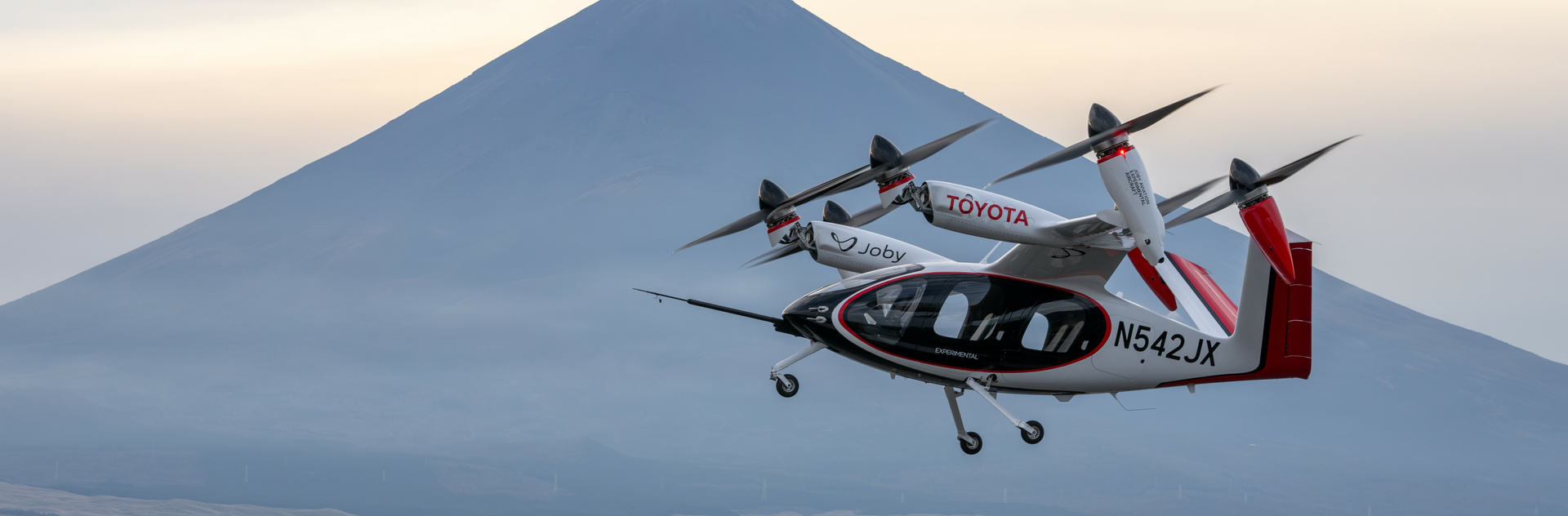
sustainability
Revolutionizing air mobility
| Petra Rehmet
FiberForm speeds up eVTOL production in record time
Together with the renowned National Institute for Aviation Research (NIAR) at Wichita State University, KraussMaffei is driving the advancement of thermoplastic lightweight solutions in the aerospace industry. At the heart of this collaboration is a newly developed structural component with a complex rib structure —designed specifically for eVTOL aircraft, which are capable of vertical take-off and landing.
It is manufactured using KraussMaffei's proven FiberForm process — and in record time: Instead of taking more than 100 hours as with the metal version, the production now takes only around two minutes, while maintaining the same strength and safety.
In the FiberForm process, thermoplastically impregnated continuous fibers (organo sheets) are placed into the mold, formed, and then overmolded.
This combination of thermoforming and overmolding is fully automated and offers numerous advantages: significantly lower weight, substantial time and cost savings, and greater design freedom without compromising mechanical performance.
