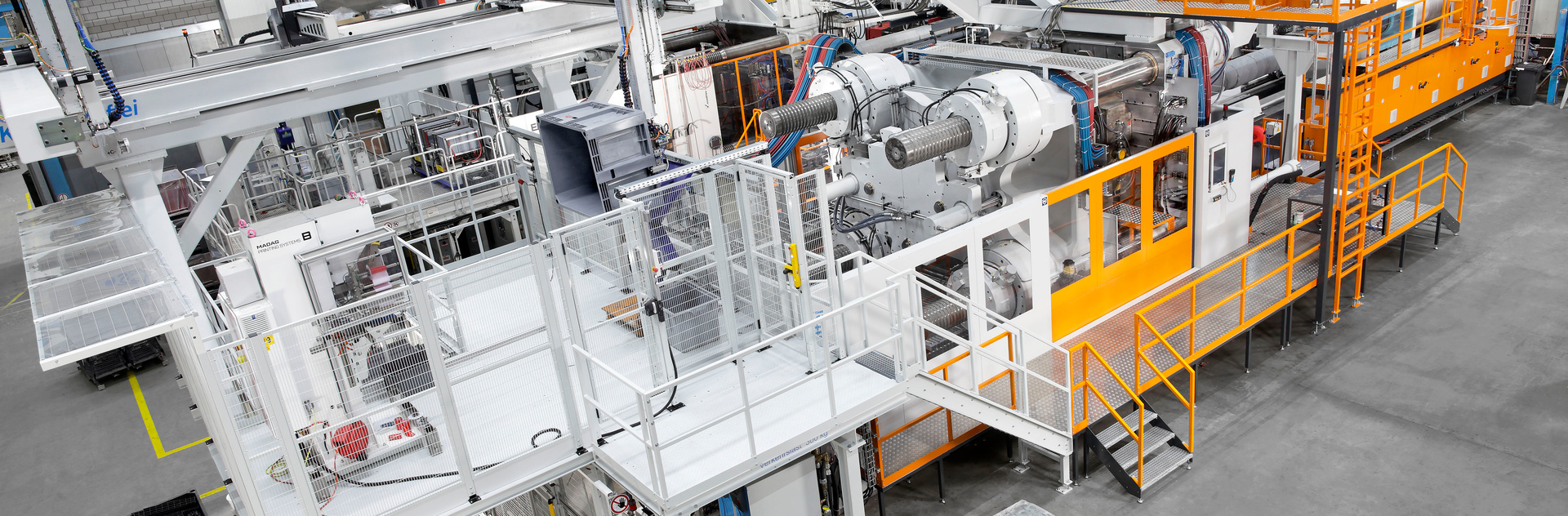
trendgineering
Largest injection molding machine in Switzerland
| Petra Rehmet
Utz, a family-owned company, commissions MX 4000
Not all packaging is equal. For state-of-the art logistics and automated production processes, boxes, pallets and Paloxes must be capable of substantially more than just holding goods. They are moved by storage robots and feature IML barcodes, integrated RFIDs and, of course, the logo of the company that owns them. Ever innovative, Utz has specialized in this application and, for this reason it has commissioned Switzerland's largest injection molding machine, a KraussMaffei MX 4000-75000.
As a global player, Utz has over 1350 employees and state-of-the-art production locations in Germany, England, France, Poland, China, the USA and Mexico. The group's origins are in Bremgarten, some 15 kilometers west of Zurich. The group operates a total of 50 injection molding machines from KraussMaffei, 22 of which are running in Switzerland at clamping forces starting at 800 kN.
In the opinion of Andreas Schlegel (Head of Operations / Managing Director), Utz combines the best attributes of many family-run companies: a flat hierarchy, good workplace atmosphere, financial independence and scope for individual creativity.
