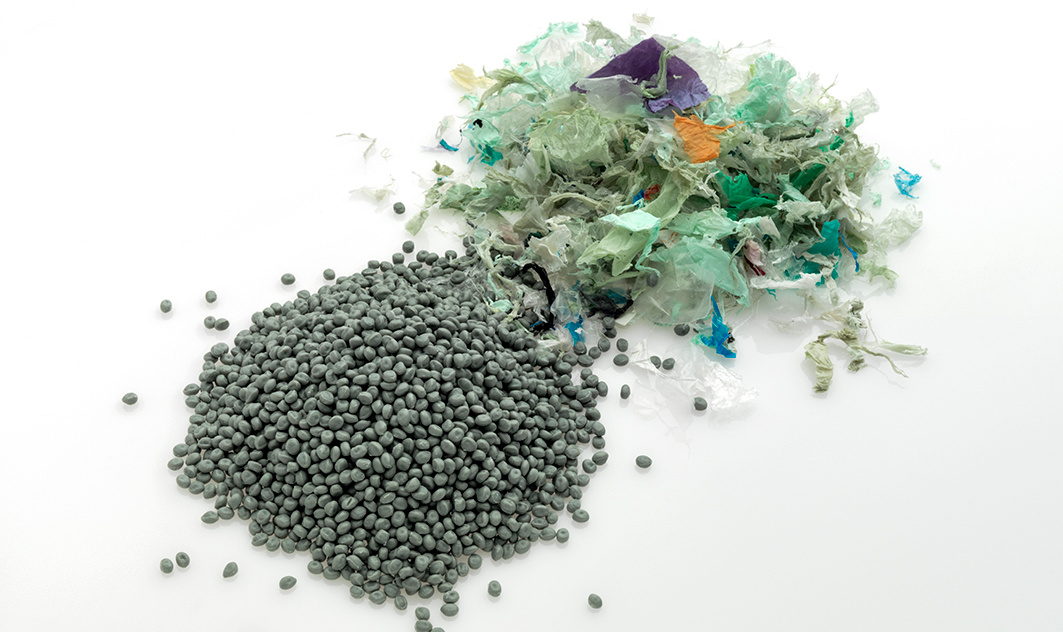
sustainability
Reducing CO2 emissions twice over
| Hannah Bösselmann
Thermoplastic foam injection molding with post-consumer recyclate
Foam injection molding inherently saves material. And it gets even better: How about using post-consumer recyclate instead of virgin material in the process to reduce the CO2 footprint even further? In collaboration with the Schmalkalden University of Applied Sciences, KraussMaffei has investigated this question, with particular focus on what this means for the mechanical component properties.
Analyses by KraussMaffei and the Schmalkalden University of Applied Sciences show the effects that result when thermoplastic foam injection molding, specifically the MuCell process, is combined with the use of post-consumer recyclate (PCR).
The test arrangement combined requirements of the highest difficulty because the foamed component was to weigh up to 12% less than the compact one and be made from 100% recycled granules. This comes from processed post-consumer waste (PCR) and is therefore significantly more contaminated and less homogeneous in terms of material characteristics than single-variety recyclates from industrial waste (PIR).
Do the negative influences add up?
Recycled material from post-consumer waste has often undergone a stressful reprocessing process in which it was melted in an extruder; in the process, the plastic is always negatively affected by shear forces and thermal stress. For the use of such recycled material in the MuCell process, it was therefore necessary to clarify whether the two effects add up. In addition, the electrical properties were to be analyzed in cooperation with an industrial partner.
Determination of tensile properties, flexural strength and impact strength
All three analyses (tensile properties, flexural properties and impact strength) showed that the MuCell process does not affect post-consumer recyclates more than virgin material. The original fear that both factors would possibly cumulate and that the mechanical properties would thus deteriorate exponentially has not been confirmed. What also had no effect was loading the melt with 50% more propellant than necessary. Here we wanted to go to the limit, but the process window was not restricted by this either. This means that there is neither an oversized drop in the mechanical properties, nor a limitation of the process control.
Study of the electrical properties
As previously explained, the electrical properties of the test specimens were also investigated—in the form of creepage resistance (CTI) and surface resistance. No difference between virgin or recycled material and compact and foamed components could be demonstrated.
