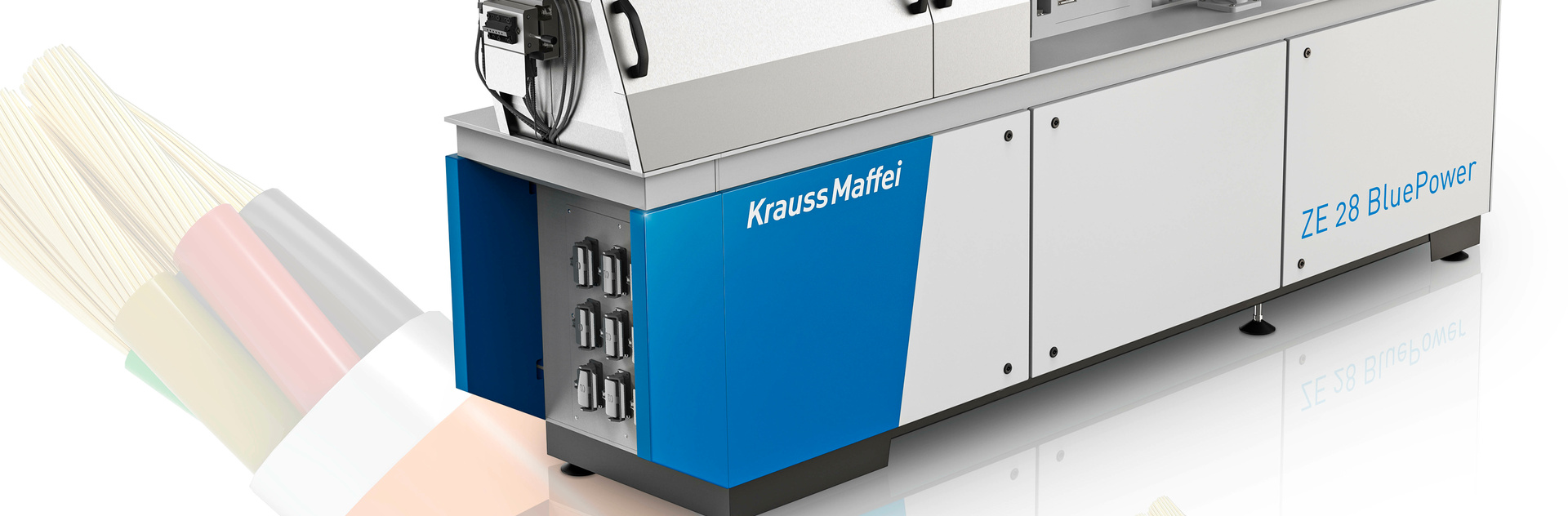
trendgineering
Innovative Extrusion Technology for Halogen-Free Cable Compounds
| Melanie Baum
How ZE BluePower from KraussMaffei Extrusion Is Setting New Standards in the HFFR Market
The market for halogen-free flame-retardant compounds (HFFR) is growing rapidly — driven by stricter building regulations, increasing fire safety demands, and a global shift toward sustainable materials. For compound manufacturers, this creates a clear imperative: competing in this dynamic environment requires highly precise and flexible processing technology. This is exactly where the ZE BluePower from KraussMaffei Extrusion comes in— delivering a solution that is uncompromising in terms of efficiency, quality, and process reliability.
Cable compounds based on halogen-free flame retardants not only offer excellent insulation and flame resistance, but also meet the stringent requirements of the European Construction Products Regulation (CPR).
HFFR cables are now the material of choice for public buildings and transport infrastructure. However, this market shift comes with challenges: high ATH (aluminum trihydroxide) loadings, sensitive raw material systems, and narrow process windows require precisely engineered technology.