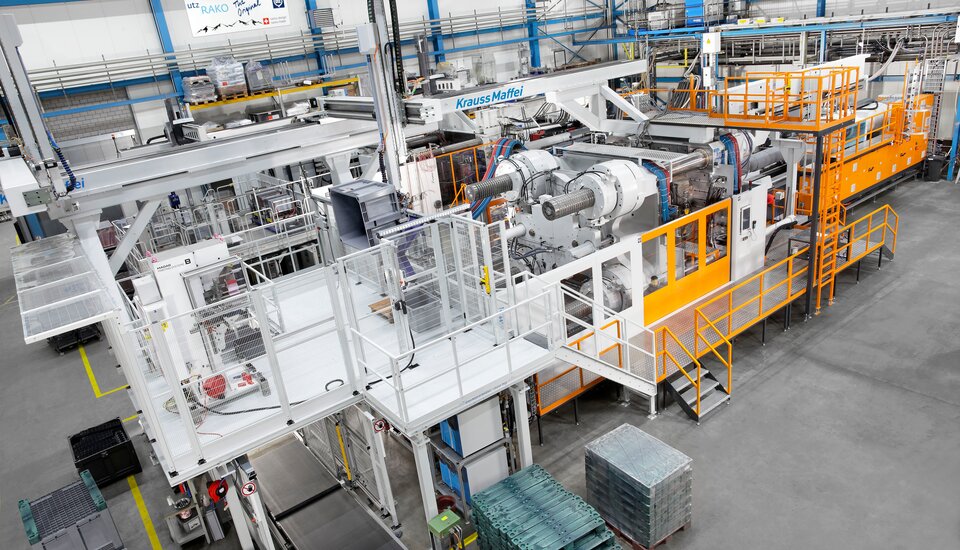
National record: with a clamping force of 40,000 kN, the KraussMaffei MX 4000-75000 is Switzerland's largest injection molding machine
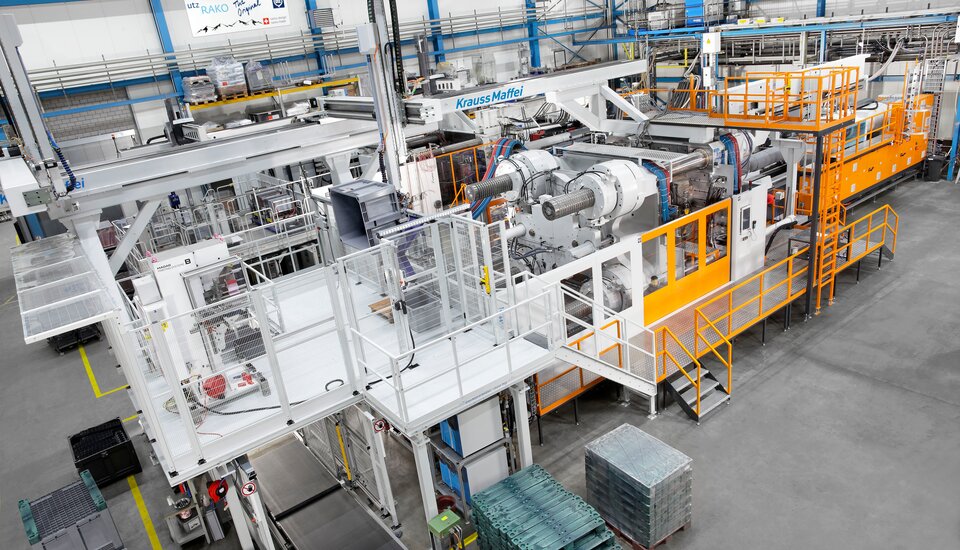
Furthermore, because the 75-year-old company is very innovative and 100 percent self-financed, major decisions are also made quickly and independently together with the group management - such as the acquisition of a new MX 4000-75000 with a clamping force of 40,000 kN.
Heavyweight commissioned on schedule
The colossal machinery traveled on a total of 22 trucks from Munich to Bremgarten: one for the machine bed, each platen, one per two tiebars and one each for many other components. Split up in this configuration, the machine crossed numerous bridges that span the area's many bodies of water and, after a twelve-week setup period, was put in to operation shortly before Christmas as the customer had requested.
Schlegel recalls this exciting time: "We have a group-wide standard for the machine specification. However, this machine size was unprecedented for us as well. Very little space was available and the equipment of the machine was expanded further by adding a few options. At the end of the process, everybody was relieved that we'd done everything correctly in the planning stage, because many interfaces have to be coordinated with each other. Including automation, the entire system is now significantly larger than before."
