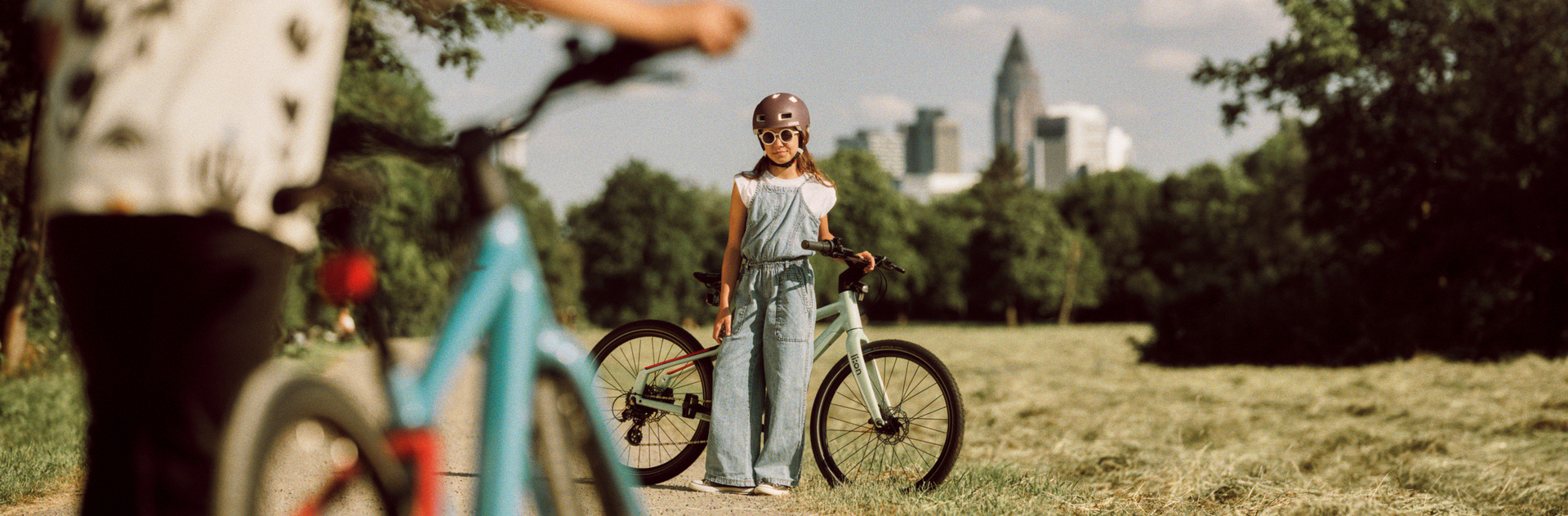
sustainability
The ultimate children's bike
| Petra Rehmet
Stylish, safe and sustainably produced
The new Lion Bike by Marcel Kittel and Tony Martin, both former professional cyclists, stands for an extraordinary bike series that makes kids even more visible on their bikes and ensures more sustainability in manufacturing. The frame and fork are made of a high-performance polymer with recycled carbon fibers. They are produced by specialist Weber Fibertech on an MX 1600 from KraussMaffei.
It started with a quest for a bike suitable for children - featuring maximum safety, sustainably produced, with a super-stylish look. Sounds simple, but none of the current children's bikes could meet the standards of the three proud fathers. So the two professional cyclists, along with co-founder Franz Blechschmidt, set out to set these new standards themselves with a childlike spirit of inquiry and a mentality that led to serial victories in the Tour de France and world championships. The result is the most visible and therefore safest children's and teen bike.
