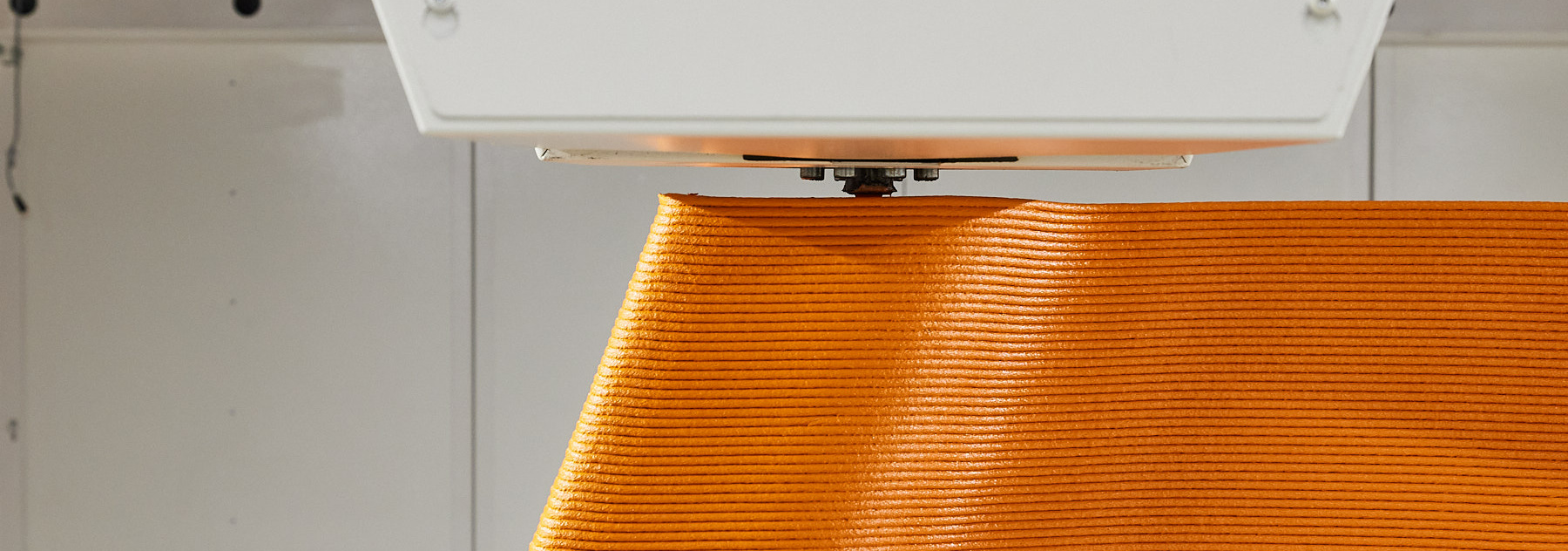
trendgineering
A look behind the scenes
| Julia Reich
From order to delivery of a finished 3D component
What actually happens in the halls of Additive Manufacturing from the moment an order is placed? How does the printing process works? And how do the AM experts get the heavy component out of the printer? We show the single steps using the example of the 3D-printed mold for a flying wing.
It all starts with a request: In this example from Deep Blue Aviation, a company for research and development of, among other things, forward-looking designs for aircraft. The company needed a vacuum infusion mold for their flying wing - in high component quality, quickly available and produced cost-effectively. No problem for the Additive Manufacturing team, as these requirements meet exactly with the advantages of 3D printed components.
With regard to the quality requirements and the necessary dimensions of the mold of 1.2 x 0.4 x 1.8 m, it quickly became apparent that the large-format powerPrint 3D printer with its space of 2 x 2.5 x 2 m is ideally suited for this component and its requirement profile. Another important aspect is the sustainability of the component. Thanks to the material flexibility of the powerPrint, a variety of sustainable granulates can additionally be processed, whereupon recycled PETG with 30% glass fiber is chosen.
Start of the printing process
After the CAD file has been successfully checked and the material supply has been ensured, the printing process can start.