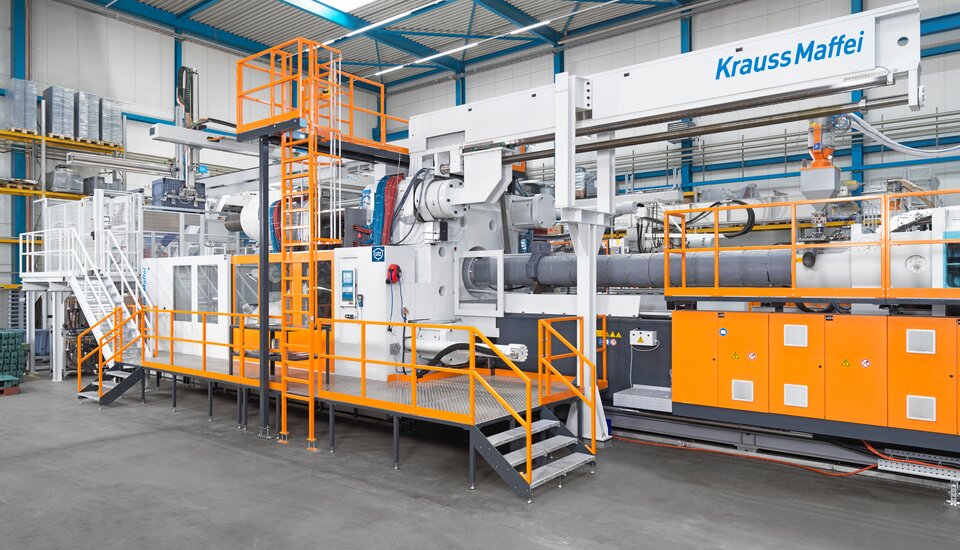
Right on schedule: After 12 weeks of set-up, the MX 4000 went online on the requested date and replaced an older machine with a clamping force of 27,000 kN that offered limited technical options and had only a simple linear robot.
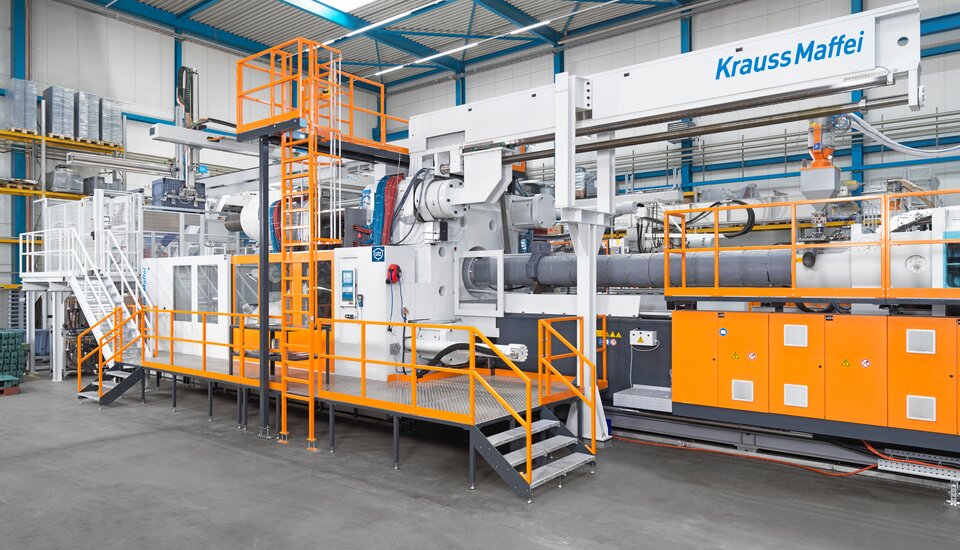
The 4000 series heavyweight replaced an older machine with a clamping force of 27,000 kN that offered few technical options, had only a simple linear robot and had fallen far behind the state of the art in terms of energy balance.