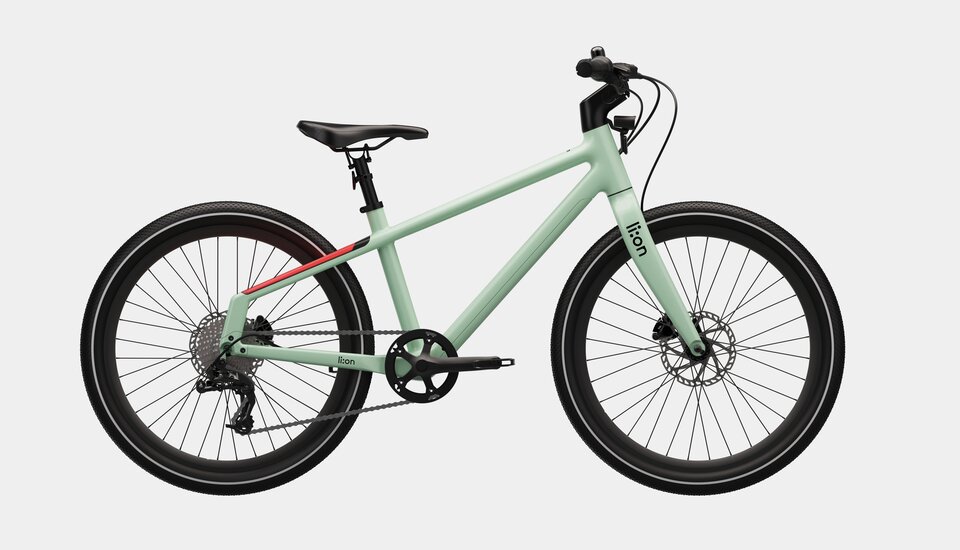
Cool and sustainable: The new Lion Bikes for kids with frame and fork made of high-performance polymers and recycled carbon fibers.
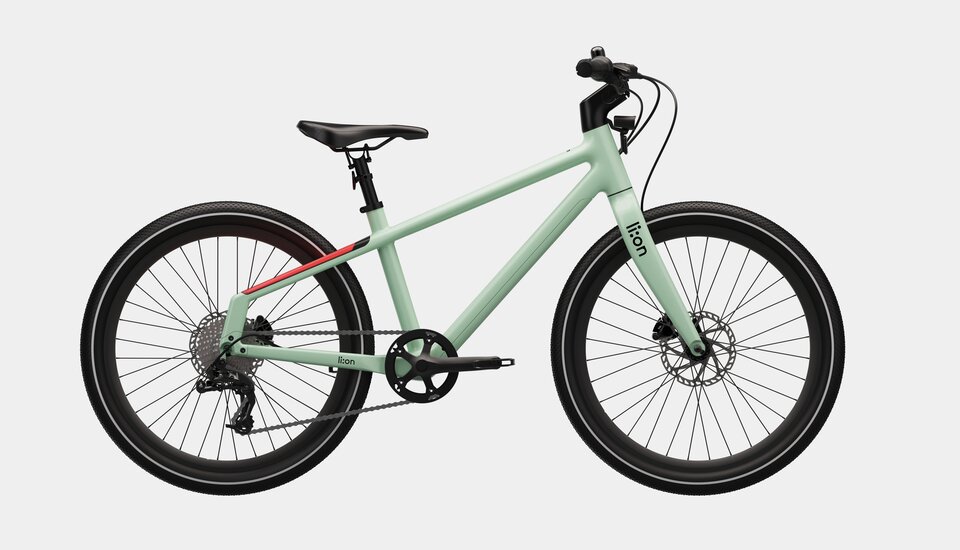
Safety first – even in a cool and sustainable design
Lion Bikes have a special paint that makes the frame glow. The unusually large lighting system with daytime running lights that is completely integrated into the frame enhances the visibility of the bikes. The frame and fork are made of the high-performance polymer polyamide 6 with 40 percent recycled carbon fibers – a groundbreaking new and resource-saving material mix in the bicycle industry. Thanks to these durable and 100% recyclable materials, the main components can be produced using a state-of-the-art injection molding process. Benefits for kids: a clean look with no welded seams at all, a stylish design and, most importantly, a mini-CO2 footprint.