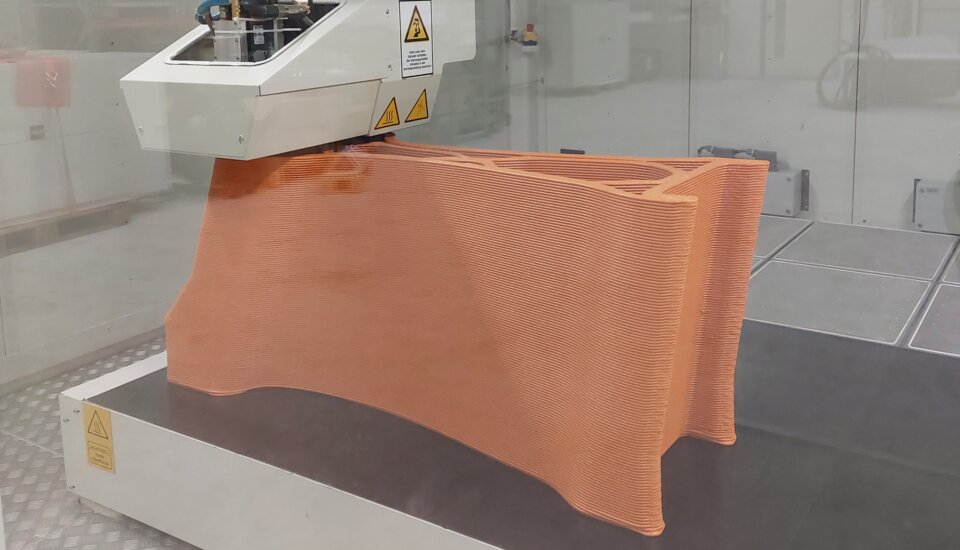
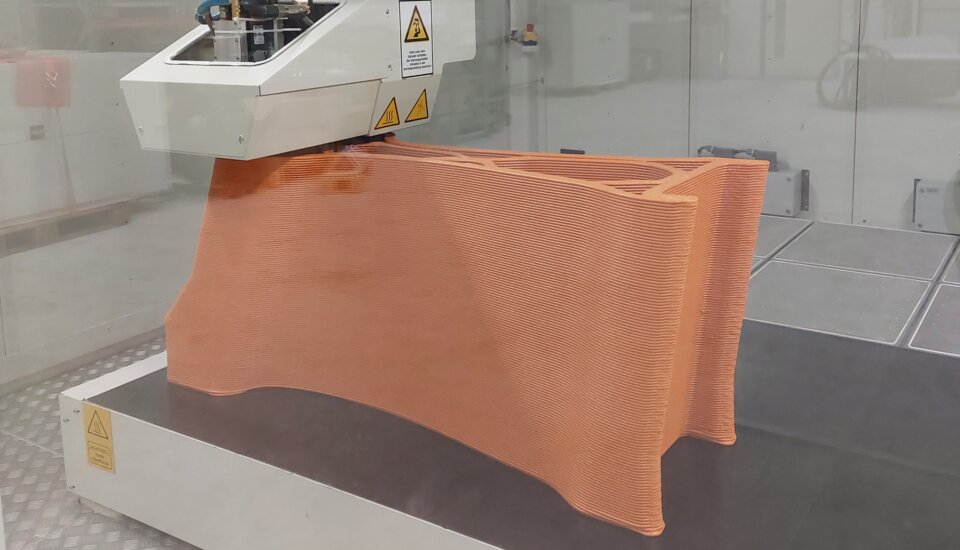
With a discharge of 10 kg/h, the powerPrint prints precisely and accurately layer by layer. Thanks to the closed, thermally insulated space, external interference is avoided and efficient thermal management is ensured, so that high component quality is always guaranteed.
Are you interested in the many other special features of the large-format 3D printer powerPrint? In our training offer you will learn everything that is important for your business.
