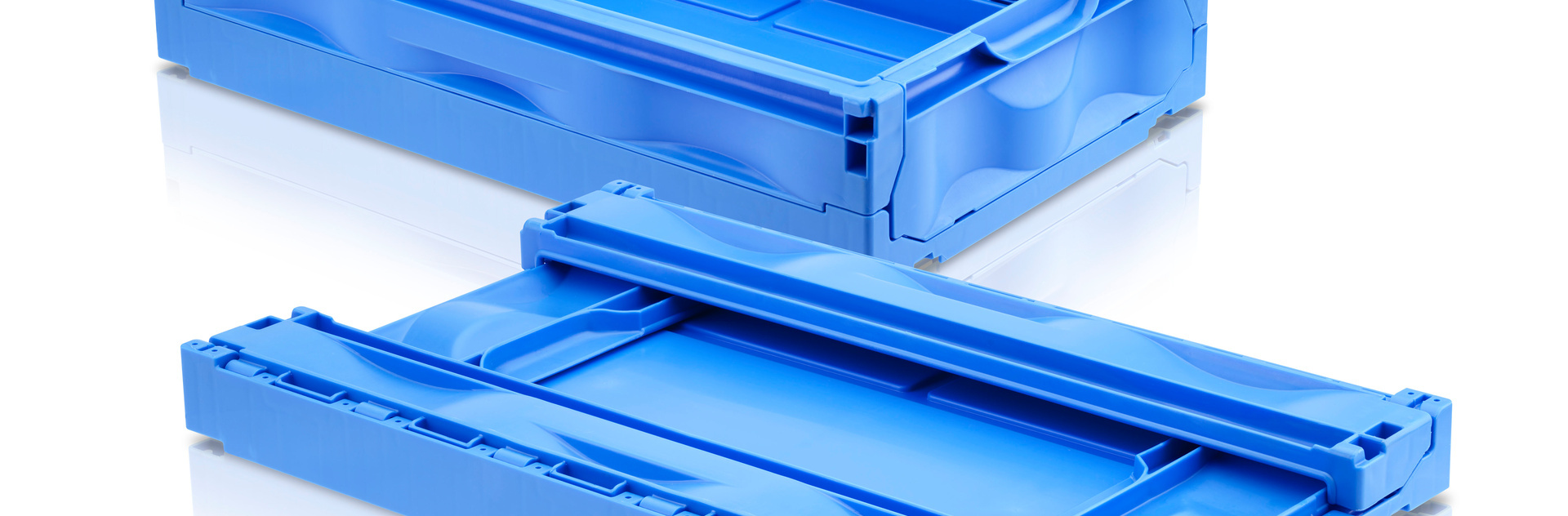
sustainability
New material made from three recyclates
| Petra Rehmet
Live at K 2022: Reusable crates made with three recyclates
When it comes to recycling plastics, aspirations and reality often diverge. This is because pure polymer is only available in limited quantities. Therefore, as many sources as possible must be used to achieve the necessary volume of recyclate. With Direct Compounding Injection Molding (DCIM), KraussMaffei is demonstrating at K 2022 how a new material can be compounded from three recyclates of different viscosities.
FFP2 masks are everywhere. What should be done with the scrap created during production? It should be recycled, of course. The staple fiber fleece made of polypropylene is as liquid as water (melt volume rate MVR 800-1000), entirely different from shredded gummy scraps of HDPE from the production of blow-molded parts from the toy industry (MVR < 1). If you also add HDPE from injection molding production with a consistency similar to honey (MVR 5-15), you have the three components that are being combined into one new material at K 2022.
KraussMaffei is focusing its trade show presence on circular economy - and the DCIM direct compounder with its single-screw extruder plays a central role. It is suitable for shot weights from 50 to 2000 grams and thereby complements the IMC system (Injection Molding Compounder, with twin-screw extruder), which has been tried-and-tested for 20 years and is economically attractive for shot weights of 1500 grams or more.
Saving costs with DCIM
The current costs of polymers result in material dealers no longer being able to purchase enough recycled materials to cover their demand. So it´s necessary to take action yourself. The DCIM process (Direct Compounding Injection Molding) makes this easy by blending, modifying with additives, reinforcing or filling and feeding the material directly into the injection molding process.