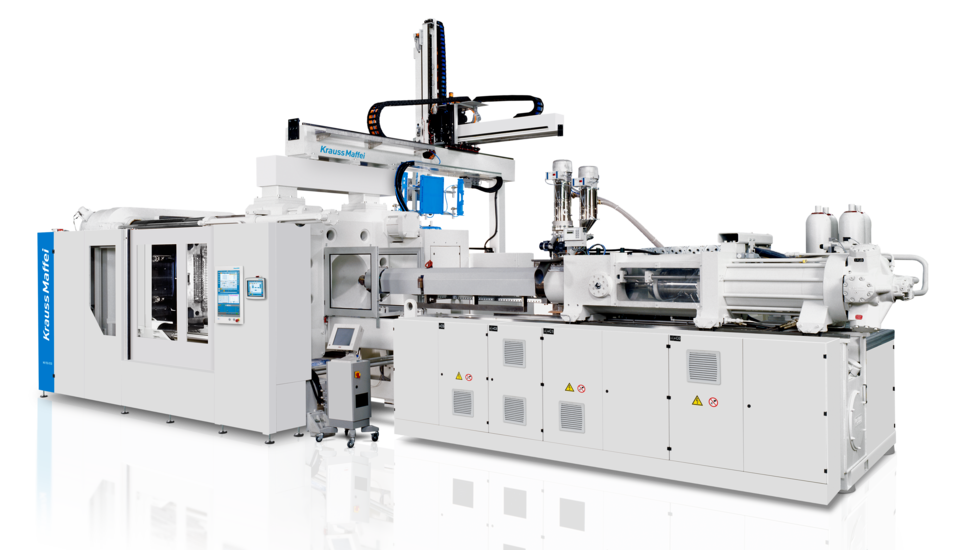
A guarantee for a high injection volume: The MX series from KraussMaffei
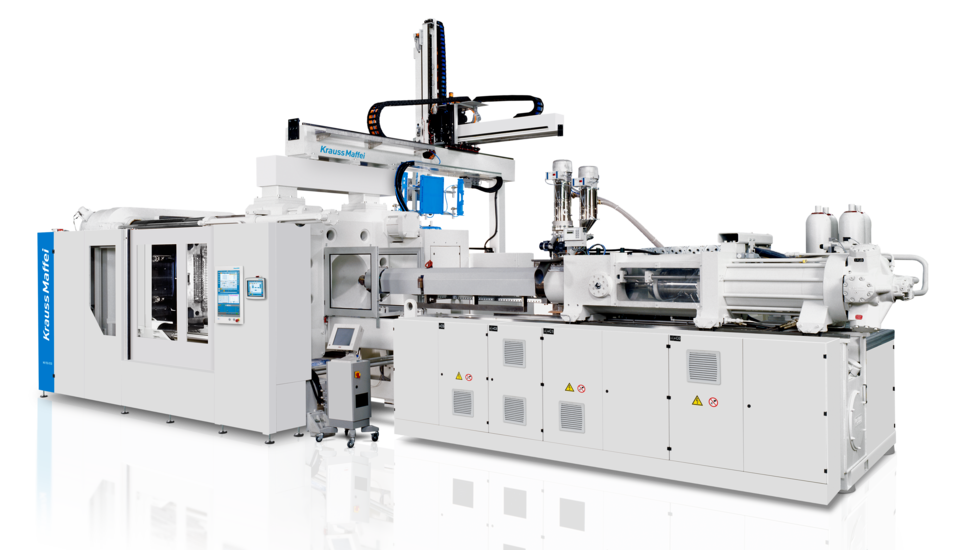
The frame and fork are being manufactured by specialist Weber Fibertech, on an MX 1600 from KraussMaffei, which is to be delivered this November. The first finished Lion Bikes will then be available on the market from spring 2024, in time for Easter. To ensure that all this can be done in terms of quality and on-time delivery, Weber Fibertech is relying on the many years of experience and expertise of KraussMaffei.
The technical performance of the MX series has won us over, and there's no turning back. In particular, we were impressed by how, with a screw diameter of 120 mm, injection was carried out at 300 mm/s, thus achieving a large volume with rapid mold filling. That was just great. High praise goes to Andreas Moll and his team at KraussMaffei.Friedbert Schmitt
CEO of Weber Fibertech
More ease and zero scrap thanks to WIT process
To ensure that the frame and fork are stable and at the same time require less material, Weber Fibertech uses the KraussMaffei MX 1600 in combination with the WIT process. So-called water injection molding is ideal for producing such functionally complex, highly integrated plastic components with hollow body construction. The appropriate machine and technology come from PME fluidtec, specialist with more than 100 successful WIT processes on the market.