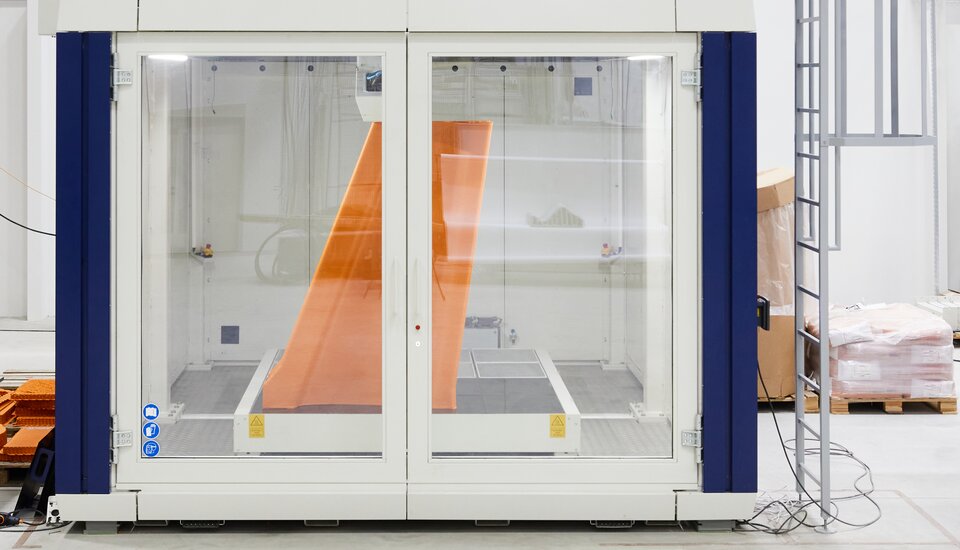
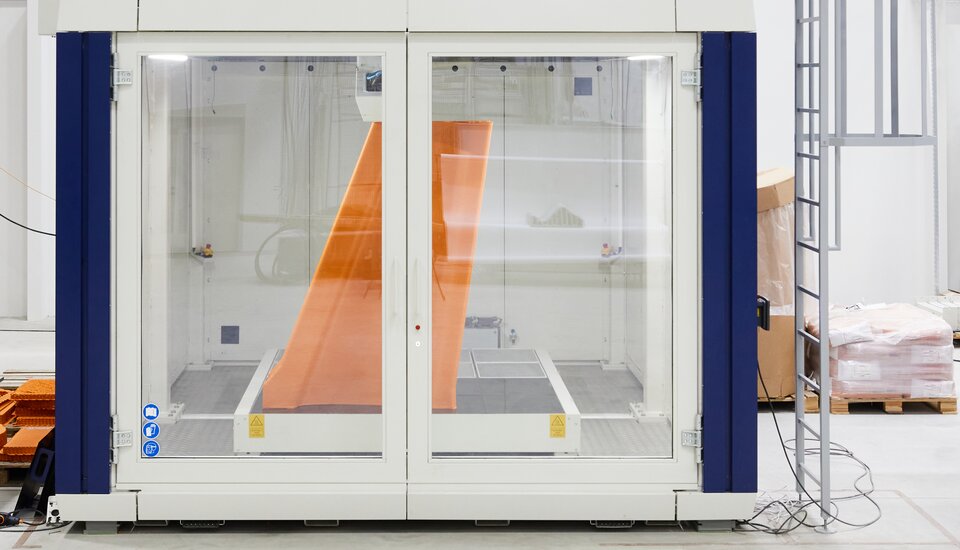
The printing process for the 3D-printed mold for the flying wing takes a total of 30 hours without any interruptions. Another advantage of the powerPrint is that, thanks to the digital RemoteAccess function, the powerPrint and the printing process can also be accessed and monitored remotely.
Completion of the component
As soon as the component is ready, it's a matter of opening the doors and retracting the ceiling! With a weight of over 300 kg, a practical solution is needed.