The DCIM process saves costs for external compounding (on average, about 0.6 €/kg) and gives the processor maximum control over the materials used.Franz-Xaver Keilbach
Global Product Owner Circular Economy / Recycling
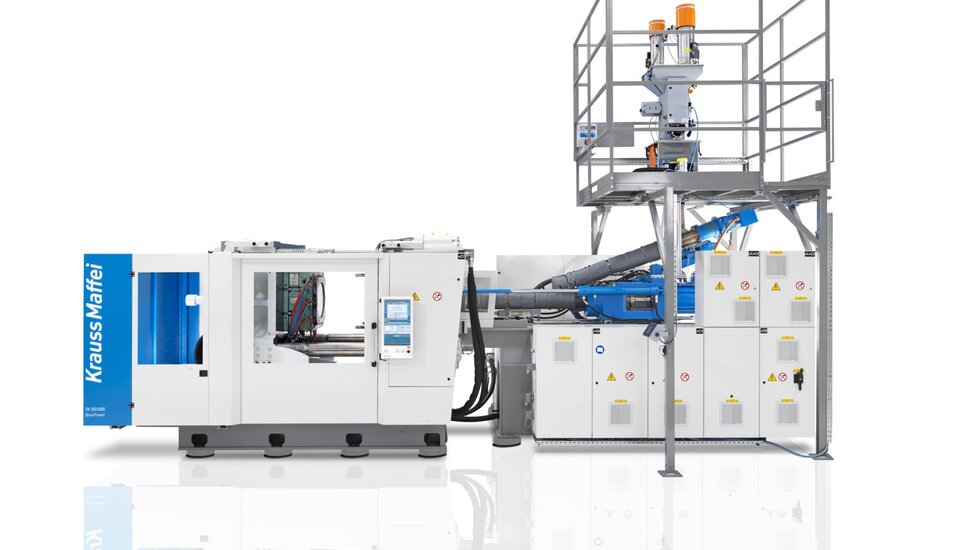
Injection molding and compounding in a single heating process
Production in one heat: DCIM technology from KraussMaffei saves valuable cycle time and reduces material costs by up to 50 percent.
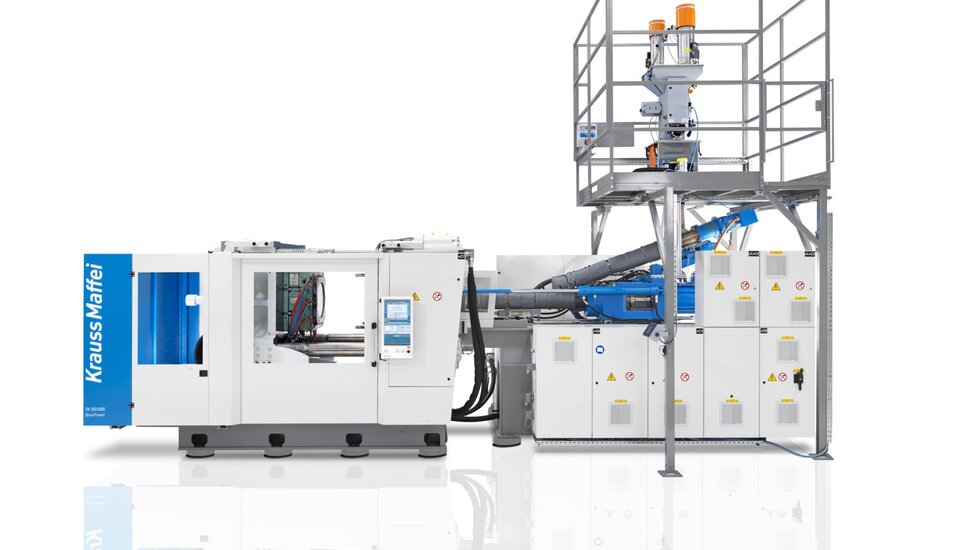
For DCIM, a single-screw extruder is installed in a piggyback position directly over the injection unit of a standard hydraulic machine (usually from the GX series). Both produce in intermittent operation, which means that the extruder stops when the injection volume for the next cycle has been reached.
For the trade show application, the three materials are additionally mixed with the masterbatch, stabilizer additive and micaceous iron oxide as fillers. The last of these results in a cooling time reduced by up to ten percent. Turning the six individual components into a homogeneous melt is achieved by the special screw of the extruder. It has an optimized design and an extraordinarily length. The ratio of length to diameter is usually about 17-23 L/D (standard injection molding machines), but for DCIM it is an impressive 30 L/D.
Production in one heat saves valuable energy
In view of the current energy problem, it is also of particular interest that all production is accomplished in a single heating process, so the compounded melt goes directly from the extruder into the plasticizing unit of the injection molding machine without interruption and without heat loss. This one-step process conserves energy, reduces the CO2 footprint and is gentle on the material since degradation of the polymer is reduced.