The special feature here is that PME is using the mass back-pressure method in the WIT process for bicycle frames for the first time. The melt displaced by the water is pressed back into the plasticizing unit and reused in the next shot for the frame or fork. This means that there is no waste during production, which in turn saves material during production and is beneficial for the carbon footprint.
67 percent lower CO2-footprint
Going one step further and comparing the production of Lion Bikes with conventional aluminum frames and forks, CO2 emissions are 67 percent lower for each bike produced. Since the components are now made in Germany, this also shortens the supply chains and transport routes. Another important contribution to sustainability efforts.
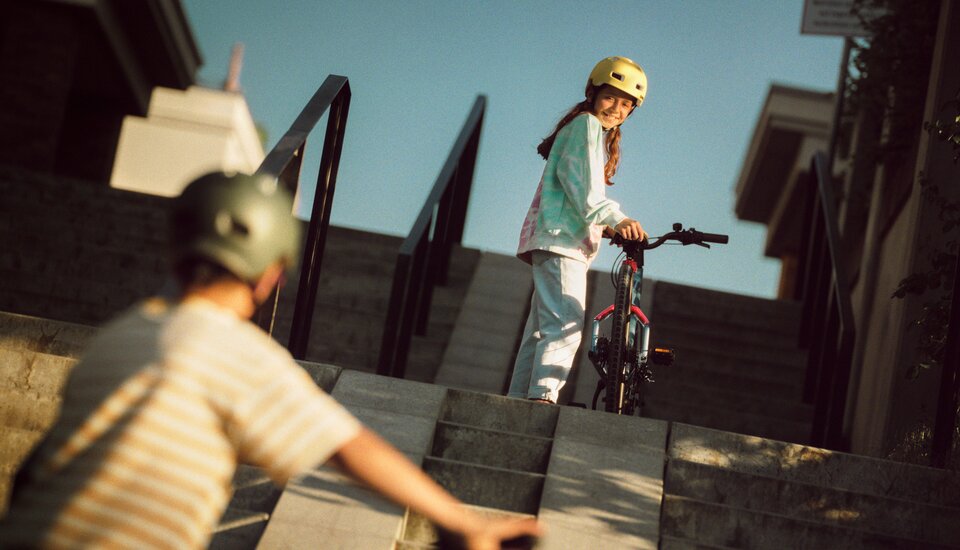
Off to new adventures: The new Lion Bikes provide more visibility and thus safety for the kids
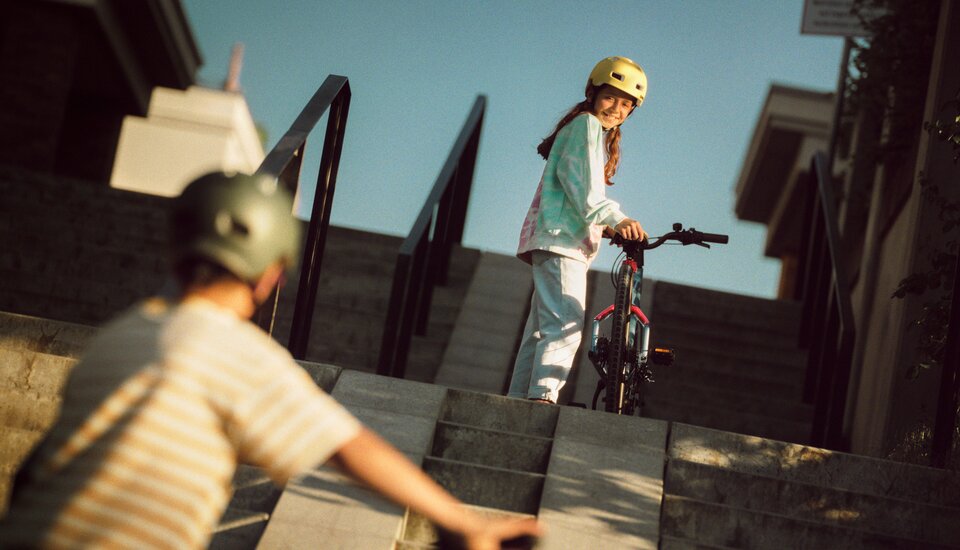
Lion Bike live at the KraussMaffei booth at Fakuma
Live at the KraussMaffei booth at Fakuma visitors can experience how more safety, cool design and sustainable production are revolutionizing the bicycle industry (Friedrichshafen, October 17 - 21, Hall A7, Booth 7303). Together with partner Weber Fibertech and PME, KraussMaffei is showing the prototype of the new Lion Bikes. Friedbert Schmitt:"With the processing of high-performance polymers and recycled carbon fibers and the production made in Germany, we are sending an important signal in the direction of sustainability in the bicycle industry." At the same time, kids ought to love their bike and parents should have no worries. For this they deserve nothing less than the safest and most visible bike – like the Lion Bike.