ZE BluePower: Customized Extrusion for HFFR Compounds
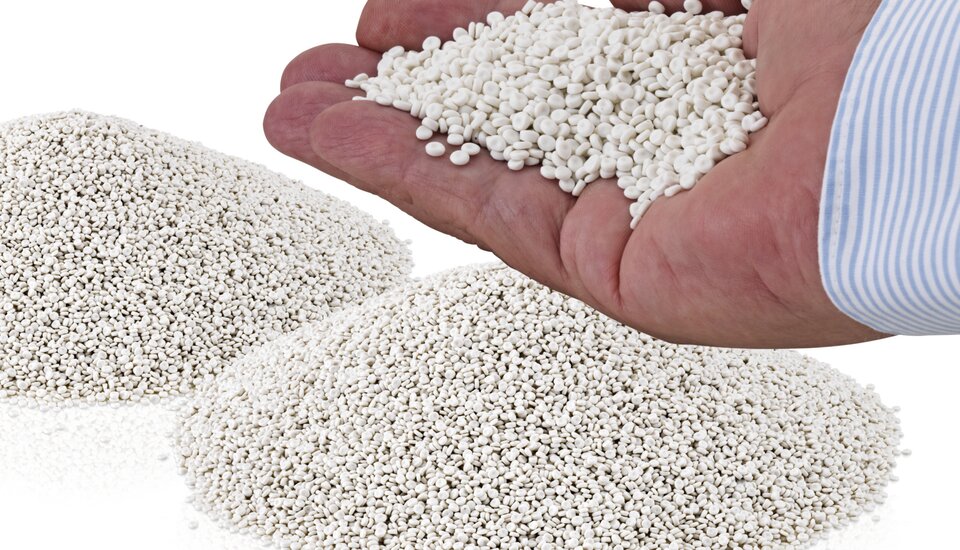
With ZE BluePower, KraussMaffei Extrusion offers a high-efficiency extrusion solution tailored specifically for the production of HFFR cable compounds — designed to process up to 65% ATH while offering maximum flexibility in process configuration.
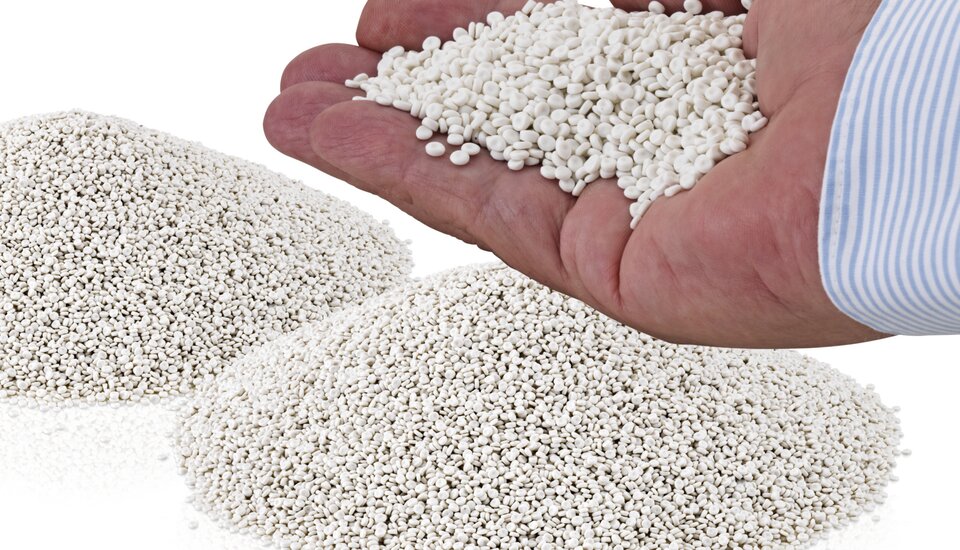
The key strengths include gentle yet intensive incorporation of flame retardants, made possible by an optimized screw configuration. Melt temperatures are reduced by up to 30 Kelvin, significantly improving product quality.
The system can be flexibly adapted to various formulations and raw materials, even when processing sensitive compounds. A wide process window allows for different fill levels and throughputs. Modular design sizes cover capacities ranging from 50 to 1,500 kg/h.