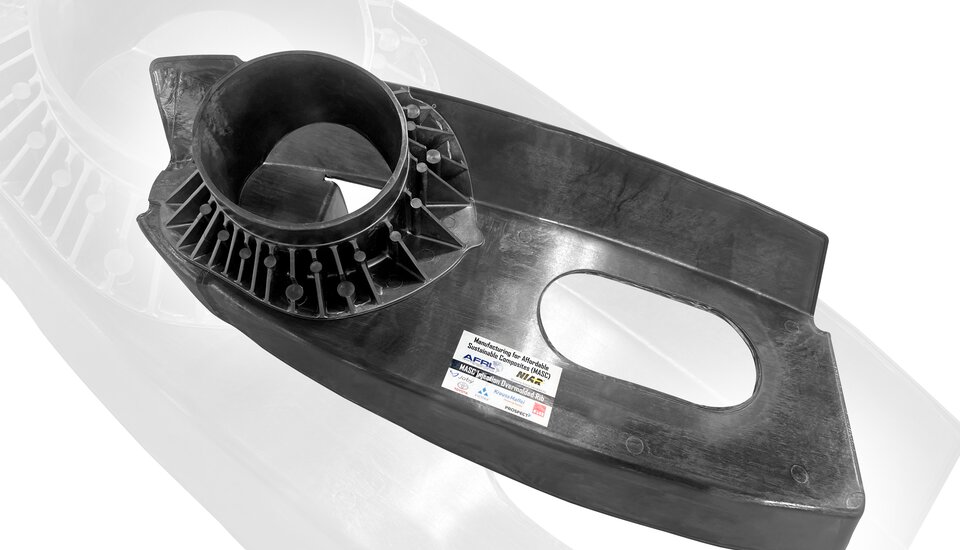
Less weight, more efficiency: The FiberForm-manufactured structural component with a highly complex rib structure
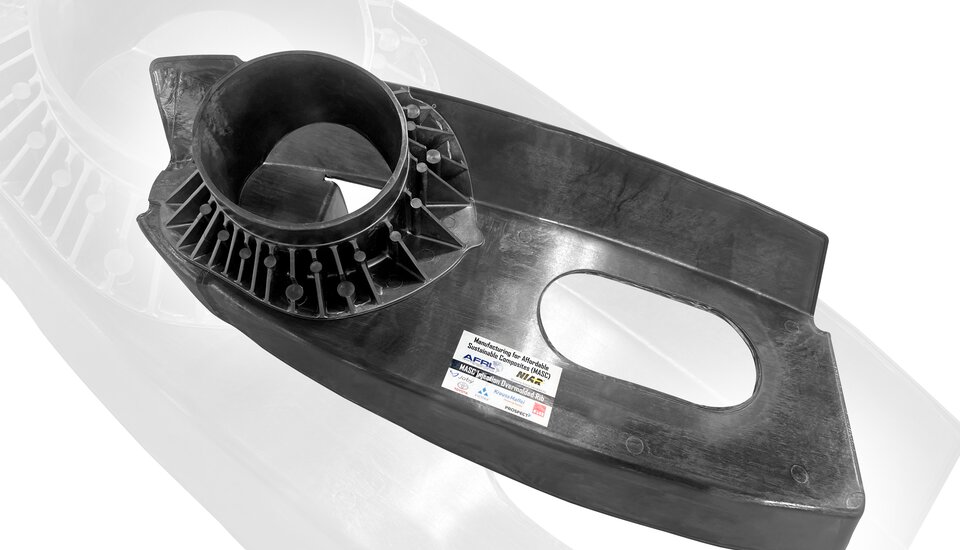
Production in just 2 minutes instead of 100 hours
The new rib structure is manufactured at the NIAR Advanced Technologies Lab for Aerospace Systems (ATLAS) on a KraussMaffei GXW 450-2000/1400 with 4,500 kN clamping force, a rotary unit, and robot-based automation.
Particularly impressive: while conventional metal rib structures are milled - with high material waste and enormous time consumption - the thermoplastic version is completed in just two minutes.
The proven expertise of all project partners was key to achieving this milestone.Dr. Waruna Seneviratne
Director NIAR ATLAS
In addition to KraussMaffei, Joby Aviation, Toyota, Victrex, and Prospect were involved. The project is part of the U.S. Air Force Research Laboratory's funding program "Manufacturing for Affordable Sustainable Composites."