Sustainable transport crates made of three different recycled materials
At the trade show booth, the new polyolefin plastic created in this way is turned into practical five-piece collapsible crates, like the kind used for transporting fresh fish. The cycle time of the GX 1100-4300 DCIM is about 35 seconds, so it is perfect for DCIM because, starting from about 20 seconds, the additional material processing has no impact on cycle time.
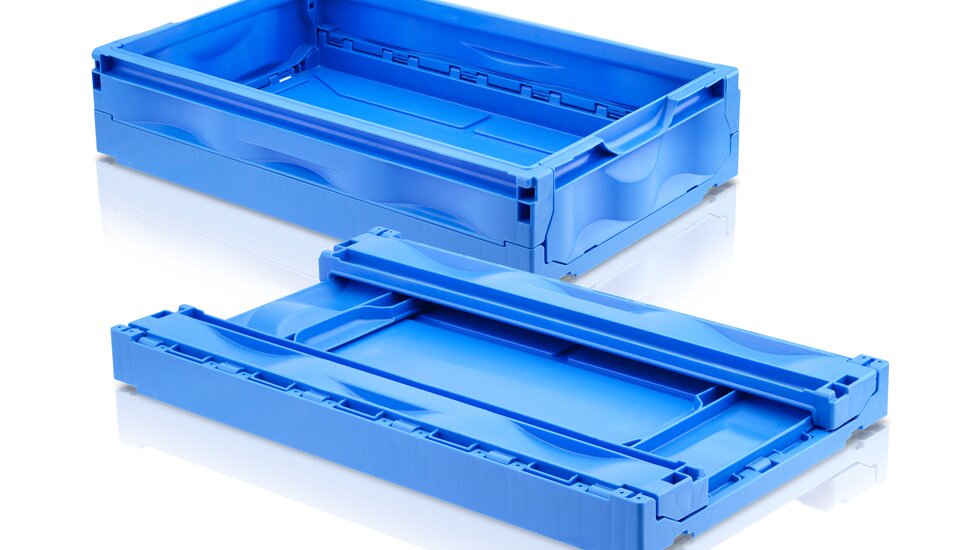
At K 2022, a GX 1100-4300 DCIM produces returnable crates from three different recyclates.
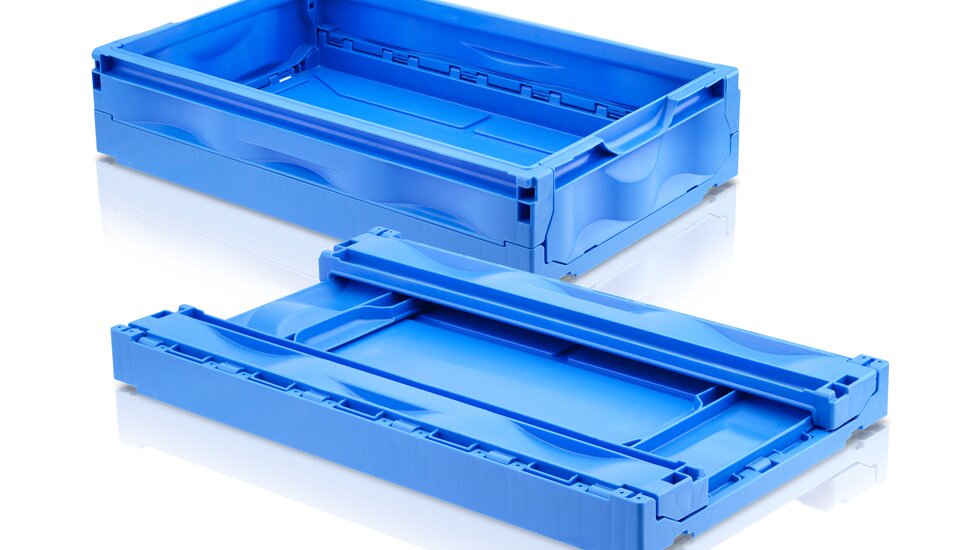
Most of the technical parts that come into question for direct compounding are above this limit. At K, an LRX 350 linear robot removes the five individual parts from the mold (SCS moldmaking) and transfers them to an automation system from Campetella, which takes over the insertion, clipping and stacking of the crates.
Taking responsibility for the materials and controlling the formulations
No doubt the cost benefits of direct compounding (about 30 to 50 percent) are in the foreground for the price-driven packaging and logistics industry, but for manufacturers of technical parts another motive can come into play: product stewardship. Companies—such as manufacturers in the area of safety-related components - that are in a dispute and have to prove that the articles they delivered were absolutely OK might also want to have control over the materials and not rely on an external compounder. Then in case of new projects or modified mechanical requirements, they will also be able to develop their own new formulations and propose them to the customer.