The project management at KraussMaffei (in the person of Martin Schönberger) worked highly focused to ensure that everything went smoothly. Although such large machines are pre-assembled in Munich, they are ultimately only assembled and commissioned at the construction site. As soon as even just a small part is missing, the schedule is thrown off. Since everything went off without missing a beat, the project was completed right on time.
We were very pleased about this because keeping to deadlines is not something that can be taken for granted nowadays.Andreas Schlegel
Head of Operations at Georg Utz AG, Member of the Management Board
To date, Georg Utz AG had been equipped for clamping forces up to 32,000 kN. Because some applications were already pushing the envelope, the company decided to expand its repertoire. The logistics specialist also wants to gain the ability to use additional multi-cavity and stack molds in the large product area.
Smart automation within the cycle time
Utz manufactures intelligent logistics and packaging solutions such as pallets, boxes and PALOXEs for a wide variety of industries. The higher their standards for traceability and automatic handling, the smarter the containers have to be.
Once it was enough to affix a barcode to one side, nowadays it is necessary to apply one to each side and, in many cases, to also apply RFIDs or IML barcodes. It goes without saying that the printed-on customer logo is always required. To prevent these and other downstream production steps from becoming a stressful bottleneck, the Utz and KraussMaffei team outfitted the MX 4000 with a high-end, two-level automation system that implements all process steps within the cycle time.
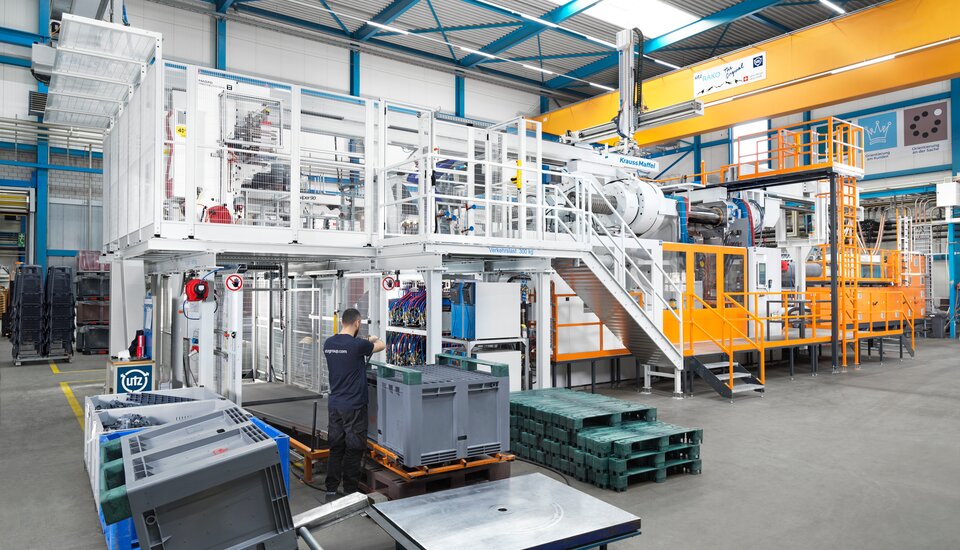
Smart automation: The sophisticated two-story automation system implements the subsequent process steps such as the application of RFIDs, IML barcodes and logos plus post-processing and partial quality control within the cycle time.