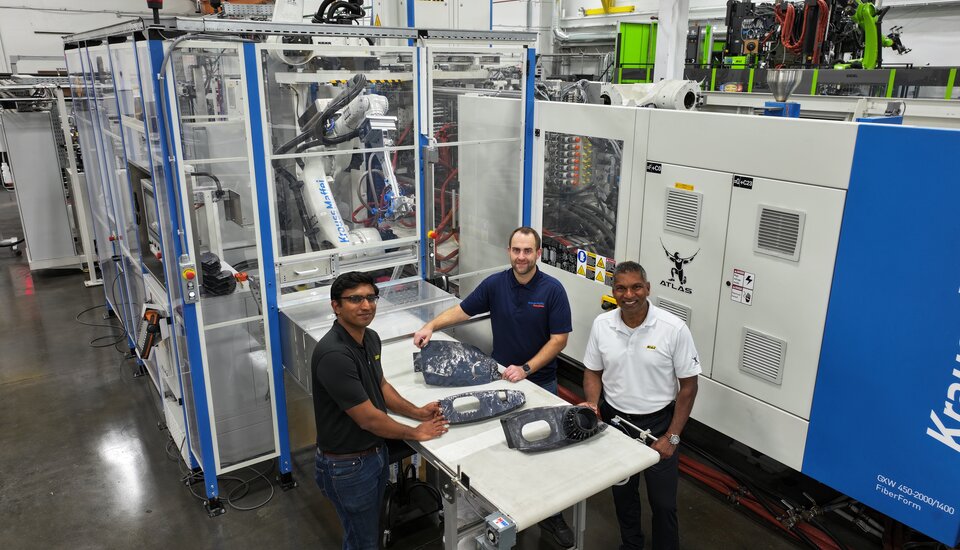
Driving the advancement of thermoplastic lightweight construction in aerospace: Induwara Herath (Research Engineer, NIAR ATLAS)Eugen Schubert (Sales and Applications Manager, IMM & Automation at KraussMaffei), and Dr. Waruna Seneviratne (Director, NIAR ATLAS) in front of the GXW 450 FiberForm at the NIAR ATLAS lab (from left).
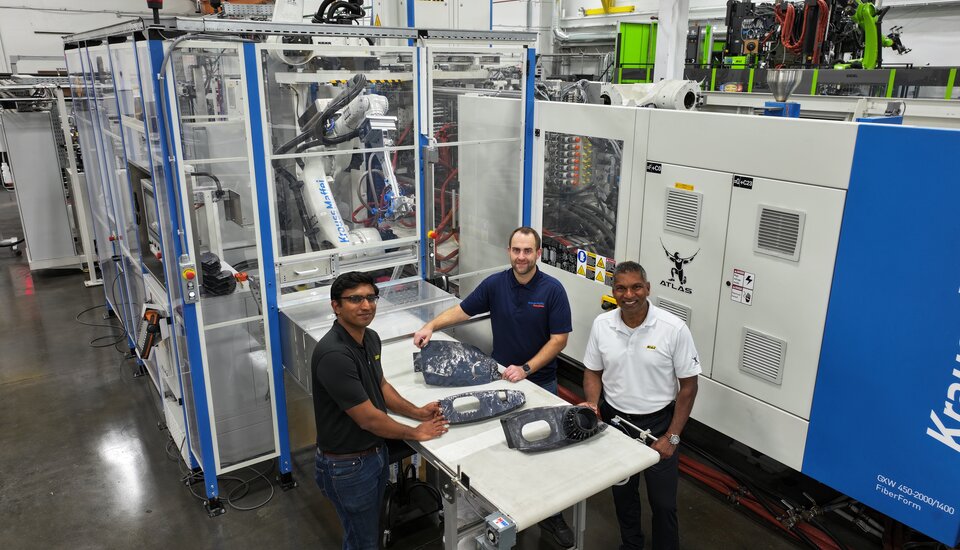
Proven technology from automotive mass production – now in aerospace
The results highlight the potential of the FiberForm technology, already established in the automotive industry, for aerospace applications.Dr. Waruna Seneviratne
Director NIAR ATLAS
Eugen Schubert, Sales and Applications Manager at KraussMaffei, also sees strong potential: "The NIAR ATLAS lab is an ideal platform for bringing new technologies to series production in collaboration with material and tooling partners."
KraussMaffei and NIAR already successfully collaborated in 2024 on the development of window latches for so-called 'Prachters'—converted cargo aircraft.
FiberForm once again impressed with short cycle times and significantly reduced component weight.
With this new rib structure, the partners are now impressively demonstrating how sophisticated aerospace components can be manufactured efficiently and economically using the FiberForm process, paving the way for further applications and future certification.