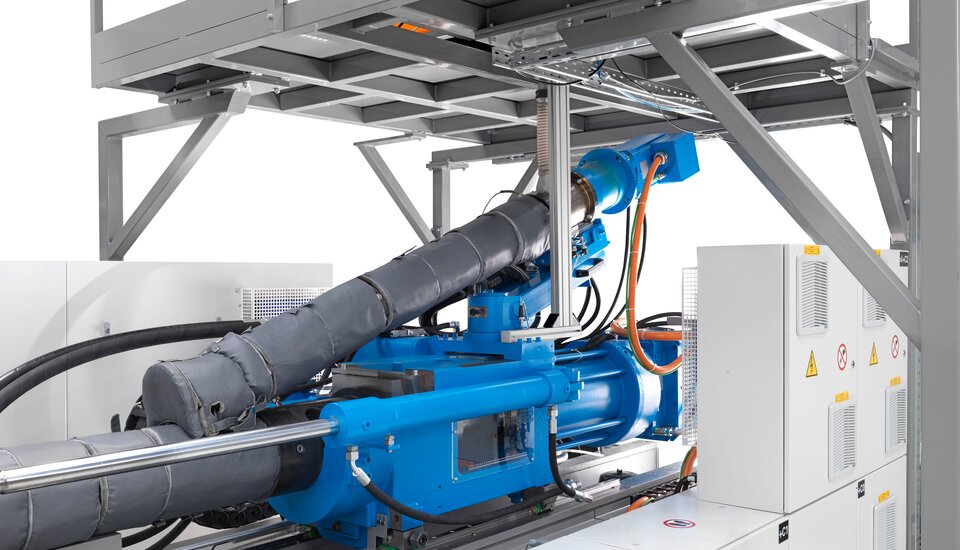
Economically attractive, particularly for part weights from 50 to 2000 g
The DCIM process from KraussMaffei uses a single-screw extruder.
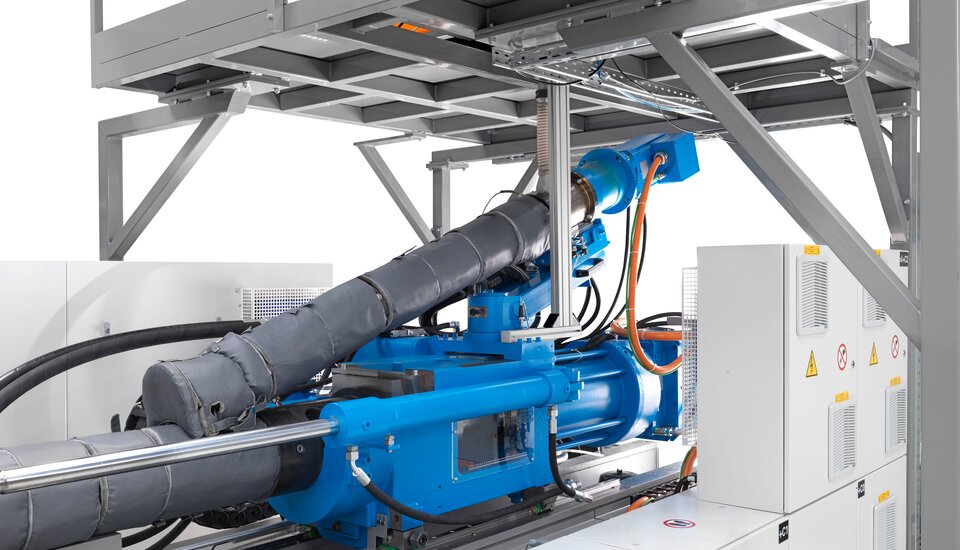
Since the concept is based on a standard machine, the additional costs for DCIM equipment are low and pay for themselves in a short time. If no compound is needed at the moment, the machine can also be used in standard injection molding mode without any elaborate conversion work. This gives the user maximum flexibility, and they are equipped for further developments within the circular economy.
Thank you to our partners
BIG-SPIELWARENFABRIK GmbH & Co. KG (blown film); Schoeller Allibert Services B.V. (HDPE injection molding products); Zettl Meditec GmbH (FFP mask fleece); Audia Plastics s.r.o. (color masterbatch); Byk Chemie (additives), Kärtner Montanindustrie (micaceous iron oxide); Campetella Robotic Center srl (automation) and S.C.S. Societa Construzione Stampi (molds)Contact
franz-xaver.keilbach@kraussmaffei.com