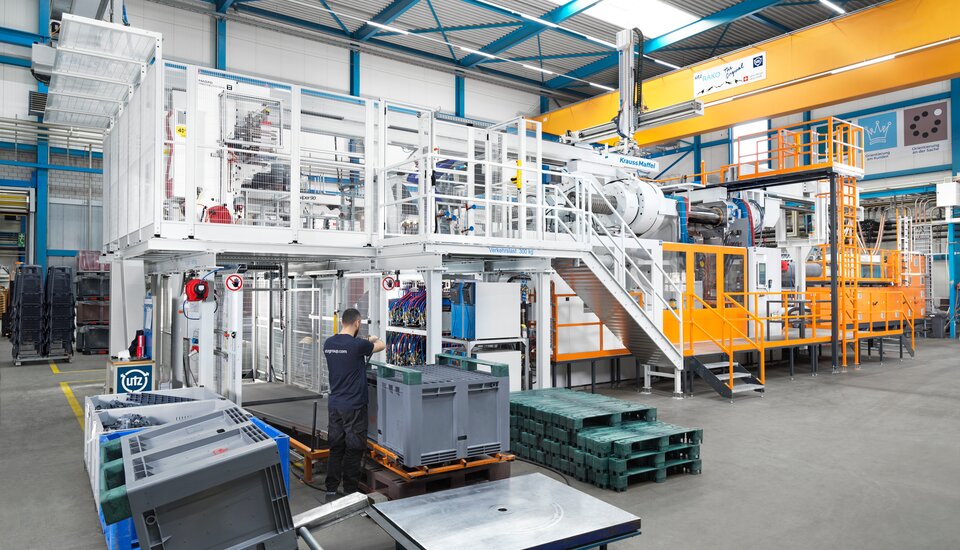
For projects like this, the Swiss-based company has a five-person automation team on site that can independently implement everything that follows the actual production cell. The LRX TwinZ with two robots right at the machine are from KraussMaffei and, with a twelve-meter-long Z-axis, have a particularly large working radius. To move projects and tools to other locations easily, the Utz team has developed a standard layout for each tonnage that covers the most important components.
Increasing percentage of recycled material
In Switzerland, around 20 different products with weights of up to 50 kilograms are produced on the new MX 4000 in three-shift operation. The material is usually a polyolefin such as PP or HDPE, but ABS or technical plastics are also sometimes used.
The percentage of recycled material is currently 35 percent and Utz operates its own recycling sites for this purpose, for example a mill in Bremgarten with a throughput of around 1.2 tons per hour. Here, in addition to internal production rejects, for example from color changes, products are also ground up that come back from the customer after the end of their life cycle. The company also purchases premium quality post-industrial and post-consumer waste, with the latter usually being prepared and compounded.
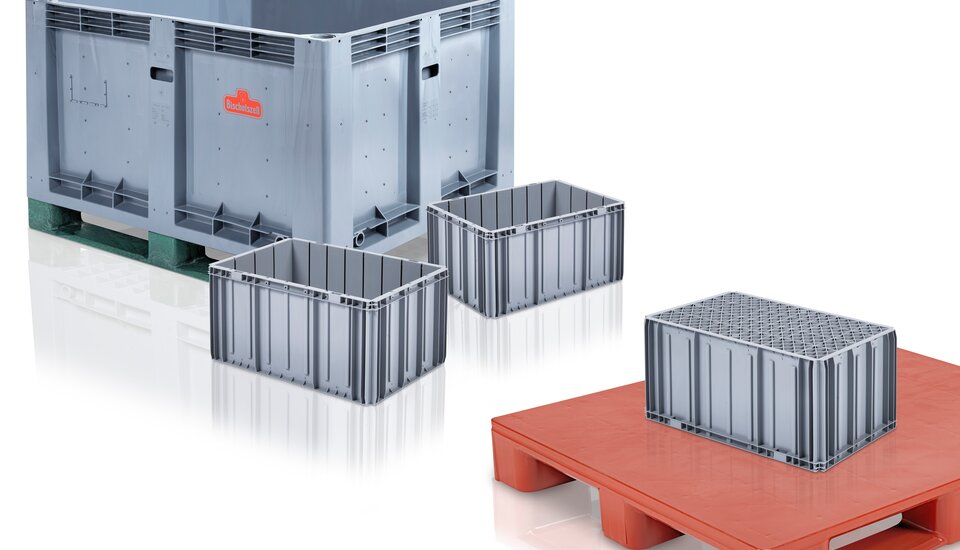
Loaded with extras: Today's pallets, boxes and PALOXEs manufactured on the MX 4000 have to do more than hold goods. They are moved by storage robots and feature IML barcodes, integrated RFIDs and, of course, the logo of the company that owns them.