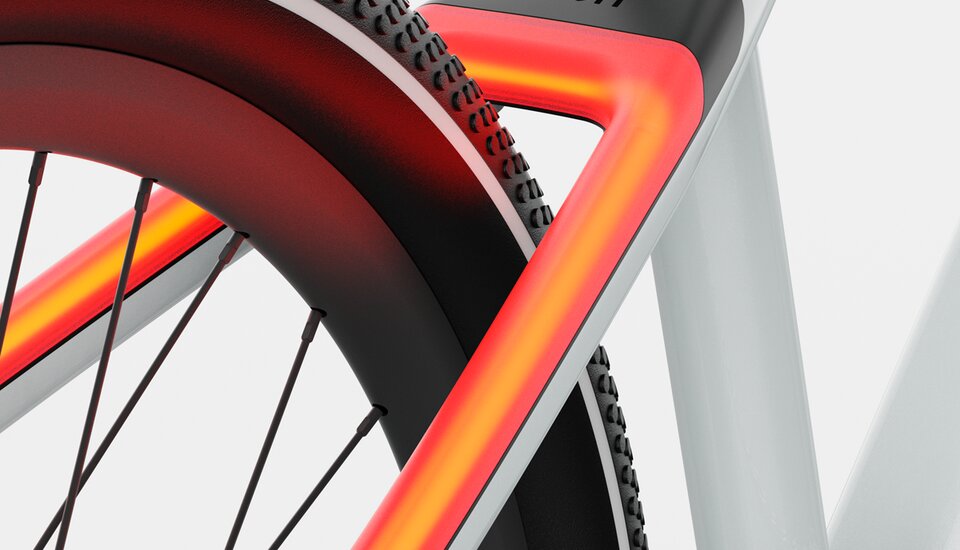
For more visibility: The attached luminous strip ensures that kids are seen well in the dark.
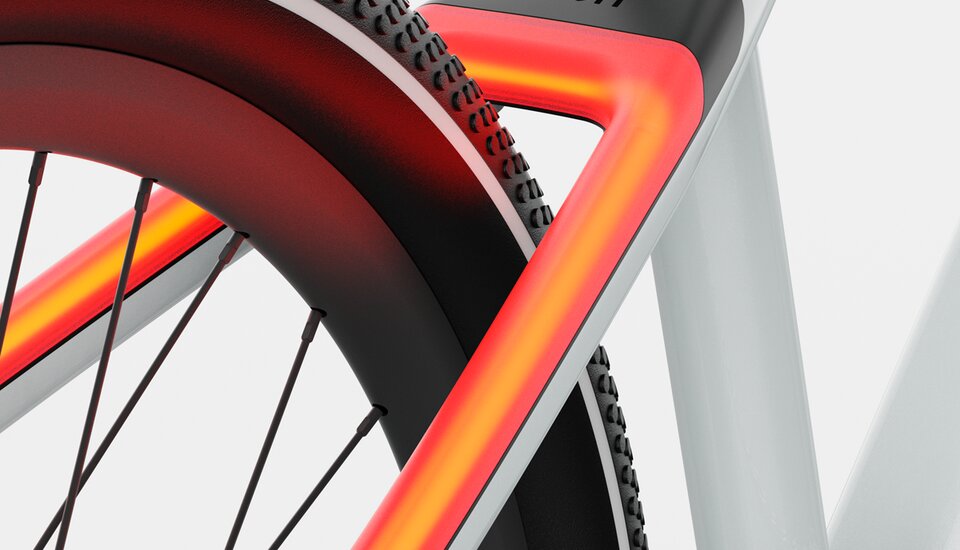