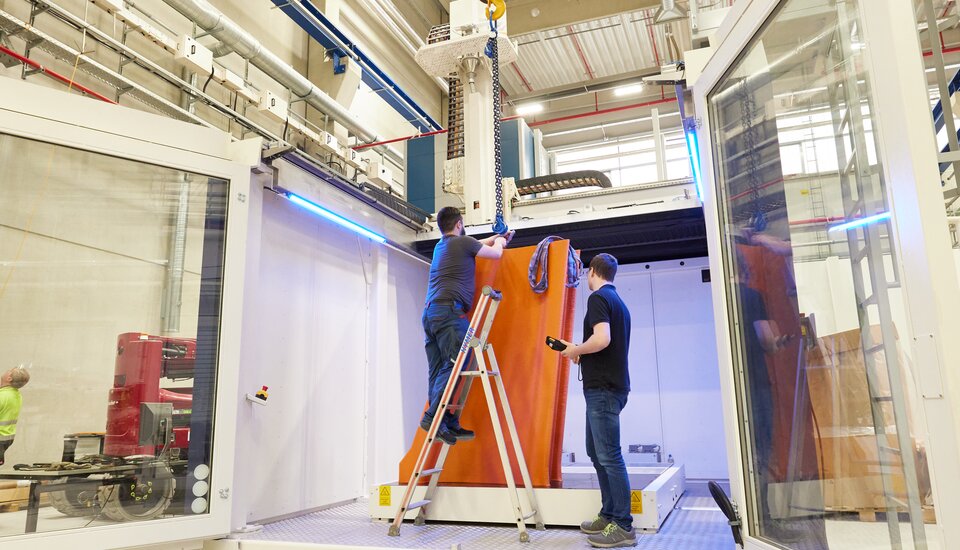
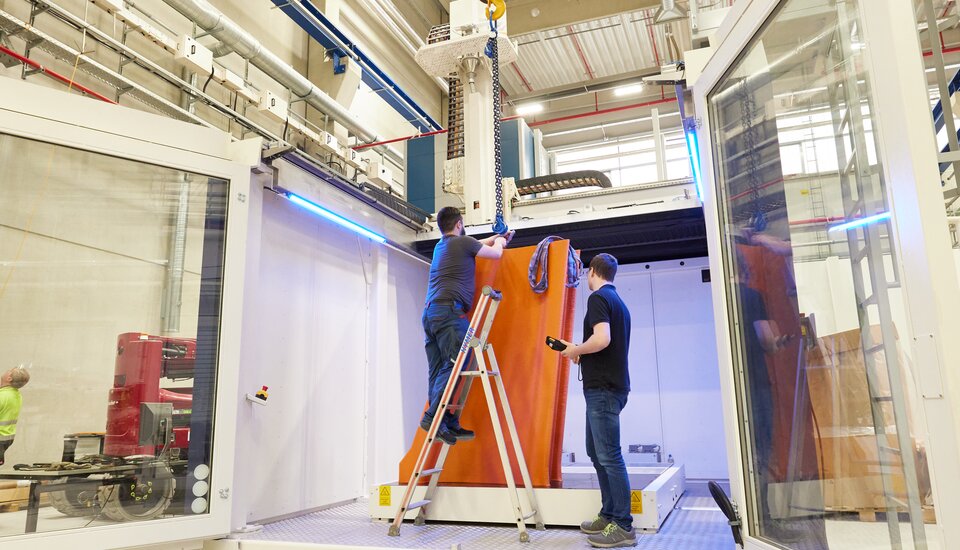
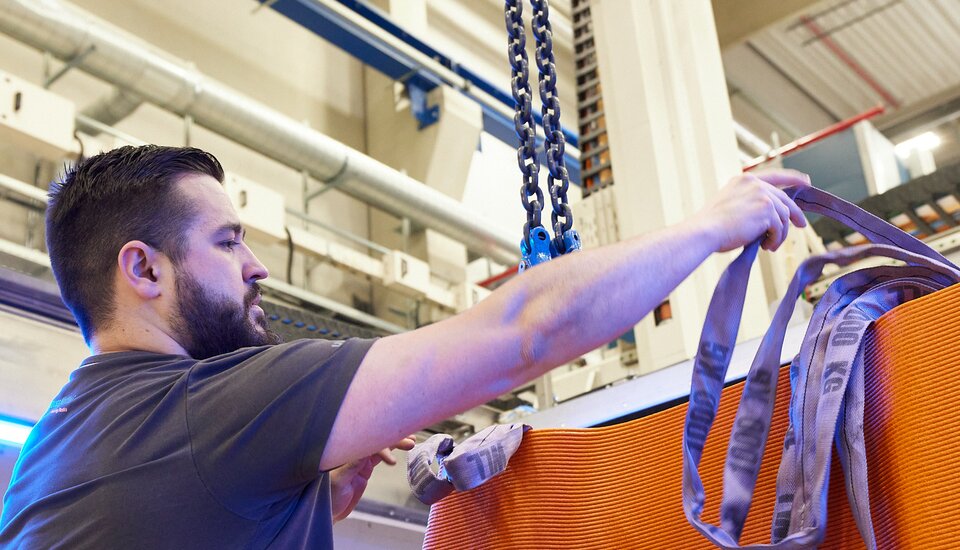
For smooth removal, stable slings are mounted in the holes provided in the component and the crane hooks are attached accordingly.
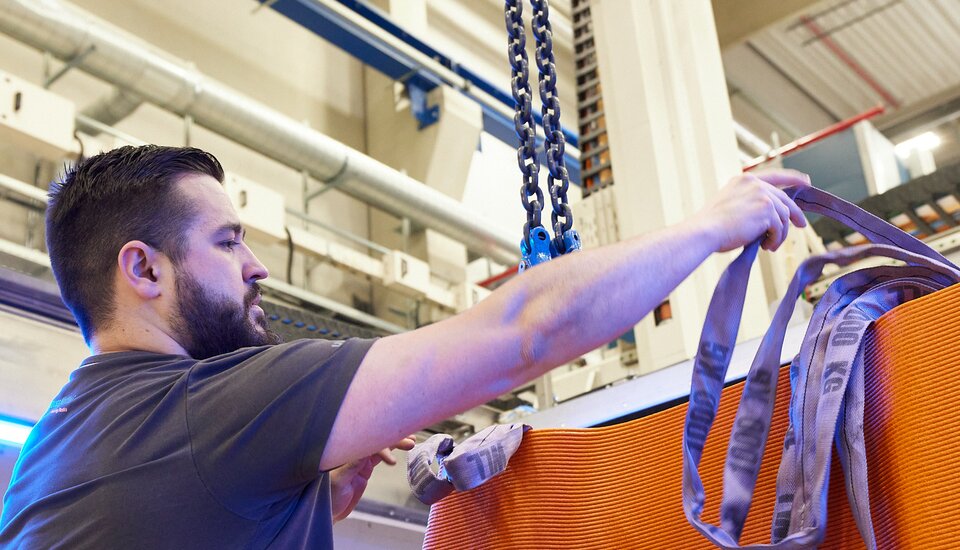
The flexible folding roof allows easy access to the component so that it can be quickly and easily removed from the space.