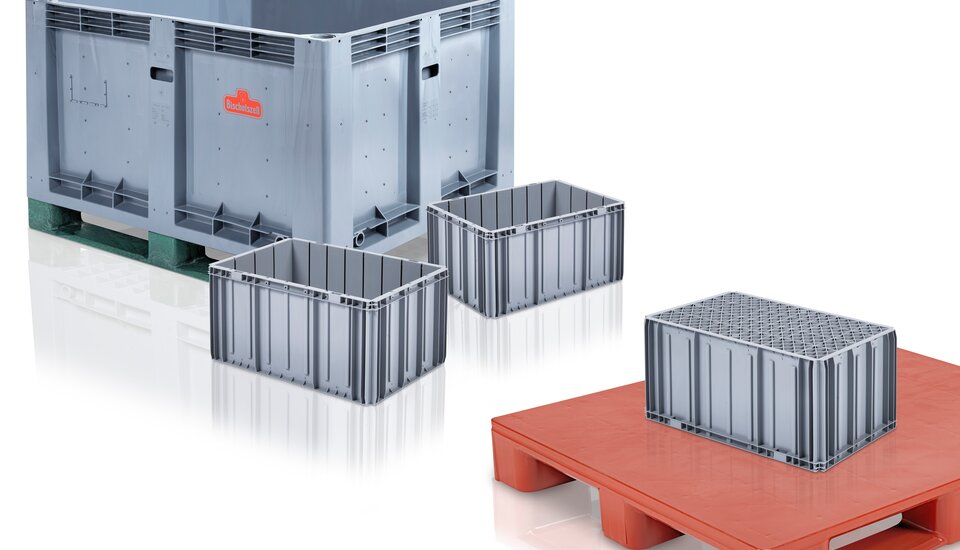
In the long term, plans call for the percentage of recycled material to increase to 80 percent in line with the group wide climate strategy. This is where one function of KraussMaffei machines plays a special role: APCplus. Based on the melt viscosity, APCplus controls the changeover point and the holding pressure level and thus ensures parts with consistent weight. This balances out batch fluctuations that result from different raw materials and percentages of recycled material.
For Utz, the important factor is that this opens up a wider gateway for material purchasing. In the case of regrind, for example, it is also possible to buy different quality grades or polyolefin blends that are more readily available. APCplus has been used on the smaller machines for two years, and in this time, scrap has decreased significantly. Therefore, the new MX is likewise equipped with these features.
Digital research project with the Eastern Switzerland University of Applied Sciences
Utz is currently using another of KraussMaffei's digital products to develop a predictive quality solution in collaboration with the Institute for Materials Technology and Plastics Processing (IWK) of the Eastern Switzerland University of Applied Sciences. The DataXplorer can save up to 500 signals per second from the machine and other sensors and display them as curves. The goal now is to determine how many of these are needed in order to predict good components reliably.
Also in use is the proven Orca temperature control system, which uses sound waves to measure the flow rate—just as orca whales do for orientation. Orca monitors and regulates all 120 cooling circuits of the MX 4000 and thus ensures optimal heat exchange with stable process control. The result is significant energy savings.
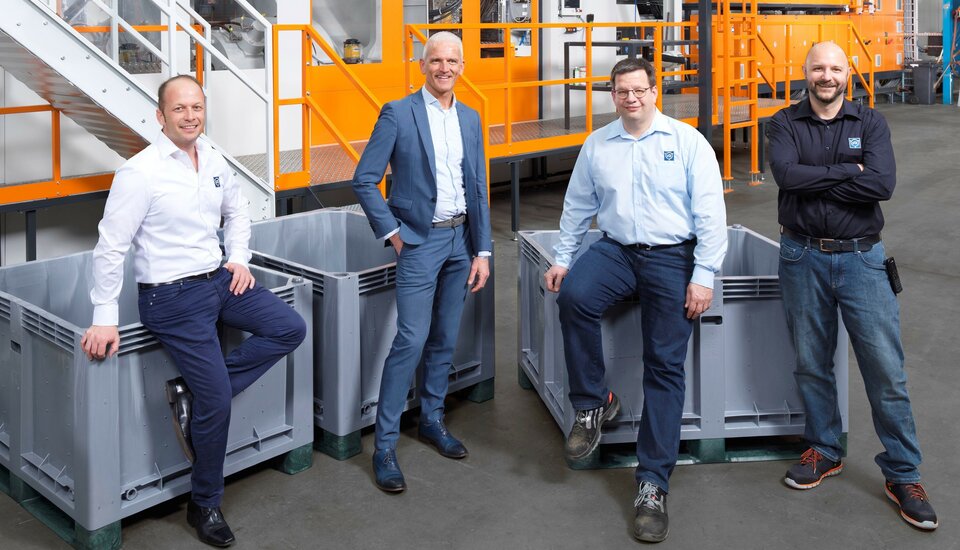
Appreciate the trusting cooperation (from left):
Andreas Schlegel (Head of Operations Georg Utz AG, Member of the Management Board), Bruno Schleiß (Managing Director Krauss-Maffei (Schweiz) AG), Marcel Meier (Head of Production Engineering Georg Utz AG) and Markus Eggimann (Head of Production Georg Utz AG).