Conclusion
What is the bottom line for the combination of the MuCell process and post-consumer recyclate? As always, the application decides. Because the mechanical properties of PCR-Compounds are usually poorer, the customer's strength specifications are the most important criterion for the respective project. Together with foam suitable article design, there are definitely opportunities to use recyclates in a targeted and sensible manner in physical foam injection molding in order to reduce the CO2 footprint of components twice over. KraussMaffei can provide you with expert advice here on which path would make the most sense for you and your requirements.
For the exact test parameters, results and when making the switch is worthwhile, refer to the technical article here in the September issue of Kunststoffe.
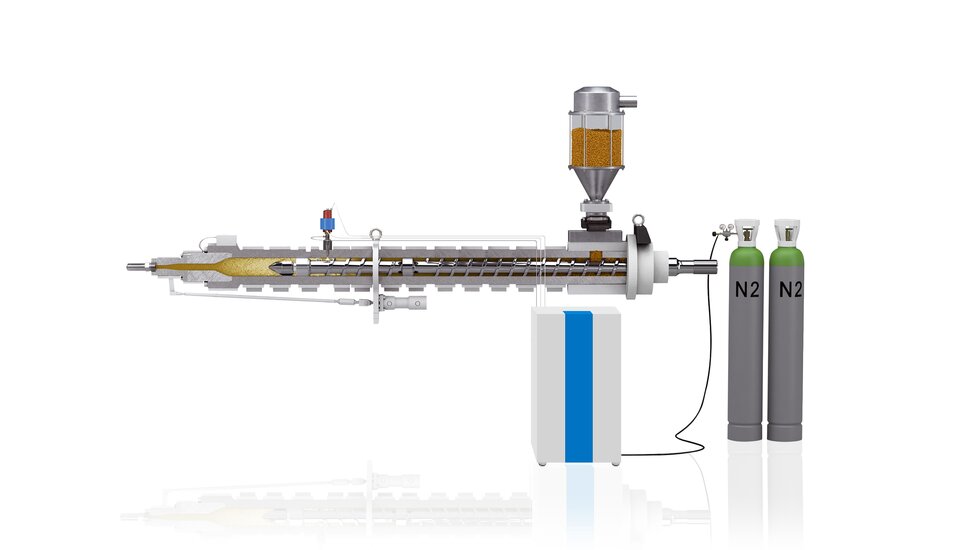
Double benefit: Reduce component weight and process recyclate with the MuCell process.
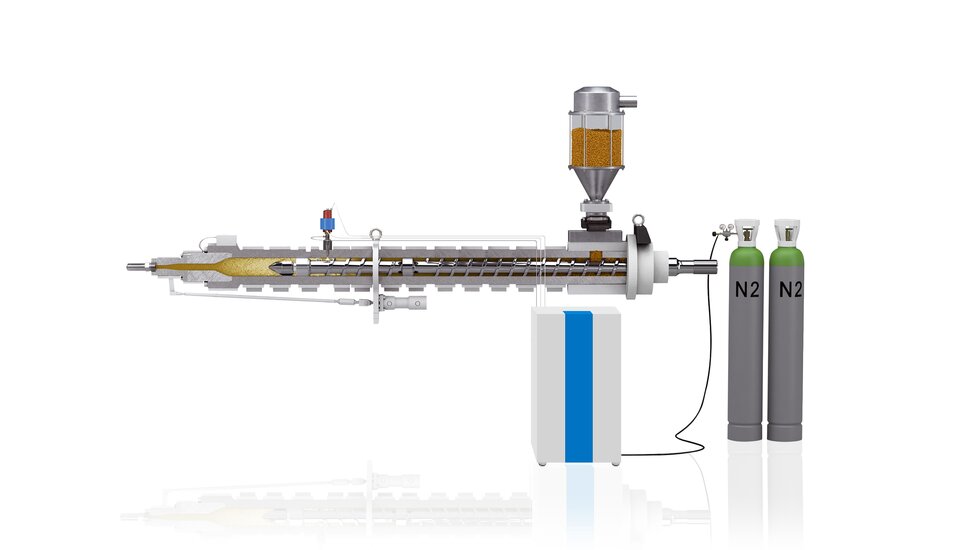
Contact
andreas.handschke@kraussmaffei.com