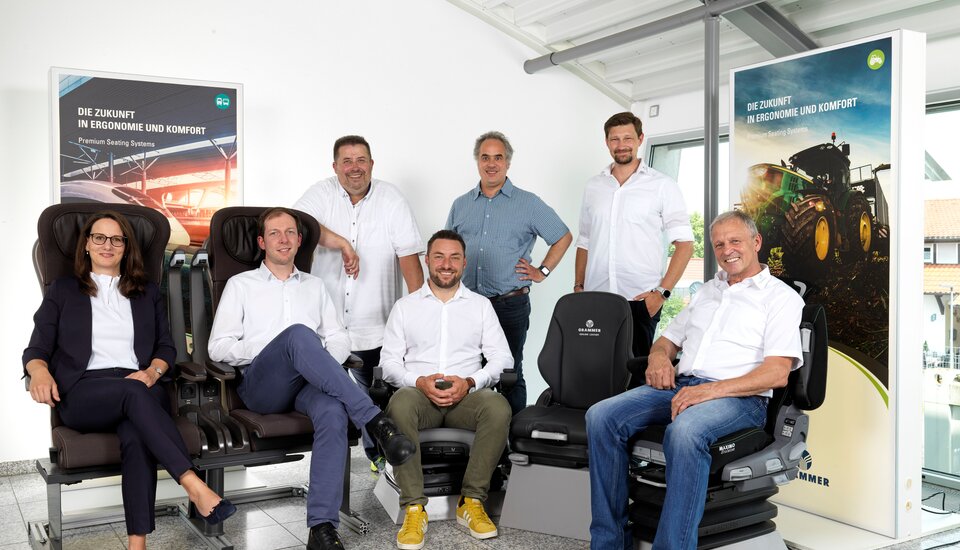
Contact
ralf.moeser@kraussmaffei.com