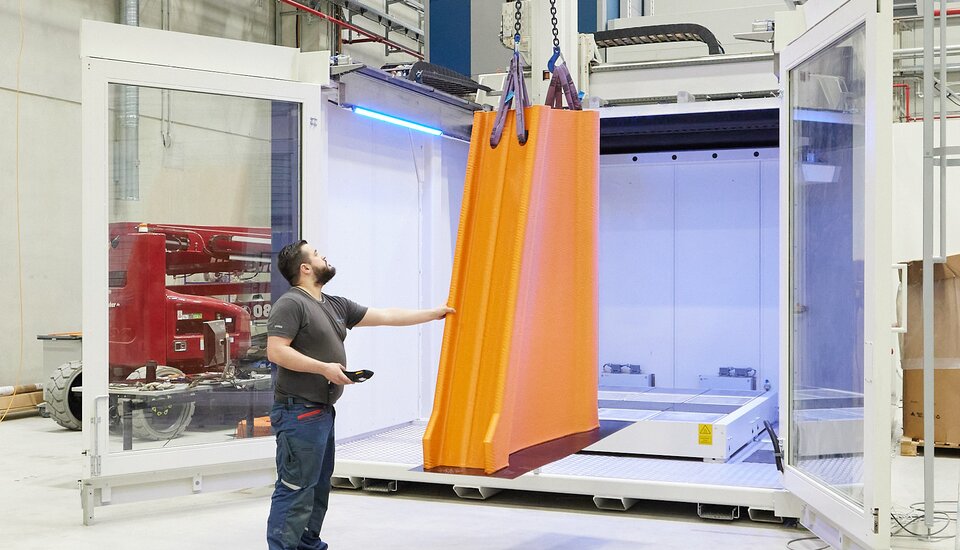
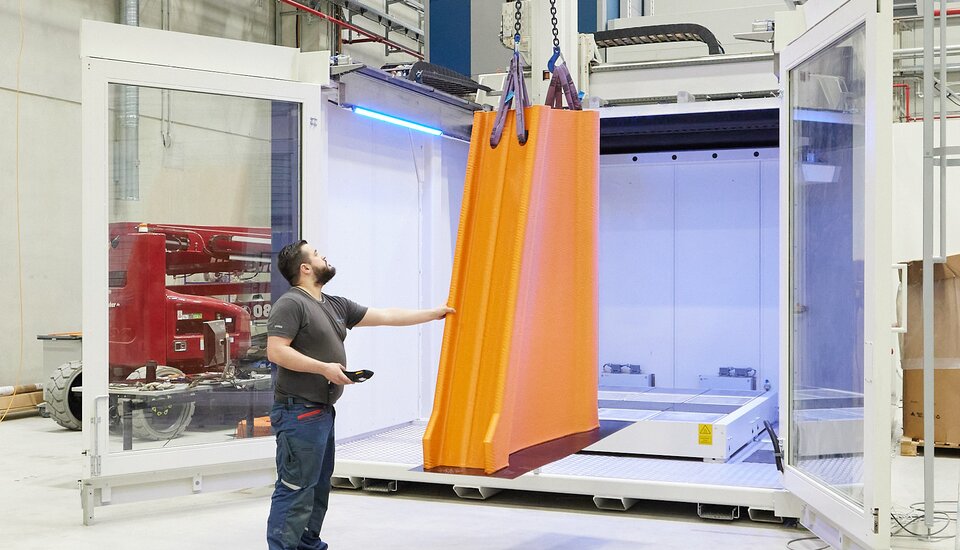
After the final milling process, the component is packed, shipped and ready for immediate use.
Does this sound interesting to you, too, and are you also considering having a large component printed for your purposes?
Put your trust in KraussMaffei's comprehensive, long-standing expertise and let our experts advise you - whether on a machine, on Print on Demand or on our range of training courses!
Contact
kristijan.mikic@kraussmaffei.com