Co-Developed with Industry Leaders
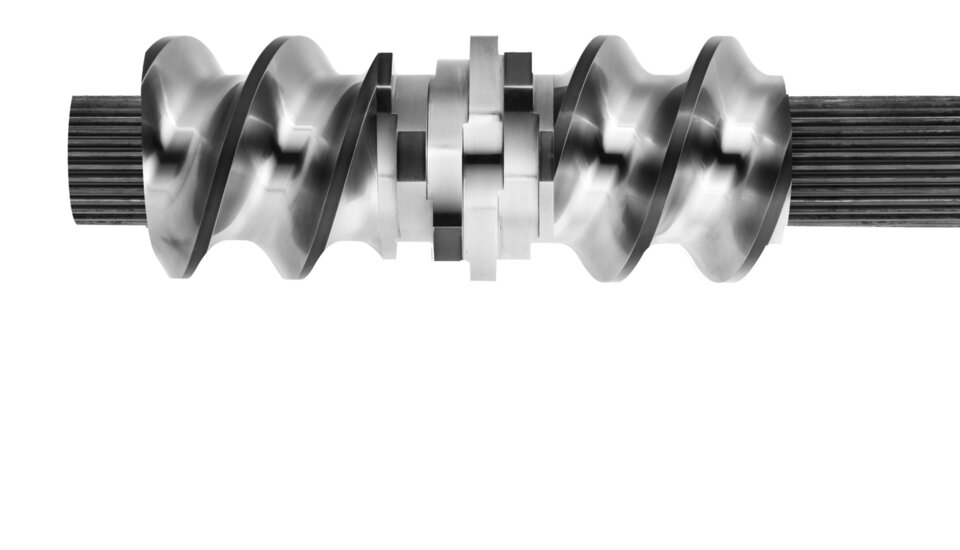
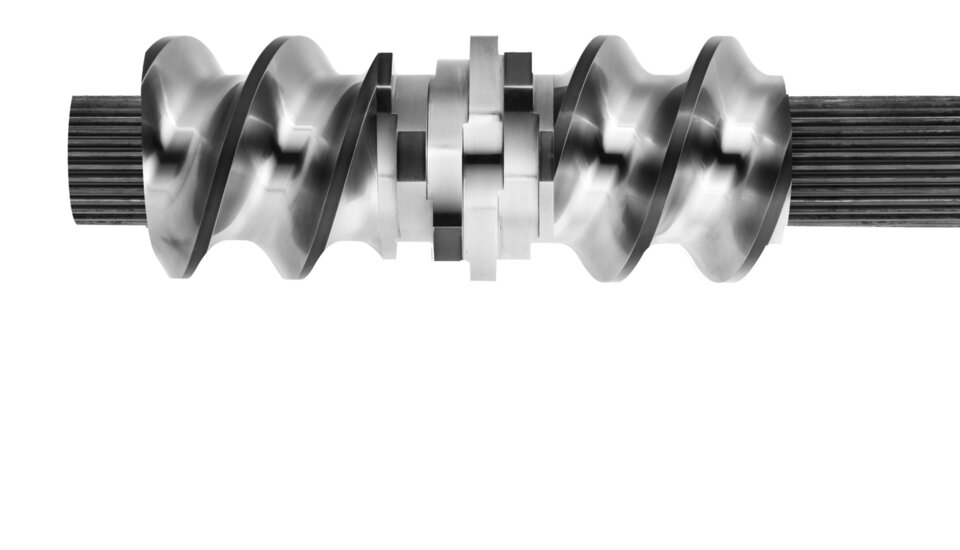
The ZE BluePower system has been rigorously tested in KraussMaffei’s Technology Center in Laatzen, Germany. In close collaboration with ExxonMobil and Huber Advanced Materials, various formulations, screw geometries, and ATH concentrations were trialed on a 48L/D ZE BluePower line — with impressive results.
We have fine-tuned the processing unit specifically for HFFR applications. All performance targets— mechanical properties, dispersion quality, and process stability — were not only met but exceeded.Bilal Ilhan
RnD Engineer Process
To ensure stable production, especially for highly filled and shear-sensitive compounds, underwater pelletizing with pressure-reduced die plates is used. This granulation setup was specifically developed to ensure consistent pellet quality under demanding conditions.
A Complete Solution for Compound Manufacturers
Whether for new installations or retrofits, ZE BluePower offers compounders a comprehensive solution — covering the entire process from raw material feeding to granulation, all precisely adaptable to specific production requirements.
With flexible processing lengths (48–56 L/D), five machine sizes, and an ideal combination of free volume and specific torque (Da/Di ratio of 1.65 / torque density of 16 Nm/cm³), the ZE BluePower is fully equipped to meet the demands of next-generation cable compounds.
With intelligent system design, validated processing technology, and strong development support from KraussMaffei’s Extrusion Technology Center, compound manufacturers gain a reliable partner to help them lead in the rapidly growing HFFR market.