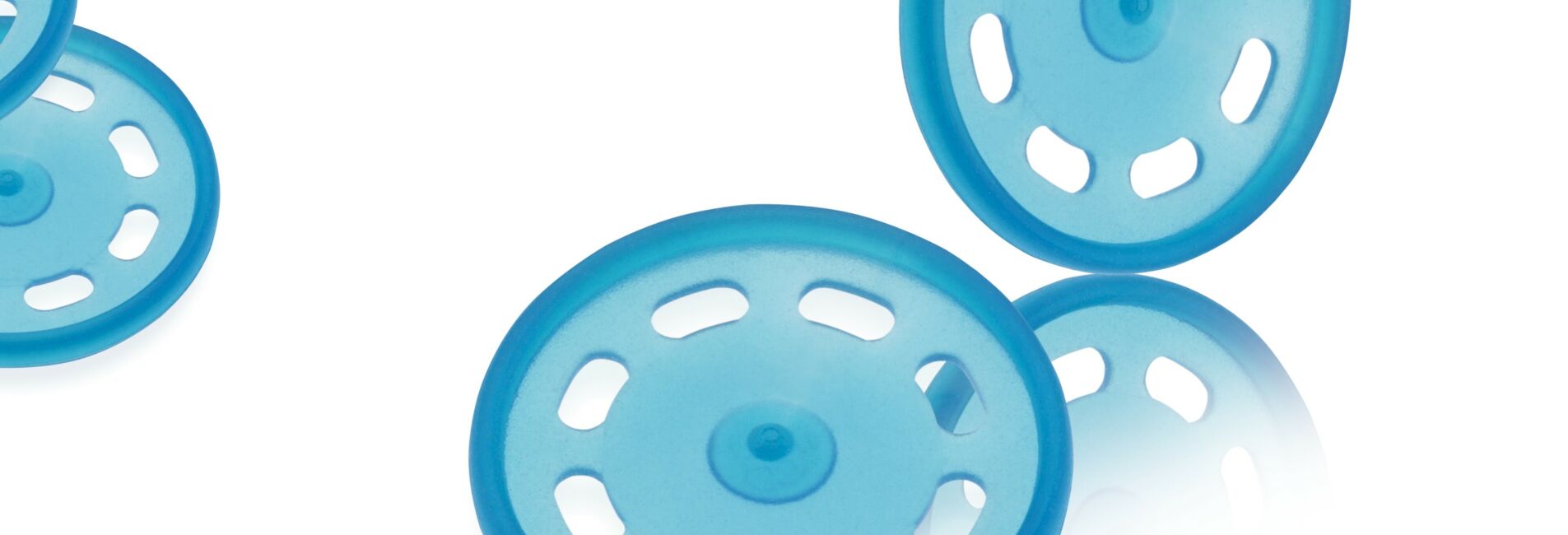
Trendgineering
Turnkey solutions for silicone processing
| Petra Rehmet
Micromembranes made of LSR – when complex handling is a challenge
Whether the application involves metering medicines accurately or separating out unwanted materials reliably, modern medicine depends heavily on reliable filter technology. Liquid silicone rubber (LSR) is particularly well suited to applications such as small medical membranes. KraussMaffei supplies complete turnkey systems for processing the high-tech material.
They are lightweight and very thin at 0.03 grams and 0.02 millimeters. Even at eight, 16 or 32 cavities, the shot weight remains minimal, which means that small, high-precision machines are necessary. The all-electric PX 25 and PX 50 injection molding machines are ideally suited for articles like these. They make it possible to create cleanroom conditions with minimum effort.
Liquid silicone rubber is an all-star
It is biocompatible and still antibacterial as well as continuously flexible yet free of plasticizers. It is rugged and heat-resistant, making it sterilizable. However, processing it differs enough from conventional thermoplastic injection molding to require either a certain amount of expertise or guidance from an experienced partner.
For example, the opposite temperature control in the plasticizing unit (cooled) and mold (hot) and the pronounced batch fluctuations that make it difficult to attain constant viscosity values and thus shot weights. Reproducible shot weights, in turn, are essential for micromembranes in order to guarantee their function. Even tiny deviations in this respect render them unusable.
Low shot weight and large plates
Using two examples, KraussMaffei demonstrates the best way to produce the miniature articles: with extremely flexible machines. A PX 50-180 SilcoSet with double adapted injection unit (screw diameter 15 mm instead of the standard 30 mm) produces membranes in a 32-cavity mold. The membranes weigh 0.03 grams and are just 0.02 millimeters thick. Therefore, this requires a low shot weight, but large platens. The PX permits the necessary enlargement of footprint while still remaining highly compact overall. The two-piece machine bed enables the customer to adapt the specific machine configuration to its project precisely. The SP180 injection unit can also supply future heavier components. It would just need a new plasticizing unit.

Micromembranes for use in medical devices:
They are produced in a 32-cavity mold
The ejector is electric and encapsulated, so it corresponds to the strict clean room requirements of medical technology. Another highlight is a servohydraulically powered injection unit for the nozzle contact force, which guarantees reliable and leak-free injection of the low-viscosity LSR material through the open cold runner. When the tiny membranes are finished, the automation gets its chance to shine.

Safe handling:
A 6-axis robot demolds all 32 microcomponents
High-end automation in the tightest of spaces
Working with great precision, a six-axis robot grips all 32 microcomponents and removes them from the mold within less than two seconds of mold opening time. This short contact period ensures process stability. A particular challenge for the KraussMaffei team was the complex demolding from the hot (190⁰ C) mold, especially in view of the requirement for a non-contact process. The footprint of the gripper is just 200 x 100 millimeters. Particular emphasis was placed on the manufacturing tolerances in order to grip all microcomponents simultaneously and with process reliability.
In almost all components, these are in the lower hundredth of a millimeter range. In addition to the gripping, the membranes are held on the gripper using a vacuum, permitting an additional query as to whether all 32 microcomponents are really in the gripper. Finely adjustable components enable the gripper to be adjusted during setup and then fixed in place. After demolding, all membranes are discharged electrically and sorted in collection tubes in cavity-separated form. The footprint of the entire automation cell is just 1,300 x 600 millimeters.
Ultra lightweight with 0.0375 grams
The second membrane project is even more challenging. In each case, a PX 25-55 CleanForm produces eight small parts weighing 0.0375 grams. Thus the total shot weight is just 0.3 grams. To make it feasible in the first place, KraussMaffei developed a screw with just 12 millimeters and partner Nexus Elastomers Systems contributed a completely new micrometering system, the ServoMix X1. These membranes have to be slit even before demolding, which is done using fine blades integrated into the gripper. The subsequent bagging within in the system is monitored using a camera system. Thanks to the modular design, it is effortless to equip this PX with cleanroom technology such as laminar flow boxes, enclosed drives, antistatic finish or FDA-compliant hydraulic fluid.

Intricate micro parts for medical technology:
Slotted micromembranes made of LSR weighing just 0.0375 g
High yield of good parts
The APC plus machine function is also recommended for silicone processing. It ensures extreme shot weight consistency and thus a high yield of good parts for the tiny parts. In a worst-case scenario, an underfilling here would actually cause the gripper to reach into a void when it is supposed to be demolding. APC plus calculates the optimal changeover point from shot to shot based on the melt viscosity and stored material parameters, such as compression. This makes it possible to compensate for batch fluctuations in the upstream silicone products, pigment additions or changes in ambient conditions.
Regardless of how lightweight and thin, whether with or without slot: Manufacturers of micromembranes can depend on KraussMaffei's PX systems.
Contact
cordula.wieland@kraussmaffei.com