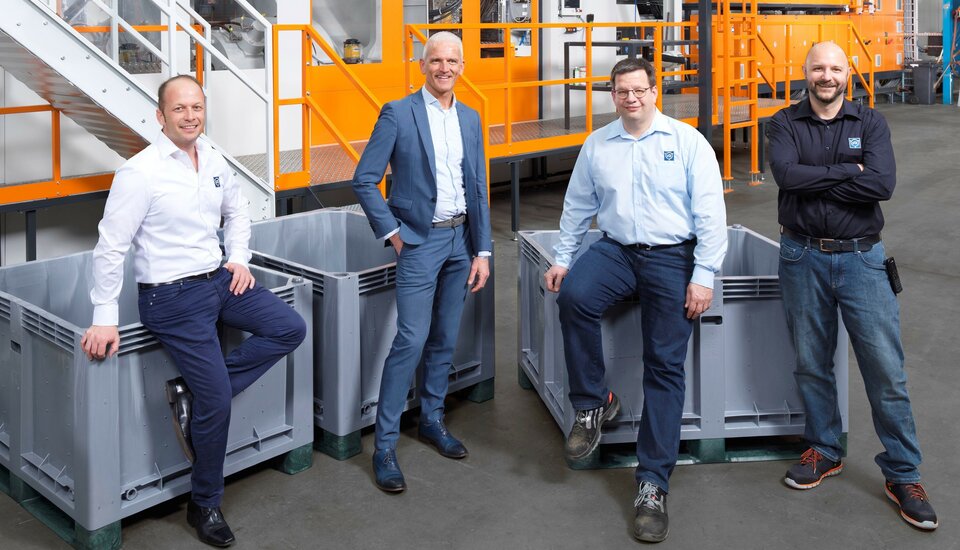
When KraussMaffei's Orca was introduced at Utz a few years ago - as the first system in Switzerland - it became clear that the partners could rely on each other. When things got rocky at the beginning, the proactive collaboration of both companies and teams helped to set up the temperature control solution in the best possible way. The mutual respect and admiration have remained.
Excellent service
This plays an important role in new investments. Surely, much of the credit goes to Bruno Schleiß, the longtime Managing Director of Krauss-Maffei (Schweiz) AG, and his team.
We scrutinize machine suppliers with regard to the technical standard, service quality and price. It's important to us that the machine consistently runs well and that help comes quickly if we do have any problems. We are very satisfied with KraussMaffei in this regard.Andreas Schlegel
Head of Operations at Georg Utz AG, Member of the Management Board
The outcome will surely be renewed conversations surrounding future additions to the machine park at Utz Group, while at Georg Utz AG in Bremgarten, the focus is on process optimizations and investments in replacements. They are also necessary to cope with general challenges, such as rising energy costs and high volatility in material prices. The megatrend of the circular economy is an additional area of focus.
With an export share of around 40 percent, Utz Switzerland delivers its products primarily to Italy, Austria, Eastern Europe, the Scandinavian countries and Oceania. The next goal is increasing Group sales from the current level of 350 million francs to 400 million. There's a lot more to do for the dream team of Utz and KraussMaffei.
Contact
bruno.schleiss@kraussmaffei.com